An Introduction To The Toyota Production System
Summary
TLDRIn this insightful dialogue, Lewis and Larry from Toyota share their extensive experience with the Toyota Production System (TPS), emphasizing its foundational principles like Just-In-Time, Jidoka, and continuous improvement. They highlight the importance of respecting people and engaging them in the process of identifying and eliminating waste, fostering a culture of improvement. The conversation also touches on the adaptability of TPS to technological advancements and the challenges faced by other companies in implementing similar systems, advocating for a gradual and persistent approach to change.
Takeaways
- 😀 Alerian and Larry from Toyota shared insights on the Toyota Production System (TPS) and their roles in promoting its principles within the company.
- 🏭 The foundation of TPS is 'standardized work', with 'just in time' and 'automation with a human touch' as supporting pillars, all aimed at eliminating waste ('muda').
- 🔧 The uniqueness of TPS lies in its dynamic manufacturing approach that builds to customer demand, allowing flexibility and problem exposure for continuous improvement.
- 👥 Respect for people is a core strength of TPS, emphasizing team member engagement and their role as the best resource for process improvements.
- 🕒 'Just-in-time' in TPS is about producing and conveying only what is needed, when it is needed, to eliminate waste and enhance efficiency.
- 🔄 'Jidoka' is a TPS concept that halts the production line at the first sign of a problem, ensuring quality and preventing the propagation of defects.
- 🛠️ The seven types of waste in TPS include overproduction, waiting, transportation, processing, inventory, motion, and correction, all targeted for elimination.
- 🤝 Toyota's approach to managing people involves continuous improvement and respect for individuals, encouraging team members to voice suggestions and improvements.
- 🔄 The Toyota Way emphasizes the importance of involving employees in the process of Kaizen (improvement), recognizing their expertise and contributions.
- 🔗 Toyota views its suppliers as partners, sharing the TPS philosophy to ensure mutual success and a commitment to quality and efficiency.
- 🌐 While technology and globalization are changing the landscape, Toyota remains committed to enhancing TPS rather than changing its fundamental principles, focusing on human dignity and respect.
Q & A
What is the role of Lewis Omnia at Toyota?
-Lewis Omnia is a manager at Toyota with 25 years of experience primarily in manufacturing and assembly. For the last year and a half, he has been managing the PPS group and manufacturing skills development, which includes training the organization on PPS tools and their applications.
What does Larry Edwards do at Toyota, and how long has he been there?
-Larry Edwards is a production group leader at Toyota. He has been with the company for 22 years and joined the TPS team about a year ago. He is currently learning PPS and in the process of becoming TPS certified.
Can you explain the Toyota Production System (TPS) and its main elements?
-The Toyota Production System (TPS) is designed to reduce costs by eliminating waste, known as 'muda'. It is symbolized as a house with standardized work as the foundation, 'just-in-time' and 'jidoka' (automation with a human touch) as the two pillars, and continuous improvement as the roof.
What makes the Toyota Production System unique compared to traditional production systems?
-The uniqueness of TPS lies in its dynamic manufacturing method that builds to customer demand, allowing for flexibility and change. It follows TPS principles to expose problems and uses 'kaizen' for problem-solving, which leads to waste elimination and cost reduction.
What is 'just-in-time' (JIT), and how is it applied at Toyota?
-Just-in-time (JIT) refers to manufacturing and conveyance of what is needed, when it is needed, and in the exact amount needed. It eliminates waste and enhances work efficiency. At Toyota, JIT is applied through continuous flow processing, the pull system with Kanban, building to customer demand, and leveling of volume and variety.
How does Toyota ensure the quality of its vehicles through the Toyota Production System?
-Toyota ensures quality through 'jidoka', which notifies of process problems. It involves fixed position stops, allowing team members to stop the line when abnormalities occur, an 'andon' system for calling assistance, and poka-yoke devices for error-proofing to detect and stop abnormalities.
What are the seven types of muda in the TPS, and how do they affect efficiency?
-The seven types of muda in TPS are overproduction, waiting, transportation, processing, inventory, motion, and correction. These wastes affect efficiency by adding unnecessary steps, time, and costs to the manufacturing process, which ultimately need to be reflected in the product's price.
How does Toyota manage its people within the Toyota Production System?
-Toyota manages its people by following the two main pillars of the Toyota Way: continuous improvement and respect for people. It encourages team members to use these values in their daily work, allowing them to have a voice in process setup and improvements.
What is the approach to managing the supply chain in the Toyota Production System?
-Toyota views its suppliers as partners and an extension of its plant. It has a dedicated team working alongside suppliers, challenging and supporting them to improve in all aspects of TPS. This approach is based on mutual respect and trust.
How does Toyota respond to the rapid pace of innovation and change in the industry?
-Toyota responds by funding a research and development division that always looks at new innovations and technologies. While the fundamentals of TPS do not change, the system gets enhanced with technology, focusing on making improvements and increasing efficiency.
What advice do you have for people who may move on to careers in manufacturing or service operations?
