3 Types of Inventory (Raw Materials, WIP, and Finished Goods)
Summary
TLDRThis video explains the different types of inventory for a manufacturing firm, focusing on the distinction from merchandising firms. It covers three primary inventory categories: Raw Materials (e.g., steel for a bicycle), Work in Process (partially assembled products), and Finished Goods (completed products ready for sale). Using an example from Tommy’s Car Production, the video demonstrates how these inventory types are presented on a balance sheet. The key equation for total inventory is: Raw Materials + Work in Process + Finished Goods = Total Inventory. This breakdown provides insight into the manufacturing inventory management process.
Takeaways
- 😀 Manufacturing firms have different types of inventory compared to merchandising firms, as they produce goods rather than simply buying and selling them.
- 😀 Key components of manufacturing costs include direct materials, direct labor, and manufacturing overhead, all of which contribute to inventory.
- 😀 Inventory in a manufacturing firm is categorized into raw materials, work in process (WIP), and finished goods.
- 😀 Raw materials (RM) are the basic materials used in production, such as steel for making cars.
- 😀 Work in process (WIP) refers to partially assembled or unfinished products that are still being worked on.
- 😀 Finished goods are completed products that are ready for sale, such as a fully assembled car.
- 😀 The flow of inventory in a manufacturing firm goes from raw materials to work in process to finished goods.
- 😀 In financial reporting, inventory categories are typically broken down on the balance sheet, showing the value of raw materials, WIP, and finished goods.
- 😀 A simple equation to understand inventory is: Raw Materials + Work in Process + Finished Goods = Total Inventory.
- 😀 In a sample balance sheet, Tommy’s Car Production has $40,000 in raw materials, $35,000 in work in process, and $50,000 in finished goods, totaling $125,000 in inventory.
- 😀 Understanding these inventory categories helps manufacturers track the progress of goods through production and their value at each stage.
Q & A
What is the primary difference between a manufacturing firm and a merchandising firm regarding inventory?
-A manufacturing firm not only buys inventory but also transforms raw materials into finished products through processes like assembly, labor, and overhead costs. In contrast, a merchandising firm simply purchases inventory and resells it without any transformation.
What are the three main types of inventory in a manufacturing firm?
-The three main types of inventory in a manufacturing firm are raw materials (RM), work in process (WIP), and finished goods (FG).
What does the term 'raw materials' refer to in the context of manufacturing?
-Raw materials refer to the basic materials, such as steel or fabric, that are used to create a product. These materials are the starting point in the production process.
How does 'work in process' differ from 'raw materials'?
-Work in process refers to products that have undergone some manufacturing steps but are incomplete. In contrast, raw materials are unprocessed and haven't yet been worked on.
Can you explain the concept of 'work in process' with an example?
-Work in process refers to products that are partially assembled or in the middle of being manufactured but aren't yet finished. For example, a bicycle that is half-assembled, with parts added but not yet fully completed, is in work in process.
What is meant by 'finished goods' in a manufacturing firm?
-Finished goods are products that are fully completed and ready for sale. They have undergone all manufacturing processes and are now ready for delivery to customers.
How does the inventory flow in a manufacturing firm?
-In a manufacturing firm, inventory flows from raw materials to work in process to finished goods. This progression represents the transformation of basic materials into completed products.
What is the equation used to calculate total inventory in a manufacturing firm?
-The total inventory is calculated by adding the values of raw materials, work in process, and finished goods. The equation is: Raw Materials + Work in Process + Finished Goods = Total Inventory.
Can you provide an example of how inventory is broken down on a balance sheet?
-For example, in Tommy's Car Production, the balance sheet might show inventory broken down as follows: $40,000 in raw materials, $35,000 in work in process, and $50,000 in finished goods, resulting in a total inventory of $125,000.
Why is it important to break down inventory into these categories (raw materials, work in process, finished goods)?
-Breaking down inventory into these categories helps manufacturing firms assess the stage of production for their goods, manage costs effectively, and determine the value of assets at different stages of the production process.
