Inventory Management overview in Operations & Supply Chain Management
Summary
TLDRThis video script delves into the essential concepts of inventory management, explaining its functions, costs, and types. It covers raw materials, work-in-process, and finished goods, emphasizing the importance of balancing inventory investment with customer service. The script outlines the complexities of inventory management, including forecasting, ordering decisions, and the costs of holding, ordering, and stockouts. It also differentiates between independent and dependent demand, highlighting how these impact forecasting and inventory planning. Overall, the script provides a comprehensive overview of effective inventory management strategies crucial for businesses to optimize operations and meet customer demand.
Takeaways
- ๐ Inventory is any asset held for future use or sale, and its management is crucial for balancing investment and customer service.
- ๐ Firms typically invest around 30% of their assets and up to 90% of their working capital in inventory, making inventory management a significant cost factor.
- ๐ Effective inventory management involves planning, coordinating, controlling storage, handling, and movement to meet customer demand efficiently.
- ๐ A key goal in inventory management is to maintain the right balance between inventory levels and customer service, preventing both shortages and excess stock.
- ๐ Inventory serves several functions: meeting anticipated customer demand, decoupling production processes, taking advantage of quantity discounts, and hedging against inflation.
- ๐ Raw materials, work-in-process (WIP), and finished goods are the three main types of inventory, each playing a critical role in the production process.
- ๐ Cycle time is the actual time spent producing a product, while lead time includes the entire process from ordering to delivery and is typically longer than cycle time.
- ๐ Inventory management decisions revolve around two main questions: when to order and how much to order, both of which require accurate forecasting and knowledge of lead times.
- ๐ To effectively manage inventory, an organization needs a reliable tracking system, an accurate demand forecast, and an understanding of lead times and costs.
- ๐ Inventory management costs include ordering costs, holding costs, and stock-out costs, each influencing the overall efficiency and profitability of operations.
- ๐ Demand for inventory can be categorized into independent demand (forecasted) and dependent demand (calculated), with independent demand being more uncertain and requiring forecasts.
Q & A
What is the primary objective of inventory management?
-The primary objective of inventory management is to strike a balance between inventory investment and customer service, ensuring that enough inventory is available to meet customer demand without over-investing in stock.
How do inventory functions help a firmโs operations?
-Inventory serves several functions such as providing a selection of goods for anticipated customer demand, decoupling parts of the production process, allowing for quantity discounts, and hedging against inflation by locking in prices.
What are the three main types of inventory?
-The three main types of inventory are raw materials, work in process (WIP), and finished goods. Raw materials are inputs that havenโt been processed, WIP has undergone some transformation but isnโt finished, and finished goods are completed products ready for sale or distribution.
What is the difference between cycle time and lead time?
-Cycle time refers to the time it takes to manufacture a product, while lead time includes the entire process from ordering, manufacturing, shipping, and invoicing. Lead time is generally longer than cycle time.
Why is inventory management considered costly for firms?
-Inventory management is costly because a significant portion of a firmโs assets, often up to 90% of working capital, is tied up in inventory. Additionally, maintaining inventory involves financing costs, storage, insurance, and the risk of obsolescence or waste.
How do inventory managers decide when to order items?
-Inventory managers decide when to order items based on factors like inventory levels, demand forecasts, lead times, and safety stock requirements. A reliable forecast of demand and knowledge of lead times are crucial for making these decisions.
What is a stock-out and why is it a concern?
-A stock-out occurs when a product is unavailable to meet customer demand. It is a concern because it can lead to lost sales, customer dissatisfaction, and potential loss of business to competitors.
What are the key inventory management costs to consider?
-The key inventory management costs include ordering costs (placing orders), holding costs (storing inventory), unit costs (the cost of acquiring or producing items), and stock-out costs (costs related to unavailable products).
What is dependent demand in inventory management?
-Dependent demand refers to the demand for items that are directly related to the production of another product. For example, if a car manufacturer needs 10,000 cars, it will require 40,000 tires (4 tires per car). Dependent demand can be calculated based on production requirements.
How do quantity discounts affect inventory decisions?
-Quantity discounts encourage firms to buy larger quantities than they need, allowing them to lower per-unit costs. However, this increases inventory levels and holding costs, so managers must balance the benefits of discounts with the cost of holding excess inventory.
