Os 7 desperdícios do Lean
Summary
TLDRThe video script discusses the 7 Wastes concept, originating from Toyota's production system, emphasizing the importance of identifying and eliminating activities that do not add value for the customer. It explains each waste type, such as overproduction, waiting, transportation, inventory, defects, over-processing, and motion, providing examples and suggesting improvements like production pull systems, setup reduction, and 5S implementation to increase efficiency and value.
Takeaways
- 🔍 The script discusses the '7 Wastes' concept, originally from the Toyota Production System, as a fundamental tool for identifying and eliminating activities that do not add value to the customer.
- 🏭 The 7 Wastes are derived from the philosophy of Taiichi Ohno, who played a key role in developing the Toyota Production System, with a focus on removing waste for better reconstruction and efficiency.
- 🚫 The definition of waste is any activity that consumes resources without adding value to the customer, applicable both internally and externally.
- 📈 The script highlights the importance of understanding customer value and aligning company strategy to effectively identify and address waste.
- 🛠️ The 7 Wastes are visually identifiable in a business environment and include overproduction, waiting, transportation, inventory, defects, overprocessing, and underutilized employee creativity.
- 🔄 Overproduction is defined as producing more than the customer requires at a given time, leading to unnecessary waste and inefficiency.
- ⏳ Waiting waste is characterized by idle time where materials, processes, or people are waiting for something to happen, such as parts or information.
- 🚚 Transportation waste involves unnecessary movement of parts or information within the process that doesn't add value, like excessive handling or searching for parts.
- 📦 Inventory waste refers to excess stock that ties up capital that could be better utilized elsewhere, indicating a need for leaner inventory management.
- 💡 The script suggests practical changes to minimize waste, such as implementing production pull systems, improving line flexibility, and reducing setup times.
- 📋 The importance of continuous learning and adaptation is emphasized, with the script proposing exercises and courses to further understand and apply the 7 Wastes concept.
Q & A
What is the origin of the 7 Wastes concept?
-The 7 Wastes concept originated from the Toyota Production System, developed by Taiichi Ohno, who was influenced by his mentor, Eiji Toyoda. It was further popularized by Taiichi Ohno's work and teachings.
What does the term 'Muda' refer to in the context of the 7 Wastes?
-In the context of the 7 Wastes, 'Muda' is a Japanese term that refers to any activity that consumes resources but does not add value, especially from the customer's perspective.
How can the concept of 7 Wastes be applied in a non-manufacturing environment?
-The concept of 7 Wastes can be applied in non-manufacturing environments by identifying activities that do not add value to the customer or the process. This includes administrative tasks, information flows, and any other activities that consume resources without contributing to the final product or service.
What is the first waste in the 7 Wastes, and how can it be addressed?
-The first waste is Overproduction. It can be addressed by aligning production with actual customer demand, implementing pull production systems, reducing lot sizes, and improving setup times to be more flexible and responsive.
What are some strategies to reduce Waiting as a form of waste?
-Strategies to reduce Waiting as a form of waste include synchronizing work processes, improving communication, implementing pull systems, and balancing workload across different stages of production.
How can Transportation and Motion wastes be minimized?
-Transportation and Motion wastes can be minimized by optimizing the layout of workspaces, implementing 5S practices, using milk-run routes for material handling, and ensuring that all movements contribute to the production process.
What is the impact of Inventory as a form of waste?
-Inventory as a form of waste ties up capital that could be used for other investments. It also increases the risk of obsolescence and requires additional space and handling, leading to higher costs and reduced efficiency.
How can Defects be prevented to reduce waste?
-Defects can be prevented by improving process controls, implementing quality checks at each stage, using Poka-Yoke (mistake-proofing) techniques, and ensuring that all team members understand the importance of quality in their work.
What is Overprocessing, and how can it be identified and reduced?
-Overprocessing is any activity that involves more work than necessary from the customer's perspective. It can be identified by analyzing the value-added steps in a process and comparing them to the actual process. Reducing Overprocessing involves streamlining operations, eliminating unnecessary steps, and focusing on what the customer is willing to pay for.
