Proactive Strategies for Resilient Supply Chains: Mitigating Hidden Risks
Summary
TLDR本视频脚本讨论了供应链的弹性问题,由麻省理工学院的David教授和Accenture的董事总经理pfk共同介绍。David教授领导MIT数据科学实验室,专注于数据科学,特别是供应链弹性。他们开发了一种新的供应链弹性评估方法,通过与福特汽车公司的合作,成功预测了2020年初新冠疫情对供应链的影响。pfk强调了供应链弹性管理的重要性,提出了五个最佳实践要素,并讨论了如何通过数字化孪生和压力测试来优化供应链弹性。他们还分享了如何利用这些工具来快速响应市场变化,提高企业竞争力。
Takeaways
- 🎓 **学术与实践结合**:Dr. Levy 与 Accenture 的合作展示了学术界与咨询公司之间的成功合作,共同开发了供应链韧性压力测试工具。
- 📈 **供应链韧性的重要性**:通过 COVID-19 大流行,供应链韧性从边缘话题变成了核心议题,企业开始重视并投资于韧性建设。
- 🔍 **数据科学的应用**:MIT 数据科学实验室与福特汽车公司合作,开发了新的方法来衡量供应链的韧性并识别潜在风险。
- 📊 **数字孪生技术**:构建供应链的数字孪生是实现供应链可视化和韧性管理的关键步骤。
- ⏱️ **时间关键指标**:引入了时间恢复(Time to Recover)、生存时间(Time to Survive)和性能影响(Performance Impact)等关键性能指标来评估供应链的韧性。
- 💡 **前瞻性管理**:通过预测性分析,企业可以提前识别潜在的供应链问题,并采取预防措施,从而避免未来的业务中断。
- 🌐 **全球化风险**:供应链的全球性质意味着一个地区的中断可能对全球产生连锁反应,因此需要全球视角来管理风险。
- 📉 **财务影响的量化**:通过建立数字孪生模型,企业可以量化供应链中断对财务的具体影响,从而更准确地评估风险和投资。
- 🛠️ **风险缓解策略**:通过压力测试和场景分析,企业可以确定和优先处理风险缓解活动,以提高供应链的韧性。
- 🚀 **竞争优势**:在面对全球性的中断时,能够快速反应并有效管理供应链的企业可以将其转化为竞争优势。
- 📚 **持续学习与改进**:企业需要持续地从每次供应链中断中学习,不断改进其韧性管理策略,以适应不断变化的全球环境。
Q & A
什么是供应链弹性(resiliency),它为什么重要?
-供应链弹性是指供应链在面对各种干扰时,能够快速响应并恢复正常运营的能力。它重要是因为在当前的商业环境中,如自然灾害、政治冲突、疫情等不可预测的事件频发,拥有弹性的供应链能够帮助企业减少中断带来的影响,保持业务连续性,甚至在某些情况下,通过快速反应获得竞争优势。
Dr. Levy 在供应链弹性方面有哪些贡献?
-Dr. Levy 是麻省理工学院(MIT)的教授,他在供应链弹性方面做出了显著贡献。他与福特汽车公司合作,开发了一种新的方法来衡量供应链的弹性水平,并识别潜在风险。他的研究成果发表在《哈佛商业评论》上,并且他在2020年初准确预测了新冠疫情对北美和欧洲供应链的影响。
Accenture 和 MIT 是如何合作来提升供应链弹性的?
-Accenture 与 MIT 合作,将 MIT 开发的技术规模化,应用到多个行业中。他们共同开发了所谓的“供应链压力测试(residency stress test)”,帮助企业通过模拟不同的干扰情景来测试和提高其供应链的弹性。
什么是供应链压力测试,它如何帮助企业?
-供应链压力测试是一种评估工具,它借鉴了金融行业在2008年金融危机后的做法,要求企业模拟各种潜在的干扰情景,以测试其供应链的抗压能力。通过压力测试,企业能够识别潜在的风险点,制定应对策略,从而在真正的危机发生时能够更加迅速和有效地响应。
在供应链管理中,为什么需要高层领导的支持?
-在供应链管理中,需要高层领导的支持来打破内部隔阂,实现端到端的可视化管理。没有高层的支持,采购、生产、研发等部门可能无法协同工作,形成统一的供应链弹性策略。
如何衡量供应链的弹性?
