Lean Manufacturing One Piece Flow vs. Mass Production Paper Airplane Simulation (Lean Tip 005)
Summary
TLDRThis video provides an insightful look into lean manufacturing, focusing on converting batch production into one-piece flow. The demonstration, conducted by Lean Smarts employees, illustrates how streamlining processes can lead to over 50% improvements in efficiency. Key lean principles like waste reduction, motion efficiency, and flow improvement are explored, with a clear example of making paper airplanes. The video is part of a broader introductory mini-course on lean manufacturing available at LeanSmarts.com, offering more insights into lean history, methods, tools, and cultural implementation.
Takeaways
- 📦 Lean manufacturing aims to convert batch production into one-piece flow, significantly reducing waste and improving efficiency.
- ✈️ In the demonstration, employees make paper airplanes in a batch production process first, which highlights common inefficiencies.
- 👀 Viewers are encouraged to look for waste in the process, such as motion, waiting, transportation, and inventory.
- 🛑 Motion waste occurs when unnecessary movements are made, such as constantly picking up and putting down papers.
- ⏳ Waiting and boredom are other forms of waste, as seen when employees have downtime while waiting for batches to finish.
- 🚚 Transportation waste occurs when finished products are moved from one department to another, which causes delays.
- 🏭 Inventory waste happens when more products are produced than the next department can handle, resulting in excess stock.
- 📉 The overproduction in batch processing causes a multiplication of other wastes, such as excess inventory and waiting.
- 🔄 By switching to one-piece flow, where products move from department to department as soon as they are ready, waste is drastically reduced.
- 💡 One-piece flow led to a 64% improvement in efficiency, cutting production time from 4 minutes 59 seconds to 1 minute 47 seconds.
Q & A
What is the main focus of the video clip featured in the introduction?
-The video focuses on demonstrating the concept of converting batch production into one-piece flow, showcasing the benefits and efficiency gains that can be achieved through lean manufacturing techniques.
Who are the employees in the video, and what task are they performing?
-Two employees from Lean Smarts are featured in the video, and they are tasked with making paper airplanes. Their process highlights the differences between batch production and one-piece flow.
What are some of the common wastes observed during the batch production process in the video?
-The common wastes identified include motion (repeatedly picking up and putting down papers), waiting (as one department waits for the other), transportation (moving the batch between departments), and inventory (producing more airplanes than needed at once).
What is the primary issue with batch production as described in the video?
-Batch production leads to overproduction, where more items are produced than are needed by the next internal or external customer. This results in inefficiencies and various types of waste, such as excessive inventory, unnecessary motion, and longer lead times.
How does one-piece flow differ from batch production?
-One-piece flow involves processing and moving one item at a time through the production line, rather than working on batches of items. This allows for faster overall production, less waste, and improved efficiency between departments.
What was the time difference between batch production and one-piece flow in the paper airplane example?
-The batch production process took 4 minutes and 59 seconds, while switching to one-piece flow reduced the time to 1 minute and 47 seconds, which is a 64% improvement.
What is overproduction, and how does it relate to the video’s example?
-Overproduction occurs when more products are made than needed at a given time, which can lead to wasted resources, space, and time. In the video, the batch production of five paper airplanes at once, when only one could be processed at a time, is an example of overproduction.
What is the key takeaway from the lean manufacturing demonstration?
-The key takeaway is that implementing lean manufacturing techniques, such as one-piece flow, can lead to significant reductions in production time and overall waste, improving efficiency by 50% or more in many cases.
What other topics does the Lean Smarts mini-course cover?
-The mini-course covers the basics of lean manufacturing, including its history, methods, common tools (like 5S, leveling production, and the 7 wastes of lean), and how to create a lean culture within an organization.
How can viewers access the full mini-course on lean manufacturing?
-Viewers can sign up for the free mini-course on the Lean Smarts website. The course is delivered over five days, with five videos that provide a comprehensive introduction to lean manufacturing concepts and tools.