What is the significance of understanding the customer's perspective in identifying and addressing the 7 Wastes?
-Understanding the customer's perspective is crucial because it helps identify which activities add value and which do not. By focusing on what the customer is willing to pay for, organizations can eliminate non-value-added activities and improve efficiency, quality, and customer satisfaction.
How can the 7 Wastes concept contribute to overall business improvement?
-The 7 Wastes concept contributes to overall business improvement by providing a framework for identifying and eliminating non-value-added activities. This leads to reduced costs, improved efficiency, better resource utilization, and ultimately, higher customer satisfaction and business competitiveness.
Outlines
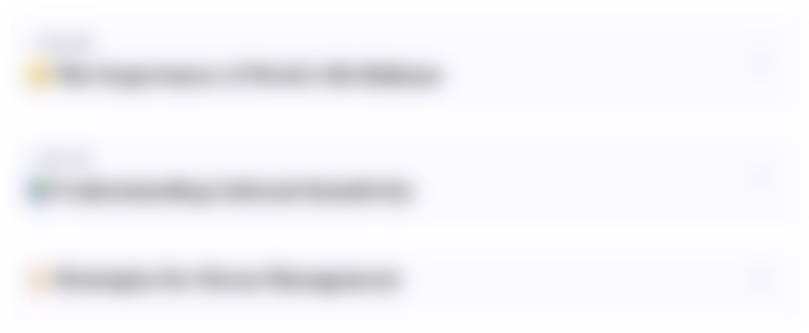
Esta sección está disponible solo para usuarios con suscripción. Por favor, mejora tu plan para acceder a esta parte.
Mejorar ahoraMindmap
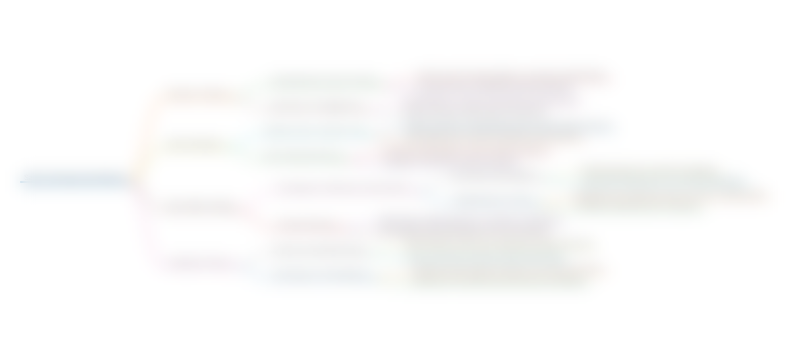
Esta sección está disponible solo para usuarios con suscripción. Por favor, mejora tu plan para acceder a esta parte.
Mejorar ahoraKeywords
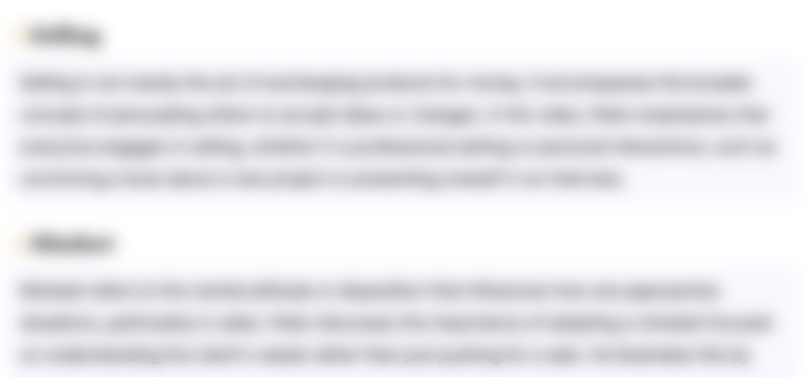
Esta sección está disponible solo para usuarios con suscripción. Por favor, mejora tu plan para acceder a esta parte.