Outlines
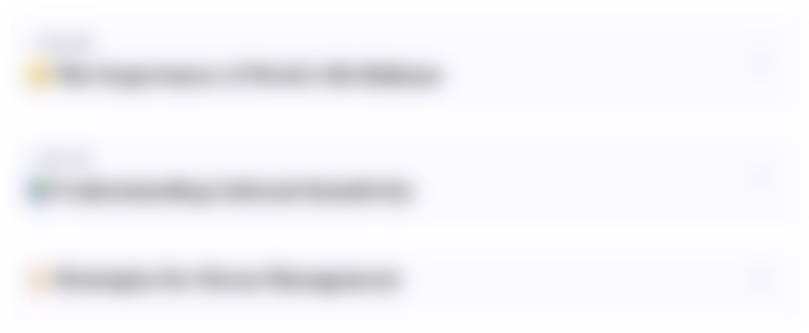
This section is available to paid users only. Please upgrade to access this part.
Upgrade NowMindmap
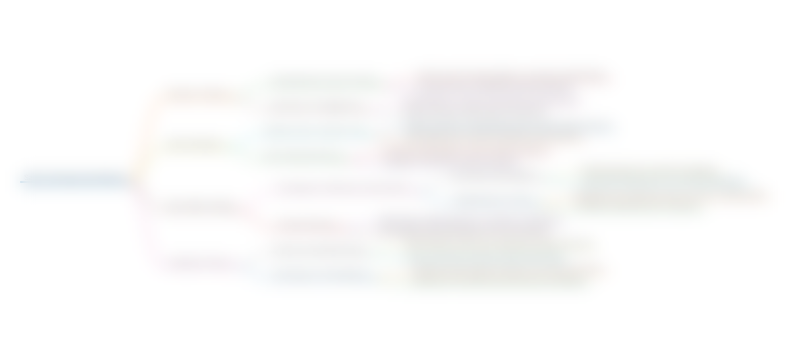
This section is available to paid users only. Please upgrade to access this part.
Upgrade NowKeywords
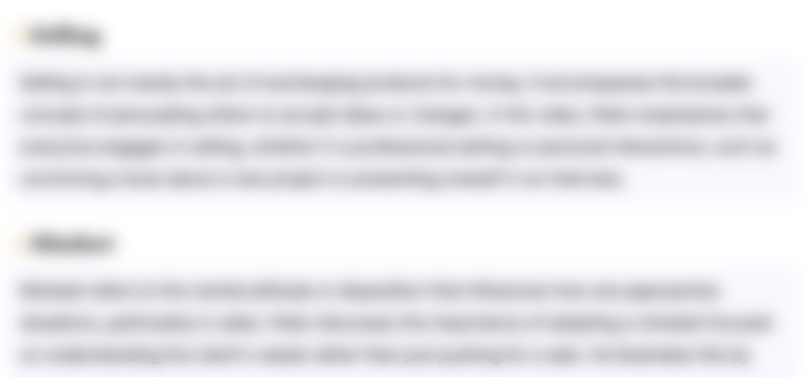
This section is available to paid users only. Please upgrade to access this part.
Upgrade NowHighlights
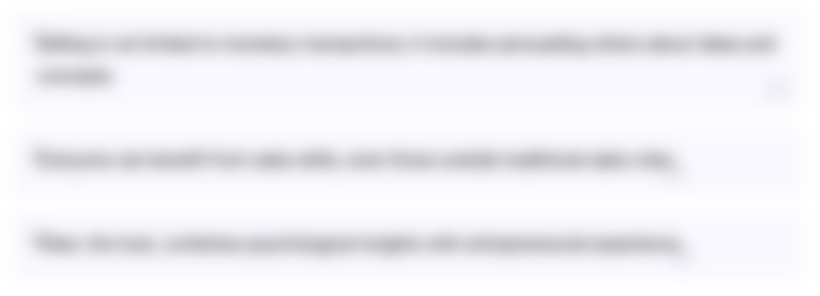
This section is available to paid users only. Please upgrade to access this part.
Upgrade NowTranscripts
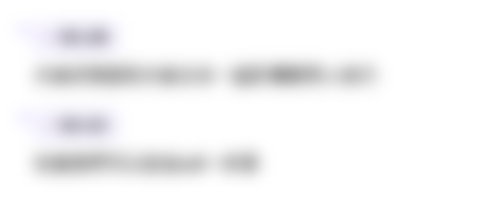
This section is available to paid users only. Please upgrade to access this part.
