Understanding True Stress and True Strain
Summary
TLDRThis video explains the differences between engineering and true stress-strain curves obtained from tensile tests on ductile materials. It highlights that engineering stress and strain, based on initial dimensions, are approximations, while true stress and strain account for changes in the specimen’s cross-sectional area throughout the test. The video also details why engineers typically use engineering curves, despite the greater accuracy of true curves, and how true stress and strain can be derived mathematically from engineering values. The importance of true curves in analyzing large plastic deformations is emphasized.
Takeaways
- 📈 The typical stress-strain curve for a ductile material from a tensile test is an approximation.
- ⚙️ Engineering stress and strain are approximations of the true values and are based on the initial dimensions of the specimen.
- 📊 True stress and strain take into account the changing dimensions of the test piece during the tensile test.
- 📉 The engineering stress-strain curve drops after necking, while the true stress-strain curve continues to increase.
- 🔧 Engineers often use engineering curves because measuring the instantaneous cross-sectional area during a test is difficult.
- 🔍 The engineering and true stress-strain curves are very similar in the elastic region but differ significantly in the plastic region.
- 🧮 True stress is calculated by dividing the applied force by the instantaneous cross-sectional area, considering volume conservation.
- 📐 True strain accounts for continuous changes in the specimen's length and can be calculated mathematically using integration.
- ⚖️ The assumption of constant volume holds until necking occurs, after which true stress must be based on actual measurements.
- 🔗 True strain is also known as logarithmic or natural strain due to its mathematical form involving the natural logarithm.
Q & A
What is a typical stress-strain curve for a ductile material, and how is it obtained?
-A typical stress-strain curve for a ductile material is obtained by performing a tensile test. It provides a general approximation of stress and strain behavior under load but doesn’t represent the true stress and strain in the specimen.
What is the difference between engineering stress and true stress?
-Engineering stress is calculated by dividing the applied force by the initial cross-sectional area of the specimen, while true stress considers the instantaneous cross-sectional area, accounting for changes throughout the test.
Why is the engineering stress-strain curve commonly used despite not reflecting true stress and strain?
-The engineering stress-strain curve is often used because it is challenging to measure the instantaneous cross-sectional area during testing. Additionally, most engineering applications involve small deformations in the elastic region, where true and engineering stresses are similar.
How can true stress and strain be determined without directly measuring the instantaneous cross-sectional area?
-True stress and strain can be calculated from the engineering stress-strain curve by making certain assumptions, such as assuming constant volume, which is generally valid in the elastic and plastic regions before necking occurs.
What happens to the engineering stress-strain curve after necking?
-After necking, the engineering stress-strain curve drops, reflecting a rapid reduction in the cross-sectional area. This reduction does not occur in the true stress-strain curve, which continues to increase.
Why is it important to use the true stress-strain curve in cases of significant plastic deformation?
-The true stress-strain curve is important in cases of significant plastic deformation because it accounts for the actual stress experienced by the material, which is crucial for accurately modeling large strains in analyses like manufacturing or finite element analysis.
What is the assumption made when calculating true stress in the elastic and plastic regions?
-It is assumed that the volume remains constant in both the elastic and plastic regions. In the elastic region, volume changes are minimal, and in the plastic region, the material is considered incompressible, which justifies this assumption.
Why is the constant volume assumption not valid after necking?
-After necking, there is a significant reduction in the cross-sectional area that affects the specimen’s volume, so the constant volume assumption no longer holds. True stress calculations beyond necking require actual cross-sectional measurements.
How is true strain defined compared to engineering strain?
-True strain considers the continuous change in the specimen’s length throughout the tensile test, unlike engineering strain, which only considers the change from the initial length. True strain can be calculated by summing up incremental strain changes or integrating over the entire test.
What is logarithmic or natural strain, and why is true strain also called this?
-True strain is also known as logarithmic or natural strain because its calculation involves the natural logarithm, reflecting a continuous change in length. The formula for true strain uses integration, resulting in a logarithmic function.