Outlines
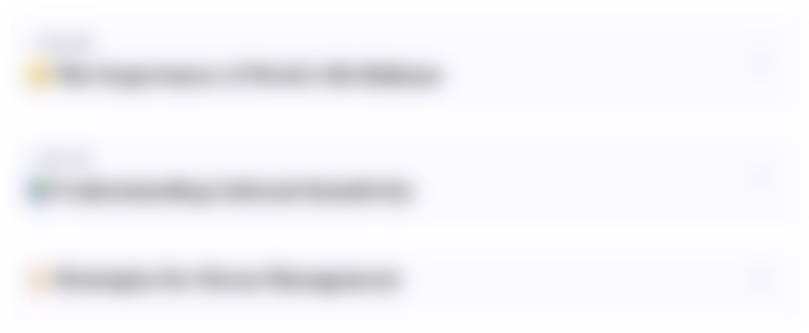
This section is available to paid users only. Please upgrade to access this part.
Upgrade NowMindmap
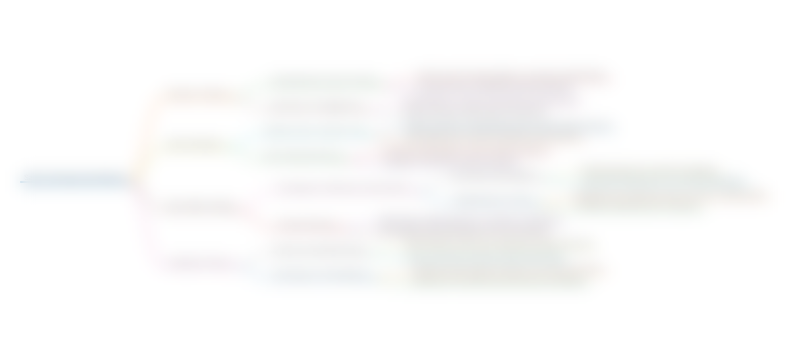
This section is available to paid users only. Please upgrade to access this part.
Upgrade NowKeywords
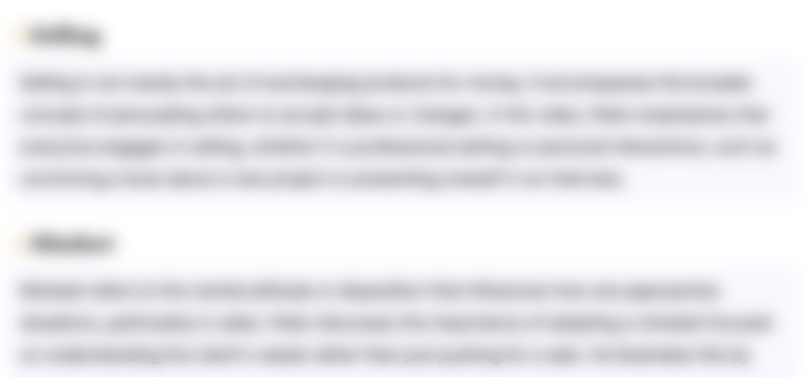
This section is available to paid users only. Please upgrade to access this part.
Upgrade NowHighlights
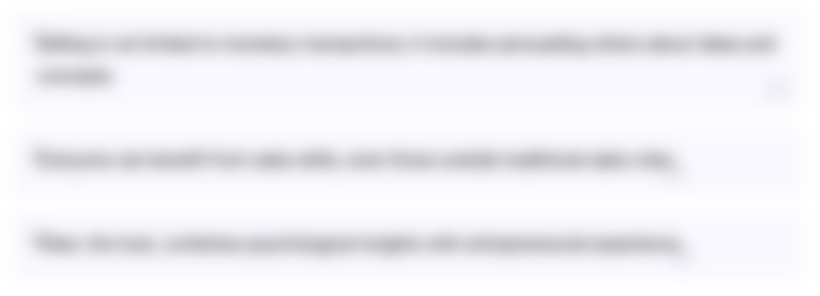
This section is available to paid users only. Please upgrade to access this part.
Upgrade NowTranscripts
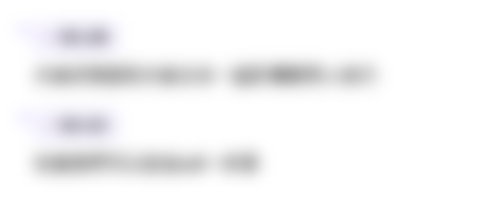
This section is available to paid users only. Please upgrade to access this part.
Upgrade Now5.0 / 5 (0 votes)