How Die Casting Aluminum Works - How It's Made
Summary
TLDRThe video provides an in-depth look at the die-casting process for aluminum at Metazel Manufacturing, one of Europe's largest pressure die-casting facilities. It highlights the advantages of aluminum, such as being lightweight and tough, and showcases the advanced technologies used in their casting process. From melting aluminum in induction furnaces to precise robot casting, and extensive quality checks, the video emphasizes how Metazel produces high-quality aluminum parts for industries like automotive, household appliances, and more. The company ensures every product meets rigorous standards before delivery to clients.
Takeaways
- 😀 Aluminium is widely used in industries such as automotive, power tools, and construction due to its lightweight, toughness, water resistance, and oxide-proof properties.
- 😀 The process of die casting aluminium starts with melting the raw material in induction furnaces, which can melt up to 1.5 tons of aluminium in just 45 minutes.
- 😀 Aluminium is purified in the melting process using argon gas, which removes gases and contaminants from the metal.
- 😀 The aluminium is then transferred to melting stations where it is kept in a liquid state for casting.
- 😀 Modern die casting technology is employed, such as robots with precise control over material handling to ensure contamination-free castings.
- 😀 The aluminium casting process involves using a pipette to collect material and ensuring the metal doesn't come in contact with air, preserving its purity.
- 😀 Another casting method involves pouring aluminium into a filling chamber with a ladle before forcing it into the mold.
- 😀 Once the aluminium solidifies inside the mold, it undergoes a geophysical examination to check for contaminants, air bubbles, or structural discontinuities that could affect endurance.
- 😀 The castings are then finished using tumble finishing or shot blasting, followed by machining processes using CNC-controlled machines.
- 😀 Precision quality control tests are performed on the final castings, including measurements with accuracy up to 3 microns and tests for endurance, strength, and chemical composition.
- 😀 After passing the stringent quality tests, the die castings are sent to customers for use in various industries.
Q & A
What industries benefit from die-casting aluminum products?
-Die-casting aluminum products are used in various industries, including automotive, household appliances, construction, electrical and power tools sectors, among others.
What are the main advantages of using aluminum for die-casting?
-Aluminum is lightweight, tough, water-resistant, and oxide-proof, making it an ideal material for die-casting.
How does the aluminum melting process work in the foundry?
-In the foundry, aluminum is melted in induction furnaces capable of melting 1.5 tons of material within 45 minutes. The melted aluminum is then purified using argon to remove gases and contaminants.
What role does the refiner play in the aluminum melting process?
-The refiner rotates above the furnace, administering argon through a metal treatment valve. This process helps remove gases and contaminants from the molten aluminum.
How is the molten aluminum transferred to the die-casting machines?
-The molten aluminum is transferred to the melting stations, where it is maintained in a liquid state before being inserted into the die-casting machines.
What are the two main methods of casting aluminum described in the script?
-The two main methods of casting aluminum are using a robot with a precise pipette to collect and inject the metal into molds, and pouring the molten aluminum into a filling chamber using a ladle before forcing it into the mold.
What is the significance of the genographic examination in the casting process?
-The genographic examination checks the metal structure for contamination, air bubbles, or discontinuities, as these factors can affect the durability and strength of the cast aluminum parts.
What post-casting processes are applied to the aluminum castings?
-After casting, the aluminum parts are purified, subjected to tumble finishing or shot blasting, and then moved to the machining department for processes like milling, turning, and threading.
What types of quality tests are performed on the final aluminum castings?
-Quality tests include precise measurements (up to 3 microns), endurance and strength tests, and analysis of the chemical composition of the aluminum to ensure it meets rigorous quality standards.
How does the foundry ensure that the final die-cast products meet customer requirements?
-The foundry ensures quality by performing thorough quality control tests on the aluminum parts, and once they meet the required standards, they are sent to customers.