Outlines
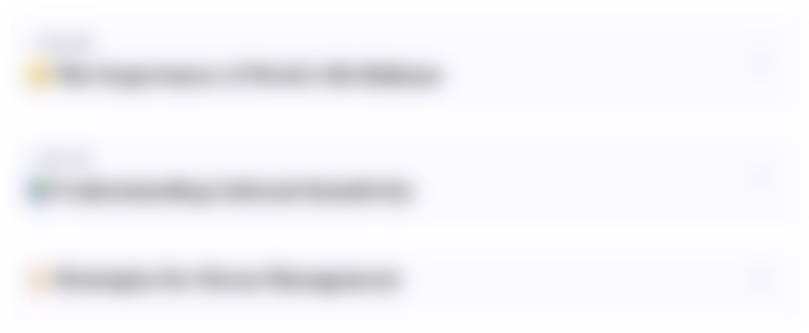
此内容仅限付费用户访问。 请升级后访问。
立即升级Mindmap
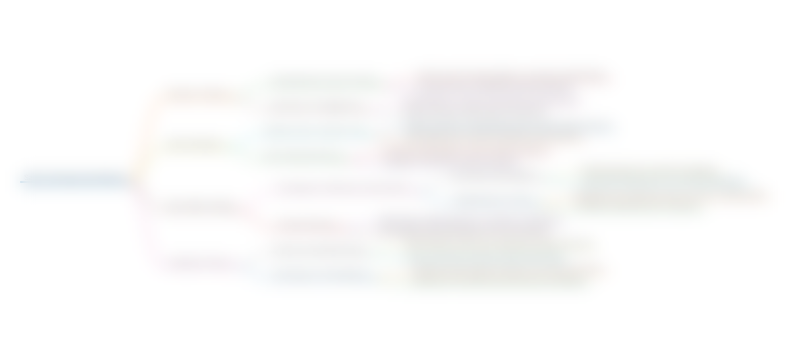
此内容仅限付费用户访问。 请升级后访问。
立即升级Keywords
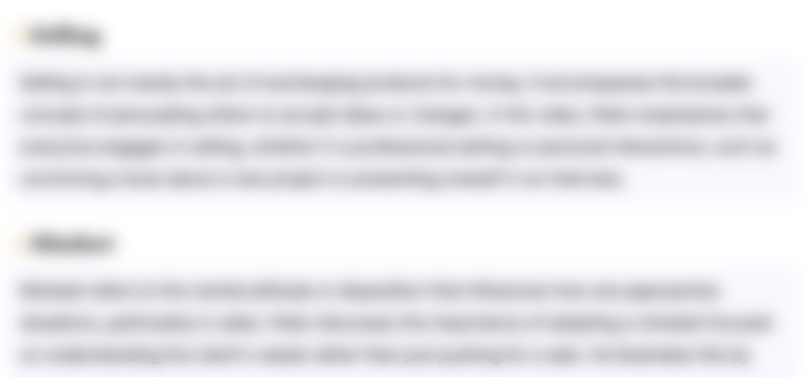
此内容仅限付费用户访问。 请升级后访问。
立即升级Highlights