Upgrade NowBrowse More Related Video
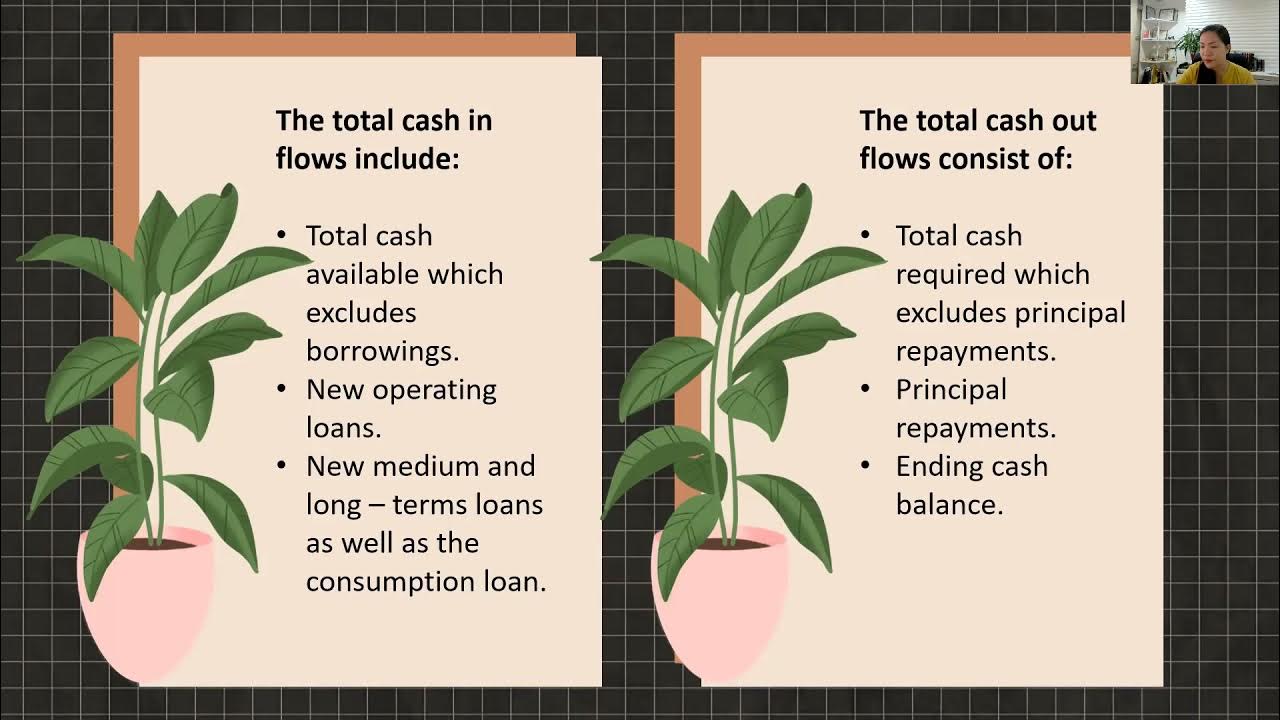
Financial Statements (September 30, 2021)

INVENTORY & COST OF GOODS SOLD
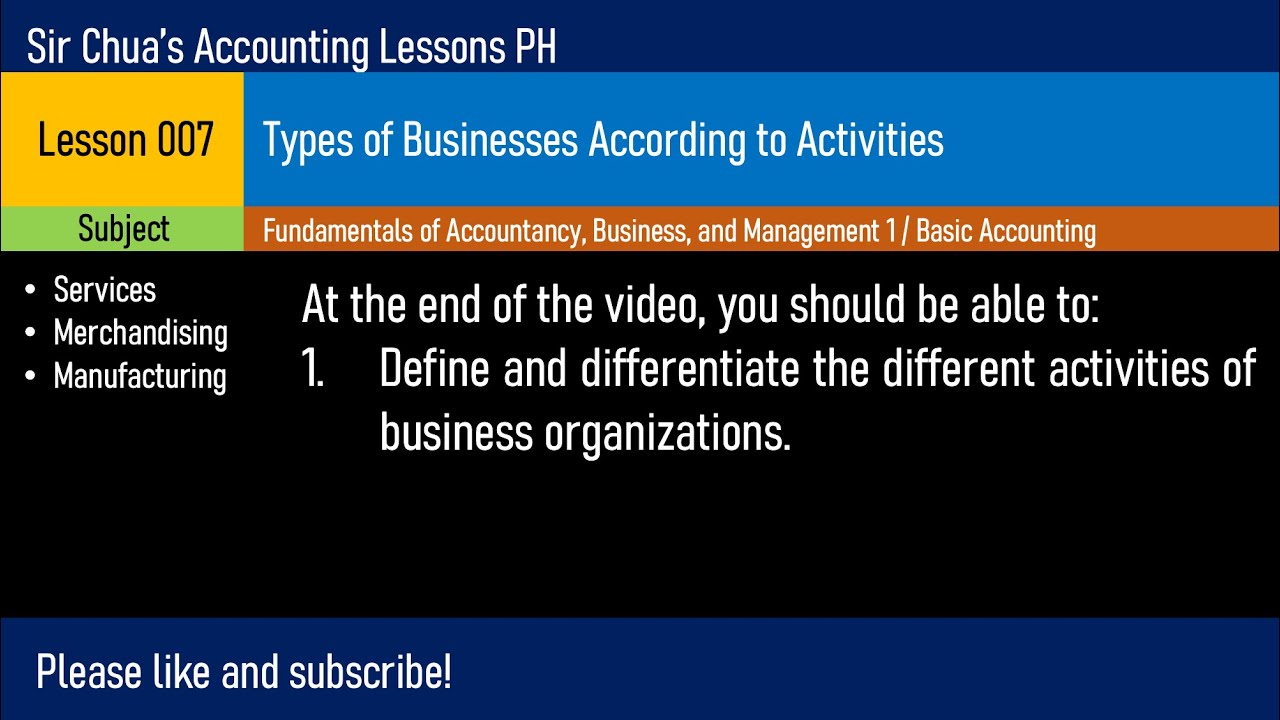
