The History of Lean
Summary
TLDRThis script delves into the history and fundamentals of lean thinking, emphasizing its evolution over centuries, not a fleeting trend. It highlights the contributions of Frederick Taylor, Ford Motor Company, and Toyota's Taiichi Ono in developing lean principles. The script underscores the importance of standard work, flow, reducing waste, and focusing on customer value. It also credits Dr. Deming for quality management and the books 'The Machine That Changed the World' and 'Lean Thinking' for consolidating lean concepts. Lean is presented as a business system fostering a learning culture that eliminates waste and adds value to customers.
Takeaways
- ๐ The importance of understanding the history of lean thinking is emphasized to avoid considering it as a passing trend and to recognize its long-term development.
- ๐ ๏ธ Frederick Taylor's 'Scientific Management' is identified as the starting point of lean fundamentals, introducing the concept of a 'best way' to do work, which is foundational to standard work.
- ๐ญ Ford Motor Company's role in lean thinking is highlighted for pioneering manufacturing systems with interchangeable parts, leading to the creation of flow and optimal manufacturing processes.
- ๐ The challenges of variety in the automobile industry led to the development of economic order quantity, which inadvertently resulted in overproduction and waste, contrary to customer demand.
- ๐ซ The concept of overproduction as the 'grandfather of all waste' is introduced, as it leads to other forms of waste in the manufacturing process.
- ๐ The Toyota Production System (TPS) is recognized for addressing the complexity of manufacturing variety without the waste associated with overproduction, building on Ford's principles.
- ๐ท Taiichi Ohno's leadership in developing TPS is acknowledged, formalizing key lean concepts such as standard work, quality at the source, and error proofing.
- ๐ The principle of 'Pull replenishment' in TPS is noted for its efficiency in responding to customer demand, reducing waste.
- ๐ Dr. Deming's influence on lean thinking through quality management is recognized, emphasizing the importance of getting things right the first time to minimize waste.
- ๐ The consolidation of lean thinking is marked by the publication of 'The Machine That Changed the World' and 'Lean Thinking,' summarizing a century of operational excellence.
- ๐ฑ Lean thinking has evolved beyond manufacturing into a business system, promoting a learning culture that focuses on problem exposure and root cause solutions to eliminate waste.
- ๐ The script concludes by reinforcing that lean is not a temporary fad but a consolidated body of knowledge aimed at delivering the highest value to customers at the lowest cost.
Q & A
Why is understanding the history of lean thinking important?
-Understanding the history of lean thinking is important to prevent team members from viewing lean as a passing fad and to appreciate its long-term development over centuries, which provides a solid foundation for current practices.
What is the significance of Frederick Taylor's work in the context of lean thinking?
-Frederick Taylor's work, particularly his book 'Scientific Management,' is significant because it introduced the concept of a 'best way' to do work, which laid the groundwork for standard work and continuous improvement in lean thinking.
How did Ford Motor Company contribute to lean thinking?