-The advice given is to treat the company as if it were your own, look for ways to improve and prove operations, and become more efficient. Be open to change, embrace teamwork, and continuously improve your job for satisfaction and personal growth.
Outlines
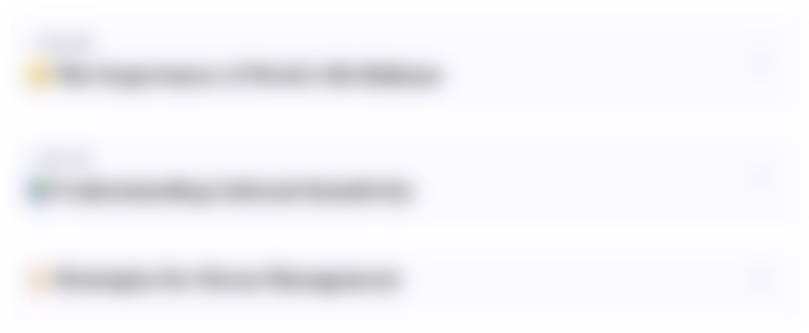
Этот раздел доступен только подписчикам платных тарифов. Пожалуйста, перейдите на платный тариф для доступа.
Перейти на платный тарифMindmap
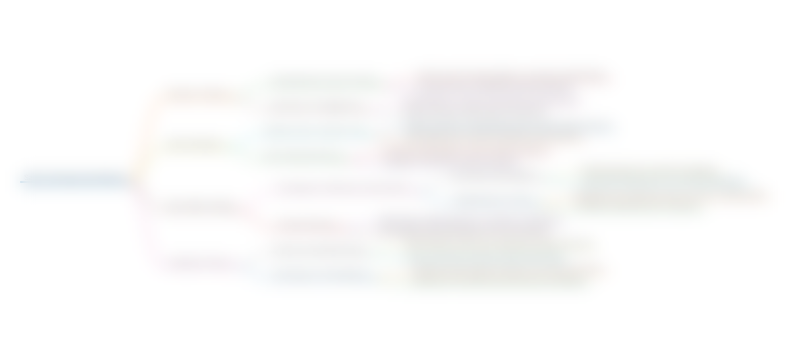
Этот раздел доступен только подписчикам платных тарифов. Пожалуйста, перейдите на платный тариф для доступа.
Перейти на платный тарифKeywords
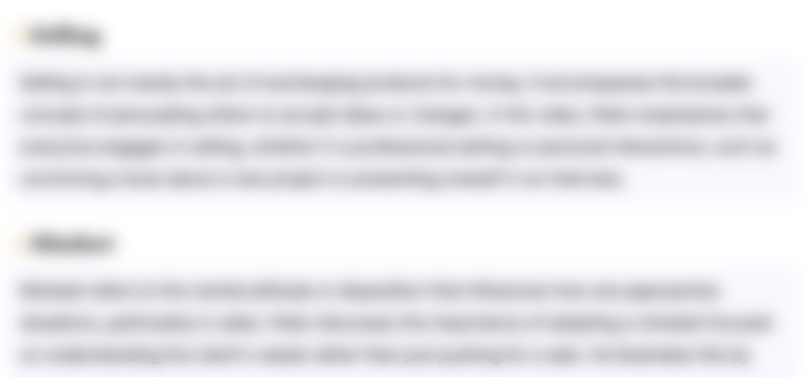
Этот раздел доступен только подписчикам платных тарифов. Пожалуйста, перейдите на платный тариф для доступа.
Перейти на платный тарифHighlights
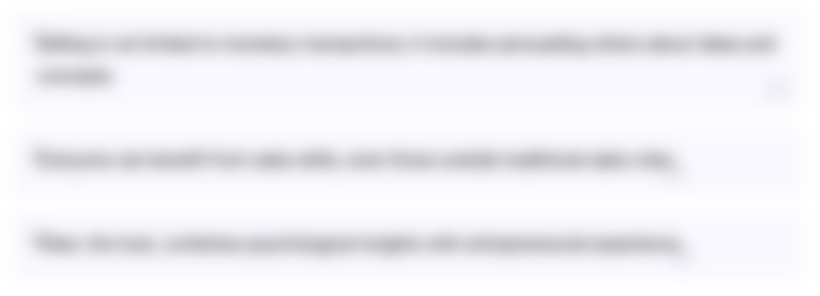
Этот раздел доступен только подписчикам платных тарифов. Пожалуйста, перейдите на платный тариф для доступа.
Перейти на платный тарифTranscripts
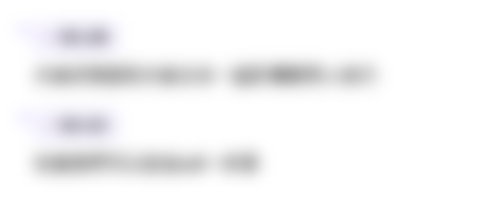
Этот раздел доступен только подписчикам платных тарифов. Пожалуйста, перейдите на платный тариф для доступа.
Перейти на платный тариф5.0 / 5 (0 votes)