IO-Link Overview
Summary
TLDRThis video provides an in-depth look at IO-Link technology and Rockwell's IO-Link masters. IO-Link is a bi-directional communication protocol that connects sensors and actuators to automation systems, using a 3-wire cable for data transmission. The Rockwell IO-Link masters simplify integration into Ethernet/IP systems, offering two options: the Point IO card and Armor Block remote I/O. The video highlights the advanced features, including automatic device configuration (ADC) and flexible communication modes. Rockwell’s solution streamlines automation, reduces downtime, and offers easy setup via Studio 5000 software and Add-On Instructions (AOIs), making it an efficient choice for industrial automation.
Takeaways
- 😀 IO-Link is an open standard, point-to-point communication protocol used for automation systems.
- 😀 The protocol is bi-directional, allowing both sending and receiving of data, but is limited to short distances (up to 20 meters).
- 😀 IO-Link uses a 24V DC serial communication system and can transmit data at three rates, with its masters capable of handling digital and analog signals.
- 😀 IO-Link connects sensors and actuators to automation systems, but not directly to common industrial protocols like SIP networks.
- 😀 The IO-Link master connects the IO-Link device to the Ethernet/IP system, ensuring communication with the higher-level controller (PAC or PLC).
- 😀 In case of communication errors (e.g., cable faults or power surges), the IO-Link master attempts retransmissions and alerts operators after multiple failures.
- 😀 There are four types of IO-Link data transmissions: process data, value status, device data, and events.
- 😀 Process data is cyclically transmitted and represents the current state of the sensor or actuator, while device data holds detailed device information, transmitted acyclically.
- 😀 Rockwell offers two types of IO-Link masters: a point I/O card for up to four devices and the ArmorBlock remote I/O block, which can handle up to eight devices.
- 😀 The ArmorBlock remote I/O line includes IO-Link hubs for easy and cost-effective I/O network expansion.
- 😀 Rockwell’s IO-Link solution integrates seamlessly with Studio 5000 software, enabling easy setup of masters and devices via add-on profiles (AOP) and automatic device configuration (ADC) for faster deployment.
Q & A
What is IO-Link?
-IO-Link is a worldwide open standard communication protocol used for point-to-point communication. It allows bi-directional data transfer between devices in an automation system.
What are the key features of IO-Link communication?
-IO-Link uses a robust 24-volt DC serial communication system and operates at three potential rates. It supports the transmission of digital signals and analog values, and is limited to short distances (up to 20 meters).
How does IO-Link handle communication errors?
-If an error is detected, the message is retransmitted up to two additional times. If the third attempt fails, the IO-Link master recognizes the failure and notifies the high-level controller, which then alerts operators or maintenance staff.
What are the types of data transmitted via IO-Link devices?
-IO-Link devices transmit four types of data: Process Data (sensor/actuator state), Value Status (indicates whether process data is valid), Device Data (device details like serial numbers and parameters), and Events (error/warning messages triggered by the device).
What are the two types of IO-Link masters offered by Rockwell?
-Rockwell offers two types of IO-Link masters: the Point IO card, which connects four IO-Link devices, and the ArmorBlock remote IO block, which can handle up to eight IO-Link devices.
What is the ArmorBlock remote IO block, and how does it expand IO-Link connections?
-The ArmorBlock remote IO block is mounted directly in the field and has four ports. With a splitter, it can support up to eight IO-Link devices. It also has IO-Link hubs for easy and cost-effective expansion of IO connections.
How does Rockwell's IO-Link solution improve integration in automation systems?
-Rockwell’s IO-Link solution allows seamless integration through the Studio 5000 software, where users can set up the IO-Link master using an add-on profile (AOP) and easily configure connections with master devices.
What are the five different modes available for configuring Rockwell’s IO-Link masters?
-The five modes for configuring Rockwell’s IO-Link masters are: IO-Link mode (for communication), DI (Digital Input), DO (Digital Output), Disabled (no assigned mode), and Fallback mode (configures an IO-Link device to behave as a standard digital input for faster response time).
What is the function of the Fallback mode in Rockwell's IO-Link masters?
-Fallback mode allows the IO-Link master to configure an IO-Link device and then instruct it to behave like a standard digital input. This helps increase the response time of digital inputs while ensuring ease of replacement.
How does Rockwell’s IO-Link solution simplify device setup?
-Rockwell’s IO-Link masters allow automatic device configuration using the Add-on Profile (AOP) and Auto Device Configuration (ADC) features, enabling new devices to be automatically set up by the PLC without requiring manual intervention or additional software.
