Gemba Glossary: The 7 Wastes
Summary
TLDRThis video script from the Gemba Glossary introduces the concept of the 7 Wastes, which can account for 40-90% of work being wasted in processes. The acronym 'TIM WOODS' helps remember the wastes: Transportation, Inventory, Motion, Waiting, Overproduction, Overprocessing, and Defects. Taiichi Ohno, of the Toyota Production System, emphasized the importance of identifying and reducing these wastes at the Gemba, the actual place of work. An eighth waste, Skills and Talent, is also mentioned, highlighting the need to utilize employees' full potential.
Takeaways
- 📊 Waste Identification: The script emphasizes the importance of identifying and countering the 7 Wastes in a process or system, which can account for 40% to 90% of wasted effort.
- 🔠 Mr. Tim Wood: An acronym to remember the 7 Wastes, where T stands for Transportation, I for Inventory, M for Motion, and so on.
- 🚚 Transportation Waste: Unnecessary movement of materials that does not add value to the product.
- 📦 Inventory Waste: Excess materials or work on hand beyond what is needed to meet immediate customer demand.
- 🏃♂️ Motion Waste: Unproductive movement of people, including walking and reaching for items that do not enhance the product's value.
- ⏱️ Waiting Waste: Idle time due to unprepared materials, machines, inspections, or information, leading to inefficiency.
- 🚫 Overproduction Waste: Producing more than what customers need, often considered the most detrimental waste.
- 🛠️ Overprocessing Waste: Designing processes that use more resources than necessary, leading to unnecessary consumption of space, energy, or labor.
- 🔧 Defects Waste: Work that falls below the quality level requested by both internal and external customers.
- 🏭 Gemba Principle: The concept of going to the place where work is done to relentlessly reduce waste, promoted by Taiichi Ohno, a key figure in the Toyota Production System.
- 🎓 Eighth Waste: The script introduces an additional waste, the underutilization of employees' skills and talents, expanding the original 7 to 8 wastes.
- 📚 Continuous Improvement: The script encourages viewers to subscribe for more insights on continuous improvement in future episodes of the Gemba Glossary.
Q & A
What is the significance of identifying the 7 Wastes in a process or system?
-Identifying the 7 Wastes is significant because it helps to recognize and eliminate activities that add costs but no value, thereby improving efficiency and reducing waste in processes or systems.
What does the acronym 'TIM WOOD' stand for in the context of the 7 Wastes?
-In the context of the 7 Wastes, 'TIM WOOD' stands for Transportation, Inventory, Motion, Waiting, Overproduction, Overprocessing, and Defects, which are the seven types of waste to be identified and eliminated.
What is the definition of 'Transportation' as one of the 7 Wastes?
-'Transportation' refers to the movement of materials that adds no value to the product, which is considered wasteful as it consumes resources without contributing to the product's value.
How is 'Inventory' defined in the context of the 7 Wastes?
-'Inventory' in this context is any material or work on hand beyond what is immediately needed to satisfy customer demand, which ties up capital and can lead to obsolescence or unnecessary storage costs.
What constitutes 'Motion' waste in the 7 Wastes?
