F3. The Eight Wastes of Lean (DOWNTIME)
Summary
TLDRTaiichi Ohno, the father of the auto production system, developed a lean manufacturing framework focused on preserving value and eliminating waste. The script discusses the eight wastes in processes: defects, overproduction, waiting, non-utilized talent, transportation, inventory, motion, and extra processing. It suggests solutions like standardized work, quality control, and empowering employees to reduce waste, leading to faster processes, lower costs, and improved customer satisfaction.
Takeaways
- 😀 Taiichi Ohno is recognized as the father of the auto production system and the creator of the lean manufacturing framework.
- 🔧 The core of lean manufacturing is to preserve value and eliminate waste that doesn't add value from the customer's perspective.
- 🚫 The eight wastes in the manufacturing process are defects, overproduction, waiting, non-mutant eyes, pallet transportation, inventory, motion, and extra processing.
- 🛠️ Defects are mistakes that require additional resources to fix and can be limited by standardized work and quality control.
- 🚫 Overproduction is a flaw where more is produced than needed, causing a tie-up of resources and can be addressed by establishing a reasonable workflow.
- ⏱️ Waiting is a waste caused by various reasons such as imbalanced work loops, long setup times, and insufficient staffing.
- 💡 Non-utilization of talent occurs when people's skills and knowledge are underutilized, which can be mitigated by empowering employees and improving communication.
- 🚚 Transportation waste is the unnecessary movement of materials, which can be reduced by simplifying processes and optimizing physical layouts.
- 📦 Inventory waste happens when there is more supply than actual demand, often due to overproduction or poor monitoring systems.
- 🔄 Motion waste is any excess movement by employees or machines that doesn't add value to the product or service and can be reduced by improving workstation layouts.
- 🛠️ Extra processing waste is the result of creating unnecessary steps or processes, which can be eliminated by streamlining and standardizing processes.
Q & A
Who is Taiichi Ohno and what is his contribution to the manufacturing industry?
-Taiichi Ohno is considered the father of the auto production system. He created a lean manufacturing framework based on the idea of preserving value and eliminating waste that doesn't increase value in the customer's eyes.
What are the eight wastes in the lean manufacturing framework?
-The eight wastes are defects, overproduction, waiting, non-utilized talent, transportation, inventory, motion, and extra processing.
Why are defects considered a waste in the manufacturing process?
-Defects are considered waste because they require additional time, resources, and money to fix, and they involve mistakes such as defective parts that need to be removed.
What are some causes of defects in manufacturing?
-Causes of defects include poor quality controls, poor repair, poor documentation, lack of standards, weak or missing processes, misunderstanding customer needs, uncontrolled inventory levels, poor design, and undocumented design changes.
How can defects be limited in a manufacturing process?
-Defects can be limited by applying standardized work plans, implementing more stringent quality control at all levels, fully understanding work requirements and customer needs, and using simple job aids such as checklists.
What is overproduction and why is it a flaw in an organization?
-Overproduction is the act of producing more than is needed or before it is required, which can tie up significant working capital and is especially common in manufacturing.
What are some causes of overproduction?
-Overproduction may occur due to 'just in case' production, unclear customer needs, long setup times, engineering changes, and poorly applied automation.
How can an organization address the issue of waiting as a waste?
-Addressing waiting as a waste involves providing adequate staffing to handle the workload at bottlenecks, improving work balance, reducing setup times, and enhancing communication.
Why is non-utilized talent considered a waste in an organization?
-Non-utilized talent is considered waste because it can have a detrimental effect on an organization, as it fails to recognize the value of skills and improvement ideas from all levels of the business.
What are some solutions to reduce transportation waste in a manufacturing setting?
-Solutions to reduce transportation waste include simplifying processes, improving physical layouts, handling products less often, and minimizing distances between steps.
How does inventory waste occur and what are its causes?
-Inventory waste occurs when there is supply in excess of real customer demand, which can mask real production issues. Causes include overproduction, poor monitoring systems, mismatched production speeds, unreliable suppliers, and misunderstood customer needs.
What are typical causes of motion waste in a manufacturing process?
-Motion waste is caused by poor process design and control, poor workstation or workshop layout, shared tools and machines, workstation congestion, isolated and siloed operations, and lack of standards.
How can extra processing waste be addressed in an organization?
