Auditing inventory - part 3 - product costing for manufacturing firms
Summary
TLDRIn this video, Amanda discusses the complexities of auditing inventory in manufacturing firms, focusing on raw materials, work-in-process, and finished goods. She emphasizes the importance of understanding accounting methods like FIFO, LIFO, and weighted average cost, as well as the challenges of product costing and overhead allocation. Amanda also highlights the need for auditors to consider jurisdictional differences, audit accounting estimates, and reassess inventory costing methods to ensure accuracy. The video is a comprehensive guide to auditing manufacturing inventory, combining financial and management accounting principles to ensure thorough evaluations and compliance.
Takeaways
- 😀 Auditing inventory in manufacturing firms is more complex due to the need to account for raw materials, work in process, and finished goods.
- 😀 Management accounting plays a crucial role in auditing, especially in understanding the costing methods for inventory like direct materials, labor, and overhead costs.
- 😀 Different inventory accounting methods (weighted average cost, FIFO, and LIFO) need to be considered, with jurisdictional differences such as LIFO being unacceptable under IFRS but allowed under US GAAP.
- 😀 The cost of inventory can be valued at the lower of cost or net realizable value (NRV) under IFRS, while under US GAAP, it's the lower of cost or market value.
- 😀 Auditors must thoroughly understand costing methods, including plant-wide, departmental, and activity-based costing, to ensure accurate inventory valuation.
- 😀 When auditing finished goods inventory, auditors should recalculate costs by examining invoices, orders, and records of raw materials used, as well as conduct variance analysis for direct materials and labor.
- 😀 Variance analysis helps identify discrepancies between budgeted and actual costs, helping to adjust inventory valuations and ensure accuracy.
- 😀 Auditors must assess management's assumptions, methods, and data used in product costing, particularly focusing on the overhead allocation and cost drivers.
- 😀 Inventory valuation errors can lead to problems in both the balance sheet and income statement, such as overstating profit or failing to meet debt covenants.
- 😀 Auditors need to ensure the accuracy of both financial and management accounting when auditing inventory, as errors can affect both the valuation and financial reporting of a manufacturing firm.
Q & A
What are the key types of inventory that need to be audited in a manufacturing firm?
-The key types of inventory in a manufacturing firm that need to be audited are raw materials, work in process (WIP), and finished goods.
Why is auditing finished goods more complicated in manufacturing firms?
-Auditing finished goods is more complicated due to accounting method choices, product costing complexity, and jurisdictional differences in inventory accounting standards.
What are the three common accounting methods used for inventory valuation?
-The three common accounting methods for inventory valuation are Weighted Average Cost, FIFO (First In, First Out), and LIFO (Last In, First Out).
What is the key difference between IFRS and U.S. GAAP regarding inventory accounting?
-The key difference is that under IFRS, LIFO is not permitted, while it is allowed under U.S. GAAP.
What is the term used under IFRS to describe the method of inventory valuation that compares cost to net realizable value?
-Under IFRS, the method of inventory valuation is referred to as the 'lower of cost or net realizable value (NRV)'.
What are the essential components of product costing in manufacturing firms?
-The essential components of product costing are direct materials (DM), direct labor (DL), and overhead costs (OH).
What are some common methods of allocating overhead in manufacturing firms?
-Common methods of allocating overhead include plant-wide overhead, departmental overhead, and activity-based costing (ABC).
Why is variance analysis important when auditing manufacturing inventory?
-Variance analysis is important because it helps auditors assess if the company is accurately reflecting its product costs, identifying differences between actual costs and budgeted costs, and detecting inefficiencies.
What does the acronym 'MAD' stand for in the context of auditing accounting estimates?
-In auditing accounting estimates, 'MAD' stands for Method, Assumptions, and Data, which auditors must examine when evaluating estimates used in inventory valuation.
What is the risk of incorrect inventory valuation in the financial statements?
-Incorrect inventory valuation can lead to misstated financial statements, such as overstated or understated profits, which can affect the balance sheet, income statement, and potentially violate debt covenants.
