Turbine Assembly - Aircraft Gas Turbine Engines #10
Summary
TLDRThe video script delves into the intricacies of gas turbine engines, highlighting the turbine's role akin to an axial flow compressor in reverse. It discusses the conversion of thermal and kinetic energy from hot gases into mechanical energy, which powers the compressor and gearbox. The script explores materials like high-temperature steel, nickel-based alloys, and superalloys used in turbine blades, addressing challenges like creep and high-temperature operations. It also covers advanced manufacturing processes like single-crystal casting and the use of ceramics. The discussion extends to turbine stages, spool configurations, and the impact of rotational speed on efficiency and stress. The script concludes with insights on temperature monitoring and the losses incurred during turbine operation.
Takeaways
- 🔧 The turbine in a gas turbine engine functions similarly to an axial flow compressor in reverse, extracting energy from hot gases and converting it into mechanical energy to drive the compressor and other accessories.
- 💧 The turbine's first section, the nozzle guide vane, directs air onto the rotor blades, playing a crucial role in the energy conversion process.
- 🌡️ Modern engines can reach temperatures as high as 1700 degrees Celsius in the turbine, which is a significant factor in material selection and design.
- ⚙️ Gearboxes in gas turbine engines can be used to operate accessories or power propellers and rotors in engines not predominantly using jet propulsion for thrust.
- 🏋️♂️ The high rotational speeds of turbine blades can subject them to tensile loads exceeding two tonnes, leading to a phenomenon known as creep, where the metal stretches beyond its ability to return to its original shape.
- 🛠️ Early turbine blades were made from high-temperature steel, but advancements led to the use of nickel-based alloys, superalloys, and now single-crystal casting for improved heat and creep resistance.
- 🔬 Superalloys are complex mixtures of metals like chromium, cobalt, nickel, titanium, and tungsten, offering higher temperature limits and better performance than traditional steel.
- 🌀 The turbine assembly consists of one or more stages on a single shaft, which can be part of a spool when coupled with a compressor, affecting the engine's efficiency and operation.
- 🛑 Active clearance control and blade shrouding are used to minimize losses due to gas leakage and reduce blade vibration, enhancing the turbine's performance.
- ✈️ Free turbines, which are not connected to a compressor, can operate at their own optimum speed, offering benefits such as reduced noise pollution during taxiing and the ability to fit a parking brake.
Q & A
What is the function of the nozzle guide vane in a gas turbine engine?
-The nozzle guide vane in a gas turbine engine directs the air axially onto the blades of the rotor section, helping to convert the energy from the hot gases into mechanical energy.
How does a gas turbine engine utilize the energy available in the gas stream?
-A gas turbine engine utilizes the heat energy, potential pressure energy, and kinetic energy from the gas stream, converting these into mechanical energy to drive the compressor and other accessories.
What is the significance of the rotational speed of the turbine in a gas turbine engine?
-The rotational speed of the turbine is critical as it determines the blade tip velocity and the efficiency of energy conversion. High speeds can lead to blade tip velocities exceeding 1500 feet per second.
Why is the material of turbine blades important in gas turbine engines?
-The material of turbine blades is crucial because it must withstand high temperatures and tensile loading. Early blades were made of high-temperature steel, but advancements led to the use of nickel-based alloys, superalloys, and even single crystal casting for improved creep resistance.
What is creep, and how does it affect turbine blades?
-Creep is a phenomenon where the metal of the blade stretches beyond its ability to return to its original length due to the combined effects of high temperature and tensile loading. Over time, this can lead to blade failure.
How do turbine blades convert the energy from the gas stream into mechanical energy?
-Turbine blades convert the energy by extracting heat, pressure, and kinetic energy from the gas stream, which is then transformed into mechanical energy to drive the engine's compressor and other components.
What is the purpose of the divergent gas flow annulus in a turbine stage?
-The divergent gas flow annulus allows for longer blades to be fitted to each turbine stage, which helps control the gas stream velocity as it expands into the larger volume available at the rear of the engine.
Why are free turbines advantageous in certain gas turbine engine designs?
-Free turbines, which are not connected to a compressor, can operate at their own optimum design speed, leading to benefits such as reduced noise pollution during taxiing, less starting torque requirement, and the possibility of fitting a parking brake.
How does increasing the number of turbine stages affect the power output and turbine diameter?
-Increasing the number of stages in a turbine allows for an increase in power output without the need to increase the turbine diameter, which can help reduce drag and stress on the engine.
What are the different types of turbine blades used in gas turbine engines, and what determines their selection?