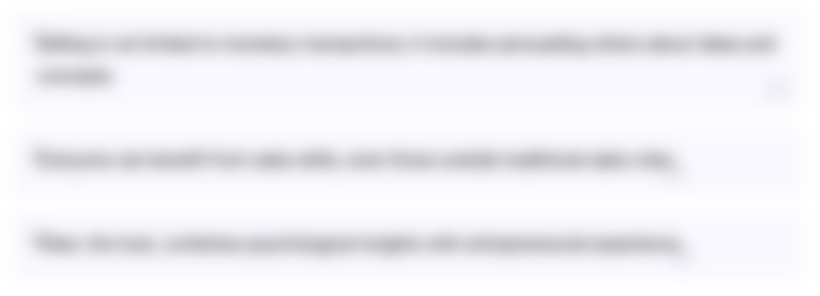
此内容仅限付费用户访问。 请升级后访问。
立即升级Transcripts
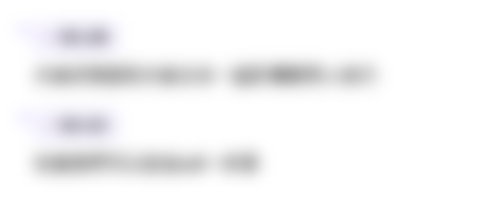
此内容仅限付费用户访问。 请升级后访问。
立即升级浏览更多相关视频
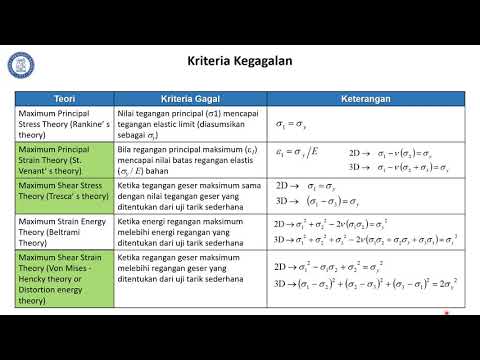
Analisis Kegagalan Logam: Modul 1 Segmen 2 (Kriteria Kegagalan)
