Stress and Strain | Stress strain curve of mild steel | Mechanical Properties of Solids |
Summary
TLDRThis video explores the fundamental concepts of stress and strain in civil engineering, focusing on their role in material behavior under load. It defines stress as force per unit area and strain as the deformation caused by external forces. The video also discusses stress-strain curves, particularly those generated by tensile loads, highlighting key points such as proportional limit, elastic limit, yield point, ultimate strength, and fracture point. These curves are essential for understanding material properties like modulus of elasticity, yield strength, and ductility, with practical applications in engineering design and testing.
Takeaways
- 😀 Stress is the force per unit area experienced by a material when an external force is applied.
- 😀 Strain refers to the deformation of a material due to an applied force and has no units, only indicating a change in shape.
- 😀 The stress-strain curve is a graphical representation of a material’s behavior under load, often focusing on tensile loads.
- 😀 Stress-strain curves help engineers determine key mechanical properties like modulus of elasticity, yield strength, ultimate strength, and ductility.
- 😀 The proportional limit is the point at which the material's stress and strain maintain a linear relationship, described by Young's modulus.
- 😀 The elastic limit is where elastic deformation ends and plastic deformation begins, with the material returning to its original dimensions if the load is removed.
- 😀 The yield point indicates the start of plastic deformation in the material, marking the transition from elasticity to permanent deformation.
- 😀 The ultimate stress or breaking stress is the maximum stress the material can withstand before it starts to neck.
- 😀 The fracture point represents the failure point in the material, where it ultimately breaks.
- 😀 Stress-strain curves are typically generated using universal testing machines to analyze the mechanical properties of materials.
Q & A
What is stress in the context of civil engineering?
-Stress is defined as the force per unit area that a material experiences when an external force is applied. It can result from factors like uneven heating or permanent deformation. The formula for stress is Force divided by Area, and the unit of stress is Newton per square meter (N/m² or Pascals).
How is strain different from stress?
-Strain refers to the deformation a body experiences due to an applied force, and it is dimensionless. Unlike stress, which has units (N/m²), strain is a ratio of the change in length to the original length, and it does not have units.
What does the stress-strain curve represent?
-The stress-strain curve is a graphical representation of how a material behaves when subjected to increasing loads. It helps engineers understand material properties like modulus of elasticity, yield strength, ultimate strength, and ductility under tension or compression.
What is the proportional limit on the stress-strain curve?
-The proportional limit is the point on the stress-strain curve where the material no longer follows Hooke's Law, and the relationship between stress and strain becomes nonlinear. Up to this point, the material deforms proportionally to the applied stress.
What is Young's modulus, and how is it related to the proportional limit?
-Young's modulus, or the modulus of elasticity, is a measure of the material's stiffness. It is calculated as the slope of the stress-strain curve up to the proportional limit, indicating the material's resistance to elastic deformation.
What happens at the elastic limit on the stress-strain curve?
-At the elastic limit, elastic deformation ends, and plastic deformation begins. If the applied load is removed at this point, the material will return to its original shape. Beyond this point, the material will experience permanent deformation.
How does the yield point relate to the elastic limit?
-The yield point is similar to the elastic limit, as both indicate the transition from elastic to plastic deformation. Beyond the yield point, the material undergoes permanent, plastic deformation that does not revert once the load is removed.
What is ultimate tensile strength, and where is it found on the stress-strain curve?
-Ultimate tensile strength, or breaking stress, is the highest stress a material can withstand before it begins to neck or weaken. It is represented as the peak of the stress-strain curve, beyond which the material can no longer support the load.
What is the fracture point in the stress-strain curve?
-The fracture point is the point at which the material completely fails and breaks. It represents the final stage of the material’s behavior under stress, where the material reaches its breaking point.
Why are stress-strain curves important for engineers?
-Stress-strain curves are crucial for engineers because they provide essential information about a material’s mechanical properties, such as elasticity, strength, and ductility. This data helps engineers design safer and more efficient structures by understanding how materials will behave under various loads.