-Extra processing waste can be addressed by examining and mapping the organization's processes to identify and eliminate unnecessary documentation, standardize processes, empower employees, and reduce unnecessary processes and meetings.
Outlines
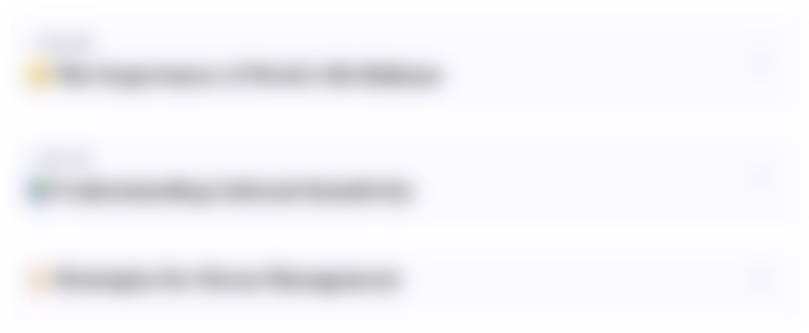
This section is available to paid users only. Please upgrade to access this part.
Upgrade NowMindmap
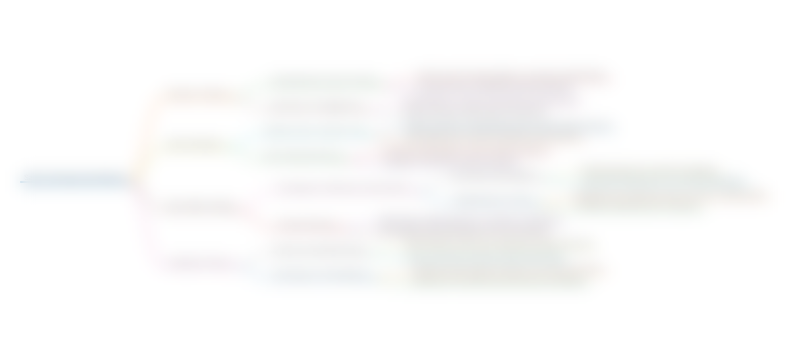
This section is available to paid users only. Please upgrade to access this part.
Upgrade NowKeywords
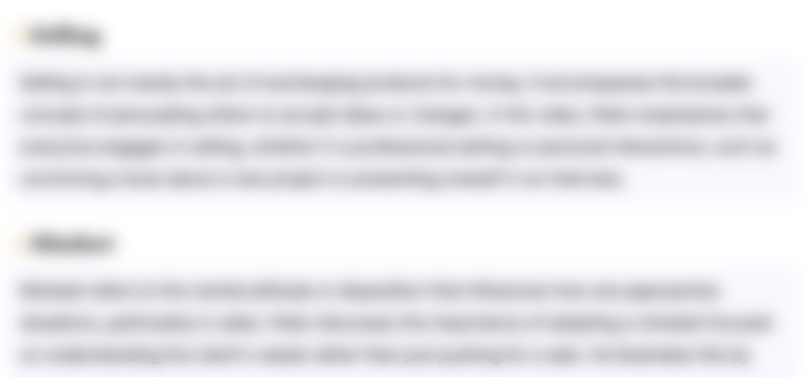
This section is available to paid users only. Please upgrade to access this part.
Upgrade NowHighlights
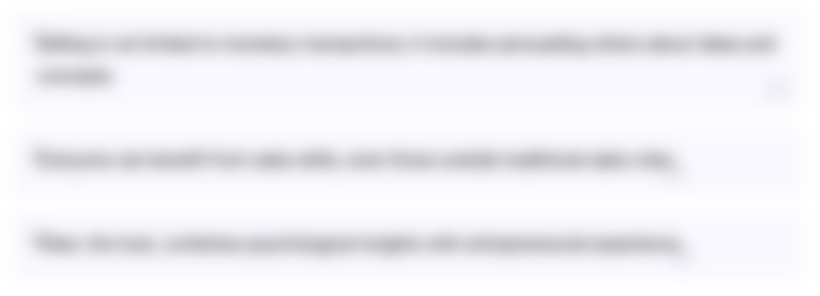
This section is available to paid users only. Please upgrade to access this part.
