Modelo Toyota de Produção - Just In Time & Kanban
Summary
TLDRThe Toyota Production System (TPS) revolutionized manufacturing with its two core principles: Just in Time (JIT) and automated automation in abnormal situations. Originating from Sishi Toyota’s innovative automatic loom in the late 19th century, TPS evolved through the work of Kiichiro Toyoda, who adapted mass production methods for automobile manufacturing. Despite initial challenges, the system emphasized efficiency, quality control, and waste reduction, eventually gaining global recognition. TPS’s success, including its role in Toyota's recovery during the 1973 oil crisis, showcases its lasting impact on modern production techniques worldwide.
Takeaways
- 😀 The Toyota Production System (TPS) emphasizes a harmonious production flow, eliminating waste and ensuring precise products for society.
- 😀 TPS is built upon two main pillars: automation in abnormal situations and Just in Time (JIT) production.
- 😀 The concept of automation in abnormal situations originated with Shishi Toyota, who invented the automatic loom (TR) to prevent defects in textile production.
- 😀 Shishi Toyota’s loom innovations included automatic thread-break detection and a mechanism to stop the loom when thread breaks, ensuring high-quality output.
- 😀 The Toyota automatic loom, Model G, enabled uninterrupted operation and allowed a single operator to manage over 30 looms simultaneously.
- 😀 The second pillar of TPS, Just in Time, was inspired by Toyota's founder's desire to produce only what was needed, when needed, and in the necessary quantity.
- 😀 In 1933, Toyota pivoted to automotive production, utilizing lessons learned from loom manufacturing to develop an efficient automotive production system.
- 😀 The concept of JIT was refined and implemented to optimize production by focusing on minimizing waste and improving operational efficiency.
- 😀 Taishi Ono played a crucial role in perfecting the JIT concept by creating a system inspired by supermarkets, where each process requests materials only as needed.
- 😀 By the 1970s, TPS had spread beyond Toyota and was adopted by industries worldwide, particularly after the company demonstrated resilience during the 1973 oil crisis.
Q & A
What is the Toyota Production System (TPS)?
-The Toyota Production System (TPS) is a manufacturing methodology aimed at eliminating waste, improving efficiency, and producing high-quality products. It focuses on continuous improvement through principles like 'Just-in-Time' (JIT) and 'Automation in Anomalous Situations' (Jidoka).
Who is Sakichi Toyoda and how did he contribute to TPS?
-Sakichi Toyoda, the father of the Toyota Group, invented the automatic loom in 1890, which was a major breakthrough in manufacturing. His invention introduced automation to prevent defects in production, a principle later expanded upon in the Toyota Production System (TPS).
What is the principle of 'Jidoka' in TPS?
-'Jidoka' refers to the principle of automation with a human touch, where machines are designed to automatically stop when a defect is detected. This ensures that defective products are not produced and allows for quick identification and resolution of issues in the production line.
How did Kiichiro Toyoda influence the development of TPS?
-Kiichiro Toyoda, the son of Sakichi, expanded on his father’s principles and applied them to the automobile industry. He developed the Just-in-Time (JIT) system and integrated it into automotive production, significantly improving efficiency and reducing waste in the manufacturing process.
What is the concept of Just-in-Time (JIT) and how did it evolve?
-Just-in-Time (JIT) is a production principle that focuses on producing only what is necessary, when it is necessary, and in the required quantity. Kiichiro Toyoda introduced JIT after observing mass production techniques in the U.S. and adapted them for Toyota’s automotive production, focusing on efficiency and reducing inventory.
What role did Sakichi Toyoda's automatic loom play in the development of TPS?
-The automatic loom, invented by Sakichi Toyoda, was the first step towards automation in manufacturing. Its ability to stop automatically when a defect was detected laid the foundation for Jidoka, one of the key principles of TPS, focusing on preventing defects and improving production efficiency.
How did the Toyota Production System address the challenge of producing high-quality products?
-TPS addressed this challenge through its dual focus on Jidoka and Just-in-Time. Jidoka ensures defects are immediately identified and corrected, while JIT minimizes waste and ensures products are only made when necessary, thereby maintaining high quality without excess production.
What was the resistance to the Just-in-Time system and how was it overcome?
-Initially, workers were resistant to the Just-in-Time system due to their familiarity with traditional production methods. The system required careful training and a shift in mindset. Taishi Ono, a key figure in implementing JIT, led extensive training efforts to help workers understand and adopt the new approach.
How did the Toyota Production System spread globally?
-By the 1970s, the Toyota Production System became widely recognized for its efficiency and effectiveness, especially during the 1973 oil crisis. As a result, other industries and manufacturers worldwide began adopting the TPS methodology to improve their own production systems.
What impact did the Toyota Production System have on global manufacturing practices?