-衡量供应链弹性可以通过几个关键的指标,如恢复时间(time to recover)、生存时间(time to survive)和性能影响(performance impact)。这些指标帮助企业量化在特定干扰下,供应链恢复正常运营所需的时间和对企业财务的影响。
什么是数字孪生(digital twin),在供应链管理中它扮演什么角色?
-数字孪生是一种虚拟模型,它能够代表物理世界中的实体或系统。在供应链管理中,数字孪生可以用来模拟整个供应链的运作,帮助企业进行风险评估、决策制定和性能优化。
为什么说供应链风险常常隐藏在意想不到的地方?
-供应链风险常常隐藏在意想不到的地方,因为传统的风险管理往往关注于那些显而易见的、成本较高的供应商。然而,一些小型供应商或者那些看似不重要的环节,一旦发生问题,也可能对整个供应链造成巨大的影响。
企业如何利用数字孪生来提高供应链的弹性?
-企业可以通过建立供应链的数字孪生来模拟不同的运营场景和潜在的干扰情景。通过这种方式,企业能够识别风险,优化库存管理,制定灵活的采购策略,并在危机发生前制定应对措施。
在当前的全球形势下,企业应如何考虑其供应链的地理分布?
-企业在考虑供应链的地理分布时,不能仅仅关注于将供应商和生产设施靠近市场需求,以期望提高弹性。实际上,根据数据,仅仅改变供应商的地理位置并不能保证供应链的弹性。企业需要综合考虑多种因素,包括政治稳定性、基础设施、供应商的可靠性等。
半导体行业的供应链问题对多个行业产生了哪些影响?
-半导体行业的供应链问题对汽车、消费电子、医疗设备等多个行业产生了影响。由于半导体短缺,许多行业面临生产延迟和成本上升的问题。此外,半导体供应链的复杂性和全球性意味着一个地区的干扰可能会对全球市场产生连锁反应。
企业如何平衡供应链的效率和弹性?
-企业需要在供应链的效率和弹性之间找到合适的平衡点。这意味着在优化成本和提高服务水平的同时,也要考虑到潜在的风险和干扰。企业可以通过建立数字孪生、进行压力测试、制定灵活的策略来提高供应链的弹性,同时保持效率。
在当前的能源危机中,企业应如何提高供应链的弹性?
-面对能源危机,企业需要采取多种措施来提高供应链的弹性。这可能包括寻找替代能源、优化能源使用、建立多元化的供应商网络、提高能源效率等。此外,企业还需要密切关注市场动态,快速响应能源价格的变化和政策调整。
Outlines
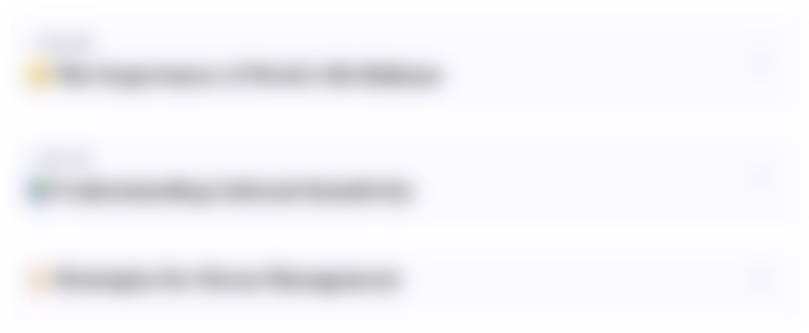
Cette section est réservée aux utilisateurs payants. Améliorez votre compte pour accéder à cette section.
Améliorer maintenantMindmap
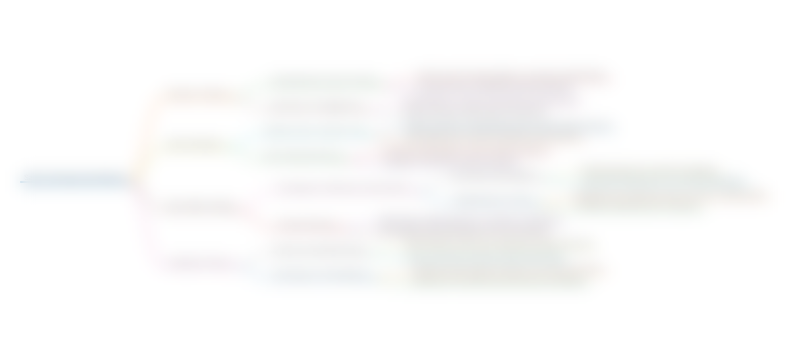
Cette section est réservée aux utilisateurs payants. Améliorez votre compte pour accéder à cette section.
