Latihan Soal Teknik Mesin/Pemesinan #mesin bubut
Summary
TLDRThis video tutorial explains essential calculations for lathe machine operations, covering various practical problems faced by machine operators. It provides step-by-step guidance on determining spindle speeds, feed rates, cutting times, and the necessary adjustments for tapering workpieces. With clear examples and detailed explanations, viewers can understand the formulas and techniques used to optimize lathe operations. The video is designed for those working in machining and manufacturing industries, offering a comprehensive approach to solving real-world lathe machine problems with precision.
Takeaways
- 😀 Lathe machines are commonly used in industrial applications for machining various materials, with a focus on calculating important parameters like cutting speed, feed rate, and machining time.
- 😀 Cutting speed is crucial for determining the appropriate spindle speed (RPM) for a lathe operation, and can be calculated using the formula: C = (π × D × N) / 1000.
- 😀 When calculating spindle speed (N) based on cutting speed (C), the formula is rearranged to N = (1000 × C) / (π × D), where D is the diameter of the workpiece.
- 😀 In Example 1, the spindle speed is calculated for a 22 mm diameter part with a cutting speed of 40 m/min. The closest available machine speed is 590 RPM.
- 😀 Feed rate (F) can be determined using the formula: F = feed per revolution × N, where N is the spindle speed. This is important for determining the speed at which material is removed from the workpiece.
- 😀 In Example 2, the feed rate is calculated for a 10 mm diameter workpiece, and the result is 191 mm/min based on a cutting speed of 40 m/min and a feed rate of 0.4 mm/rev.
- 😀 To calculate the time needed for a facing operation, the formula is: Facing time = (π × D × 0.5) / (F × N), where D is the diameter, F is the feed rate, and N is the spindle speed.
- 😀 In Example 3, the facing time for a 22 mm diameter workpiece is calculated as approximately 30 seconds, with a 4 mm offset and a feed rate of 0.05 mm/rev.
- 😀 Surface machining time can be calculated using the formula: Time = (Length of surface) / (Feed rate × Spindle speed). This formula helps to determine how long it will take to machine a specific length of material.
- 😀 In Example 4, the time required to machine a surface is calculated as 35 seconds, based on a 30 mm length, 590 RPM spindle speed, and a feed rate of 0.1 mm/rev.
- 😀 Tapered shafts can be machined by calculating the required offset using the formula: X = (D_initial - D_final) / (2 × L), where D_initial is the starting diameter, D_final is the final diameter, and L is the length of the taper.
- 😀 In Example 5, the offset required to make a tapered shaft with an initial diameter of 30 mm and final diameter of 25 mm over a length of 80 mm is found to be 3.125 mm.
Q & A
What is the main topic of the video script?
-The video discusses the operation and calculations related to lathe machines, including cutting speed, feed rate, and time calculations for various lathe operations.
What is the first example problem in the video about?
-The first example problem involves a worker performing turning on a workpiece with a diameter of 22 mm. The cutting speed is given as 40 meters per minute, and the task is to determine the appropriate machine speed from several available options.
How do you calculate the cutting speed (C) for the first example?
-The cutting speed (C) is calculated using the formula: C = (π * D * N) / 1000, where D is the diameter and N is the machine speed in RPM. In this case, the cutting speed was found to be 40 meters per minute.
What is the correct machine speed for the first example problem?
-The correct machine speed is 590 RPM, as it is the closest option to the calculated speed of approximately 579.039 RPM.
What is the second example about in the script?
-The second example focuses on determining the feed rate (F) when the cutting speed (40 meters per minute) and the workpiece diameter (10 mm) are given, with several machine speeds to choose from.
How do you calculate the feed rate in the second example?
-To find the feed rate, you first calculate the machine speed using the formula: N = (1000 * C) / (π * D). Then, the feed rate is calculated by multiplying the feed per revolution (F) by the machine speed (N). In this case, the feed rate was determined to be 191 mm per minute.
What is the correct feed rate for the second example?
-The correct feed rate is 191 mm per minute, as it was calculated using the available options and found to be the most accurate.
What is the focus of the third example problem?