Upgrade NowTranscripts
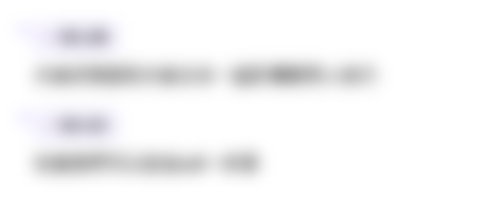
This section is available to paid users only. Please upgrade to access this part.
Upgrade NowBrowse More Related Video
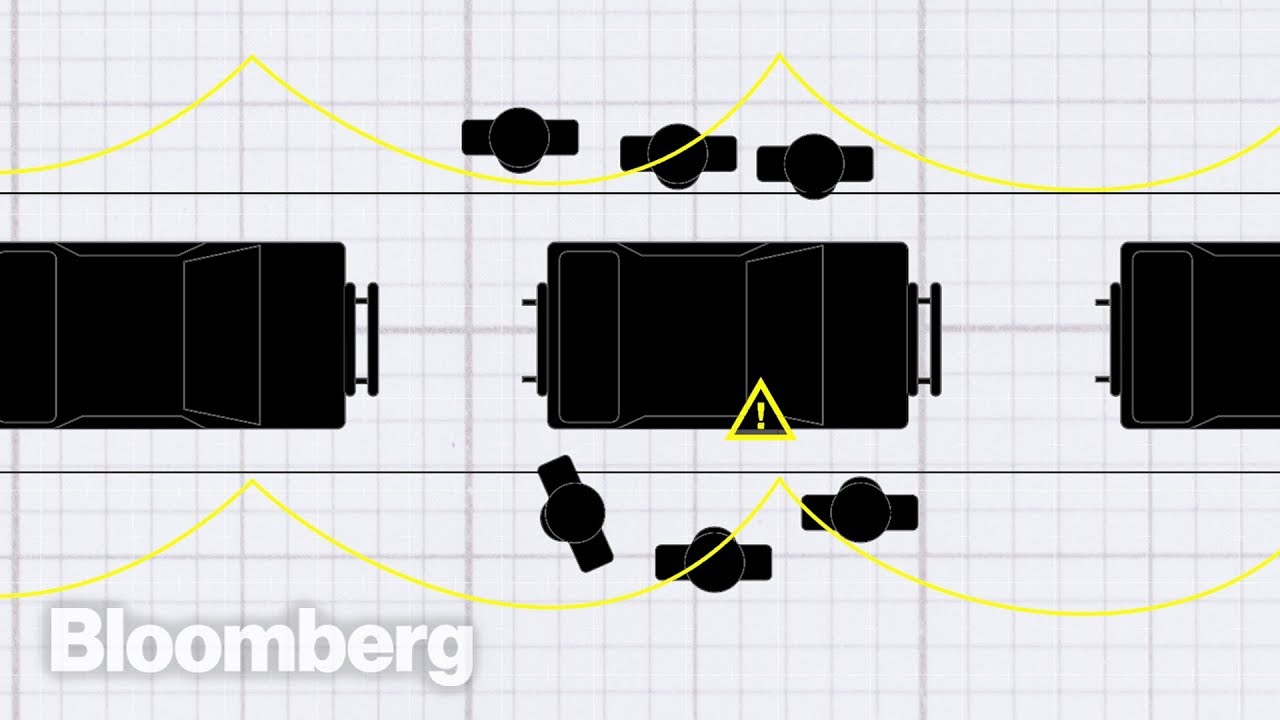