Mejorar ahoraHighlights
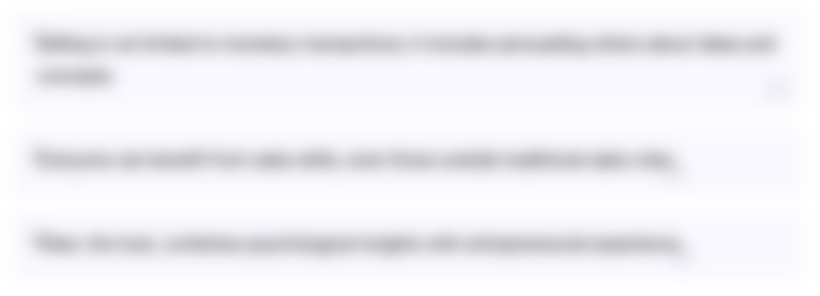
Esta sección está disponible solo para usuarios con suscripción. Por favor, mejora tu plan para acceder a esta parte.
Mejorar ahoraTranscripts
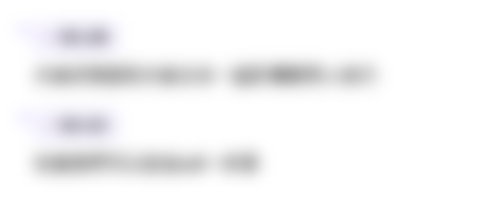
Esta sección está disponible solo para usuarios con suscripción. Por favor, mejora tu plan para acceder a esta parte.
Mejorar ahoraVer Más Videos Relacionados