Lesson 007 - Types of Businesses According to Activities (Service, Merchandising, Manufacturing)
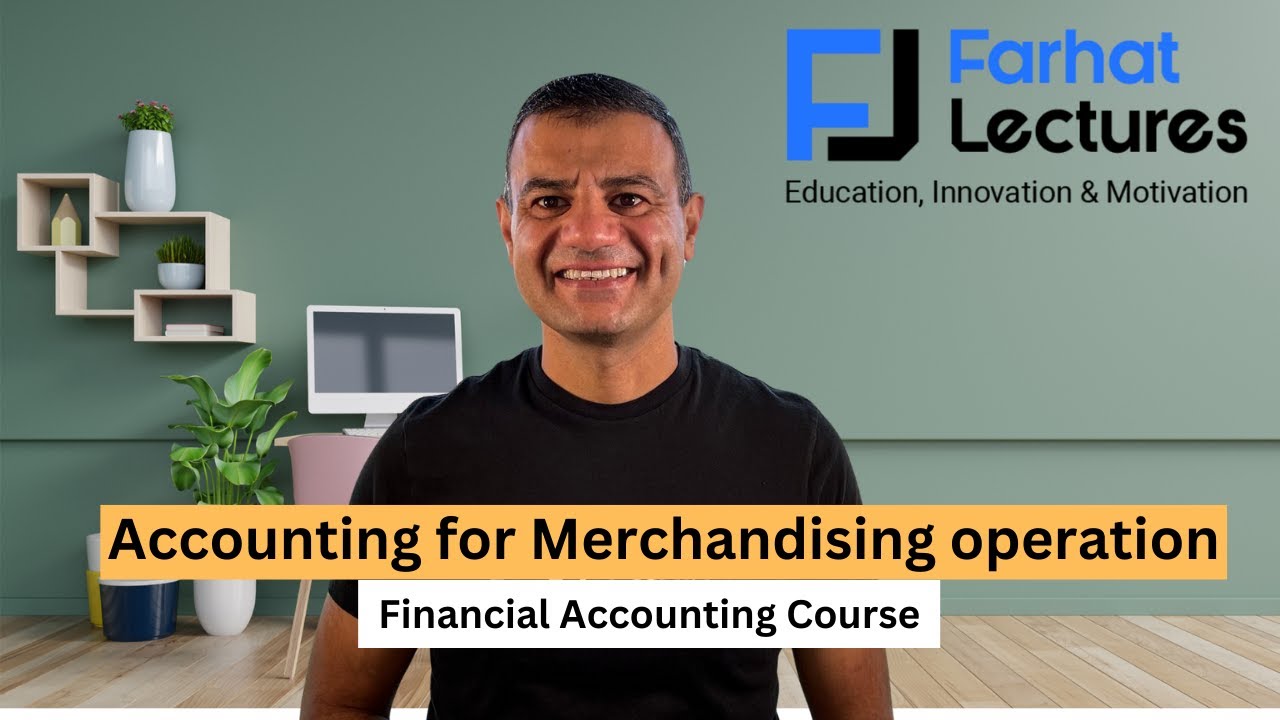
Accounting for Merchandising operation