Outlines
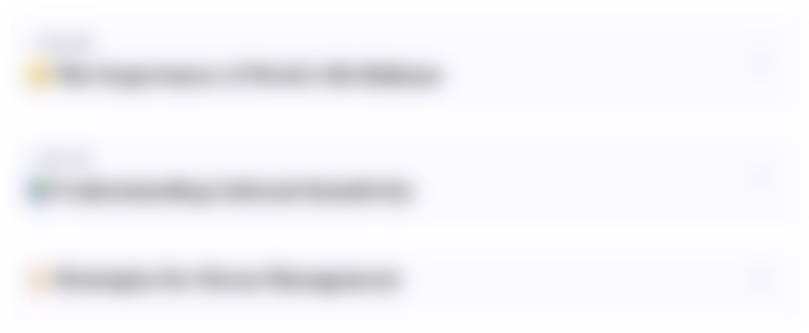
This section is available to paid users only. Please upgrade to access this part.
Upgrade NowMindmap
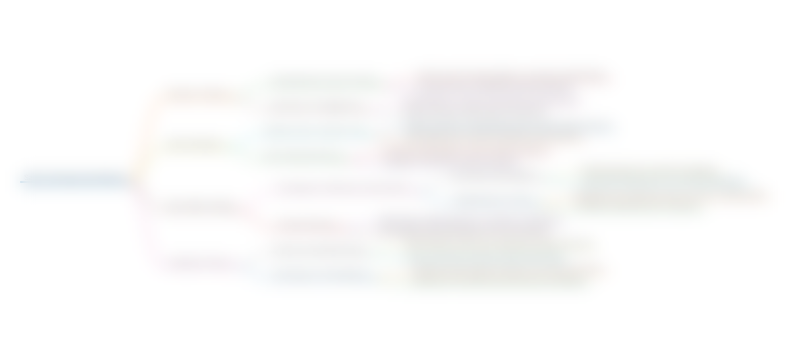
This section is available to paid users only. Please upgrade to access this part.
Upgrade NowKeywords
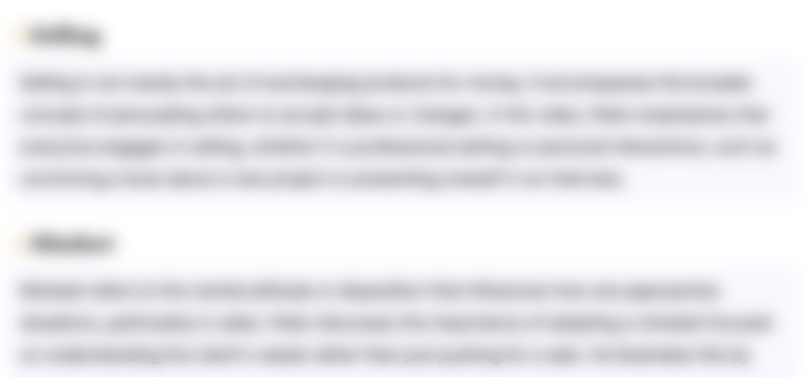
This section is available to paid users only. Please upgrade to access this part.
Upgrade NowHighlights
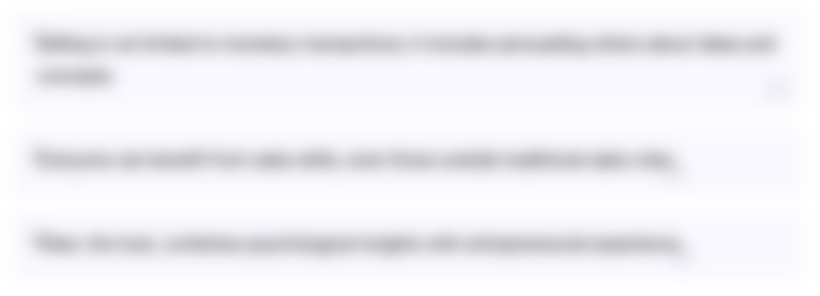
This section is available to paid users only. Please upgrade to access this part.
Upgrade NowTranscripts
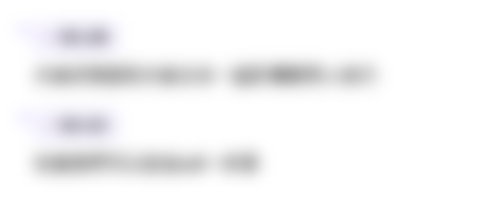
This section is available to paid users only. Please upgrade to access this part.