Outlines
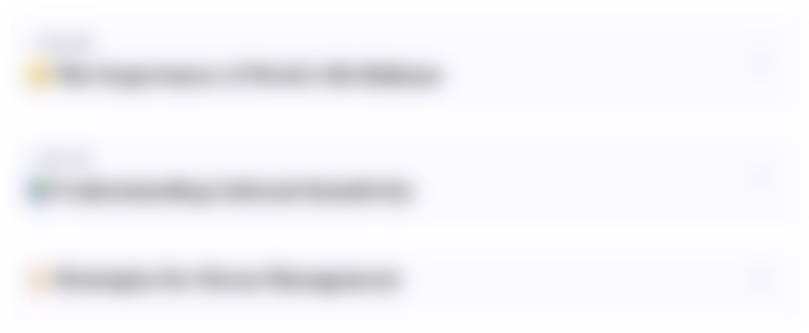
هذا القسم متوفر فقط للمشتركين. يرجى الترقية للوصول إلى هذه الميزة.
قم بالترقية الآنMindmap
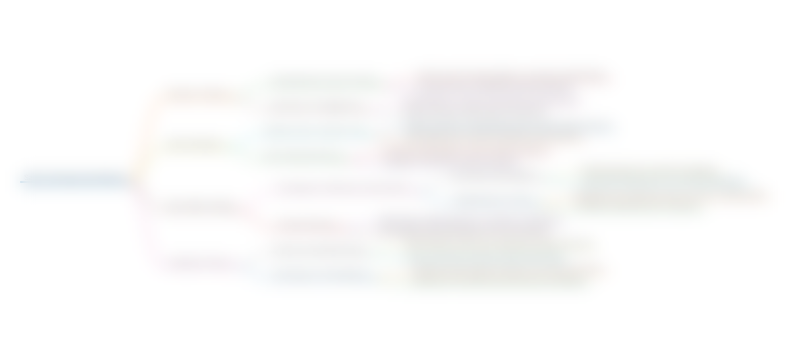
هذا القسم متوفر فقط للمشتركين. يرجى الترقية للوصول إلى هذه الميزة.
قم بالترقية الآنKeywords
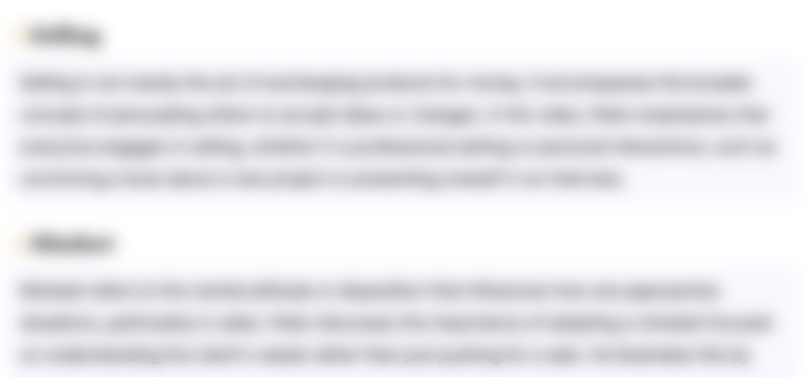
هذا القسم متوفر فقط للمشتركين. يرجى الترقية للوصول إلى هذه الميزة.
قم بالترقية الآنHighlights
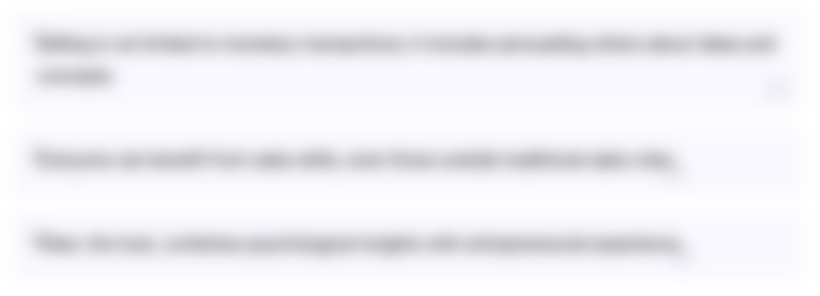
هذا القسم متوفر فقط للمشتركين. يرجى الترقية للوصول إلى هذه الميزة.
قم بالترقية الآنTranscripts
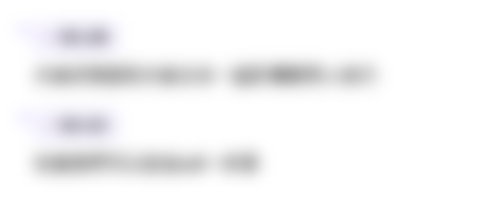
هذا القسم متوفر فقط للمشتركين. يرجى الترقية للوصول إلى هذه الميزة.