-The third example calculates the time needed for the facing operation of a workpiece, where the operator is working with a diameter of 22 mm and a feed rate of 0.05 mm per revolution.
How do you calculate the time required for the facing operation in the third example?
-The time for the facing operation is calculated using the formula: T = (D + E) / (2 * F * N), where D is the diameter, E is the offset, F is the feed rate, and N is the machine speed. The resulting time is then converted into seconds.
What is the correct time for the facing operation in the third example?
-The correct time for the facing operation is 30 seconds, calculated from the given data and formula.
What does the fourth example problem involve?
-The fourth example calculates the time required to machine a surface, specifically making a uniform surface on a workpiece with a diameter of 22 mm and a feed rate of 0.1 mm per revolution.
How is the surface machining time calculated in the fourth example?
-The machining time is calculated by the formula: T = (L + La) / (F * N), where L is the length of the machining, La is the length to be machined, F is the feed rate, and N is the machine speed.
What is the correct time for surface machining in the fourth example?
-The correct time for surface machining is 35 seconds, based on the given values and the formula used.
What is the fifth example in the video script about?
-The fifth example problem involves determining the offset or shifting distance for a part being turned, with specific dimensions for the workpiece's diameter and length.
How is the offset shift calculated in the fifth example?
-The offset shift is calculated using the formula: X = (D - d) / (2 * L), where D is the initial diameter, d is the final diameter, and L is the length of the section being turned.
What is the correct offset shift for the fifth example?
-The correct offset shift is 3.125 mm, calculated based on the given measurements and formula.
Outlines
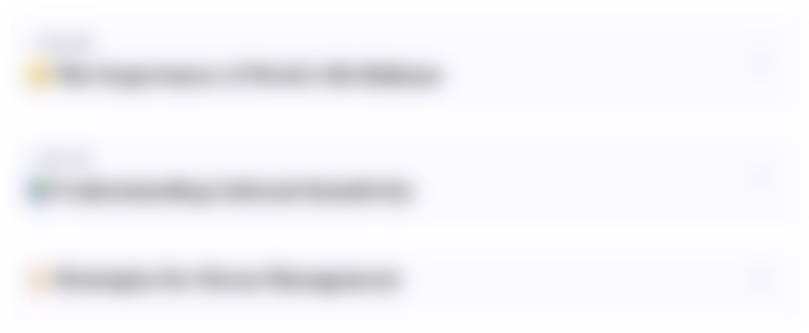
此内容仅限付费用户访问。 请升级后访问。
立即升级Mindmap
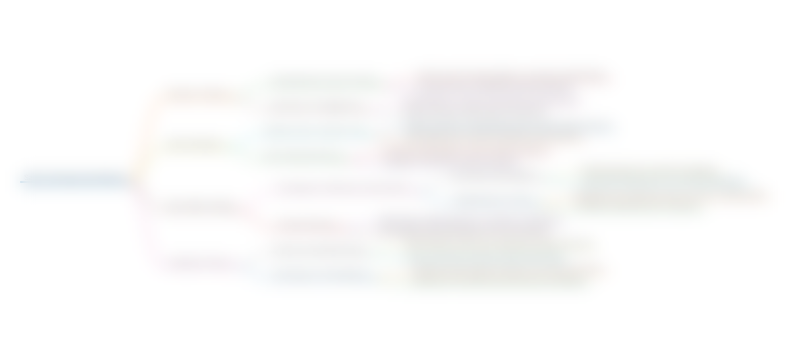
此内容仅限付费用户访问。 请升级后访问。
立即升级Keywords
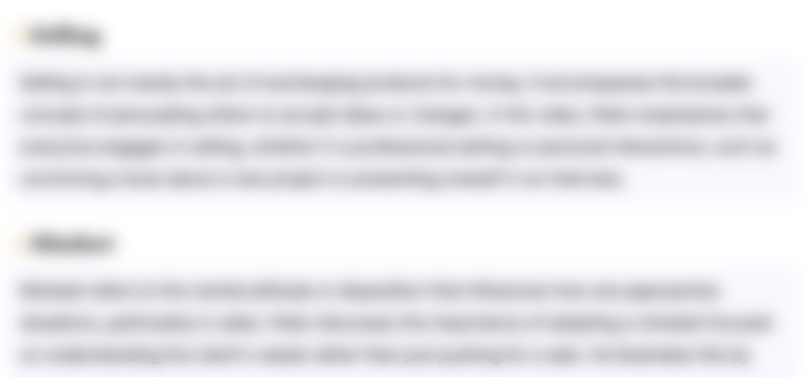