Outlines
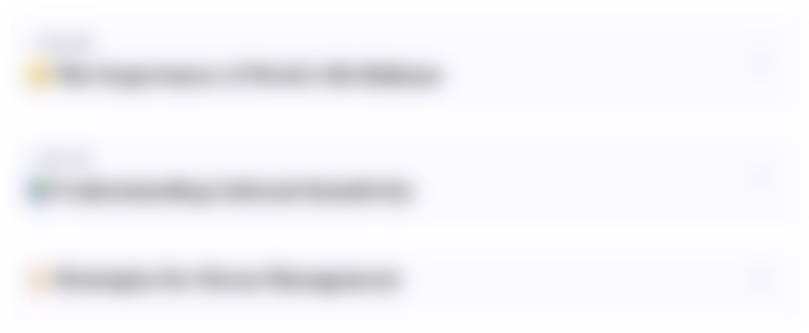
This section is available to paid users only. Please upgrade to access this part.
Upgrade NowMindmap
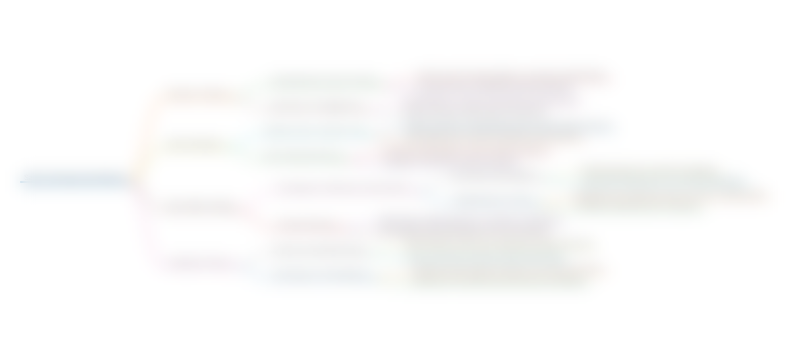
This section is available to paid users only. Please upgrade to access this part.
Upgrade NowKeywords
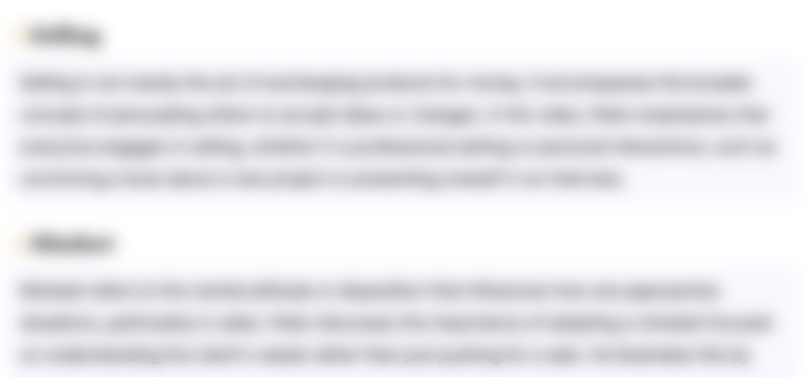
This section is available to paid users only. Please upgrade to access this part.
Upgrade NowHighlights
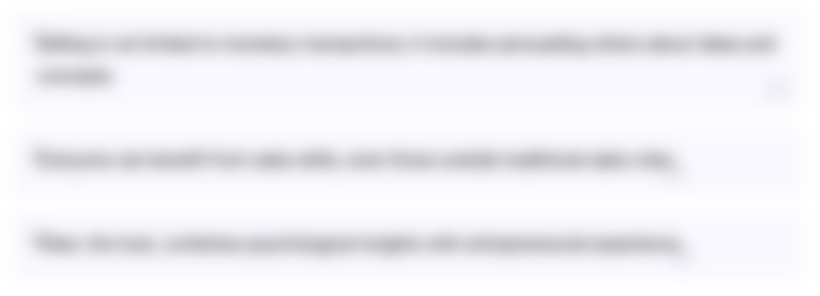
This section is available to paid users only. Please upgrade to access this part.
