What Is Casting? 11 Types of Casting Processes Explanation
Summary
TLDRThis video explores 11 types of casting processes used in manufacturing, including sand casting, gravity die casting, pressure die casting, investment casting, and more. Each process is explained with its advantages and disadvantages, showcasing their versatility in industries like automotive, aerospace, and construction. From complex components to mass production, the video offers insights into how molten metal is poured into molds to create precise parts. It also touches on common questions about the duration of casting processes and the durability of cast metal products.
Takeaways
- 😀 Sand casting is ideal for large components like engine blocks, but may produce rough surface finishes.
- 😀 Gravity die casting uses reusable molds and is great for materials like aluminum, magnesium, and cast iron.
- 😀 Pressure die casting can be low or high pressure, with high pressure ideal for mass production of precise components.
- 😀 Investment casting, or lost wax casting, is a labor-intensive process used for producing complex metal parts.
- 😀 Plaster casting offers high accuracy for thin cross-section parts but is not suitable for high-temperature materials.
- 😀 Centrifugal casting uses centrifugal forces to produce cylindrical parts, reducing defects like air pockets and shrinkage.
- 😀 Lost foam casting involves a foam pattern and is suitable for materials like alloy steel and carbon steel.
- 😀 Vacuum casting eliminates bubbles and air pockets by using vacuum pressure, ideal for structural and automotive components.
- 😀 Squeezing casting combines permanent mold casting and die forging, ideal for safety-critical automotive parts.
- 😀 Continuous casting is used for mass production of metal profiles, especially for making steel bars.
- 😀 Shell molding is a finer sand-based expendable mold casting process, suitable for industrial products like gearbox housings.
Q & A
What is casting and why is it important in manufacturing?
-Casting is a manufacturing process where molten metal is poured into a mold to create a solid object with a specific shape and structure. It is important because it allows for the creation of complex components with high precision, making it indispensable in industries like automotive, aerospace, and construction.
What is sand casting and what are its main advantages?
-Sand casting uses molds made from silica-based materials like naturally bonded or synthetic sand. It is ideal for large components like engine blocks. The main advantage of sand casting is its versatility and cost-effectiveness, though it can result in a rough surface finish.
How does gravity die casting differ from other casting methods?
-Gravity die casting uses reusable molds made of materials like steel or graphite. The molten metal is poured into the mold cavity under the influence of gravity. It differs from other methods by using gravity to fill the mold instead of pressure or vacuum.
What are the key differences between high-pressure and low-pressure die casting?
-High-pressure die casting is used for producing intricate, precise components in mass production, while low-pressure die casting is better suited for larger, simpler parts. Both involve injecting molten metal into a metal mold, but the pressure applied differs significantly.
What is investment casting and when is it used?
-Investment casting, also known as lost wax casting, involves creating a disposable ceramic mold around a wax pattern, which is then melted away and replaced with molten metal. It is used for producing complex parts with high precision, such as gears and bike parts.
What are the limitations of plaster casting?
-Plaster casting is excellent for high-precision components, especially those with thin cross-sections. However, it is not suitable for high-temperature ferrous materials, limiting its applications.
How does centrifugal casting work and what are its benefits?
-Centrifugal casting uses centrifugal forces to distribute molten metal within a preheated, rotating mold. It is particularly effective for cylindrical parts like bearings and piston rings. This process reduces defects like shrinkage and gas pockets.
What is the difference between lost foam casting and investment casting?
-Lost foam casting uses foam as the pattern instead of wax, making it a more cost-effective method for creating metal castings. Like investment casting, it involves coating the pattern with a ceramic shell, but the pattern material differs.
What makes vacuum casting ideal for automotive applications?
-Vacuum casting is performed under vacuum pressure to eliminate bubbles and air pockets in the molten metal. This results in smoother, more durable components, making it ideal for precision automotive parts like structural chassis components.
How does continuous casting contribute to mass production?
-Continuous casting involves the production of metal profiles with a constant cross-section, making it ideal for manufacturing large quantities of products like steel bars. It allows for consistent and efficient production.