Améliorer maintenantKeywords
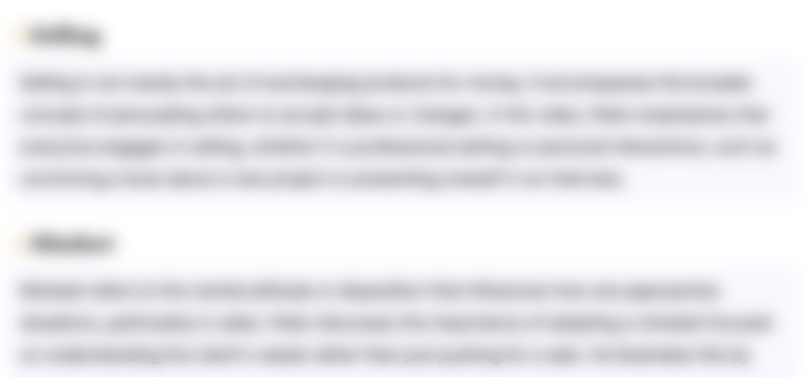
Cette section est réservée aux utilisateurs payants. Améliorez votre compte pour accéder à cette section.
Améliorer maintenantHighlights
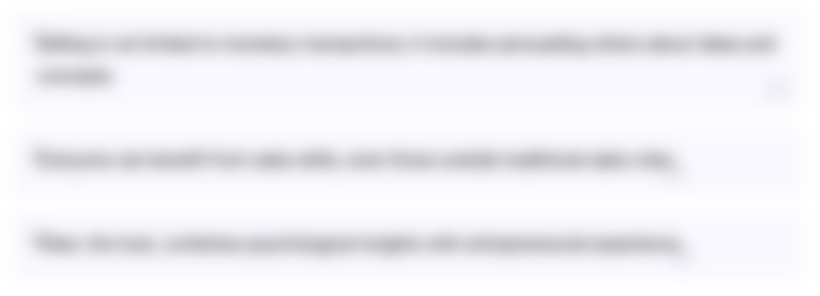
Cette section est réservée aux utilisateurs payants. Améliorez votre compte pour accéder à cette section.
Améliorer maintenantTranscripts
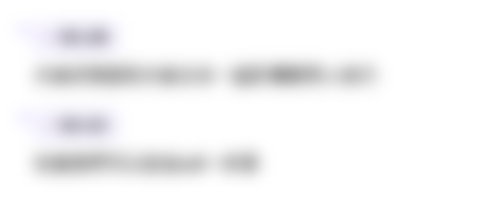
Cette section est réservée aux utilisateurs payants. Améliorez votre compte pour accéder à cette section.
