How to apply PVA (Polyvinyl Alcohol) Release Agent to Fiberglass Mold
Summary
TLDRIn this tutorial, the presenter demonstrates how to apply polyvinyl alcohol (PVA) for mold releasing. They showcase two types of PVA from different brands, explaining why they prefer one over the other. The process involves applying three thin layers of PVA using a spray gun, ensuring proper air pressure settings for an even application. The video emphasizes the importance of thin, consistent layers to avoid issues with irregularities or incomplete coverage. After the PVA layers dry, the presenter proceeds to clean the tools and prepares for the next step in the mold-making process.
Takeaways
- 😀 The video demonstrates how to apply polyvinyl alcohol (PVA) for releasing film during the mold-making process.
- 😀 The speaker uses two variants of PVA, one from Turkey and one from the USA, preferring the latter for personal use due to its better quality, despite the price difference.
- 😀 A minimum of three thin layers of PVA is recommended for proper mold release, but the layers should not be too thick.
- 😀 The speaker explains the importance of applying PVA with a spray gun for a smooth finish, as brushing leads to irregularities.
- 😀 The spray gun setup should have the air pressure reduced to around 4 bars for optimal spraying results.
- 😀 The speaker advises not to combine different brands of PVA, even though they contain the same substance, to avoid potential issues.
- 😀 Applying PVA should be done carefully, with the first layer serving as a base, and subsequent layers added after drying.
- 😀 PVA should be applied thinly to avoid it dripping down and causing a mess, and waiting for each layer to dry is crucial.
- 😀 After the first coat is dry, a second layer of PVA should be applied and left to dry for 30 to 45 minutes depending on ambient temperature.
- 😀 The third and final layer of PVA should be applied similarly, and once dry, the tools can be cleaned with water since PVA is water-soluble.
- 😀 The final goal is to proceed with laminating and removing the laminate from the mold in a later step, with the video promising a follow-up episode.
Q & A
Why does the speaker prefer the polyvinyl alcohol (PVA) from the USA over the one from Turkey?
-The speaker prefers the USA variant because it works better for them, even though the Turkish variant is cheaper. The speaker notes that the cheaper one can still be used but doesn't meet their personal preferences.
What is the recommended method for applying polyvinyl alcohol (PVA) to the mold?
-The recommended method is to apply PVA using a spray gun. This ensures a smooth, even coating. Applying with a brush is an option but can lead to irregularities on the surface.
How many layers of PVA should be applied to the mold, and what is the thickness of each layer?
-A minimum of three layers should be applied. Each layer should be thin, not too thick, to ensure proper adhesion and prevent issues like PVA falling off.
Why is it important to apply PVA in thin layers?
-Applying PVA in thin layers ensures it adheres properly to the mold. Thick layers can cause the PVA to fall off and may lead to difficulties in further applications, like lamination.
What issue does the speaker face when using thick layers of PVA?
-Thick layers of PVA can result in the substance falling off the mold, making it difficult to achieve the desired mold release effect and causing other complications in the process.
How does the speaker check if the PVA layer is dry enough to proceed with the next coat?
-The speaker checks the dryness by touching the mold in different spots and ensuring it feels dry and slightly glossy. If the layer is not dry, the next coat should not be applied.
What air pressure setting does the speaker recommend for the spray gun when applying PVA?
-The speaker recommends setting the air pressure to around 4 bars. This is crucial for proper spray application, as higher pressures (like 7-8 bars) will cause PVA to fly off.
Why is it important to clean the spray gun after applying PVA?
-Cleaning the spray gun is important because PVA is water-soluble, and residual PVA in the gun can affect future applications. Cleaning with water ensures that no PVA remains in the equipment.
What is the drying time for each layer of PVA, and how does it vary?
-The drying time for each layer of PVA is approximately 30 to 45 minutes, depending on the ambient temperature. The speaker typically waits 45 minutes between coats.
What will the speaker cover in the next video?
-In the next video, the speaker will demonstrate how to apply the laminate to the mold and how to remove the laminate from the mold after the PVA has dried.
Outlines
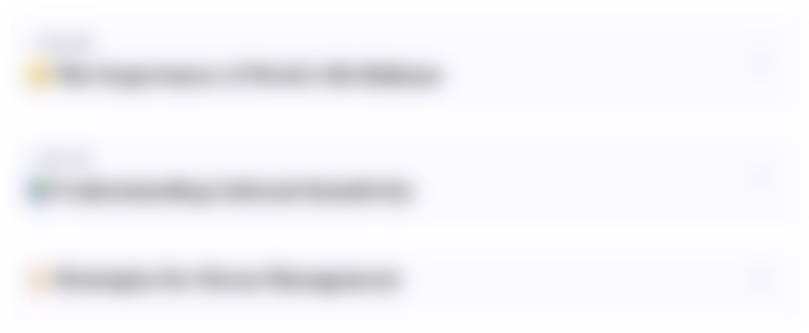
This section is available to paid users only. Please upgrade to access this part.
