Types of Inventory : The 4 Different Buckets to Know
Summary
TLDRThis video emphasizes the importance of effective inventory management, explaining that low inventory should be balanced with the need to satisfy customer demand. It covers four key types of inventory: raw materials, work in process (WIP), finished goods, and auxiliary/maintenance materials. Each type requires different management strategies to ensure a lean, efficient production process and avoid disruptions. The video highlights the role of tools like batch reduction and lean production in maintaining low WIP inventory, while underscoring the significance of forecasting and sales in managing finished goods. Viewers are encouraged to explore further resources linked in the description.
Takeaways
- 😀 Managing inventory at the lowest possible level is crucial but must not compromise customer satisfaction.
- 😀 There are four main types of inventory: raw materials, work in process, finished goods, and auxiliary materials.
- 😀 Raw materials, components, and sub-assemblies are expensive and should be minimized to reduce costs, but production should not halt due to lack of materials.
- 😀 Work in process (WIP) inventory should be kept lean, which can be achieved using lean tools like batch reduction, cell design, and SMED.
- 😀 Finished goods inventory is often the most expensive, including production costs, and must be managed carefully to meet demand efficiently.
- 😀 Sales and forecasting departments are vital in managing finished goods inventory and avoiding overstocking or stockouts.
- 😀 Auxiliary and maintenance materials inventory, though essential, does not significantly impact the overall inventory value.
- 😀 Optimizing inventory management requires tailored methods for each type of inventory.
- 😀 Inventory management should focus on meeting customer demand without overstocking or understocking.
- 😀 Businesses must find a balance between maintaining minimal inventory levels and avoiding production disruptions.
- 😀 Understanding the different types of inventory and how to manage them effectively is key to operational success.
Q & A
What is the main goal of inventory management?
-The main goal of inventory management is to maintain the lowest possible inventory levels while ensuring that customer demand is always met, thereby avoiding both overstocking and stockouts.
What is the risk of focusing too much on low inventory?
-Focusing too much on low inventory can lead to crises for both the company and customers, as production may stop due to a lack of materials, or customer demands may not be fulfilled in time.
What are the four types of inventory discussed in the video?
-The four types of inventory are raw materials, work in process (WIP), finished goods, and auxiliary/maintenance materials.
Why should raw materials and components be kept in low inventory levels?
-Raw materials and components should be kept at low levels to reduce costs, but inventory must be managed carefully to avoid halting the production process due to material shortages.
What is the goal for managing work in process (WIP) inventory?
-The goal for managing WIP inventory is to keep it as low as possible while ensuring that production meets customer demand. Lean production practices help achieve this goal.
How can lean tools help manage work in process (WIP) inventory?
-Lean tools such as batch reduction, cell design, SMED, and TPM (Total Productive Maintenance) can help streamline production processes and minimize WIP inventory by improving efficiency and reducing waste.
Why is the management of finished goods inventory critical?
-Finished goods inventory is critical because it includes all the production costs, and poor management can lead to overstocking, understocking, or missed sales opportunities. Sales and forecasting departments play a key role in this.
What role do sales and forecasting departments play in managing finished goods inventory?
-Sales and forecasting departments help predict customer demand and ensure that finished goods inventory is stocked in the right amounts, preventing both excess inventory and stockouts.
What items are typically found in the auxiliary and maintenance materials inventory?
-Auxiliary and maintenance materials include spare parts, oils, protective devices for employees, and office supplies—items that support the company's operations but do not significantly affect overall inventory costs.
Why is it important to optimize inventory management for each type of inventory?
-Optimizing inventory management for each type of inventory ensures that businesses can meet customer demand while minimizing excess costs. Each type requires specific management methods tailored to its unique role in the production process.