Améliorer maintenantVoir Plus de Vidéos Connexes
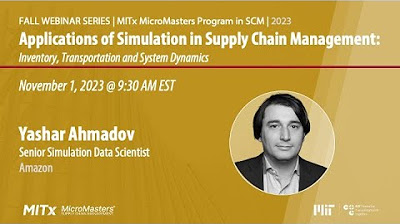
Applications of Simulation in Supply Chain Management
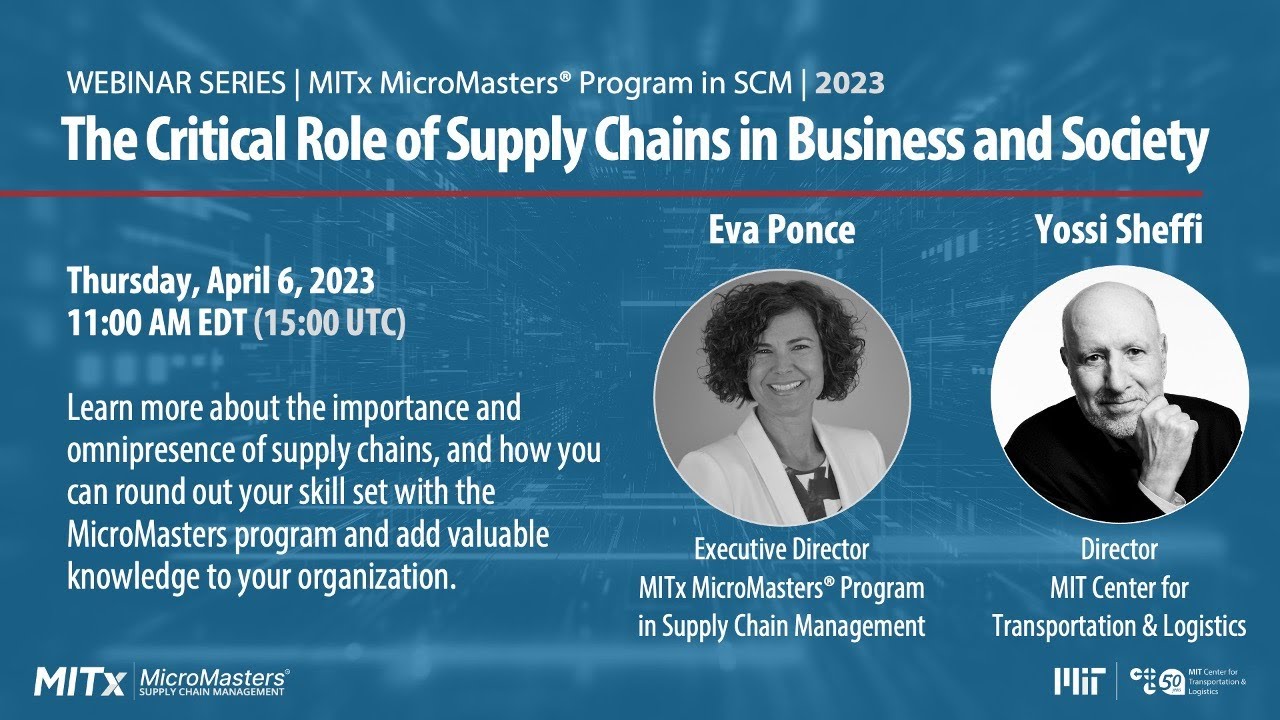
The Critical Role of Supply Chains in Business and Society

Reshaping Business and Supply Chain Strategy Beyond Covid-19 with Professor Yossi Sheffi
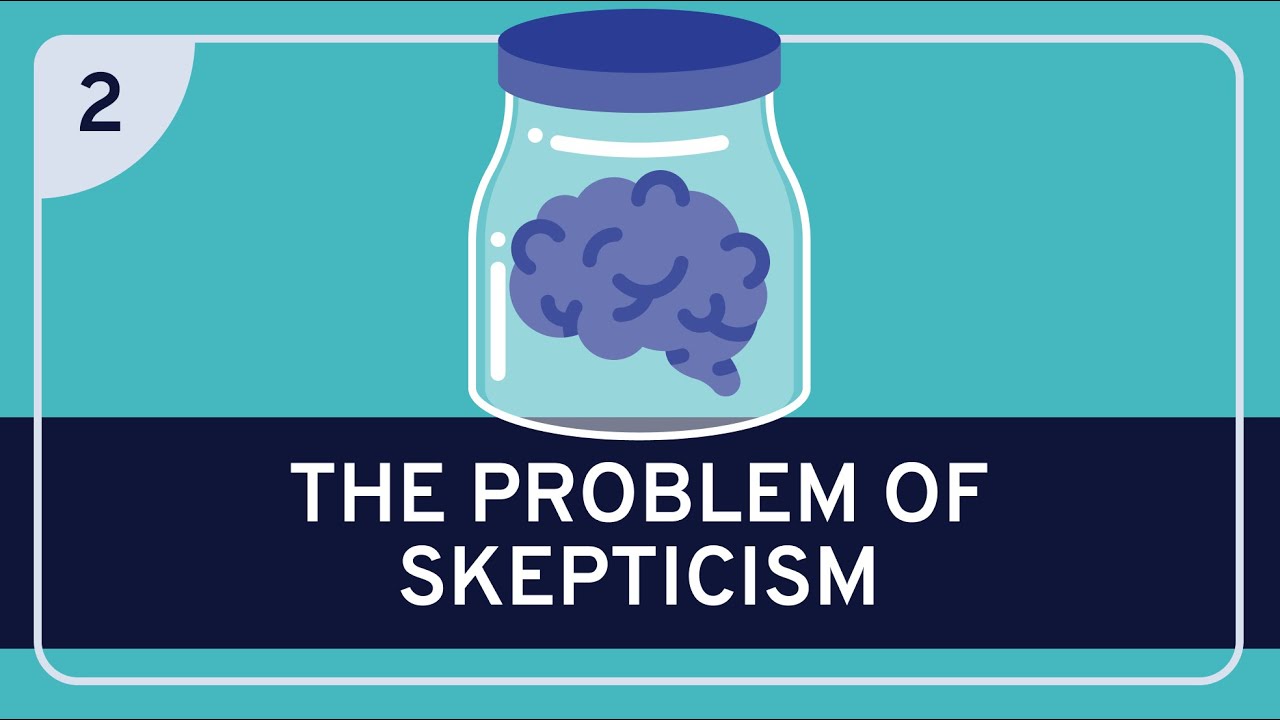
PHILOSOPHY - Epistemology: The Problem of Skepticism [HD]

Global Supply Chains: How Did All This Stuff Get Here?