Gemba Glossary: The 7 Wastes

Apa itu SEVEN WASTE (7 Pemborosan)

ムダ取りの必要性【アニメで学ぶムダ取り入門:Lesson1】
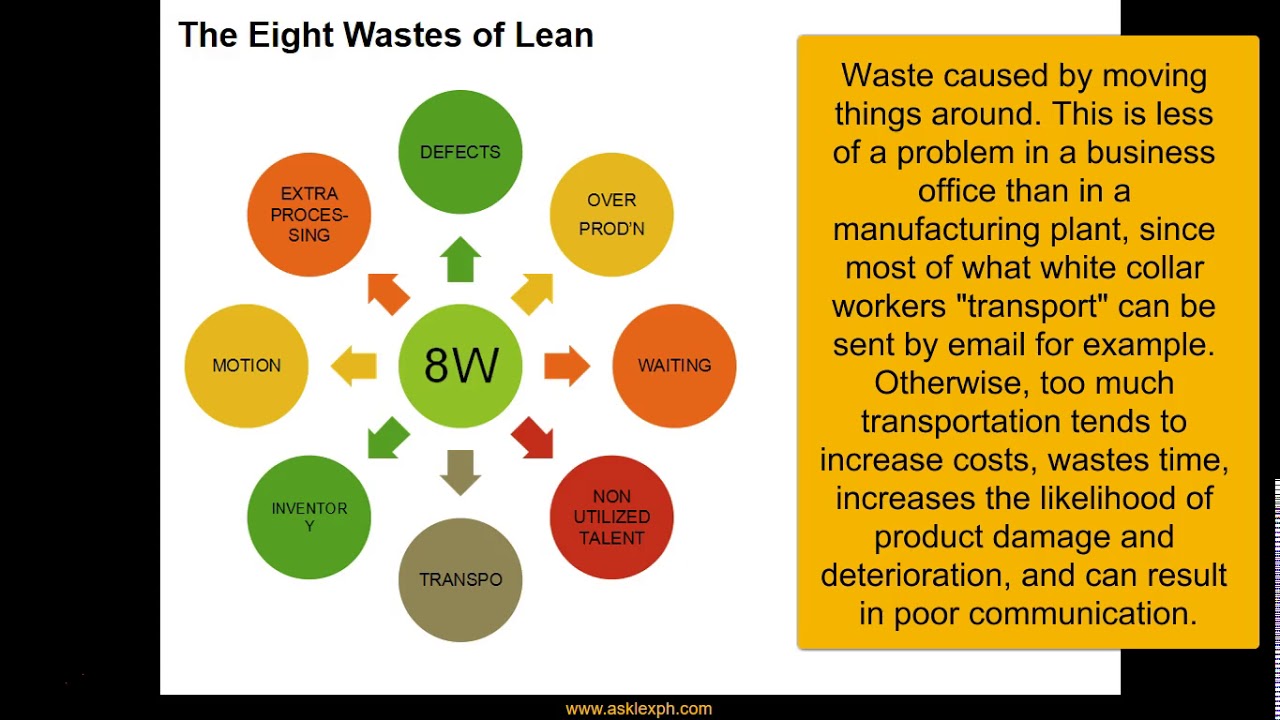
F3. The Eight Wastes of Lean (DOWNTIME)
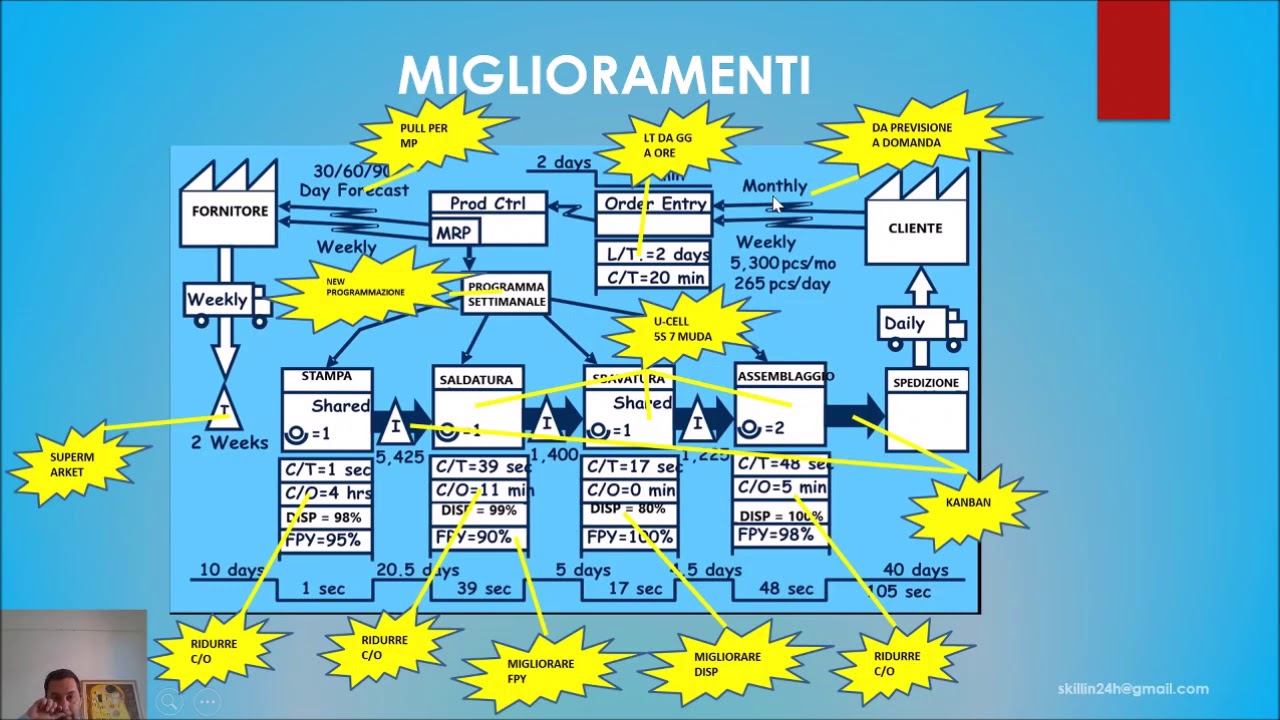
Lezione 4D - CREAZIONE VSM - Parte 4 di 4 - Lean Thinking e Toyota Producition System - Zero sprechi

Value added analysis | Value added process vs Non value added | Value Added vs Non Value added Lean
5.0 / 5 (0 votes)