Upgrade NowTranscripts
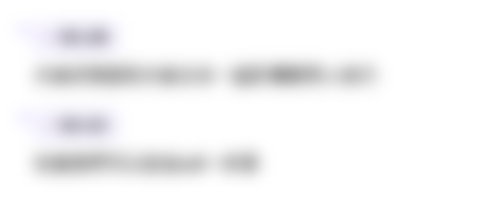
This section is available to paid users only. Please upgrade to access this part.
Upgrade NowBrowse More Related Video

3 Types of Inventory (Raw Materials, WIP, and Finished Goods)
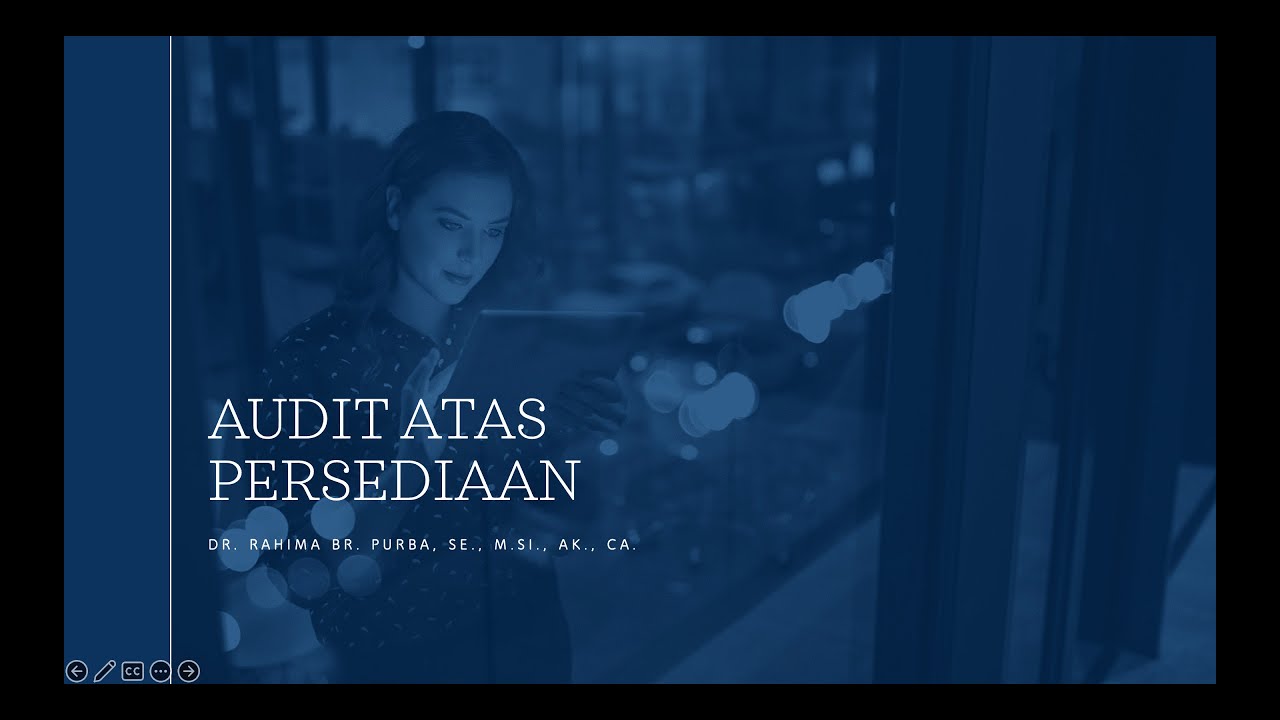
Audit atas Persediaan
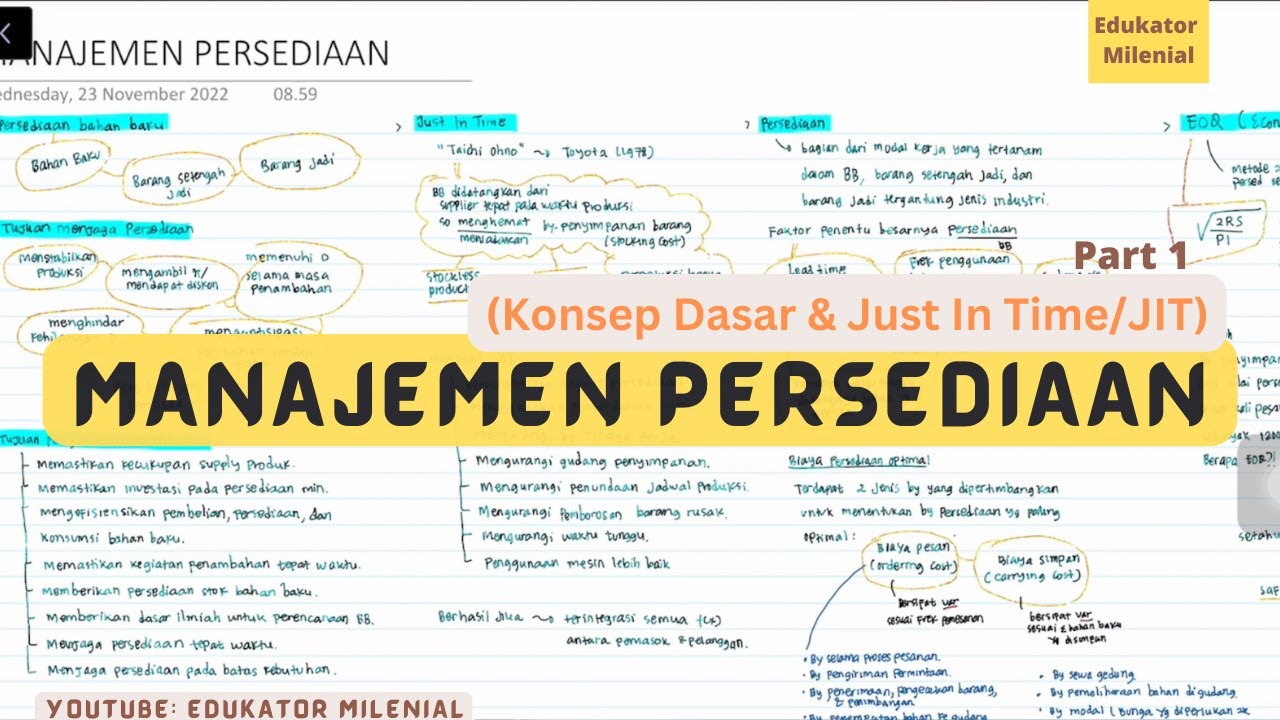
Manajemen Persediaan (Just In Time - JIT)
