Safe By Design - Part 1
Summary
TLDRIn this interactive training session, a manufacturing engineer discusses multiple issues with parts being shipped to customers, including inaccurate shipping weights, contamination, illegible barcodes, and incorrect cutouts. The engineer collaborates with an automation specialist to devise solutions using technology like integrated load cells, automated cleaning systems, machine vision cameras, and 3D sensors. They also explore the benefits of using IO-Link technology for enhanced sensor data. The conversation highlights safety concerns and the importance of incorporating safety devices to protect employees in the workplace, with a plan to consult a safety expert for further guidance.
Takeaways
- 😀 The script features a live role-playing scenario aimed at addressing manufacturing problems in an assembly line environment.
- 😀 The manufacturing engineer faces four primary issues: inaccurate shipping weights, contaminated parts, missing or unreadable barcodes, and incorrect cutouts.
- 😀 The first solution proposed is using a standard weigh scale to accurately measure shipping weights, integrated with a control system for automated feedback.
- 😀 To solve contamination issues, an automated cleaning system (similar to a car wash) is suggested to clean the plates before barcode reading.
- 😀 A machine vision camera system is proposed to ensure barcodes are correctly placed and legible, sending data to the control system for validation.
- 😀 A 3D sensor is recommended for verifying that all cutouts on the plates are in the correct positions, enhancing quality control.
- 😀 The sequence of operations is discussed, where plates are weighed, cleaned, scanned for barcodes, inspected for cutouts, and then moved along a conveyor system.
- 😀 Safety is a key concern, and integrating safety devices, such as protective measures for employees working around the system, is highlighted as an important step.
- 😀 The use of IO-Link technology is discussed, which simplifies wiring and provides real-time diagnostics and feedback from sensors and actuators.
- 😀 Various sensor options, such as photoelectric sensors and distance measurement sensors, are explored to optimize machine performance and ensure proper detection of plates.
- 😀 The conversation concludes with a consideration of cost-effective solutions, including avoiding robots due to budget constraints, but focusing on improving safety for employees with safety devices.
Q & A
What are the main issues faced by the manufacturing engineer in the script?
-The main issues are inaccurate shipping weights, contamination on parts, illegible or missing barcodes, and misaligned cutouts.
How does the automation specialist suggest solving the issue of inaccurate shipping weights?
-The automation specialist suggests using a standard weight cell with an integrated system to send weight data to a control system, providing operator feedback through visual indicators like a stack light or HMI.
What solution does the automation specialist propose for cleaning contaminated parts before shipping?
-The automation specialist proposes an automated cleaning system, similar to a car wash, using a brush to clean the parts before they are scanned by the barcode reader.
How does the automation specialist address the barcode reading issue?
-The specialist recommends using a machine vision camera to read the barcode and verify that it is correct and placed in the right position on the plate, with visual feedback provided to the operator.
What is the solution for ensuring the cutouts are correctly positioned?
-A 3D sensor is proposed to verify the position and shape of the cutouts, ensuring they are accurate before shipping.
What is the proposed sequence of operation for the machine?
-The sequence starts with weighing the plate, followed by loading it onto a conveyor. It passes through an automated brush for cleaning, then under a barcode reader for verification, followed by a 3D sensor for cutout verification. The plate is then checked at the end and either sent to the good pile or the bad pile.
How does the system ensure the plate stops in the correct position for barcode scanning?
-A servo motor is used on the conveyor to ensure the plate stops at the exact position every time for accurate barcode reading.
How does the proposed system improve the wiring process?
-The system uses IO-Link technology, which allows sensors and actuators to be connected with a single cable, reducing wiring complexity and enhancing data communication.
What are some features of the IO-Link sensors that are beneficial for the system?
-IO-Link sensors offer customizable features like adjusting signal strength for photoelectric sensors, setting alarm thresholds for dirty sensors, and receiving detailed data from sensors like distance measurement and color sensors.
How does the automation system handle diagnostics?
-The system includes automatic diagnostics with no programming required. Any issues with connected devices, such as power failures or cable disconnections, trigger alerts that inform the operator of the problem.