Outlines
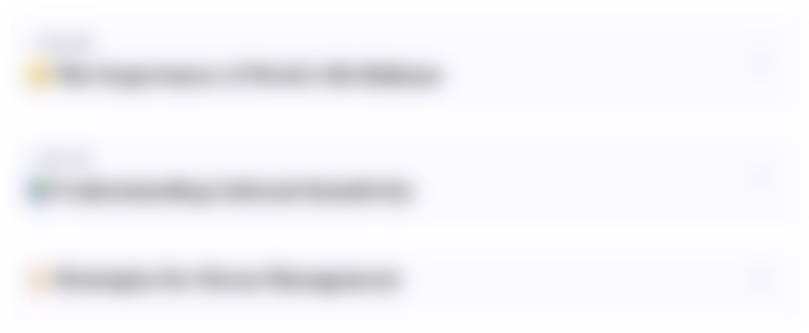
このセクションは有料ユーザー限定です。 アクセスするには、アップグレードをお願いします。
今すぐアップグレードMindmap
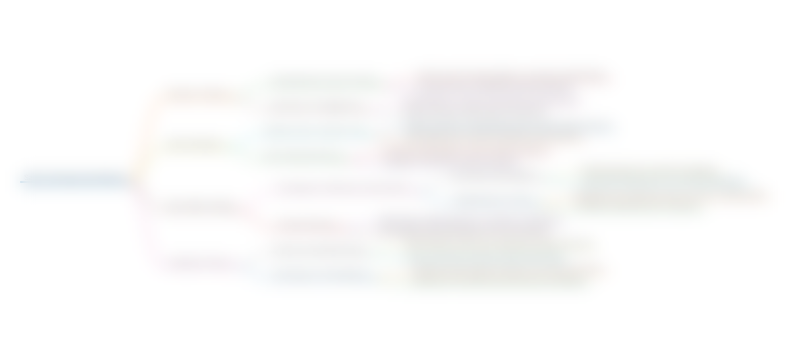
このセクションは有料ユーザー限定です。 アクセスするには、アップグレードをお願いします。
今すぐアップグレードKeywords
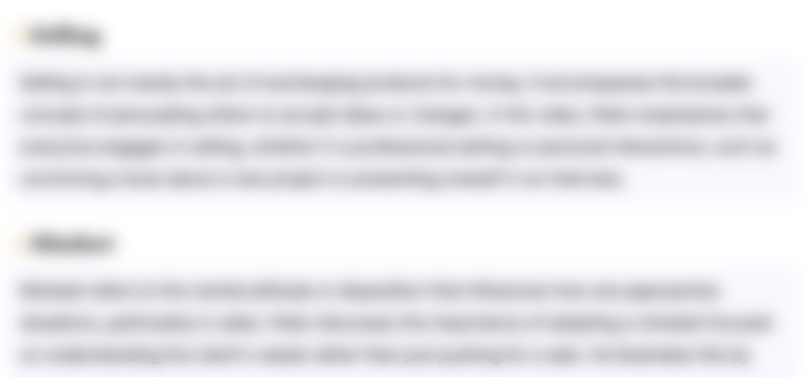
このセクションは有料ユーザー限定です。 アクセスするには、アップグレードをお願いします。
今すぐアップグレードHighlights
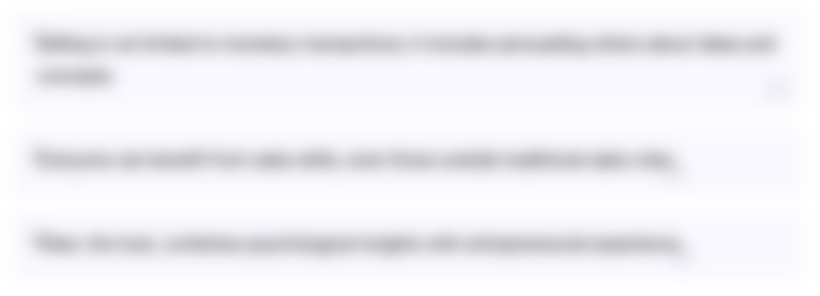
このセクションは有料ユーザー限定です。 アクセスするには、アップグレードをお願いします。
今すぐアップグレードTranscripts
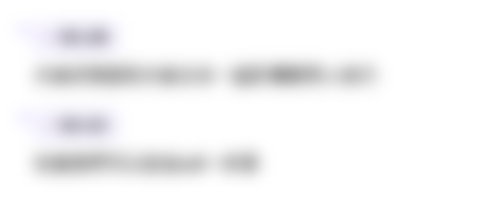
このセクションは有料ユーザー限定です。 アクセスするには、アップグレードをお願いします。
今すぐアップグレード関連動画をさらに表示

What Are The Common Types Of Metal Casting Process In Engineering and Industry?