Outlines
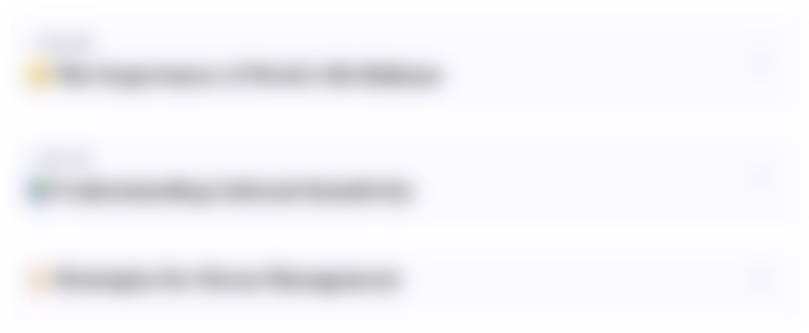
This section is available to paid users only. Please upgrade to access this part.
Upgrade NowMindmap
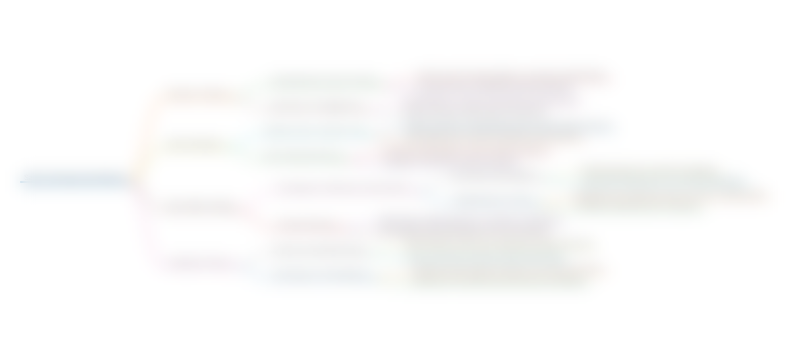
This section is available to paid users only. Please upgrade to access this part.
Upgrade NowKeywords
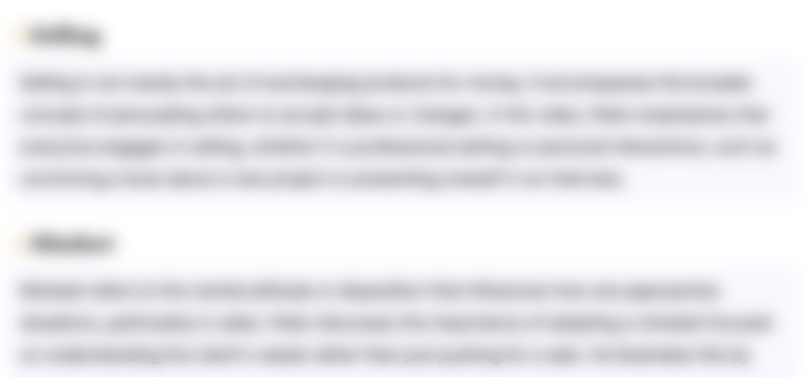
This section is available to paid users only. Please upgrade to access this part.
Upgrade NowHighlights
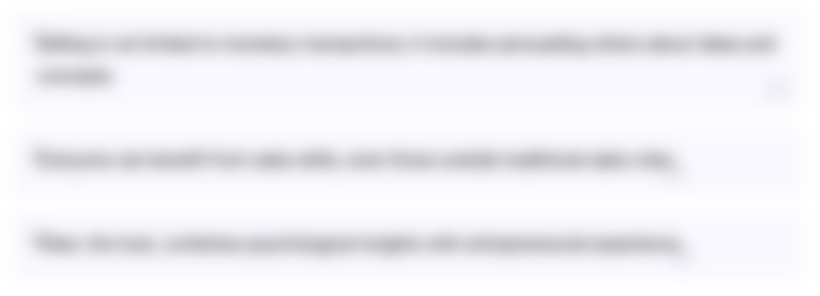
This section is available to paid users only. Please upgrade to access this part.
Upgrade NowTranscripts
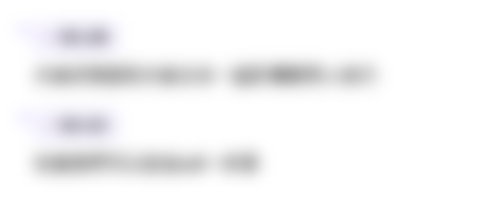
This section is available to paid users only. Please upgrade to access this part.
Upgrade NowBrowse More Related Video
5.0 / 5 (0 votes)