Stockless Production Part 1
Summary
TLDRDoug McCord, gerente de producción en Hewlett-Packard Greeley, presenta un programa piloto de producción sin inventarios. El video compara los procesos tradicionales de producción por lotes ('push') con el nuevo enfoque de producción 'pull', donde los materiales se solicitan solo cuando son necesarios. McCord destaca cómo este método reduce inventarios, tiempos de ciclo, reprocesos y espacio requerido. La demostración incluye un modelo práctico que ilustra los beneficios de la producción 'pull', como mayor calidad, productividad y participación de los trabajadores, mostrando la evolución del sistema de producción en HP Greeley.
Takeaways
- 😀 La empresa Hewlett-Packard está implementando un programa piloto de producción sin inventario en su división de Greeley, Colorado.
- 📦 El proceso tradicional de manufactura en Hewlett-Packard ha sido el método de empuje, pero están cambiando a un proceso de extracción (pull).
- 📉 La producción sin inventario promete reducir inventarios, tiempos de ciclo, trabajo en proceso, niveles de reprocesamiento y el espacio requerido para almacenar materiales inactivos.
- 👍 Los beneficios adicionales del nuevo sistema incluyen un mejor control de calidad, mayor productividad de los trabajadores y más participación de los empleados.
- 🎬 La división de Greeley ha creado una presentación para mostrar las técnicas de producción sin inventario a los empleados de manufactura.
- 🚀 La presentación ilustra cómo el sistema de empuje crea desorden, mientras que el sistema de extracción mejora la eficiencia y reduce el desorden.
- 🔧 En el ejemplo, se fabrican cajas de espuma de poliestireno con varios trabajadores asignados a diferentes tareas, demostrando la diferencia entre los sistemas de empuje y extracción.
- ⏱️ El sistema de empuje genera un tiempo de producción lento y una acumulación innecesaria de inventario en el proceso de producción.
- 🔍 Durante la demostración, se presenta un problema de control de calidad, lo que ilustra cómo el sistema de extracción puede evitar la acumulación de unidades defectuosas.
- 👷 El sistema de extracción permite abordar problemas como la sobreproducción y el reprocesamiento, logrando una mayor eficiencia en el proceso de manufactura.
Q & A
¿Qué describe Doug McCord como el método de producción tradicional en Hewlett-Packard?
-Doug McCord describe el método de producción tradicional en Hewlett-Packard como un proceso de empuje o 'batch', en el cual el material se produce y se envía al siguiente paso en el proceso, incluso si la siguiente etapa no está lista para recibirlo.
¿Cuál es la principal diferencia entre el sistema de producción tradicional y el sistema de producción sin stock que están probando?
-La principal diferencia es que el sistema sin stock ('pull') solo retira el material cuando es necesario, lo que reduce inventarios, tiempos de ciclo, y el trabajo en proceso, mientras que el sistema de empuje ('push') genera una acumulación de material que puede no ser utilizado de inmediato.
¿Qué beneficios mencionan sobre la producción sin stock?
-Los beneficios incluyen una reducción significativa de inventarios, tiempos de ciclo, trabajo en proceso, niveles de retrabajo, y el espacio necesario para almacenar material inactivo. Además, mencionan mejoras en la calidad, productividad de los trabajadores y mayor participación de los empleados.
¿Cómo visualizan los procesos de empuje en la demostración presentada en el 'Roadshow'?
-En la demostración, utilizan un producto simulado (una caja de espuma de poliestireno) y muestran cómo en el sistema de empuje se generan retrasos, acumulación de trabajo en proceso, desorden y, a veces, problemas de calidad.
¿Qué se espera lograr al comparar los sistemas de empuje y arrastre en la demostración?
-Se espera comparar cinco parámetros entre los sistemas de empuje y arrastre: el espacio utilizado, el nivel de trabajo en proceso, la productividad, la calidad, y el retrabajo requerido.
¿Cuál fue el problema de calidad que se identificó durante la demostración y qué implicaciones tuvo?
-El problema de calidad identificado fue la aparición de puntos verdes en lugar de puntos rojos en el producto, lo que sugirió un error de proveedor. Esto podría llevar a la inspección y retrabajo de una cantidad significativa de unidades, demostrando uno de los inconvenientes del sistema de empuje.
¿Cómo afecta el sistema de empuje a la cantidad de trabajo en proceso y el espacio utilizado?
-En el sistema de empuje, el trabajo en proceso tiende a acumularse, lo que requiere más espacio para almacenar material no utilizado inmediatamente y genera un desorden general en la línea de producción.
¿Qué método se utilizó para medir la eficiencia en la demostración de producción?
-Utilizaron un cronómetro para medir el tiempo que tardaba el producto simulado en pasar de una etapa de producción a otra, desde que se introducía en la línea hasta que se empaquetaba.
¿Cuál fue el tiempo medido en el sistema de empuje y cómo lo evaluaron?