How Toyota Changed The Way We Make Things
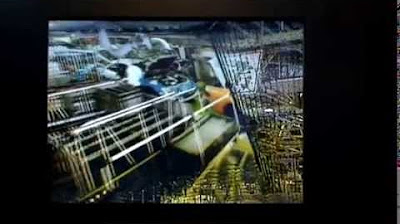
History of the Toyota Production System (TPS)

⚙ Lean Manufacturing | A pursuit of perfection
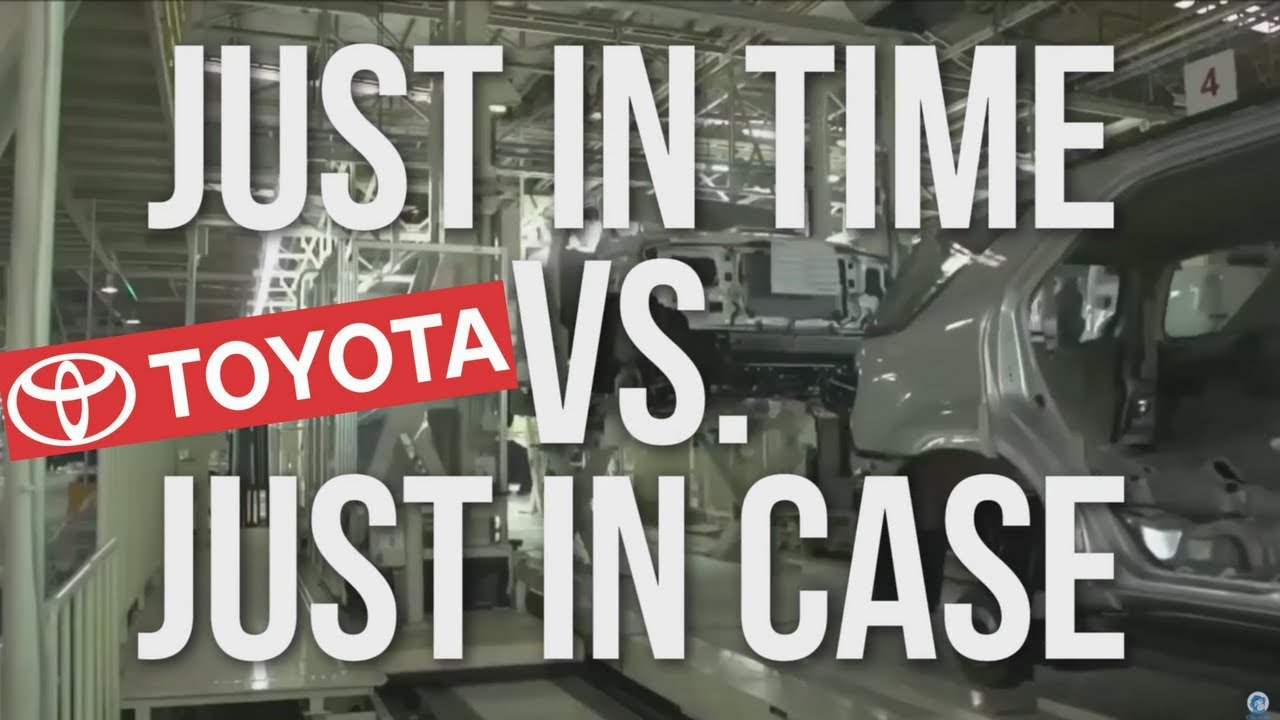
Just in Time by Toyota: The Smartest Production System in The World