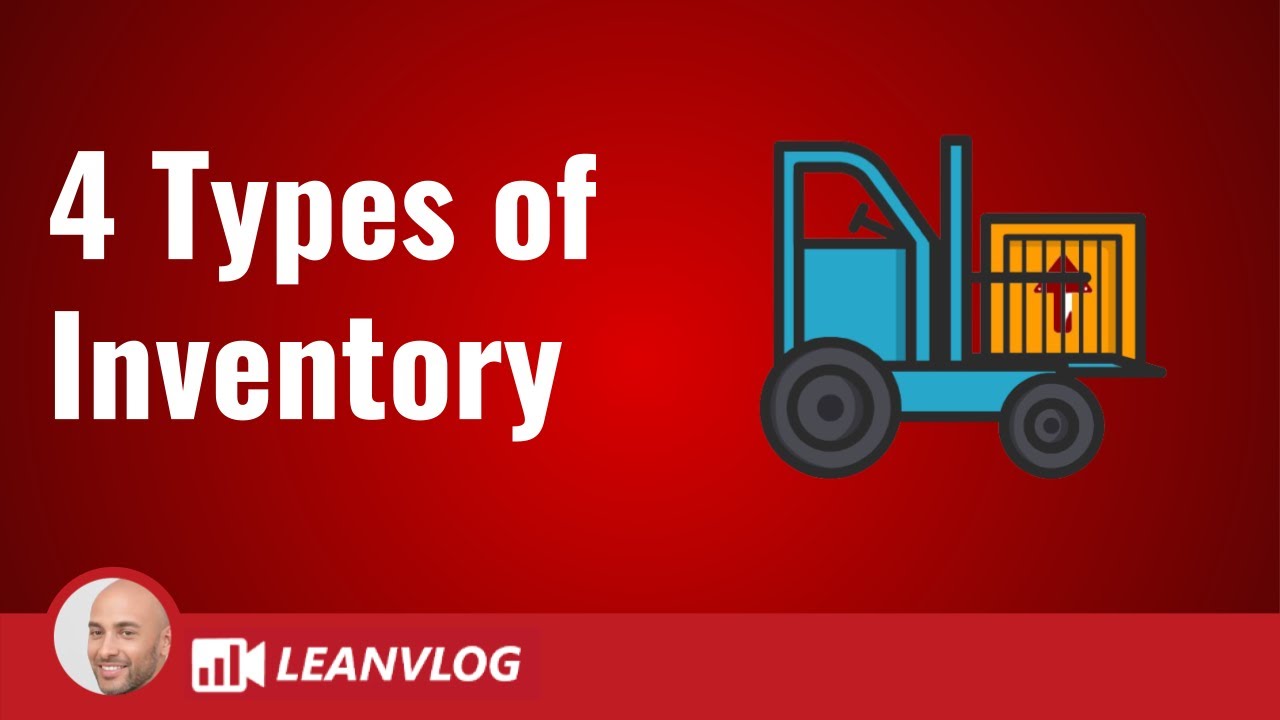
Types of Inventory : The 4 Different Buckets to Know
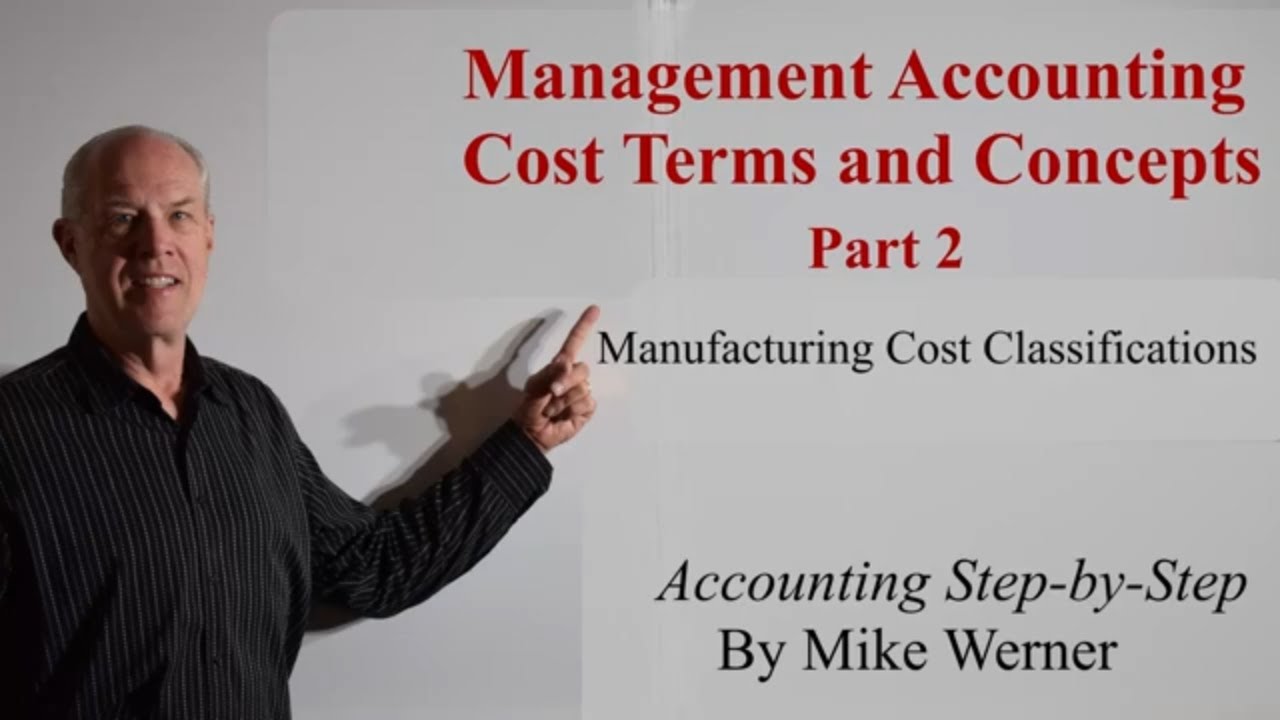
Cost Terms and Concepts in Cost & Management Accounting Part 2, Manufacturing Costs, Mike Werner
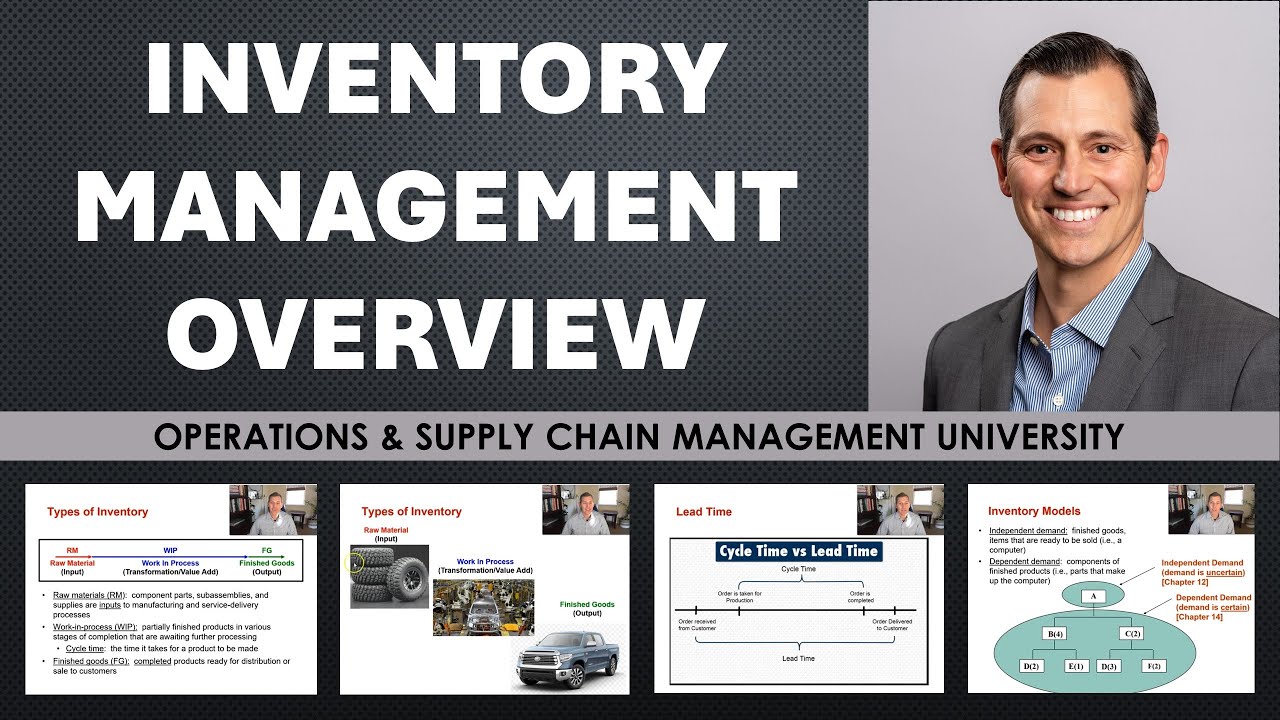
Inventory Management overview in Operations & Supply Chain Management
5.0 / 5 (0 votes)