How Toyota Changed The Way We Make Things
Summary
TLDRThe Toyota Production System, pioneered by Kiichiro Toyoda and Taiichi Ohno, revolutionized car manufacturing through 'Lean Manufacturing' and 'Just In Time' inventory, inspired by a supermarket visit. This system, combined with 'Kanban' and a focus on continuous improvement ('kaizen'), enabled Toyota to produce high-quality, affordable cars efficiently, leading to its global success and influencing industries beyond automotive production.
Takeaways
- 🚗 Toyota pioneered the 'Lean Manufacturing' philosophy, which focuses on efficiency, cost-effectiveness, and quality.
- 🏭 Post-WWII Japan's scarcity of resources led to the necessity of creative manufacturing approaches, including Toyota's innovative production methods.
- 🔧 Toyota's founder, Sakichi Toyoda, started with a loom business, but it was his son Kiichiro who established the motor company in 1937.
- 👀 The concept of 'Just In Time' (JIT) was inspired by the supermarket model, where production is aligned with consumption to minimize waste.
- 📝 The 'Kanban' system, developed by Taiichi Ohno, is a visual scheduling method that predates bar codes and helps in managing inventory flow.
- 🛠 Ohno observed inefficiencies in American car production, particularly the practice of repairing defects after production, which he sought to avoid.
- 🔴 The 'Andon' cord system allows any worker to stop the assembly line to address quality issues, fostering a culture of continuous improvement.
- 🔄 'Kaizen' is the principle of continuous, incremental improvement that has become a hallmark of the Toyota Production System (TPS).
- 📈 Toyota's production efficiency enabled them to produce a car every 1.6 man hours, significantly outpacing competitors during the oil crisis era.
- 🌏 The TPS has been emulated by various industries globally, including aerospace, technology, and healthcare, demonstrating its broad applicability.
- 🛣️ The oil crises of the 1970s highlighted the appeal of fuel-efficient Japanese cars, boosting Toyota's market position in the U.S.
Q & A
What is the significance of Toyota's 'Lean Manufacturing' system?
-Toyota's 'Lean Manufacturing' system, also known as the Toyota Production System, is significant because it revolutionized the way products are made by emphasizing efficiency, reducing waste, and focusing on continuous improvement. It has been widely emulated by companies around the world across various industries.
How did post-World War II Japan's economic situation influence Toyota's approach to manufacturing?
-Post-World War II Japan faced a scarcity of materials and resources, which forced Toyota to be creative and efficient with the limited supplies they had. This situation led to the development of the 'Just In Time' system, which aimed to minimize waste and maximize the use of available resources.
Who founded Toyota Motor Corporation and when was it established?
-Kiichiro Toyoda, the son of Sakichi Toyoda who had started a loom business, founded Toyota Motor Corporation in 1937.
What was the inspiration behind the 'Just In Time' system developed by Toyota?
-The 'Just In Time' system was inspired by a visit to a supermarket, specifically a Piggly Wiggly, where Taiichi Ohno was struck by the efficiency of customers choosing exactly what they wanted, when they wanted, and the idea of producing only enough parts to replace what was used in the next phase of production.
What is 'Kanban' and how does it relate to the Toyota Production System?
-'Kanban' is a sign-based scheduling method developed by Taiichi Ohno as part of the Toyota Production System. It shows the status of goods in, goods in production, and goods out, and is considered a precursor to modern bar codes.
How did the Toyota Production System address the issue of defective cars in the production line?
-The Toyota Production System addressed the issue of defective cars by implementing a cord at every station that any worker could pull to stop the entire assembly line if they spotted a problem. This encouraged immediate problem-solving and prevented the same mistake from recurring.
What is 'kaizen' and how is it related to the Toyota Production System?
-'Kaizen' is a Japanese philosophy of continuous, incremental improvement. It is a core component of the Toyota Production System, which emphasizes the importance of constantly seeking ways to improve processes and products.
How did the oil crises of the 1970s impact Toyota's success in the United States?
-The oil crises of the 1970s led to higher gas prices, making fuel-efficient Japanese cars, like those produced by Toyota, much more appealing to American consumers who were looking for cheaper-to-run alternatives to their gas-guzzling vehicles.
What is the significance of Toyota's achievement of producing a car every 1.6 man hours in 1972?
-Producing a car every 1.6 man hours in 1972 demonstrated Toyota's exceptional efficiency in manufacturing, which was significantly lower than their competitors. This efficiency was a direct result of the Toyota Production System and contributed to their competitive advantage.
Which other industries have adopted principles from the Toyota Production System?
-Industries such as aerospace (Boeing), technology (Intel), and healthcare (a Canadian hospital reducing ER wait times) have adopted principles from the Toyota Production System, highlighting its broad applicability and influence beyond the automotive industry.