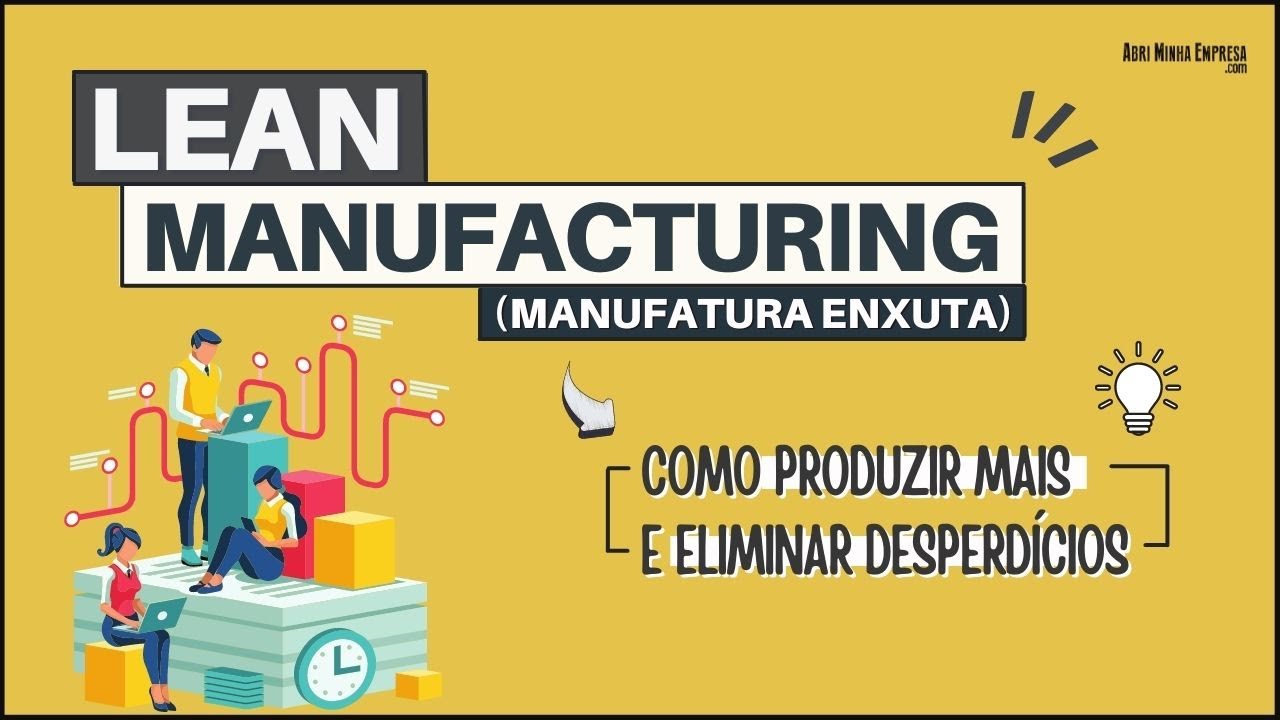
LEAN MANUFACTURING (Manufatura Enxuta) | Conheça os 8 Principais Tipos de Desperdícios
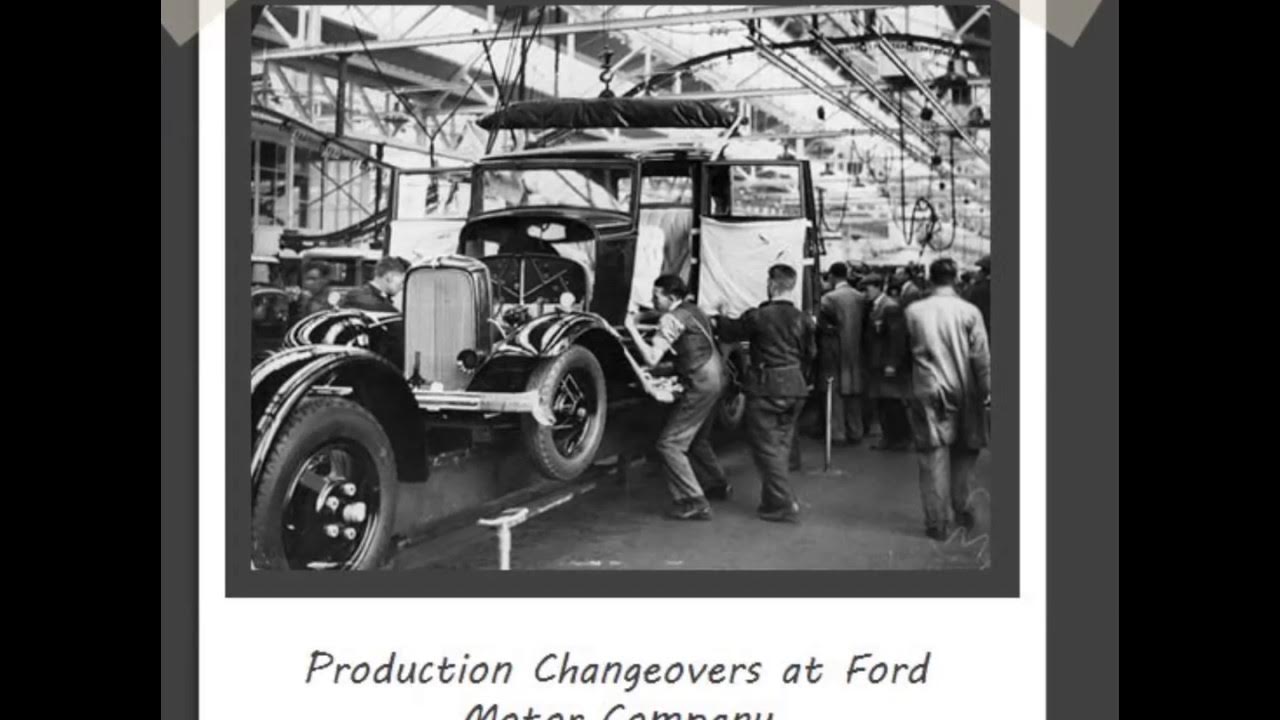
The History of Lean
5.0 / 5 (0 votes)