-The Toyota Production System revolutionized global manufacturing by introducing lean practices such as Just-in-Time and automation to improve efficiency, reduce waste, and ensure high-quality production. It became a model for manufacturers worldwide, particularly in times of economic challenges.
Outlines
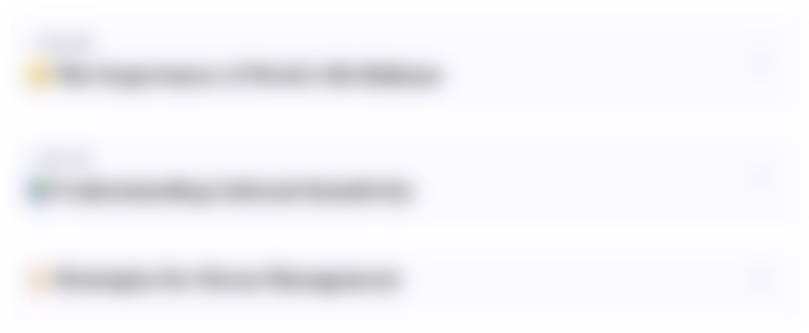
This section is available to paid users only. Please upgrade to access this part.
Upgrade NowMindmap
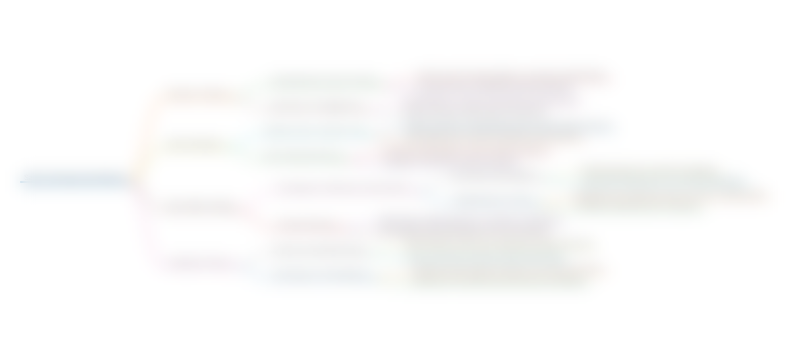
This section is available to paid users only. Please upgrade to access this part.
Upgrade NowKeywords
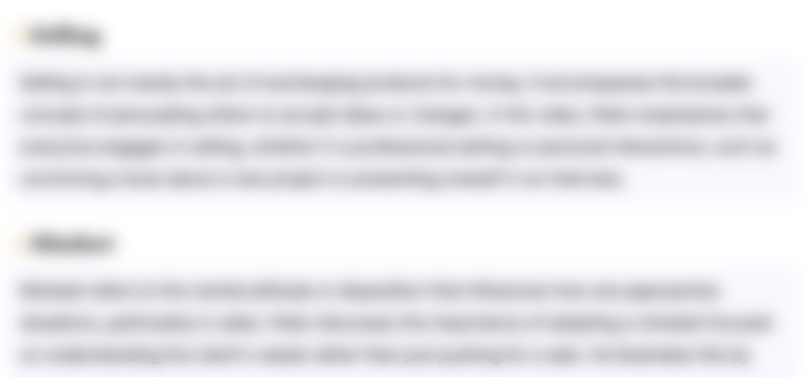
This section is available to paid users only. Please upgrade to access this part.
Upgrade NowHighlights
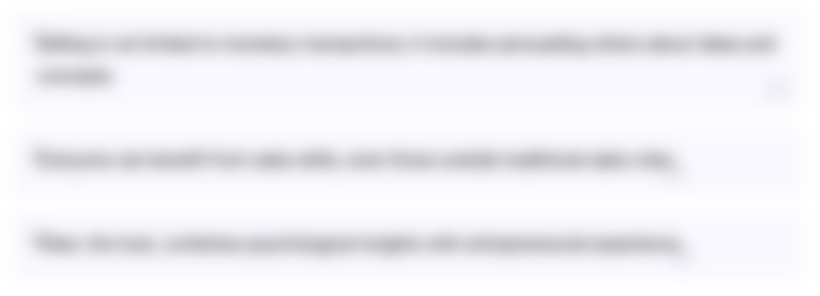
This section is available to paid users only. Please upgrade to access this part.
Upgrade NowTranscripts
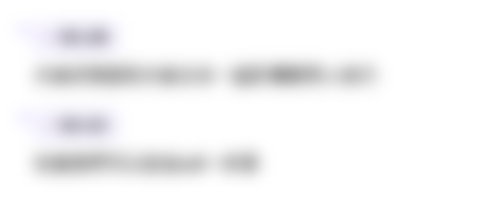
This section is available to paid users only. Please upgrade to access this part.
