Set up a Mettler Toledo SLP33 to a 5032 IO-Link Master
Summary
TLDRIn a 2023 automation fair, Metler Toledo introduced the SLP 33, a singlepoint load cell with IO-Link technology. This tutorial demonstrates setting up the load cell using Rockwell's ArmorBlock 5000 IO-Link Master in Studio 5000 software. It covers adding the IO-Link Master to a project, configuring module definitions, enabling automatic device configuration, and setting up Class B IO-Link protocol. The process simplifies installation and provides extensive data for quick setup, showcasing the load cell's capabilities from 10 kg to 500 kg with various form factors and resolutions.
Takeaways
- 🔍 The SLP 33 is a singlepoint load cell by metler Toledo that uses IO-Link Technology.
- 🛠️ A Rockwell IO-Link Master is required for setup, simplifying the integration process.
- 💻 Demonstration includes setting up the load cell using Rockwell's ArmorBlock 5000 IO-Link Master in Studio 5000 software.
- 🔌 The IO-Link Master can be added to an existing Studio 5000 project by creating a new module.
- 📱 IO-Link Masters with add-on profiles can be filtered and added to the project for easy configuration.
- 🔄 Revision 2.011 firmware allows for Automatic Device Configuration (ADC) for all IO-Link sensors, enhancing longevity.
- 🌐 The connection status of the IO-Link Master can be monitored and adjusted using data and Ethernet status events.
- 🔧 Class B IO-Link protocol requires a different setup, including the use of the fifth pin and disabling the second pin on the IO-Link port.
- 📈 The 5032 block setup allows for configurable digital inputs or outputs with higher power ratings for certain ports.
- 🔎 Discovering modules online helps in identifying and adding IO-Link devices to the system.
- 📚 Updated device description files (IOD) are necessary for adding non-Rockwell devices, formatted as XML and registered through a modified EDS tool.
- 🛡️ Configuration changes for the load cell cannot be made online and require a download to the PLC.
- 📈 The Metler Toledo load cell supports a range from 10 kg to 500 kg with different form factors and resolutions.
- 🔑 Tags for the load cell, such as 'weight value', become available in the controller tags for monitoring and control.
Q & A
What is the SLP 33 load cell by metler Toledo?
-The SLP 33 is a single-point load cell that utilizes IO-Link Technology, which was unveiled at Rockwell's 2023 automation Fair.
What is required to set up the SLP 33 load cell with Rockwell's Armor Block 5000 IO-Link Master?
-An IO-Link Master is required for setting up the SLP 33 load cell, as it uses IO-Link Technology, which simplifies the total solution.
How do you add the 5032 IO-Link Master to an existing Studio 5000 project?
-In the project, you scroll down in the project explorer, right-click on the Ethernet module, and select 'New Module' to add the 5032 IO-Link Master.
What is the significance of the module definition area in configuring the IO-Link Master?
-The module definition area is where you assign the mode for each channel and the configuration of the module, which is crucial for setting up the proper communication and functionality with the connected devices.
What does ADC stand for and what is its role in IO-Link Masters?
-ADC stands for Automatic Device Configuration. It allows IO-Link Masters to set up automatic configuration for all IO-Link sensors, storing parameters and IOD files in the controller memory for better longevity.
What is the difference between Class A and Class B IO-Link protocols?
-Class B IO-Link protocol is different from Class A in that it uses earth ground and requires the fifth pin, which automatically disables the second pin on the IO-Link port when enabled.
How can additional power be configured for certain ports in the 5032 block?
-Extra power can be configured for Ports 2, 3, 6, and 7 by setting up the second channel as an output, which has a 2 amp rating, a significant improvement over other ports limited to 250 milliamps.
What is the process for adding a sensor to the IO-Link Master in Studio 5000?
-To add a sensor, you right-click on the IO-Link shown under the master add-on profile and select 'New Module' or 'Discover Module'. 'Discover Module' works while online and searches for all IO-Link devices connected to the master.
Why is it recommended to close all Rockwell software before registering new IOD files?
-It is recommended to close all Rockwell software before registering new IOD files to prevent issues with viewing newly registered devices. Rebooting the computer after registering the files can also clear up any issues.
How can you change the sensor configuration for the load cell in Studio 5000?
-You can change the sensor configuration by setting it all inside the project and downloading directly from the PLC through the master into the sensor. This process avoids the need for messaging.
What tags will be visible in the controller tags after the sensor is created?
-The actual device tags will show up based on the name of the module created. For example, if the module was named 'load cell one', the tag to look for would be 'weight value'.
What is the range and accuracy of the SLP 33 load cell demonstrated in the video?