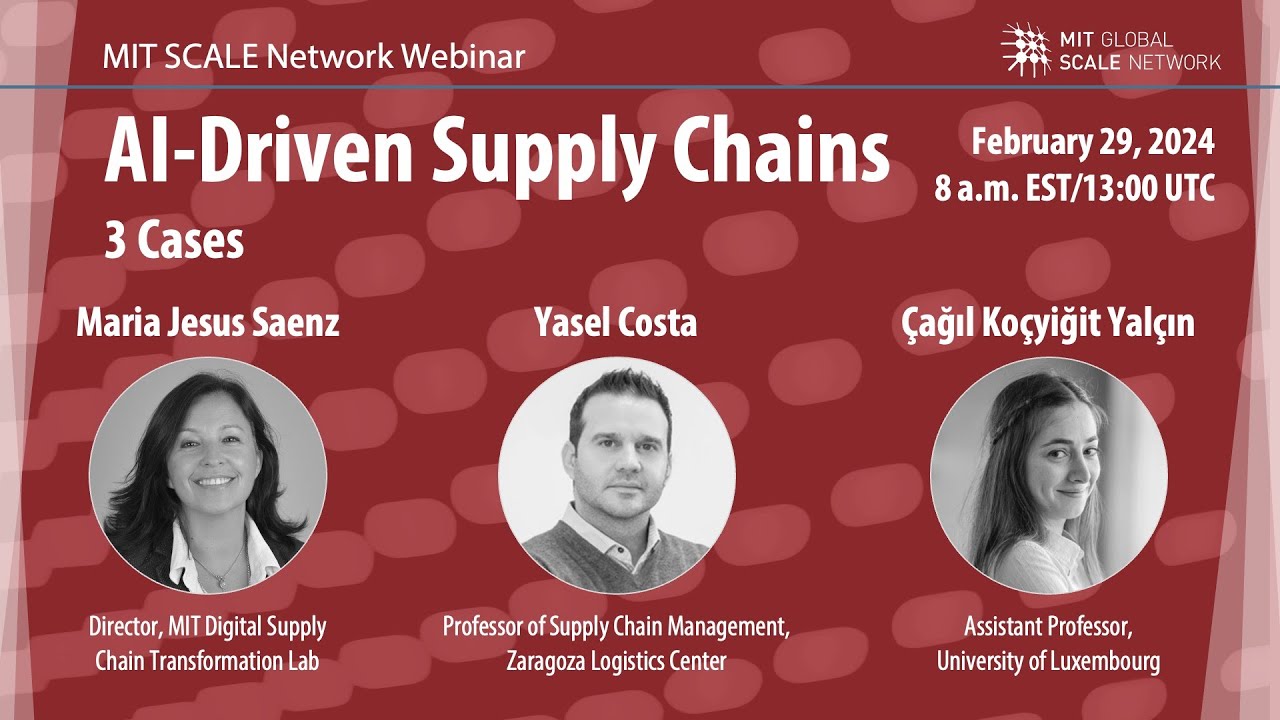
AI-Driven Supply Chains: 3 Cases | MIT SCALE Webinar | Spanish
5.0 / 5 (0 votes)