PENGECORAN LOGAM | Praktikum MK Teknologi Manufaktur

How Die Casting Aluminum Works - How It's Made
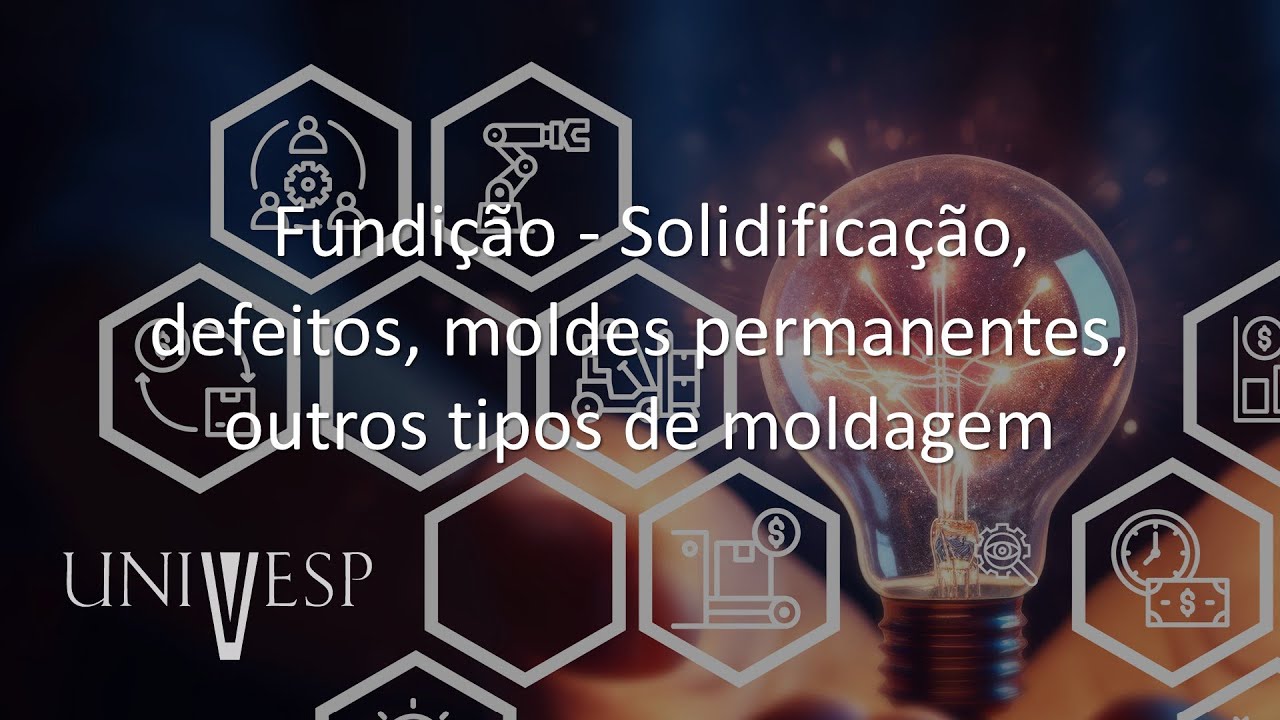
Materiais e Processos de Fabricação para Engenharia de Produção - Fundição - Solidificação, defeitos