-In the demo, the smallest form factor of the SLP 33 load cell is rated up to 20 kg with a C3 resolution, which is approximately 0.2 kg or half a pound accuracy.
Outlines
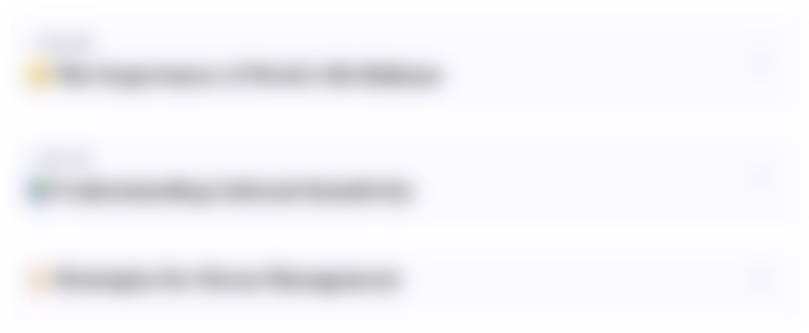
This section is available to paid users only. Please upgrade to access this part.
Upgrade NowMindmap
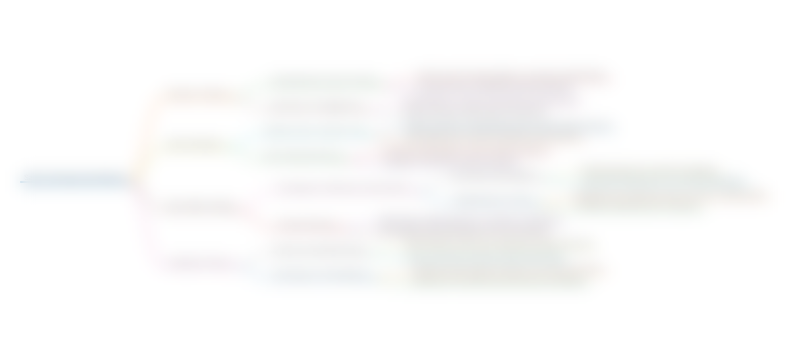
This section is available to paid users only. Please upgrade to access this part.
Upgrade NowKeywords
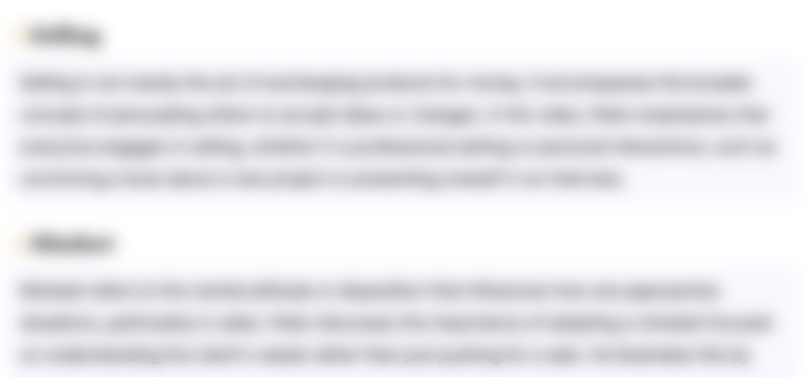
This section is available to paid users only. Please upgrade to access this part.
Upgrade NowHighlights
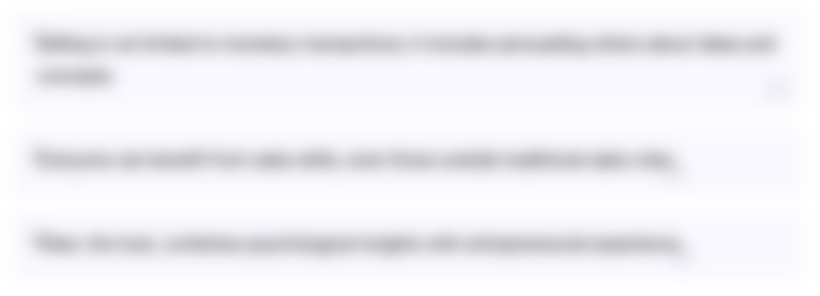
This section is available to paid users only. Please upgrade to access this part.
Upgrade NowTranscripts
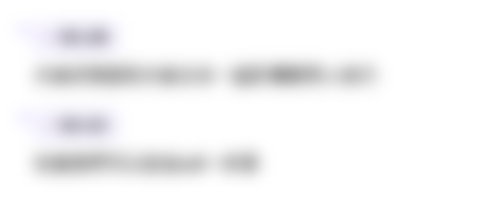
This section is available to paid users only. Please upgrade to access this part.
Upgrade Now5.0 / 5 (0 votes)