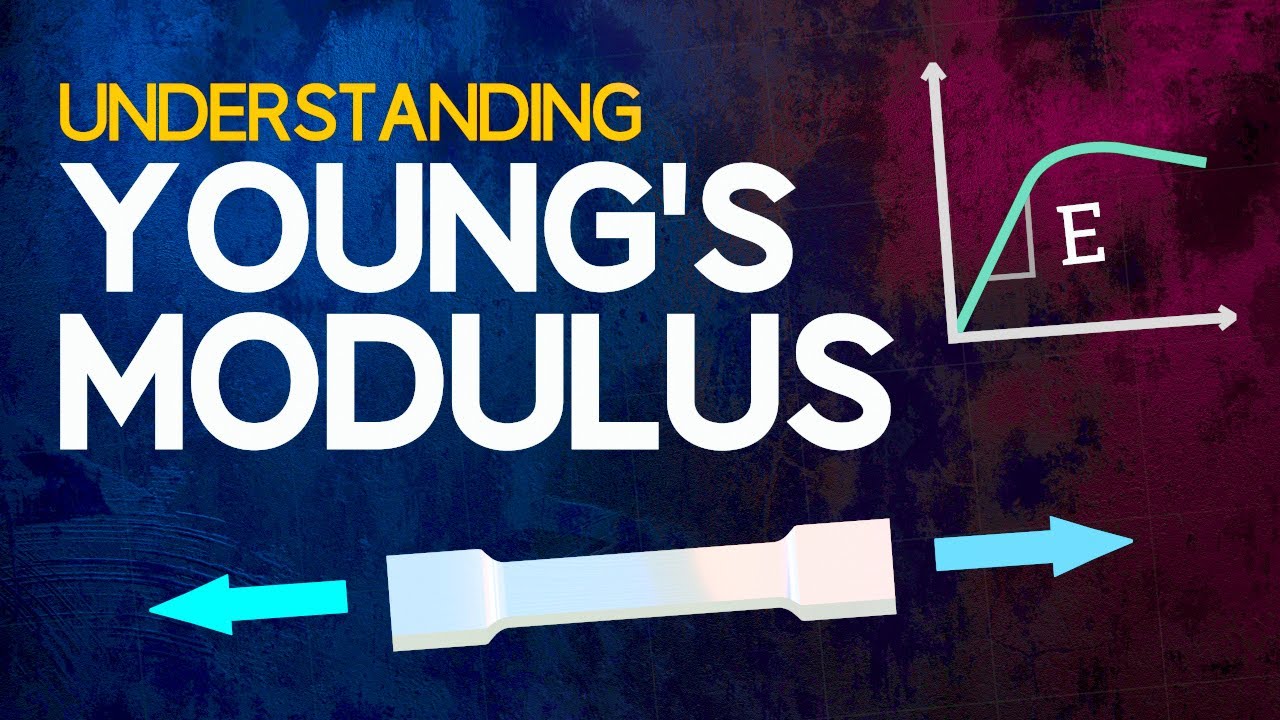
Understanding Young's Modulus

Stress and Strain | Stress strain curve of mild steel | Mechanical Properties of Solids |
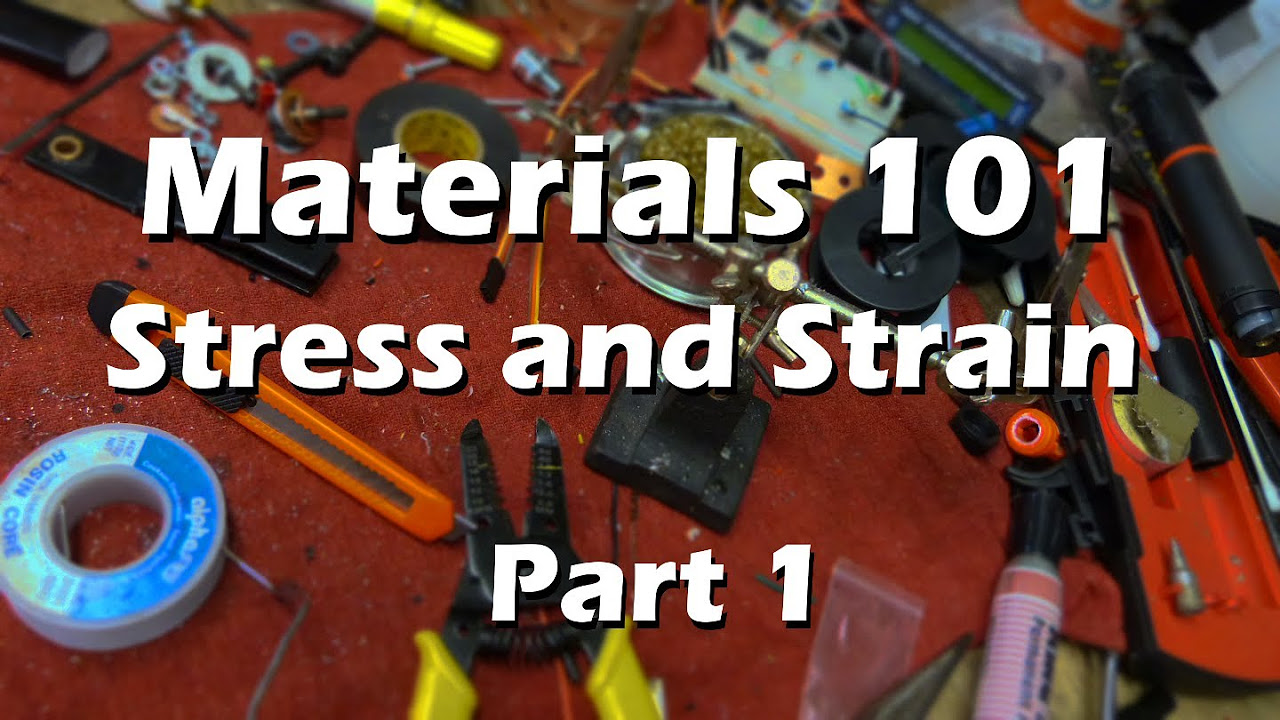