Upgrade NowBrowse More Related Video
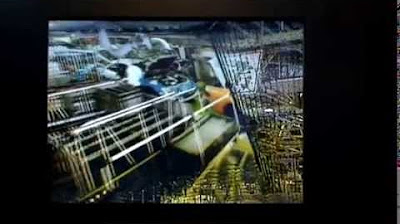
History of the Toyota Production System (TPS)

⚙ Lean Manufacturing | A pursuit of perfection
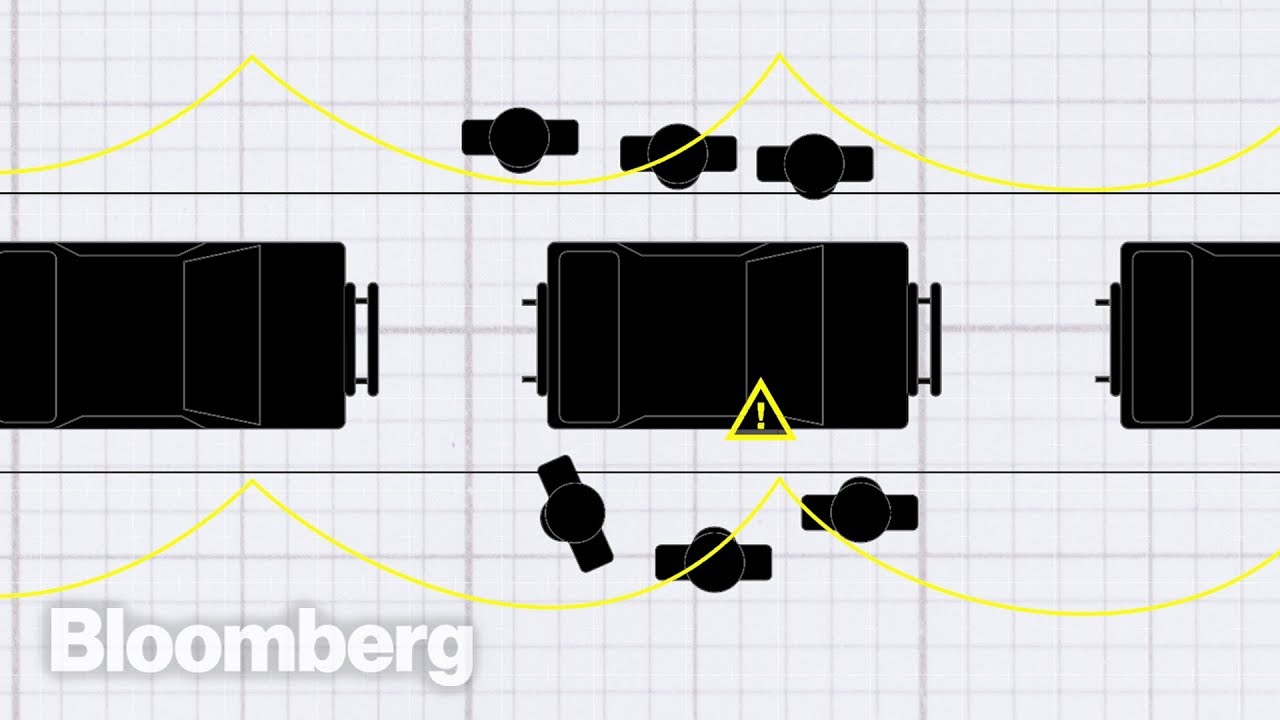
How Toyota Changed The Way We Make Things