Upgrade NowMindmap
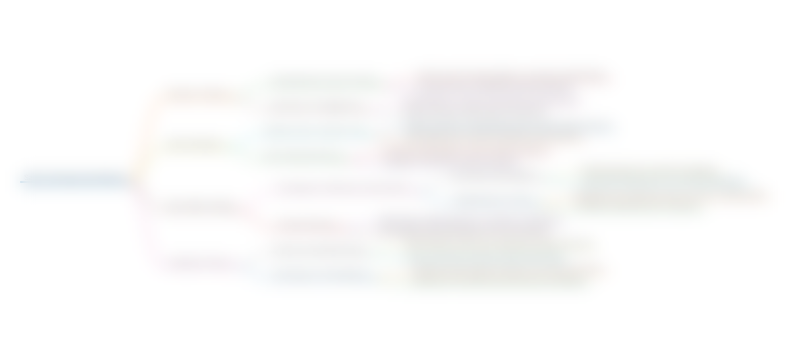
This section is available to paid users only. Please upgrade to access this part.
Upgrade NowKeywords
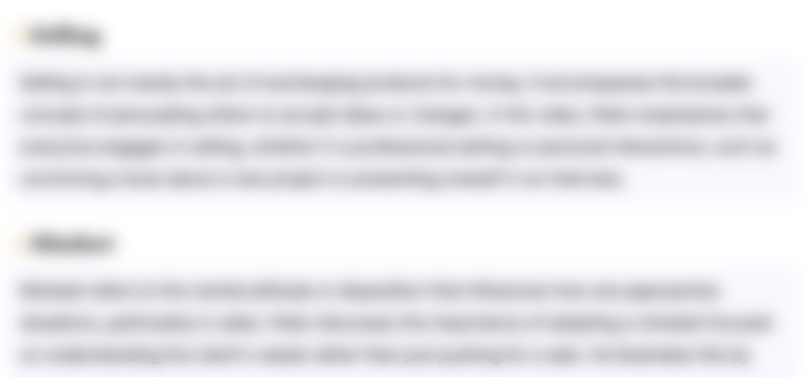
This section is available to paid users only. Please upgrade to access this part.
Upgrade NowHighlights
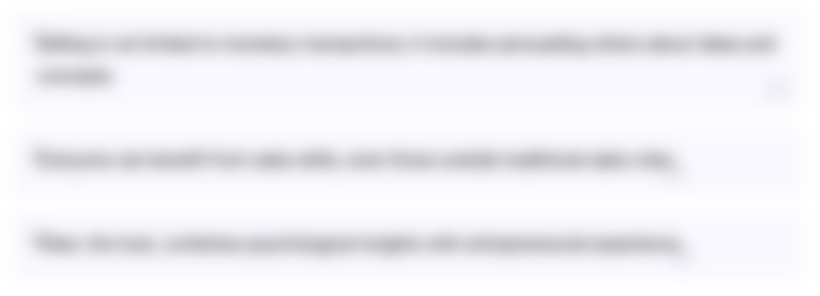
This section is available to paid users only. Please upgrade to access this part.
Upgrade NowTranscripts
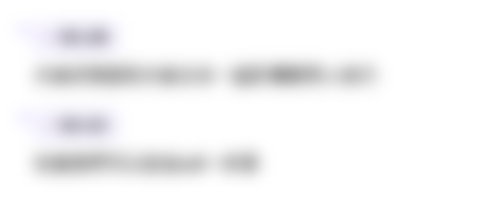
This section is available to paid users only. Please upgrade to access this part.