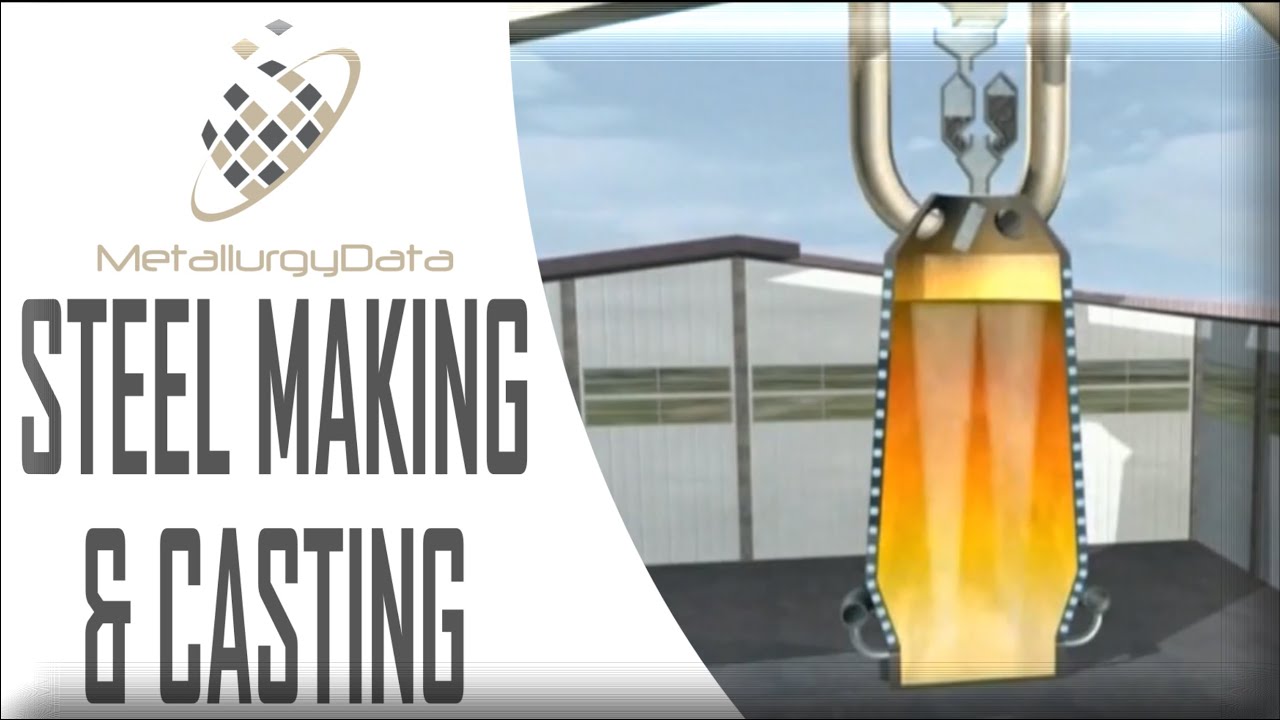
Steel Making and Casting (Principles of Metallurgy)
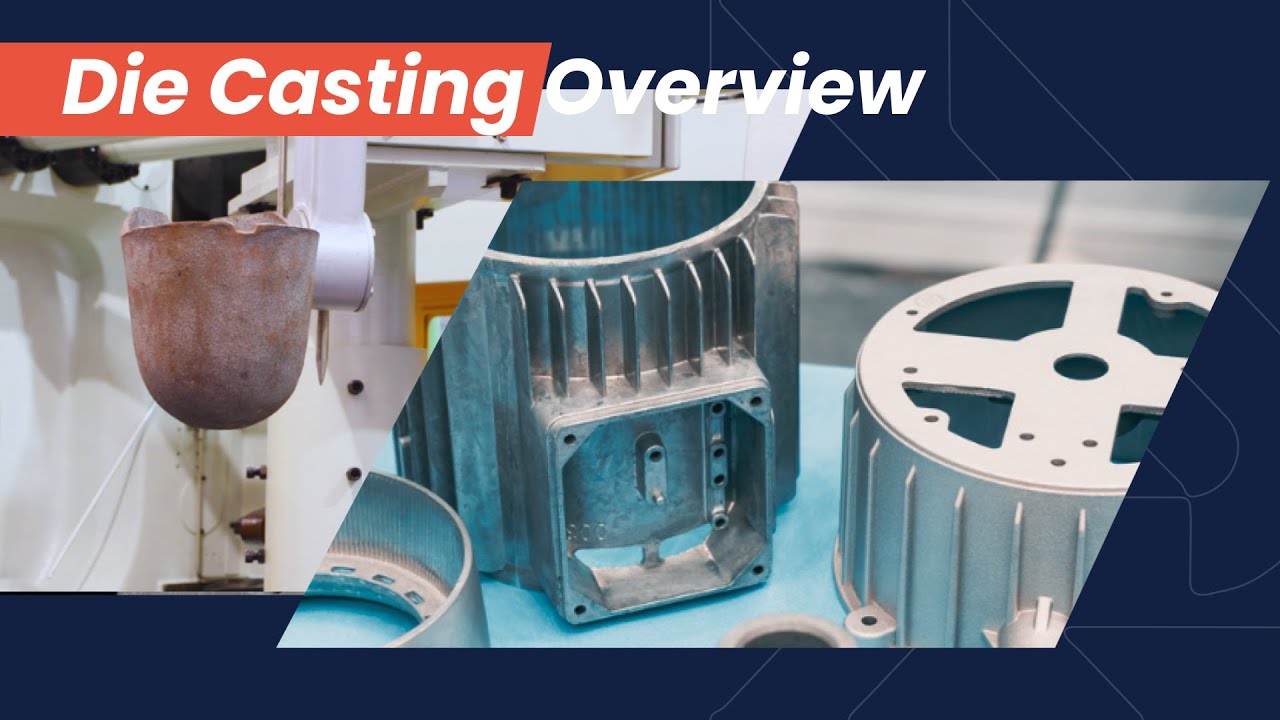
What Is Die Casting? Understand the Most Efficiency Metal Casting Process
5.0 / 5 (0 votes)