Outlines
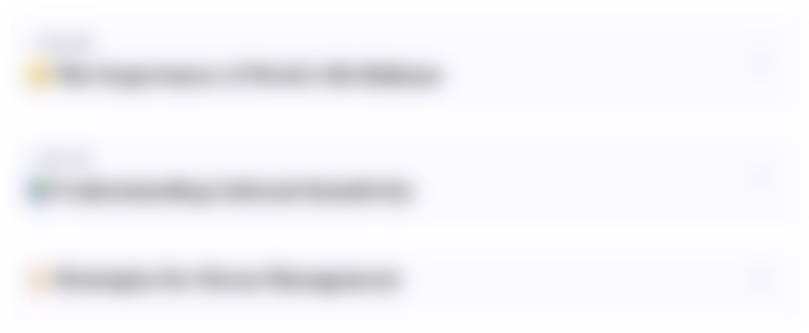
This section is available to paid users only. Please upgrade to access this part.
Upgrade NowMindmap
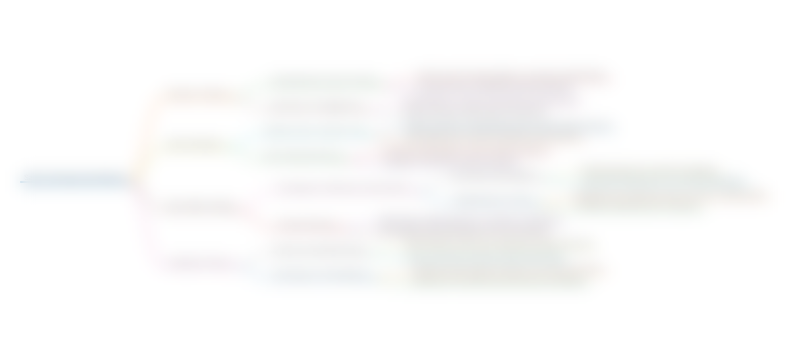
This section is available to paid users only. Please upgrade to access this part.
Upgrade NowKeywords
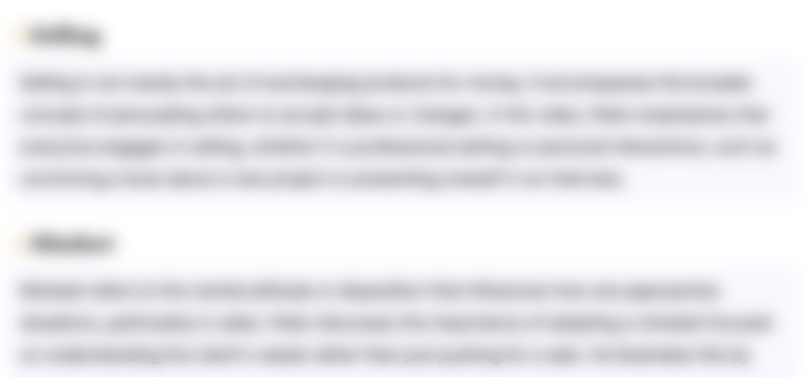
This section is available to paid users only. Please upgrade to access this part.
Upgrade NowHighlights
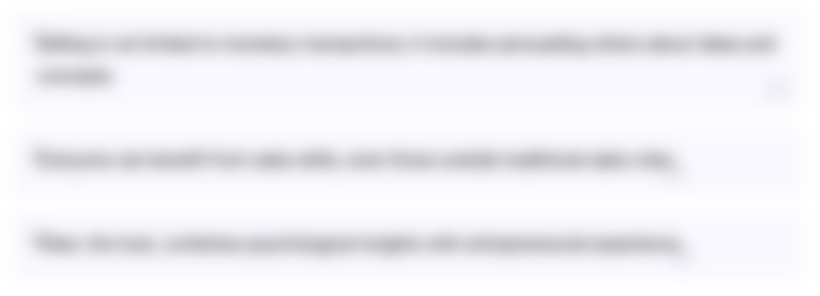
This section is available to paid users only. Please upgrade to access this part.
Upgrade NowTranscripts
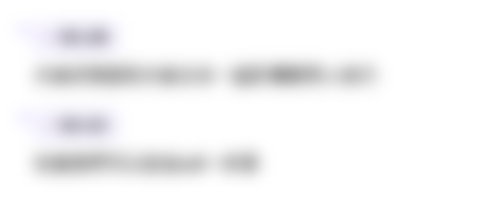
This section is available to paid users only. Please upgrade to access this part.