Upgrade NowBrowse More Related Video

Latihan 1 MasterCam X5 | Materi Belajar CNC | Membuat Blok Cekung
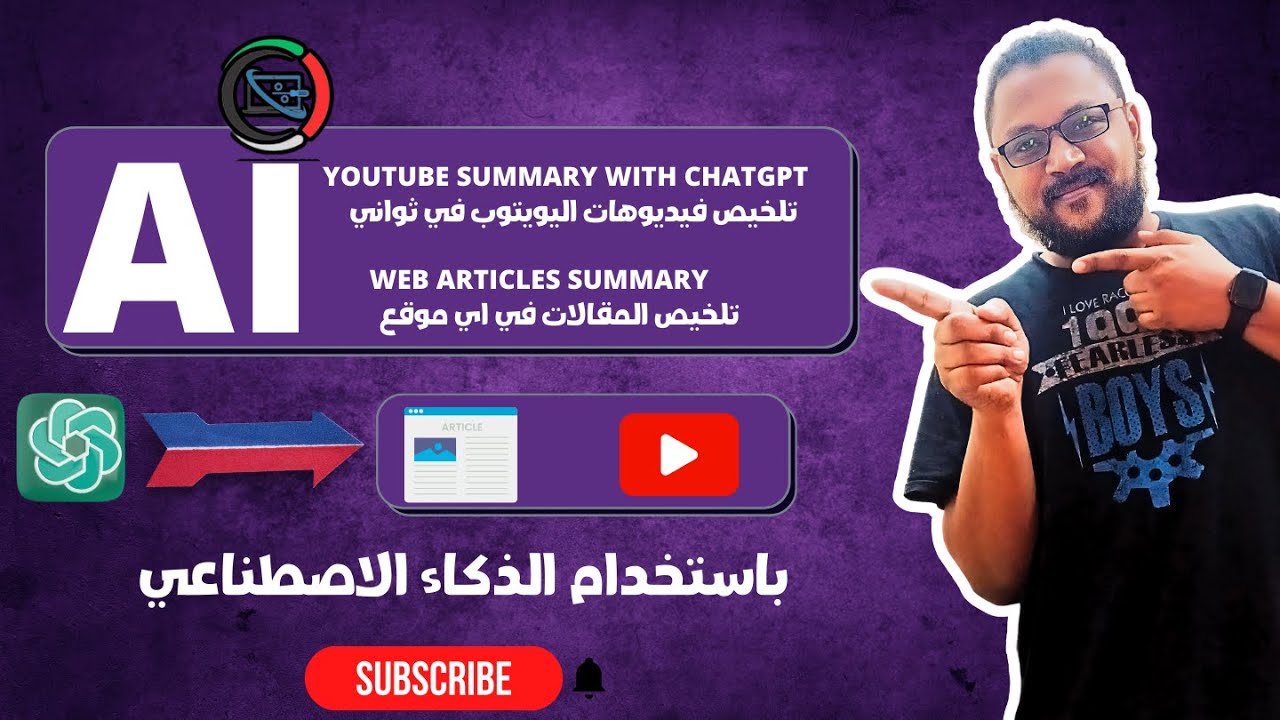
تلخيص فيديوهات اليوتيوب في ثواني باستخدام الذكاء الاصطناعي | YouTube Summary with ChatGPT

Dicas de transformação #9 Fechamento das injetoras