-El tiempo medido en el sistema de empuje fue de 3 minutos y 17 segundos. Evaluaron este tiempo como dolorosamente lento y un claro ejemplo de ineficiencia en el proceso de empuje.
¿Qué se espera que logren al reducir simultáneamente el trabajo en proceso y el número de unidades fabricadas?
-Al reducir simultáneamente el trabajo en proceso y el número de unidades fabricadas, esperan aumentar la eficiencia, reducir el desorden y mejorar la capacidad de gestión y control del proceso, alineándolo más con los principios del sistema de arrastre.
Outlines
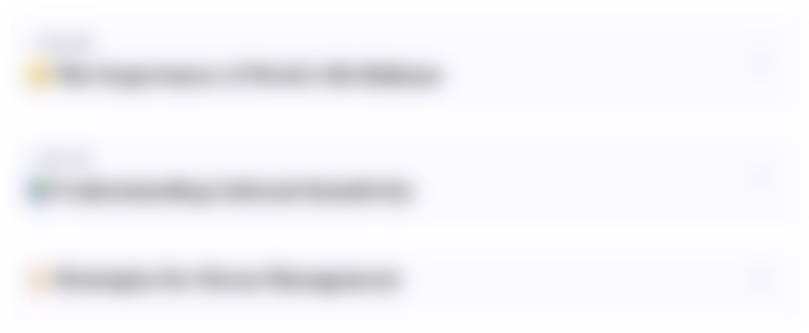
此内容仅限付费用户访问。 请升级后访问。
立即升级Mindmap
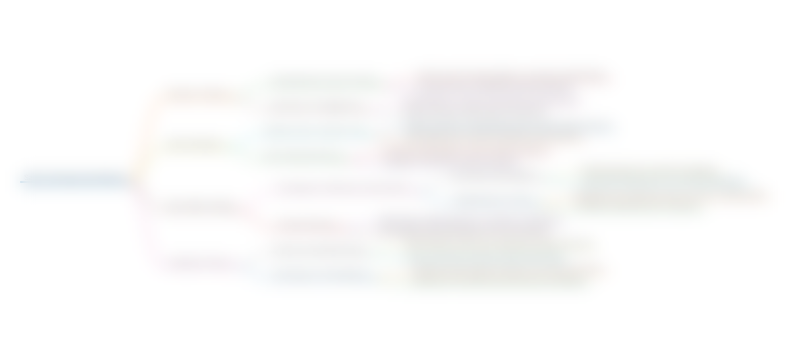
此内容仅限付费用户访问。 请升级后访问。
立即升级Keywords
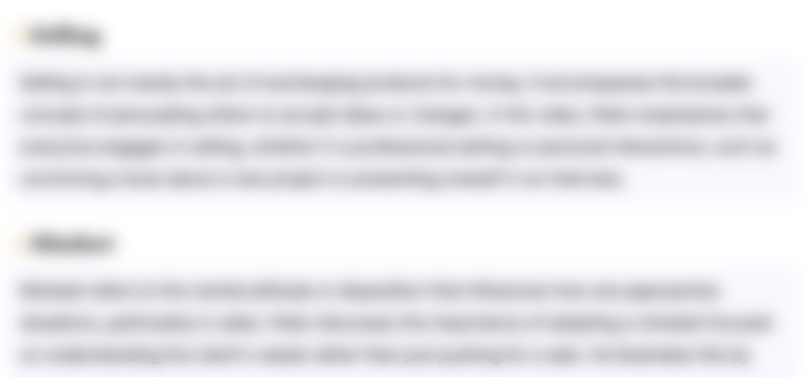
此内容仅限付费用户访问。 请升级后访问。
立即升级Highlights
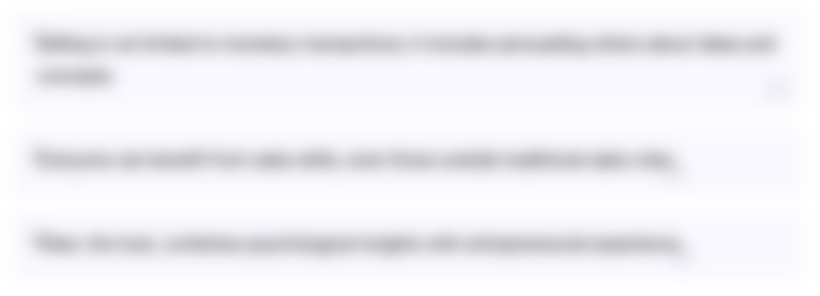
此内容仅限付费用户访问。 请升级后访问。
立即升级Transcripts
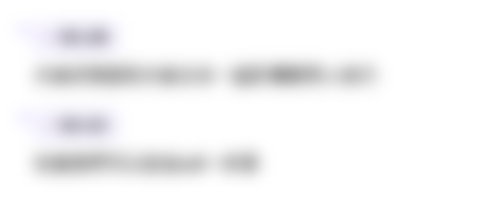
此内容仅限付费用户访问。 请升级后访问。
立即升级5.0 / 5 (0 votes)