قم بالترقية الآنتصفح المزيد من مقاطع الفيديو ذات الصلة

Lean Manufacturing : What is Single Piece Flow?
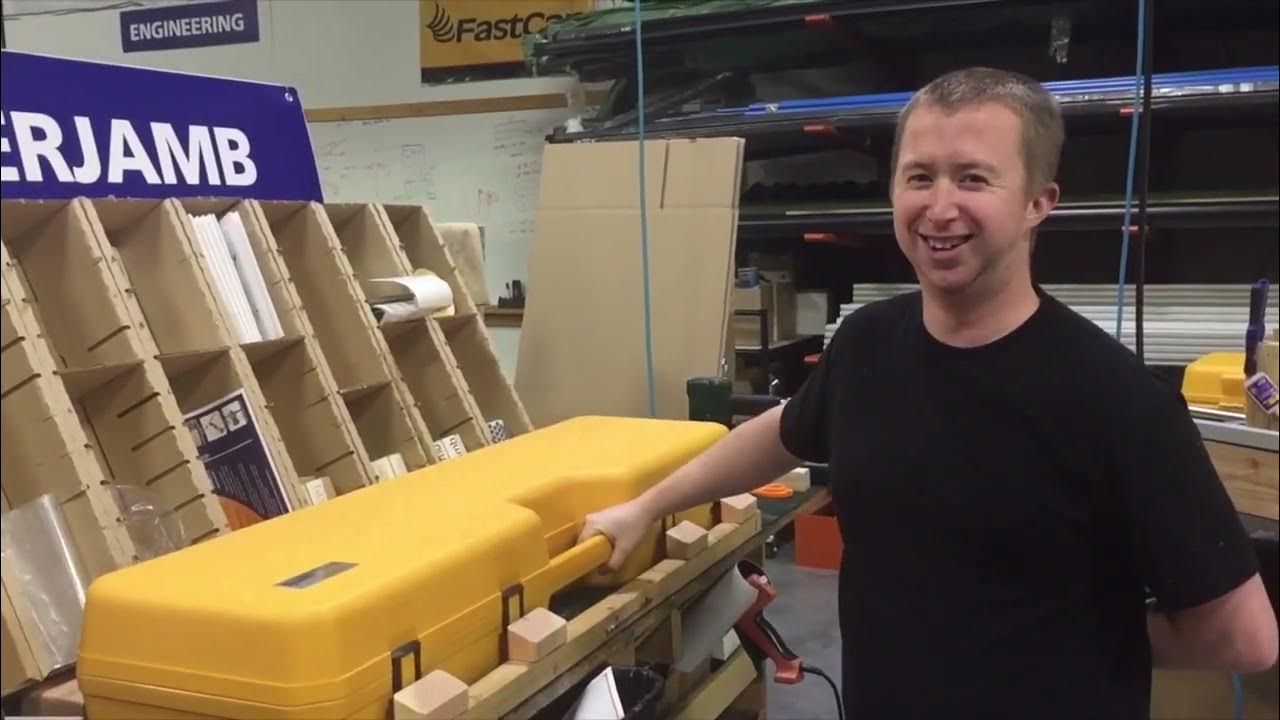
Ch3 - "One Piece Flow" - 2 SECOND LEAN Visual Audiobook
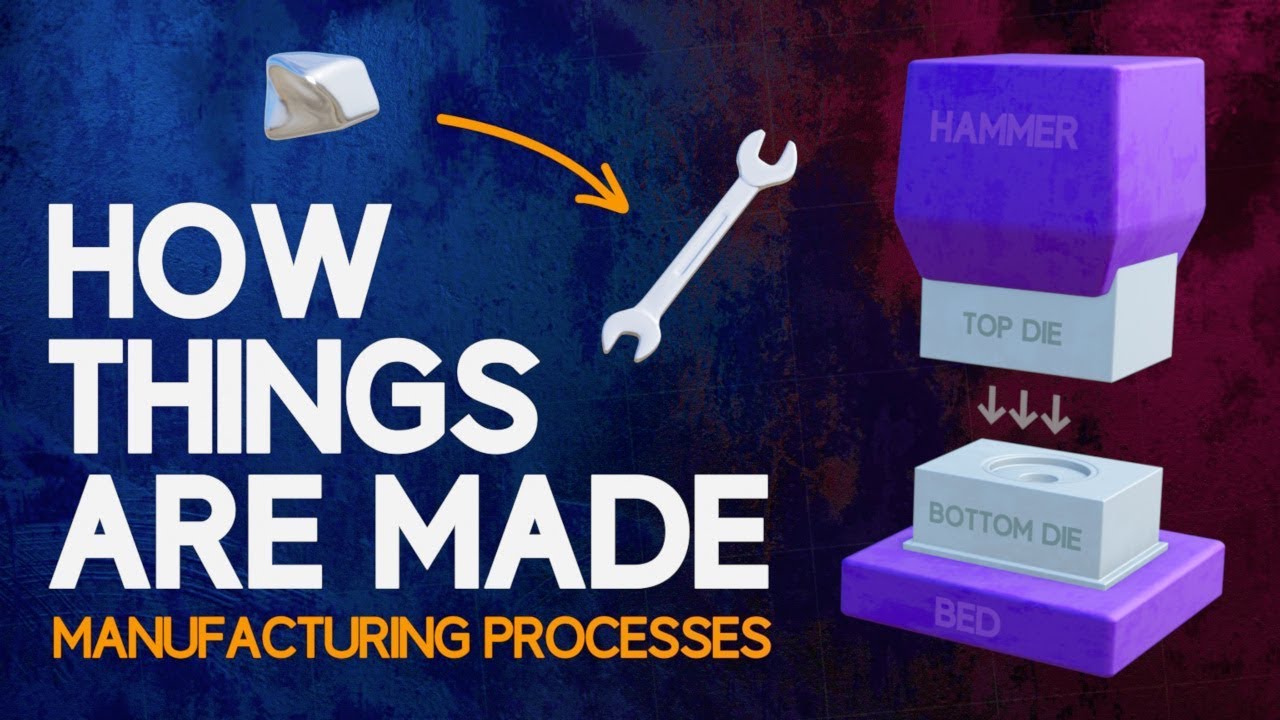