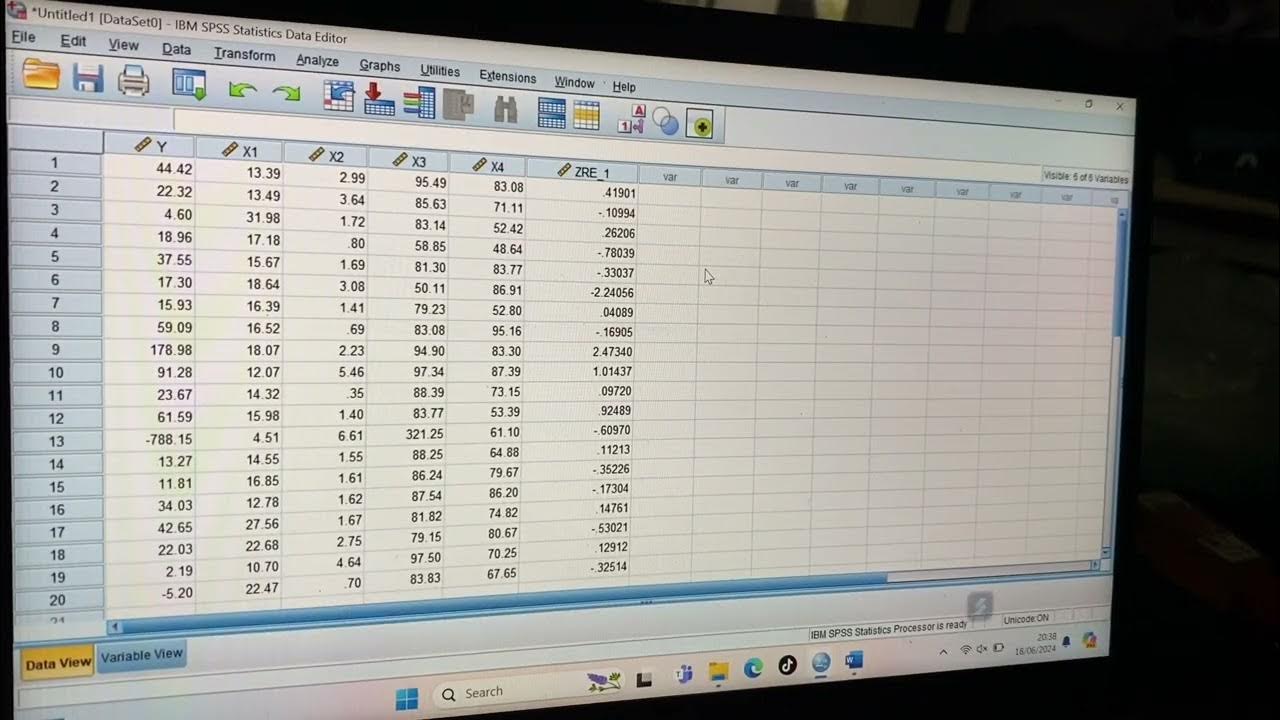
Tutorial Menggunakan Spss untuk data Panel
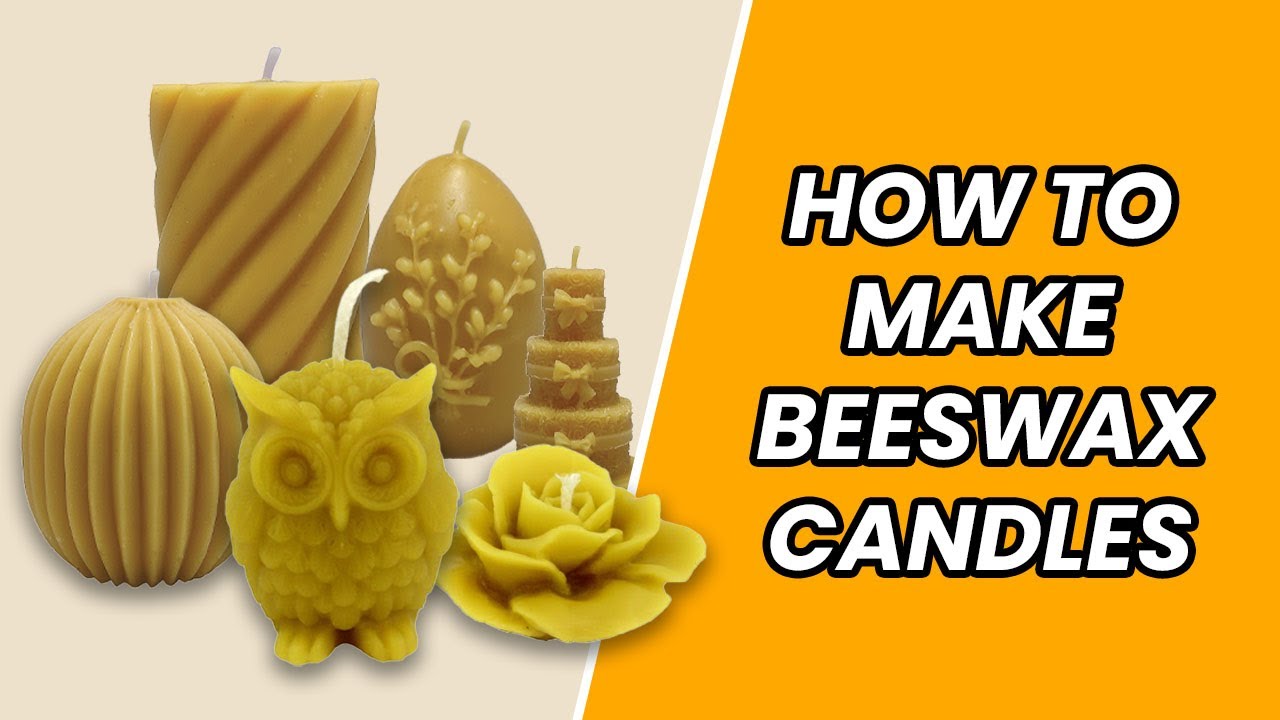
Beekeeping Guide: How To Use Candle Moulds To Create Beeswax Candles

Cara mencari angka yang mesti diinput di Excel dengan Goal Seek
5.0 / 5 (0 votes)