Upgrade NowBrowse More Related Video

5 Tips for Working With Aluminium HIGH PRESSURE DIE CASTING | Explained - Serious Engineering: Ep 28
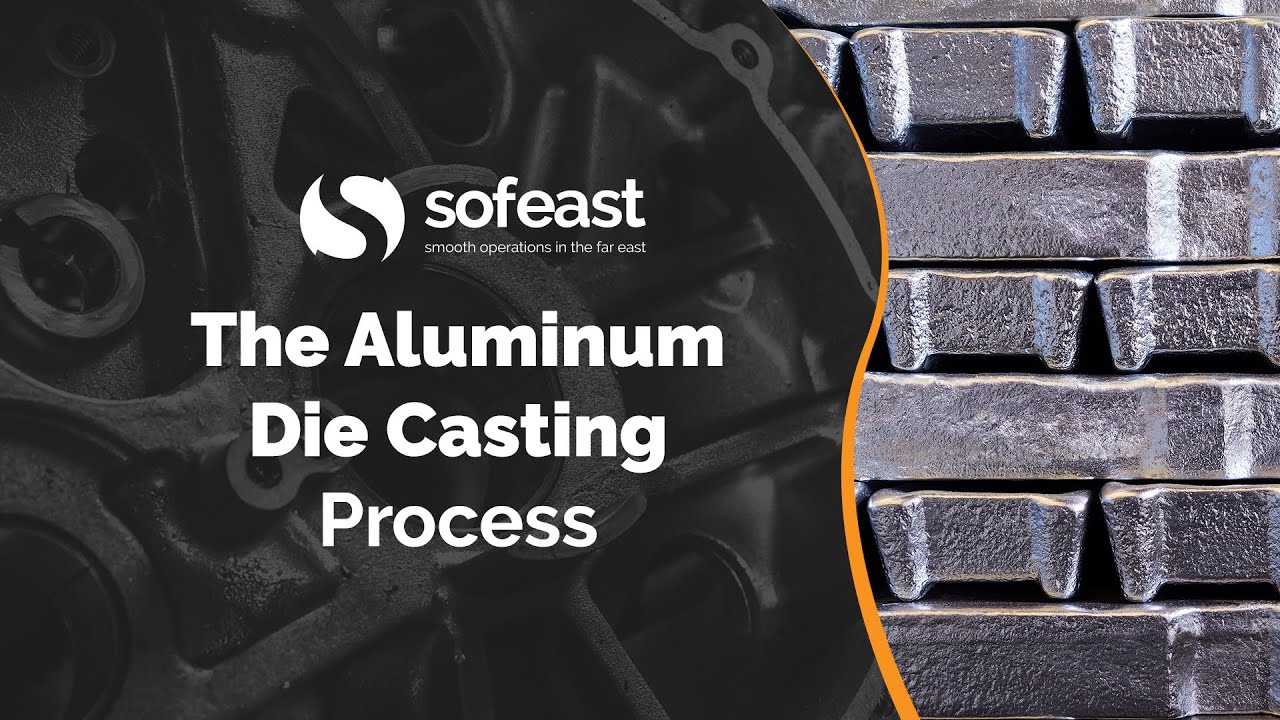
The Aluminum Die Casting Process

What Are The Common Types Of Metal Casting Process In Engineering and Industry?
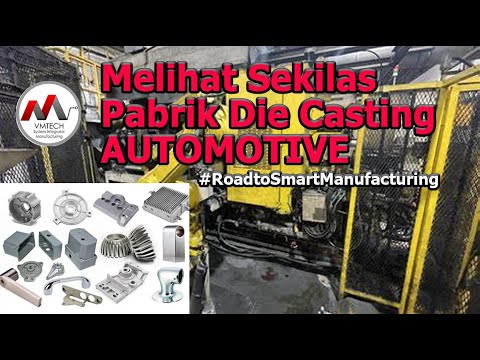
OEE Plus Die Casting Process Part #1 Pengantar HPDC

Proses Pengecoran

What Is Casting? 11 Types of Casting Processes Explanation
5.0 / 5 (0 votes)