-Ford Motor Company contributed to lean thinking by engineering manufacturing systems based on interchangeable parts, which allowed for flow and inventory reduction, setting the stage for a waste-free manufacturing process.
What challenges did the automobile industry face as it progressed in the 20th century?
-As the automobile industry progressed, it faced challenges due to customer demand for variety and customization, which introduced complexity and changeovers in the manufacturing process.
What is the economic order quantity and why was it not an effective solution for managing complexity?
-The economic order quantity is a mathematical calculation for determining optimal batch sizes in manufacturing to minimize changeover costs. However, it was not effective because it led to the production of goods not necessarily aligned with customer demand, resulting in overproduction and waste.
How did Toyota Production System address the waste of overproduction?
-Toyota Production System addressed the waste of overproduction by developing methods to manufacture variety and handle complexity without incurring the waste associated with overproduction, focusing on flow, quality, and pull replenishment.
Who is Taiichi Ohno and what is his contribution to lean thinking?
-Taiichi Ohno is a famed engineer at Toyota who was a key figure in the development of the Toyota Production System. His contributions include formalizing concepts like standard work, quality at the source, and error proofing processes.
What is the significance of Dr. Deming's work in the history of lean thinking?
-Dr. Deming's work emphasized quality management, advocating that getting things right the first time is crucial to reducing waste. His philosophy has been integral to lean thinking's focus on quality and continuous improvement.
How did the books by Jim Womack and Dan Jones contribute to the understanding of lean thinking?
-Jim Womack and Dan Jones's books, 'The Machine That Changed the World' and 'Lean Thinking,' consolidated a century of operational excellence thinking into a cohesive framework, popularizing the term 'lean' and its principles.
Why is lean thinking not just a manufacturing concept but also a business system?
-Lean thinking is not just a manufacturing concept because it has evolved into a business system that emphasizes building a learning culture, exposing and solving problems at their root cause, and focusing on delivering the highest value to customers at the lowest cost.
What is the core principle of lean thinking in terms of customer value?
-The core principle of lean thinking in terms of customer value is to focus on what the customer perceives as valuable, eliminating all forms of waste in the process, and ensuring that the business system is designed to deliver this value efficiently.
Outlines
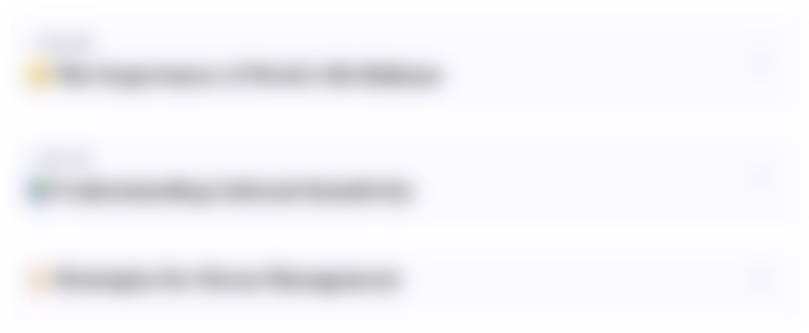
This section is available to paid users only. Please upgrade to access this part.
Upgrade NowMindmap
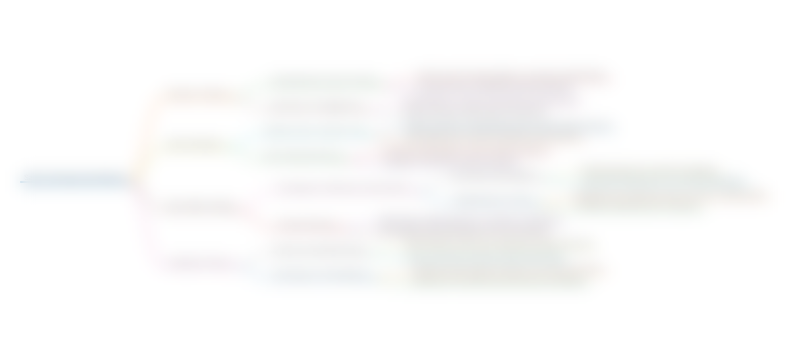
This section is available to paid users only. Please upgrade to access this part.
Upgrade NowKeywords
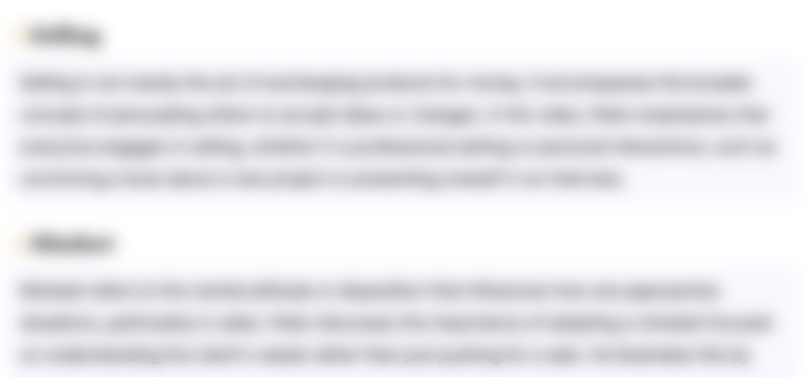
This section is available to paid users only. Please upgrade to access this part.
Upgrade NowHighlights
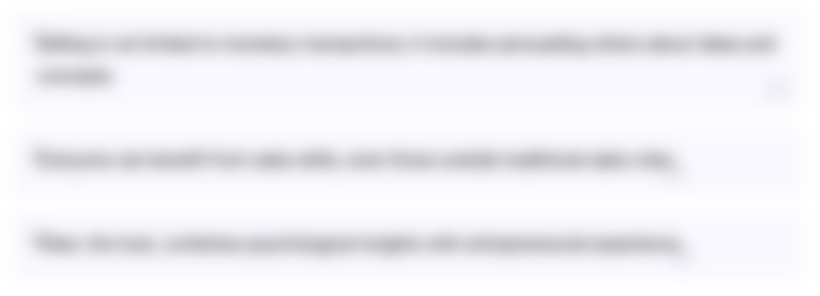
This section is available to paid users only. Please upgrade to access this part.
Upgrade NowTranscripts
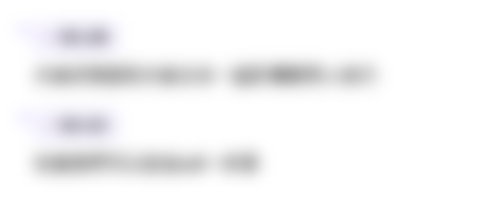
This section is available to paid users only. Please upgrade to access this part.
Upgrade NowBrowse More Related Video