Outlines
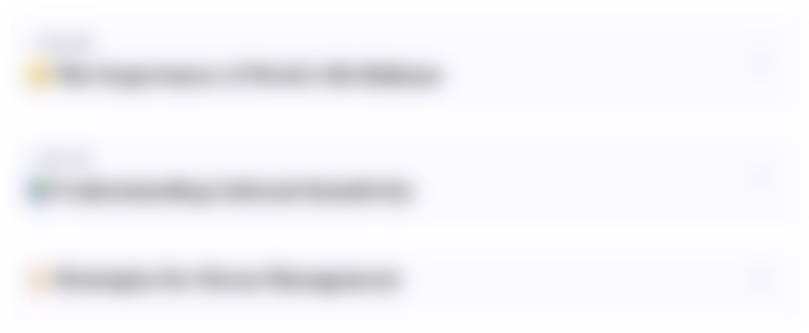
This section is available to paid users only. Please upgrade to access this part.
Upgrade NowMindmap
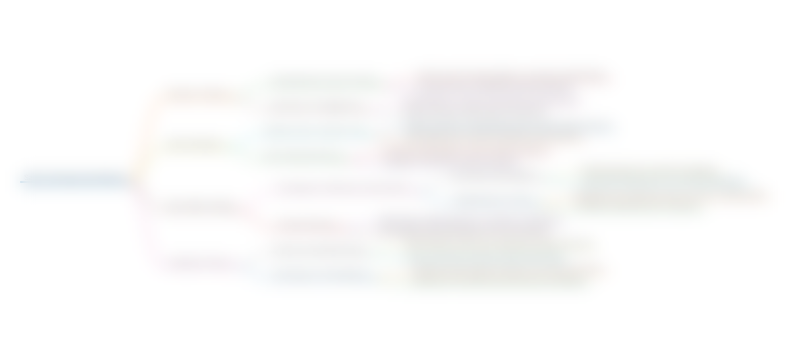
This section is available to paid users only. Please upgrade to access this part.
Upgrade NowKeywords
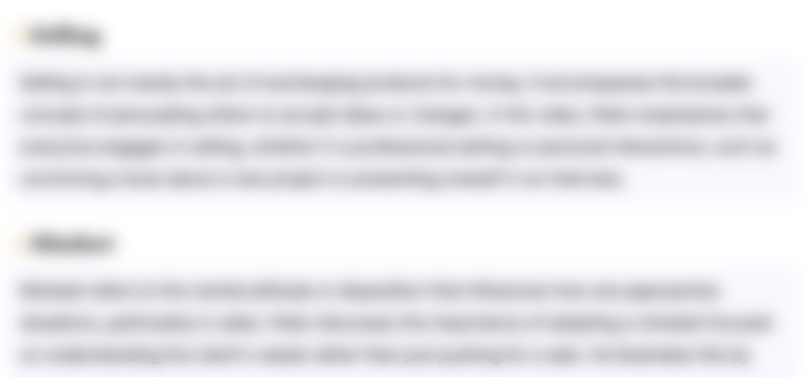
This section is available to paid users only. Please upgrade to access this part.
Upgrade NowHighlights
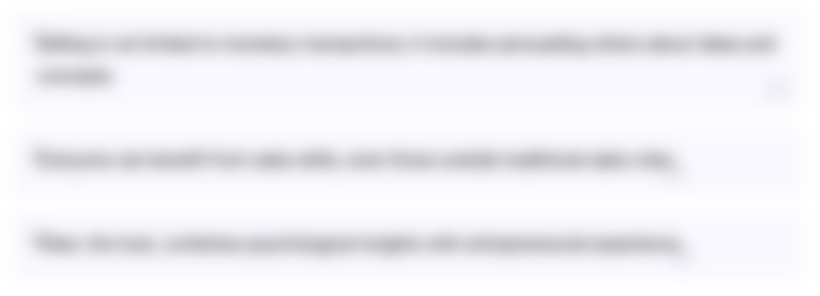
This section is available to paid users only. Please upgrade to access this part.
Upgrade NowTranscripts
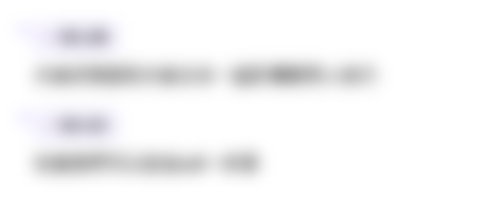
This section is available to paid users only. Please upgrade to access this part.
Upgrade NowBrowse More Related Video
5.0 / 5 (0 votes)