Materials Science Mechanical Engineering - Part 1 Stress and Strain Explained
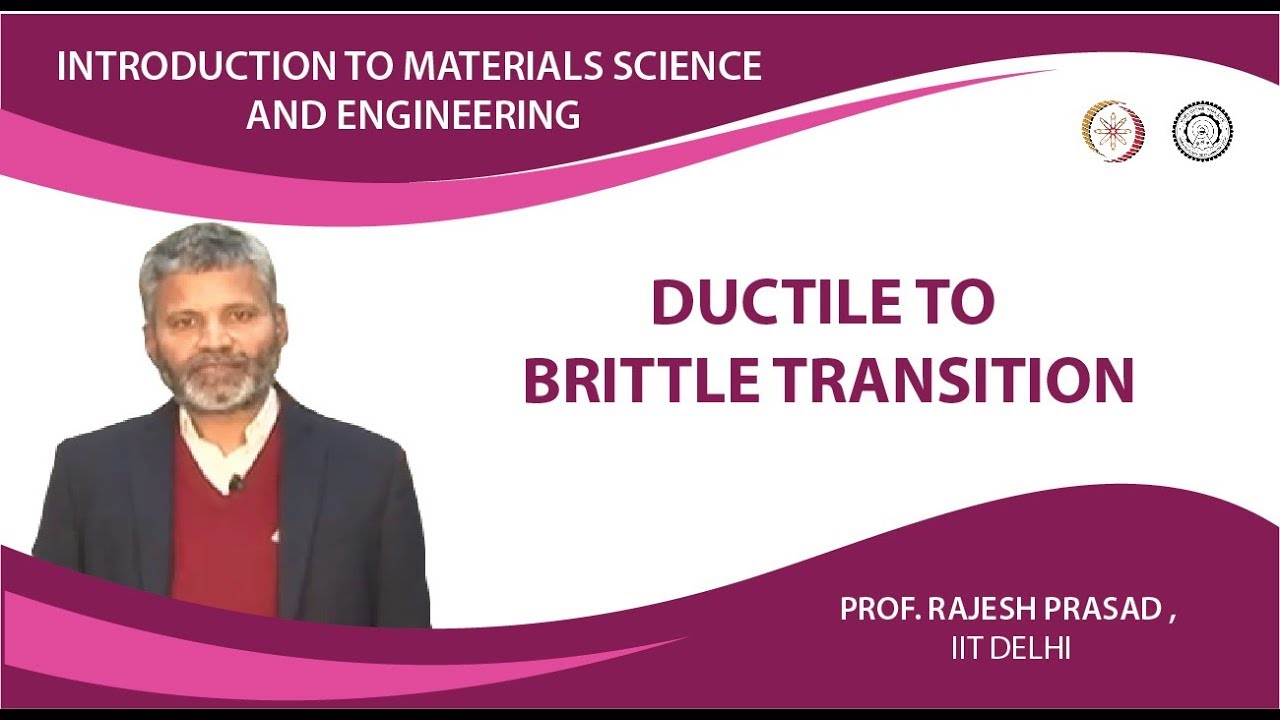
Ductile to Brittle Transition
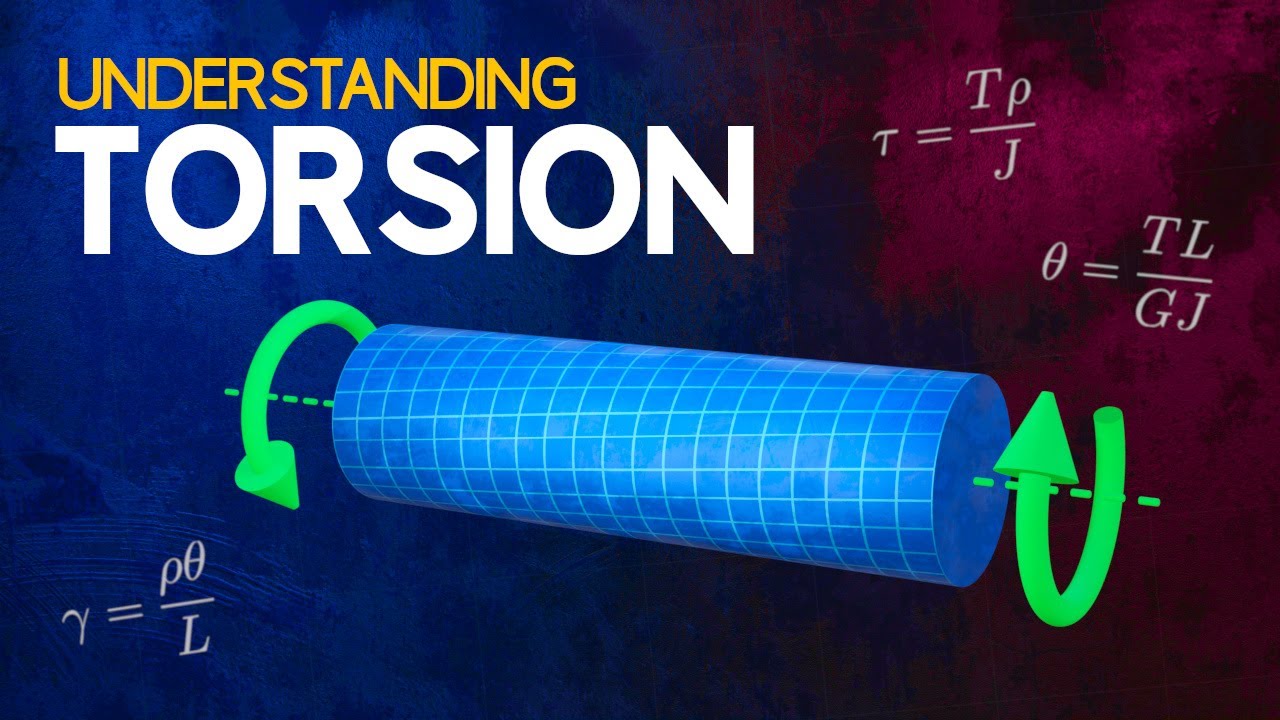
Understanding Torsion
5.0 / 5 (0 votes)