Inilah SEJARAH masuknya 6 AGAMA di Nusantara
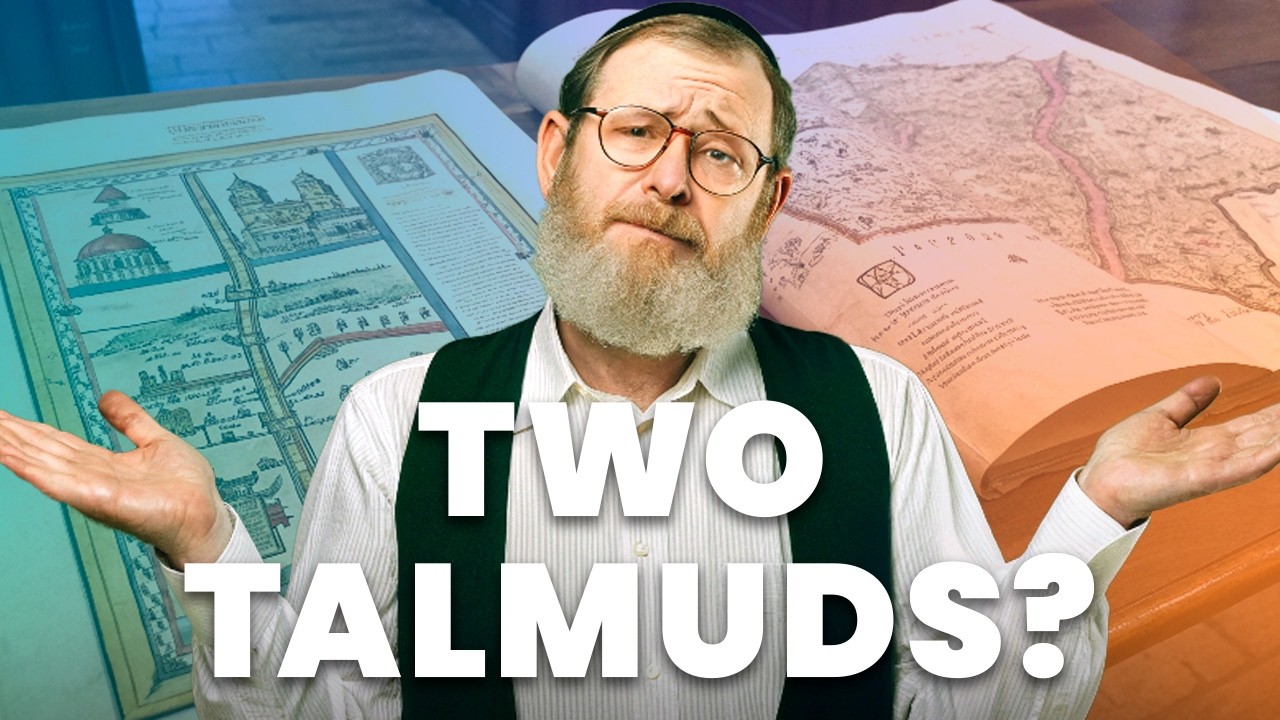
The Scholarly Debates of the Talmud | The Jewish Story | Unpacked

Dover Castle Documentary

ูุดุชู ูู ูุฐุง ุงูู ูุงู ูุฐุจุญ ุฐุจูุญุ ูุง ุงููู ุฃููุฏูู ูู ุงูุณููุงู | ุงูุฏุญูุญ

History of Renaissance | Impacts of Renaissance | World History | UPSC | General Studies

How IVF Works | The Story of Fertility | BBC Earth Science
5.0 / 5 (0 votes)