Upgrade NowBrowse More Related Video
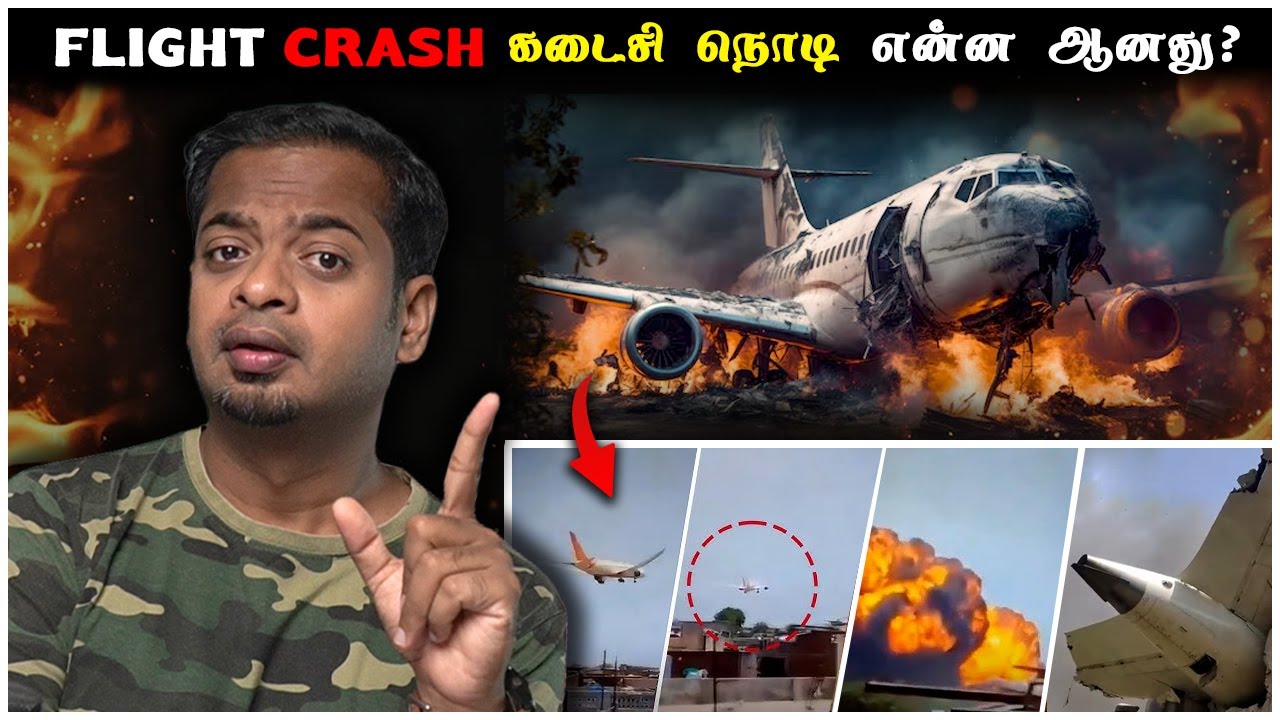
😱 WORST Flight Crash EVER 😡Ahmedabad Airport ல் உண்மையில் நடந்தது என்ன? | Mr.GK
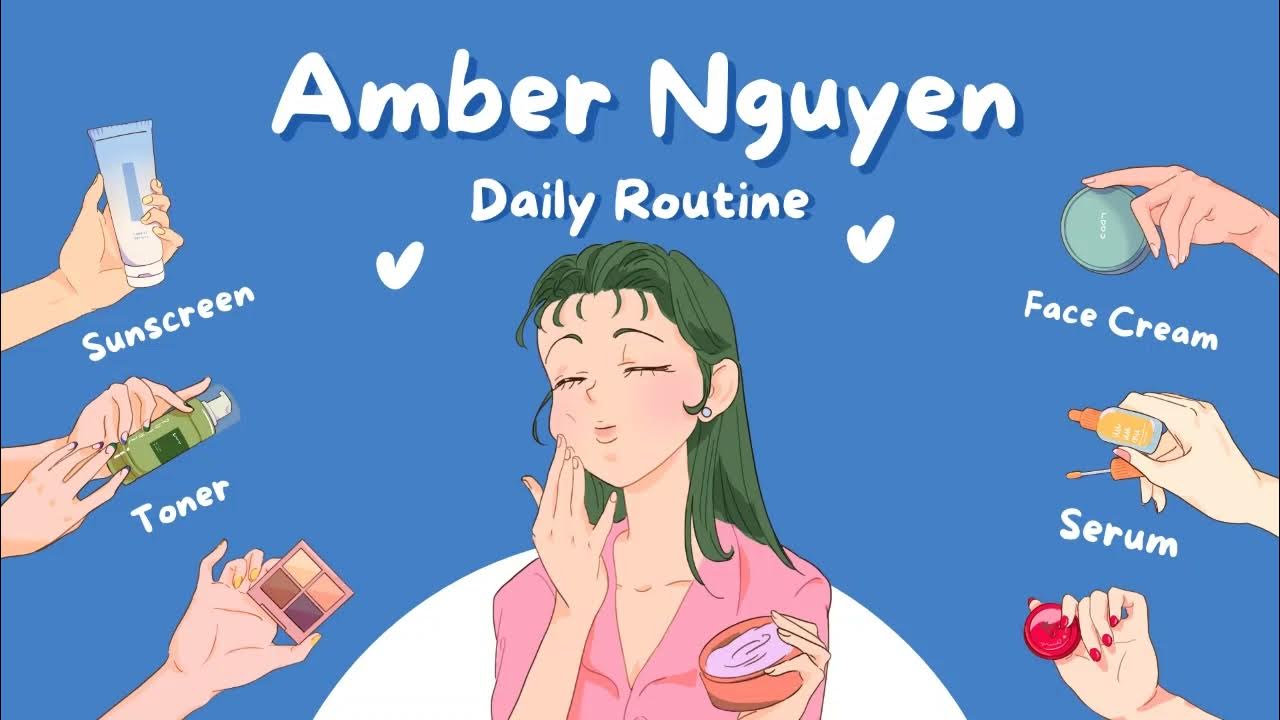