Outlines
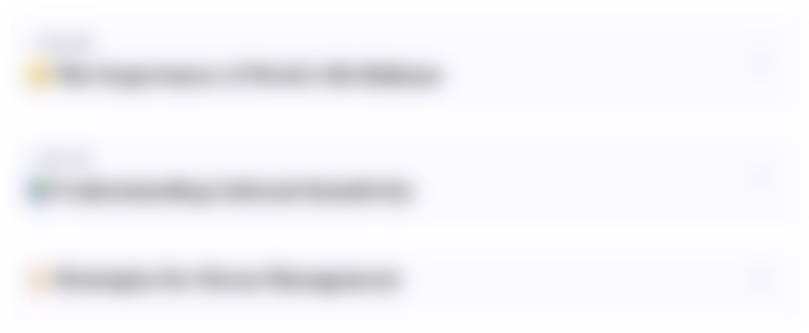
This section is available to paid users only. Please upgrade to access this part.
Upgrade NowMindmap
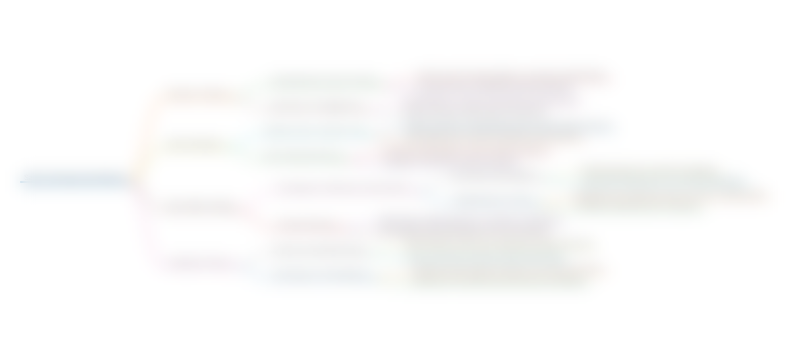
This section is available to paid users only. Please upgrade to access this part.
Upgrade NowKeywords
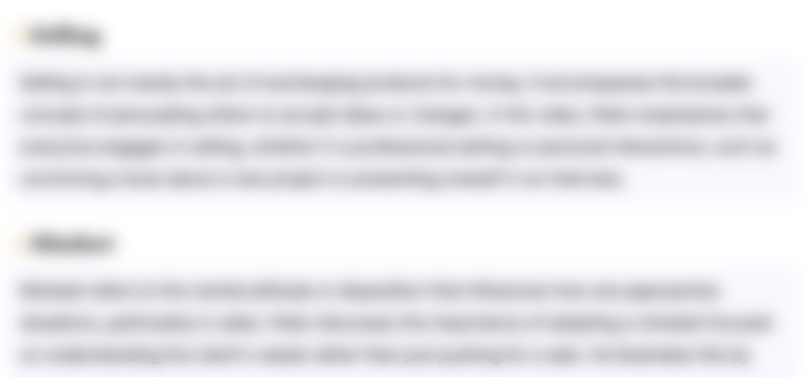
This section is available to paid users only. Please upgrade to access this part.
Upgrade NowHighlights
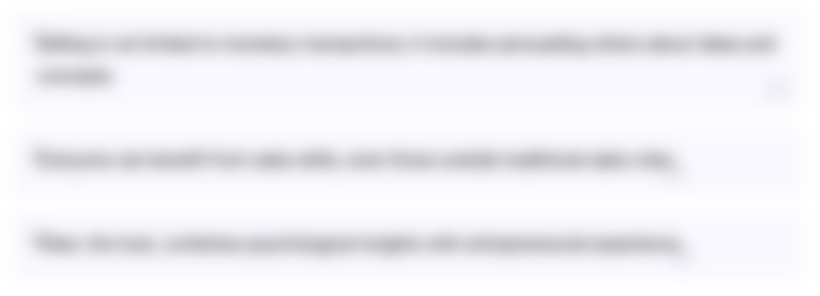
This section is available to paid users only. Please upgrade to access this part.
Upgrade NowTranscripts
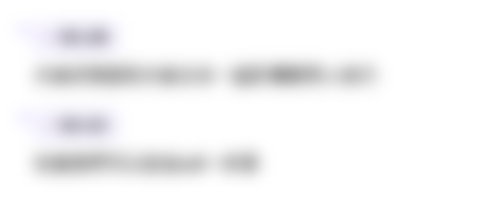
This section is available to paid users only. Please upgrade to access this part.
Upgrade Now5.0 / 5 (0 votes)