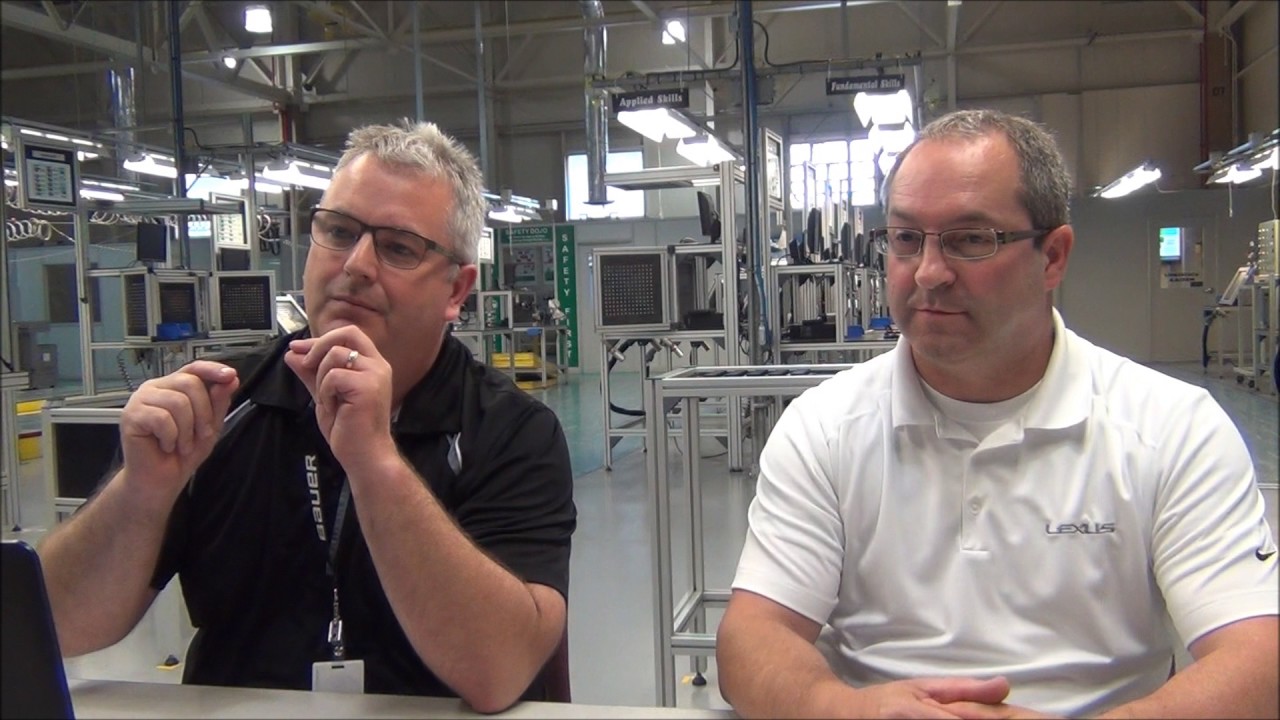
An Introduction To The Toyota Production System

Toyota’s Lean Supply Chain: The Secret Behind JIT Manufacturing Success | MBA Case study analysis
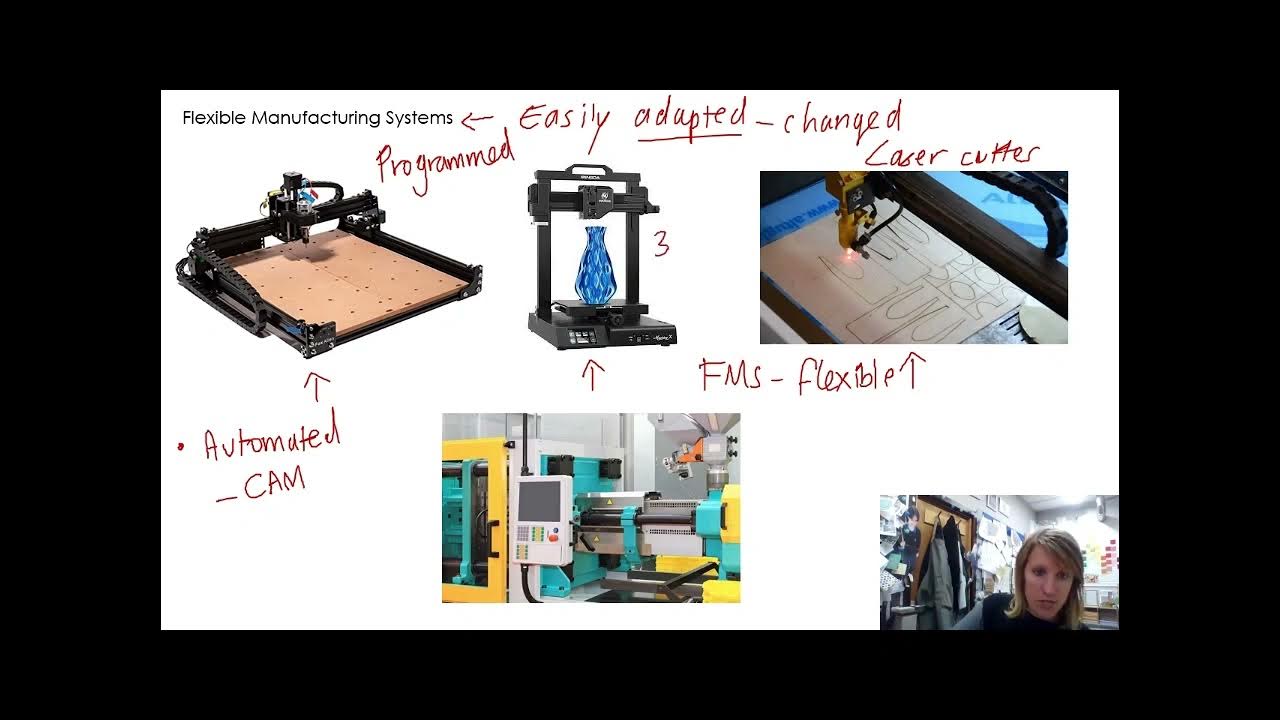
Video 2 - Flexible and Lean Manufacturing
5.0 / 5 (0 votes)