-'Motion' waste includes any movement of people that doesn't add value to the product, such as unnecessary walking or reaching for items, which can be reduced to improve efficiency.
What is the waste of 'Waiting' and why is it considered wasteful?
-The waste of 'Waiting' occurs when there is idle time created because materials, machines, inspections, or information are not ready for people. It is wasteful as it leads to underutilization of resources and lost productivity.
Why is 'Overproduction' often called the 'mother of all waste'?
-'Overproduction' is called the 'mother of all waste' because it involves making more product than customers need, which can lead to excess inventory, increased costs, and potential waste of resources.
What is the waste of 'Overprocessing' and how does it occur?
-The waste of 'Overprocessing' occurs when a product is designed in a way that uses more resources, such as space, energy, or labor, than is truly required, leading to inefficiency and unnecessary costs.
What are 'Defects' in the context of the 7 Wastes and why are they important to address?
-'Defects' in this context refer to work that is less than the level requested by customers, both internal and external. Addressing defects is important as they can lead to rework, scrap, and dissatisfaction, impacting the overall quality and cost.
Who is Taiichi Ohno and what is his contribution to the concept of the 7 Wastes?
-Taiichi Ohno is one of the chief architects of the Toyota Production System. He is credited with defining the 7 types of wastes, which describe all activities that add costs but no value, emphasizing the importance of waste reduction.
What is the concept of the 'eighth waste' and how does it relate to the original 7 Wastes?
-The 'eighth waste' refers to the waste of skills and talent, meaning not fully utilizing the abilities of employees. It extends the original 7 Wastes by adding the underutilization of human resources to the list of inefficiencies to be addressed.
What does 'Gemba' mean and why is it important in the context of continuous improvement?
-'Gemba' is a Japanese term meaning 'the real place', typically referring to the workplace where value is created. It is important in continuous improvement as it emphasizes the need to go to the source of work to observe, understand, and reduce waste effectively.
Outlines
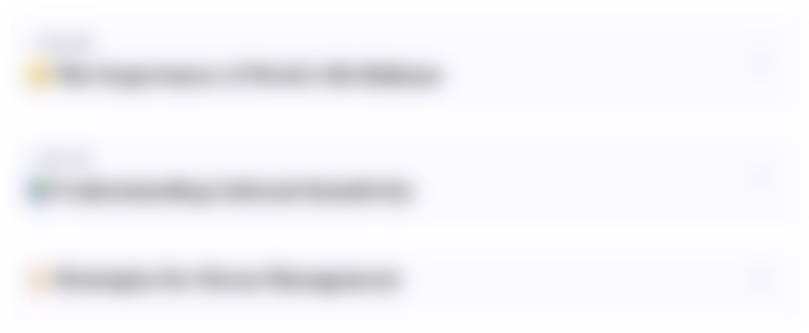
This section is available to paid users only. Please upgrade to access this part.
Upgrade NowMindmap
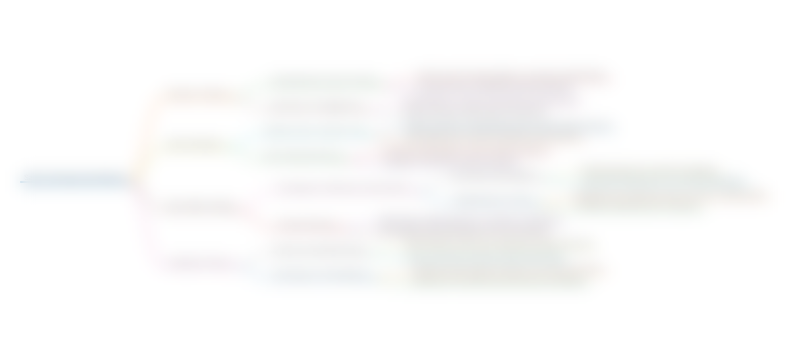
This section is available to paid users only. Please upgrade to access this part.
Upgrade NowKeywords
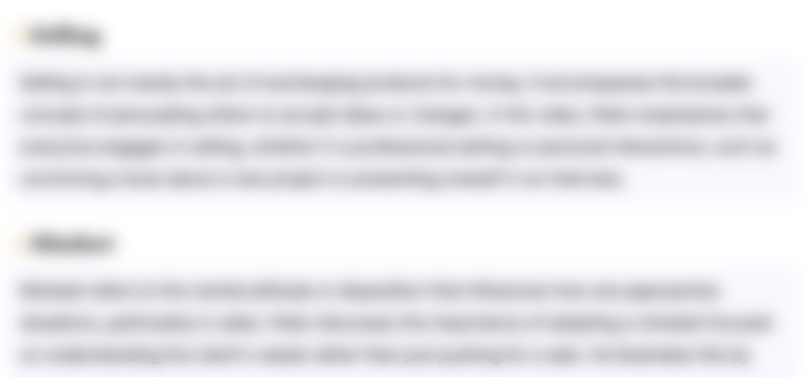
This section is available to paid users only. Please upgrade to access this part.
Upgrade NowHighlights
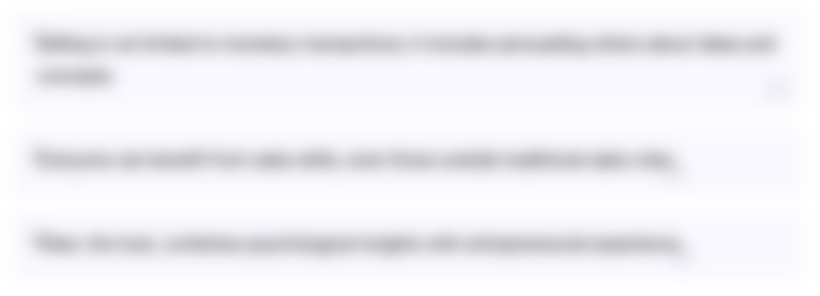
This section is available to paid users only. Please upgrade to access this part.
Upgrade NowTranscripts
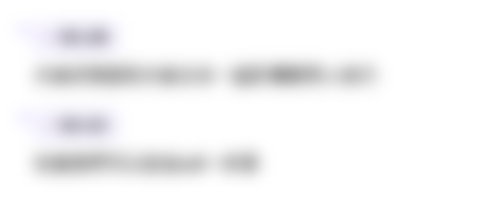
This section is available to paid users only. Please upgrade to access this part.
Upgrade NowBrowse More Related Video

AI FlashCard Generator

Princípios do Lean - Mais importante que as ferramentas.

The Next Generation of Vertical Farming | Alexander Olesen | TEDxWarrenton

Os 7 desperdícios do Lean

Introduction to pH | Biology foundations | High school biology | Khan Academy

Audit Programme क्या होता है? || Meaning, Definition & Advantages Of Audit Programme || हिन्दी में |
5.0 / 5 (0 votes)