Auditing inventory - part 3 - product costing for manufacturing firms
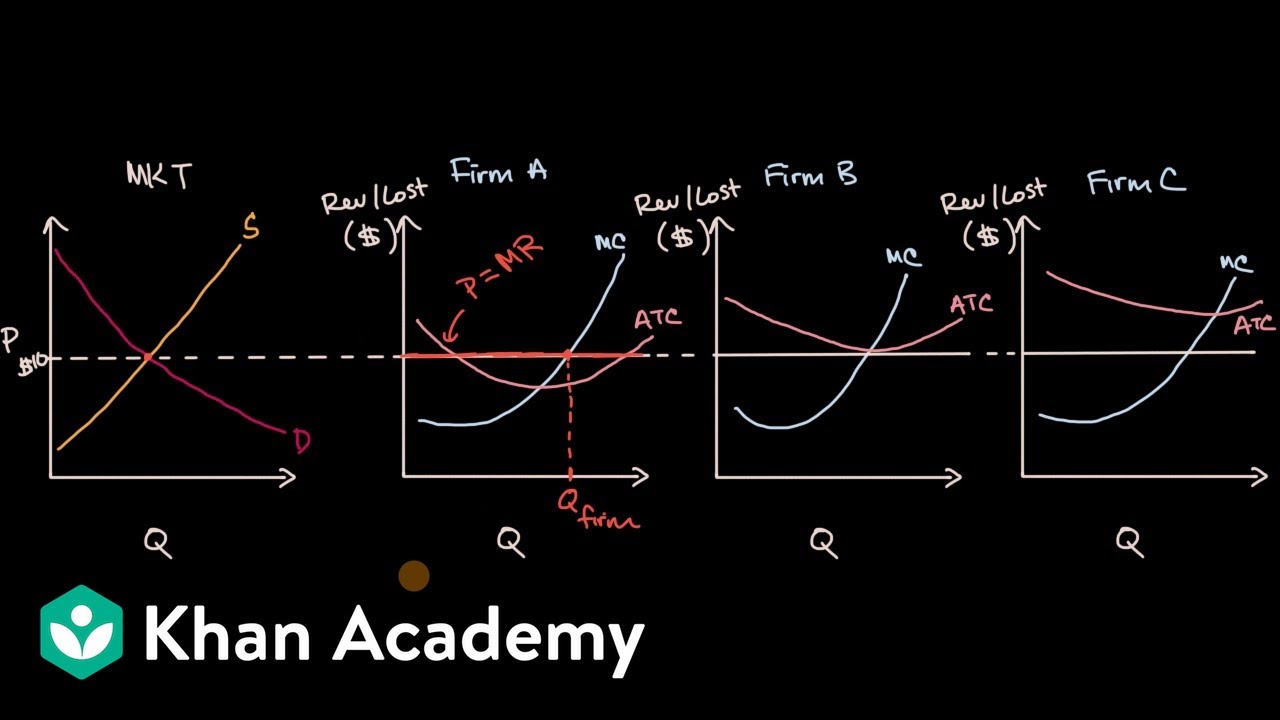
Economic profit for firms in perfectly competitive markets | Microeconomics | Khan Academy
5.0 / 5 (0 votes)