How Things Are Made | An Animated Introduction to Manufacturing Processes
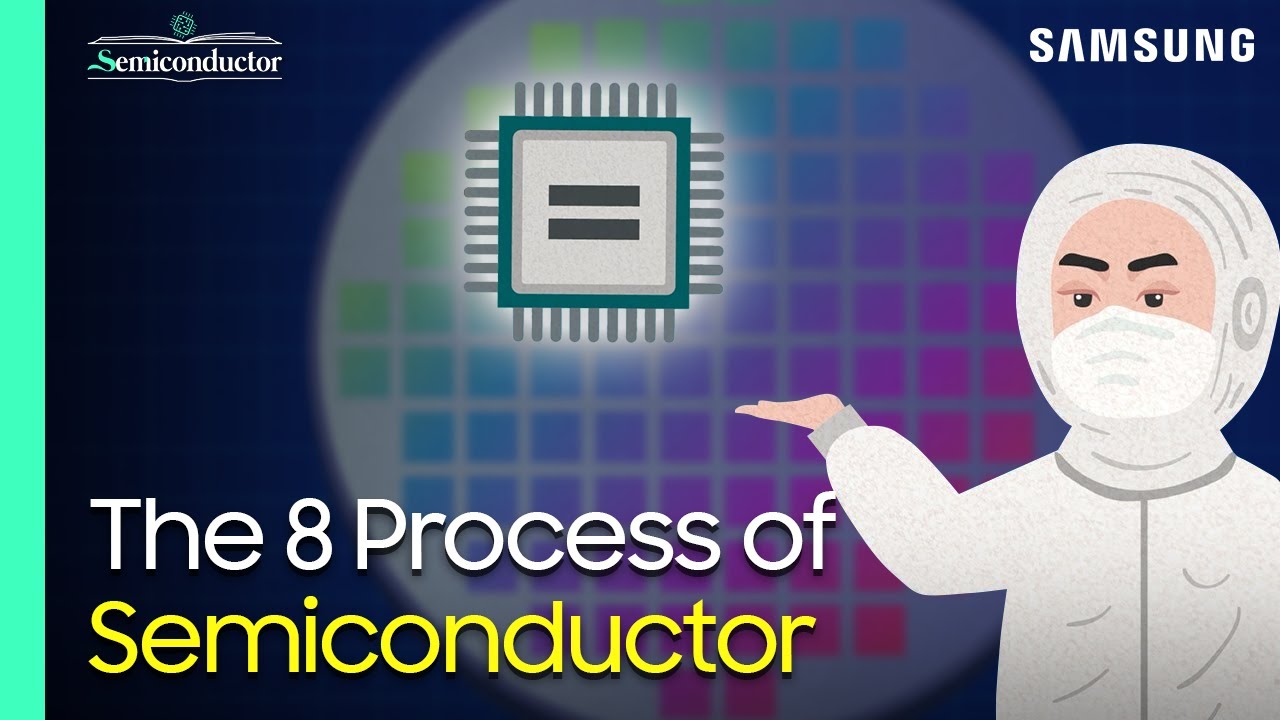
‘Semiconductor Manufacturing Process’ Explained | 'All About Semiconductor' by Samsung Semiconductor