What is the broader impact of the Toyota Production System on global manufacturing?
-The Toyota Production System has had a profound impact on global manufacturing by changing the approach to making things, emphasizing the avoidance of waste, the combination of craft with mass production, and the pursuit of constant improvement.
Outlines
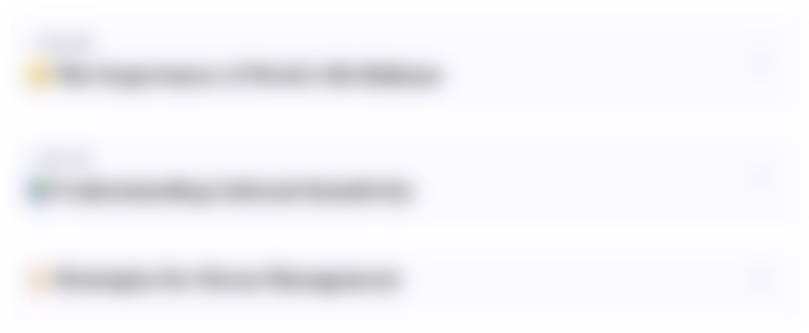
This section is available to paid users only. Please upgrade to access this part.
Upgrade NowMindmap
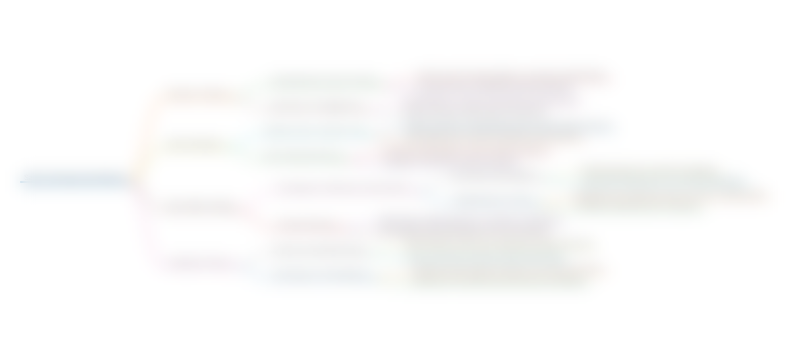
This section is available to paid users only. Please upgrade to access this part.
Upgrade NowKeywords
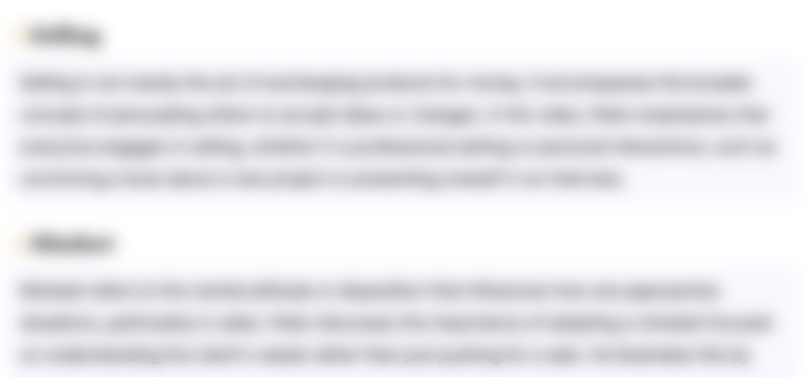
This section is available to paid users only. Please upgrade to access this part.
Upgrade NowHighlights
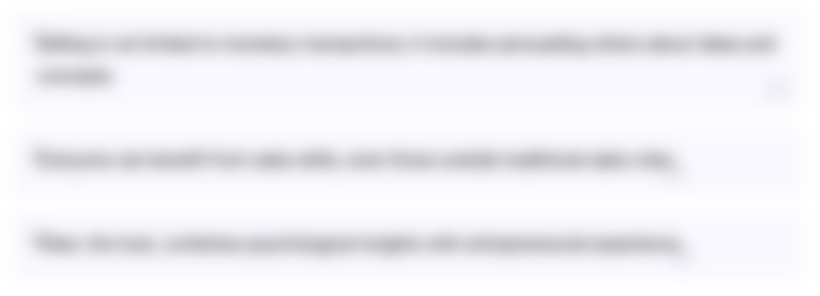
This section is available to paid users only. Please upgrade to access this part.
Upgrade NowTranscripts
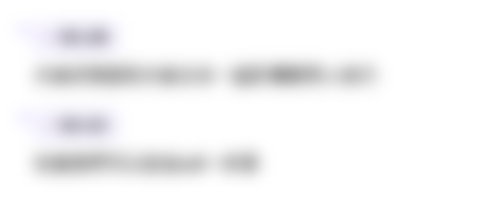
This section is available to paid users only. Please upgrade to access this part.
Upgrade NowBrowse More Related Video
5.0 / 5 (0 votes)