English for Business Studies Track 18 Leica's supply chain
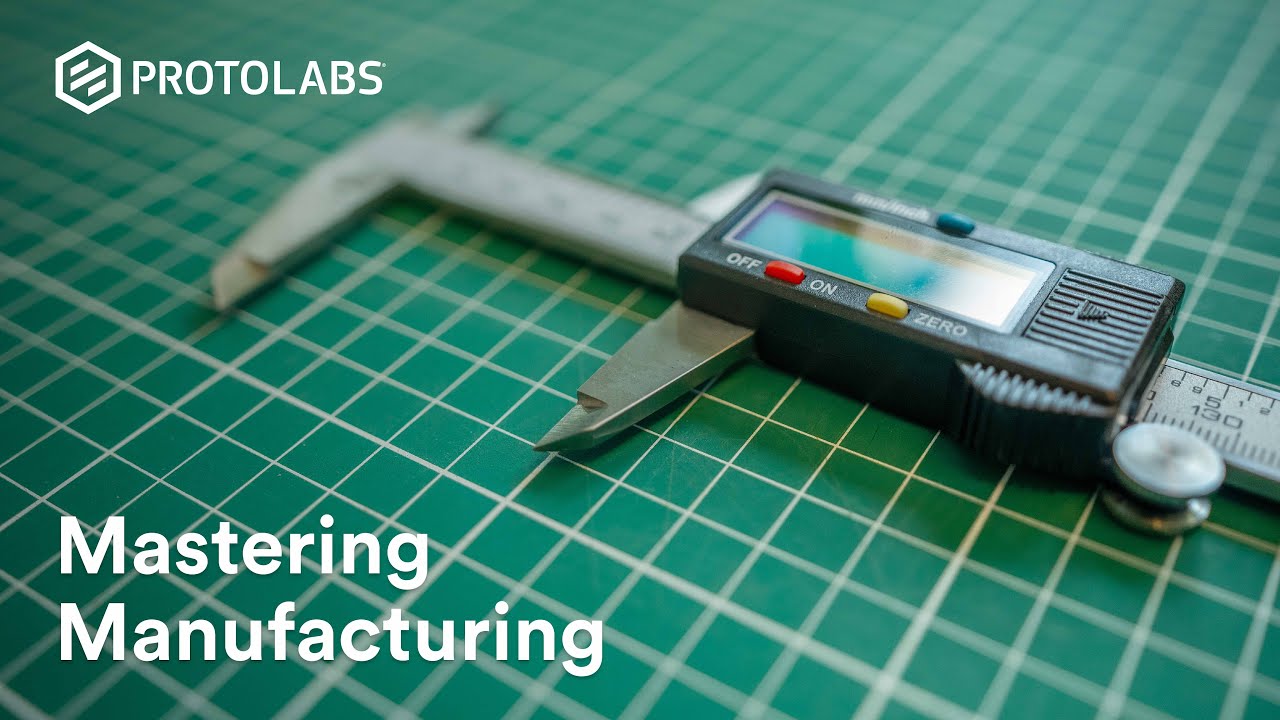
Tolerances Explained in CNC Machining (Defining for production)