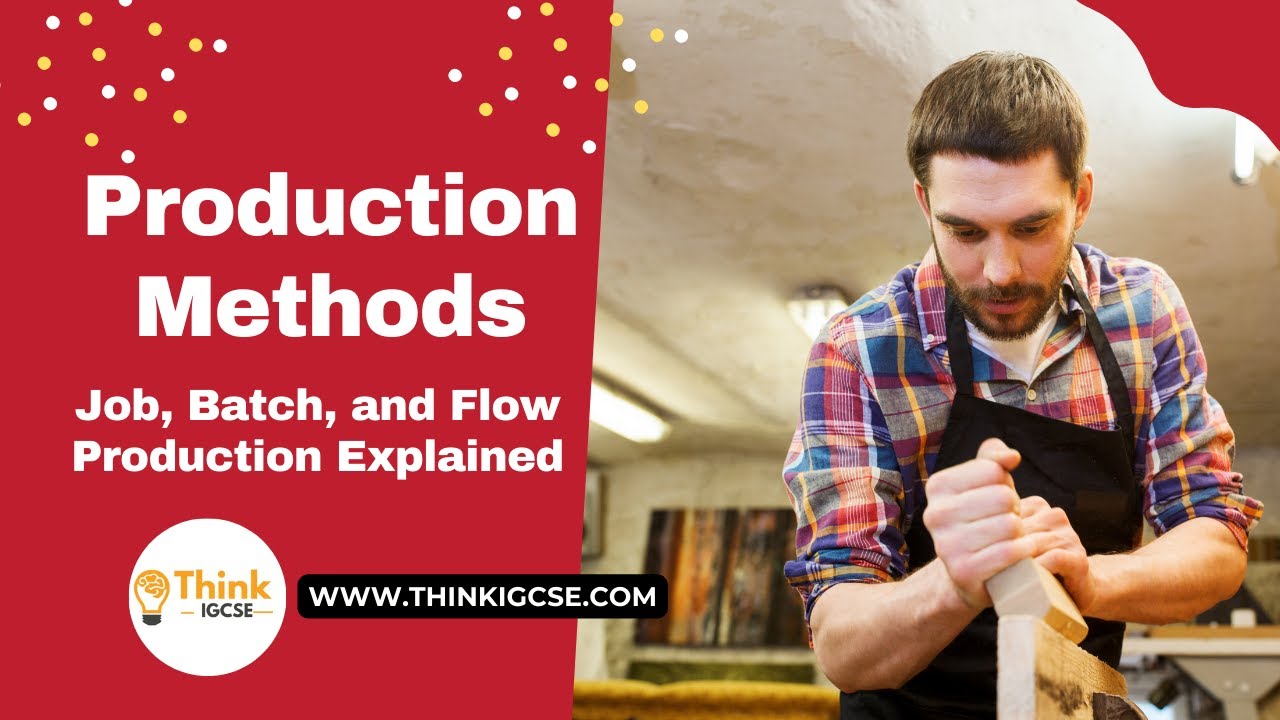
Exploring Production Methods: Job, Batch, and Flow Production Explained | ThinkIGCSE.com

Process Selection - A Review of Continuous Flow, Assembly Line, Batch Flow and Job Shop
5.0 / 5 (0 votes)