此内容仅限付费用户访问。 请升级后访问。
立即升级Highlights
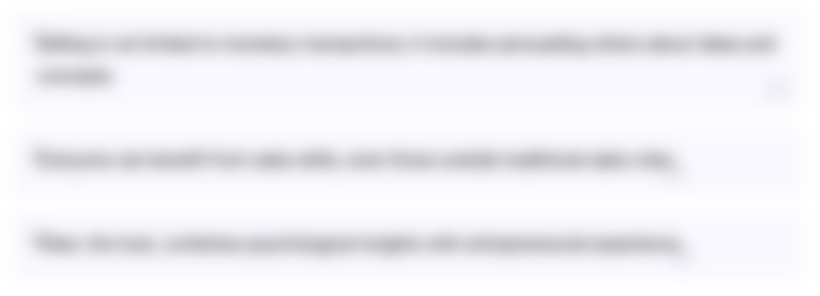
此内容仅限付费用户访问。 请升级后访问。
立即升级Transcripts
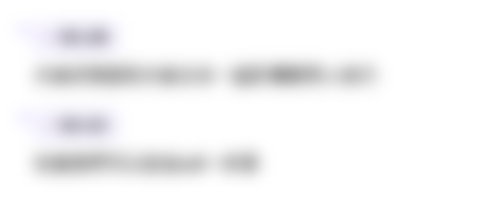
此内容仅限付费用户访问。 请升级后访问。
立即升级浏览更多相关视频
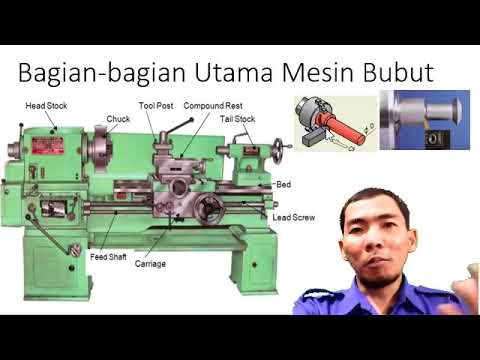
Bagian - bagian utama Mesin Bubut
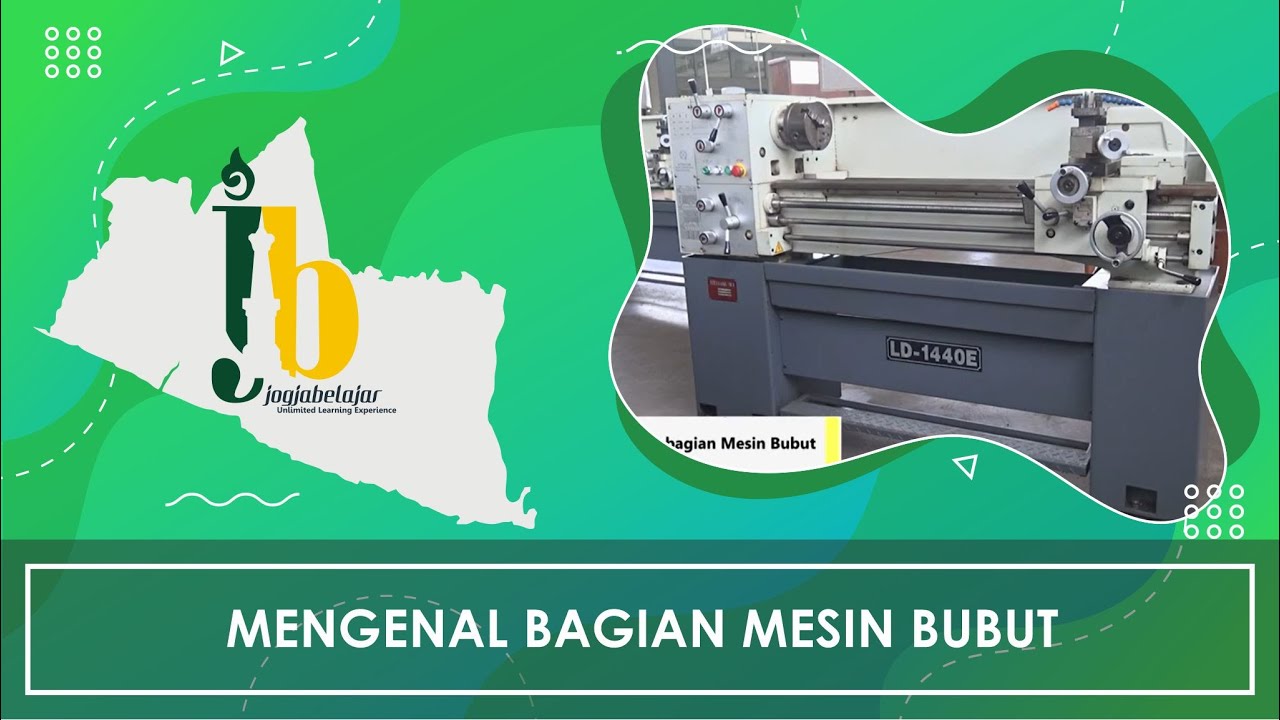
MENGENAL BAGIAN MESIN BUBUT
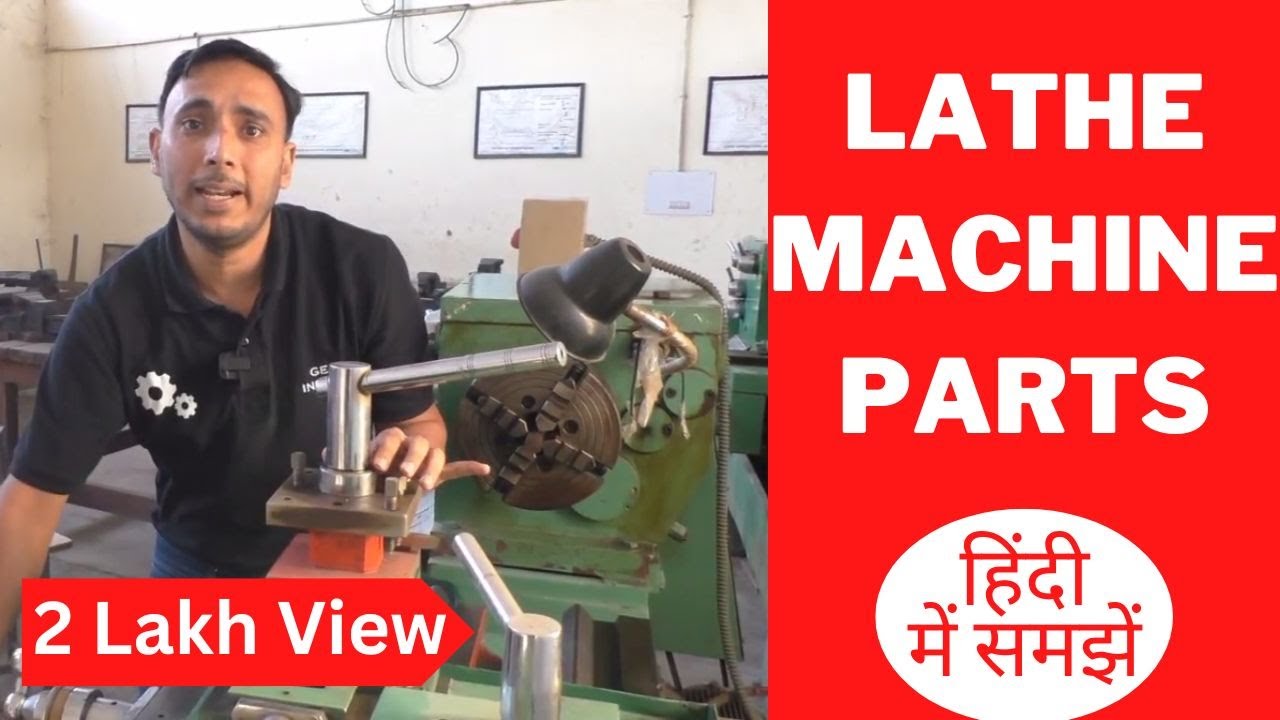
Lathe Machine Parts in Hindi
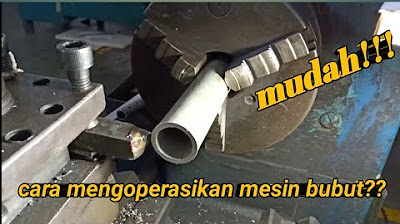
Cara mengoperasikan mesin bubut. (Tehnik dasar)||How to operate a lathe. (Basic technique)
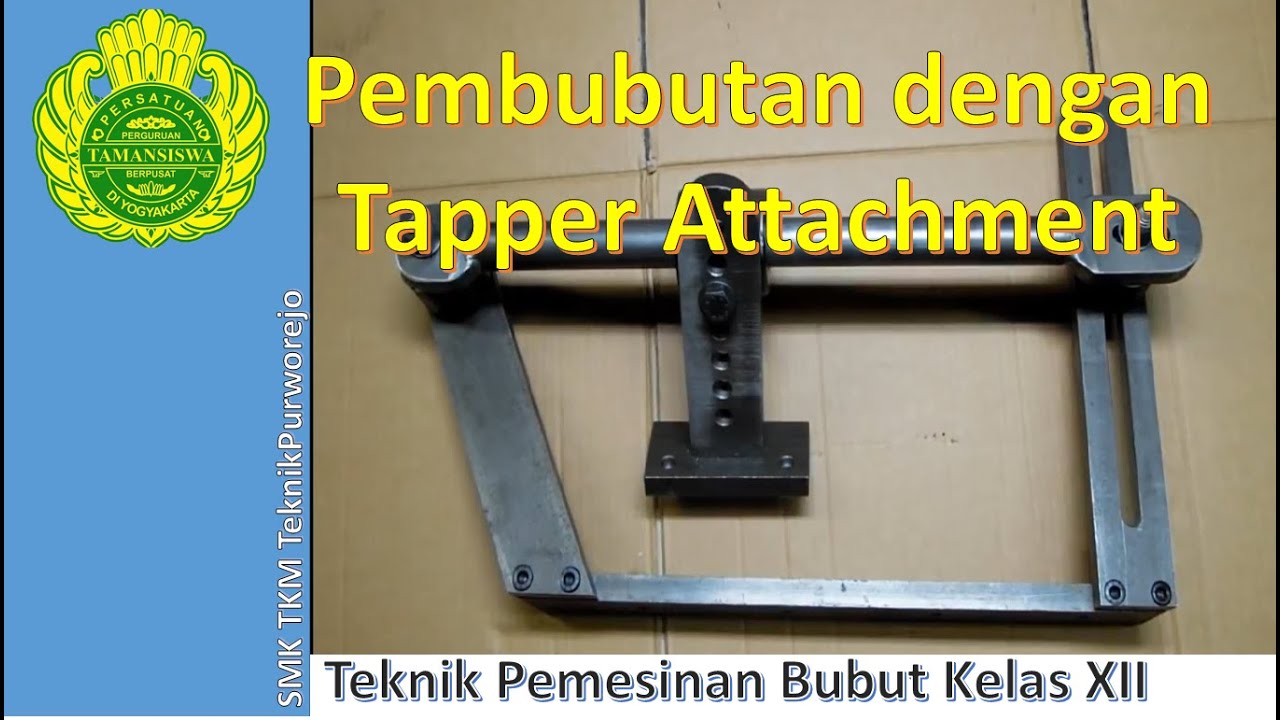
Pembubutan Menggunakan Taper Attachment || Teknik Pemesinan Bubut @Murdiyono

Penjelasan Bagian-Bagian dari Mesin Bubut dan Fungsinya
5.0 / 5 (0 votes)