Perbanyak Tanaman Dengan Kultur Jaringan

Proses Tuangan Logam Sand Casting Part 1
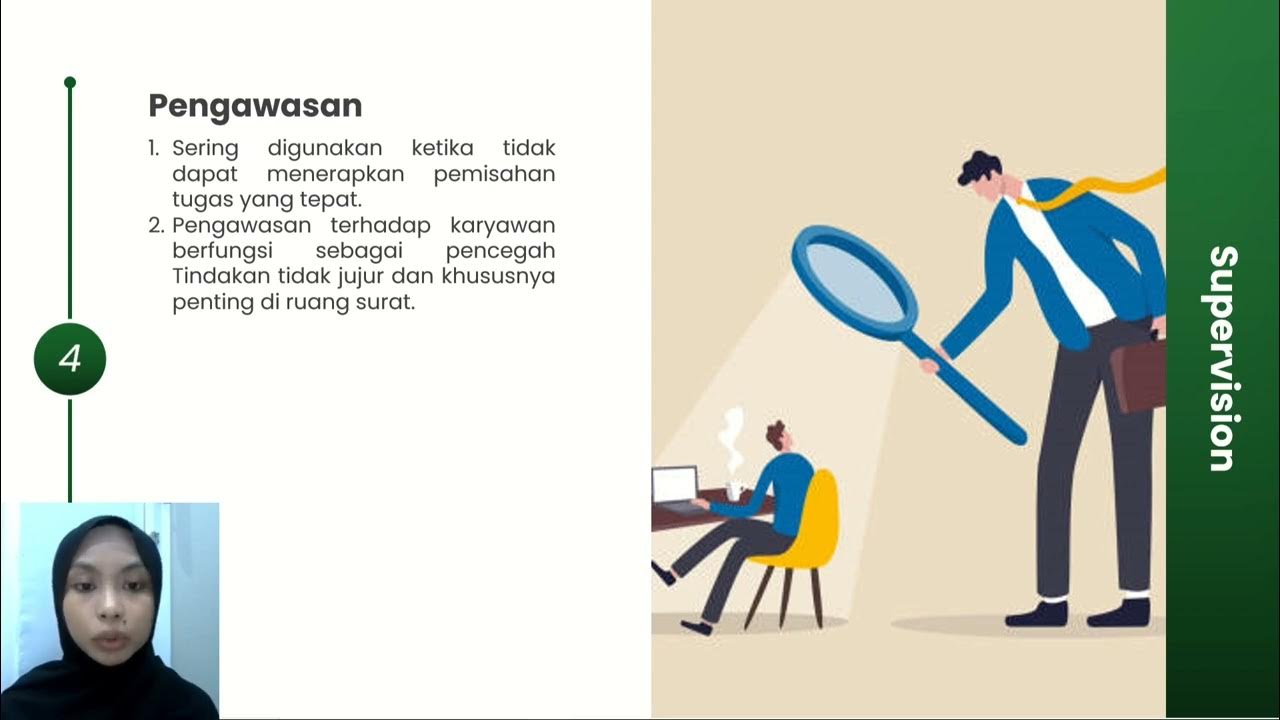
SIA-A-Presentasi Group 1 Revenue Cycle
5.0 / 5 (0 votes)