-Turbine blades can be impulse, reaction, or a combination of both, known as impulse-reaction. The selection of blade type depends on the specific design requirements of the engine, with the combination impulse-reaction type being more commonly used.
How is the turbine temperature monitored in a gas turbine engine, and why is this important?
-Turbine temperature is monitored using thermocouples placed in the gas flow within the turbine assembly. This monitoring is crucial to prevent exceeding the maximum turbine temperature, which could cause irreparable damage to the engine.
Outlines
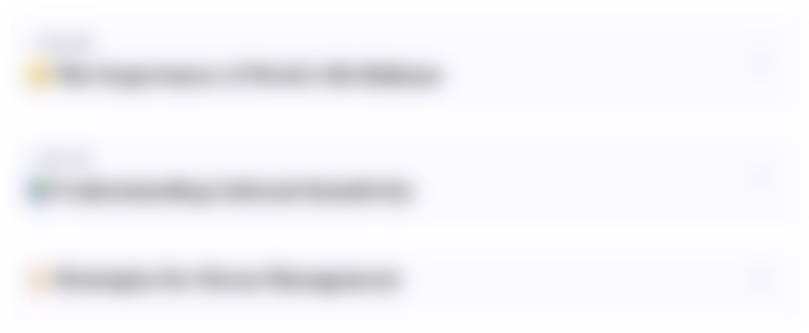
Cette section est réservée aux utilisateurs payants. Améliorez votre compte pour accéder à cette section.
Améliorer maintenantMindmap
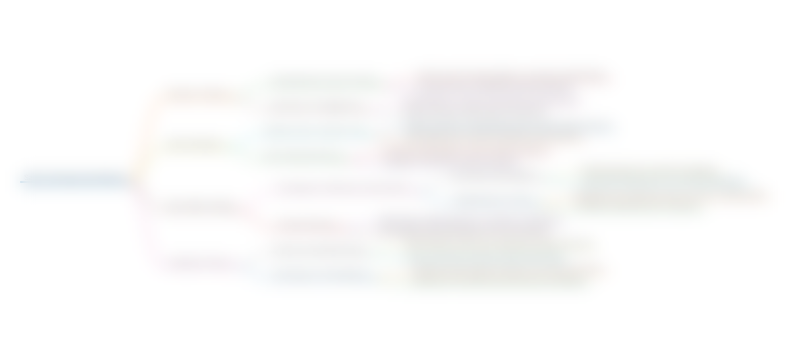
Cette section est réservée aux utilisateurs payants. Améliorez votre compte pour accéder à cette section.
Améliorer maintenantKeywords
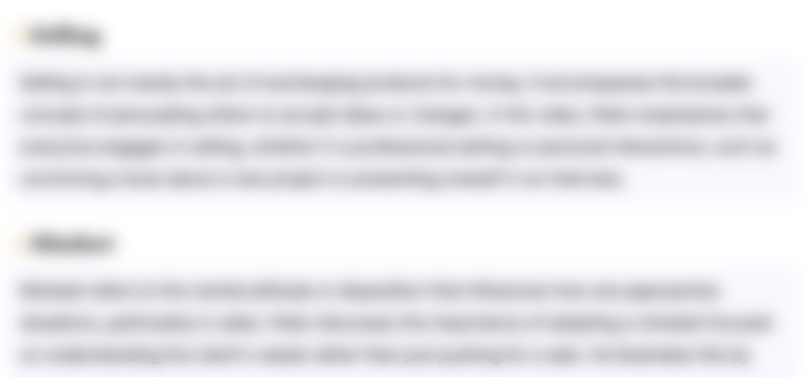
Cette section est réservée aux utilisateurs payants. Améliorez votre compte pour accéder à cette section.
Améliorer maintenantHighlights
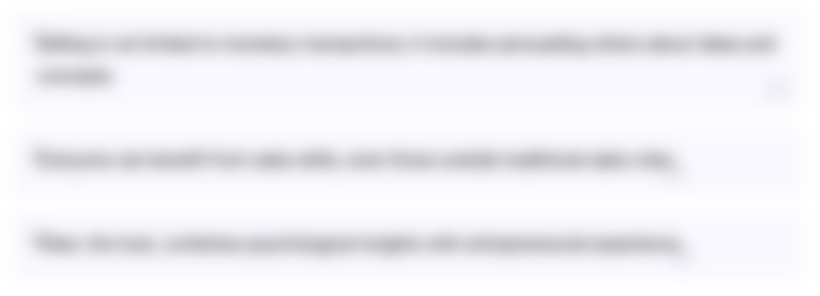
Cette section est réservée aux utilisateurs payants. Améliorez votre compte pour accéder à cette section.
Améliorer maintenantTranscripts
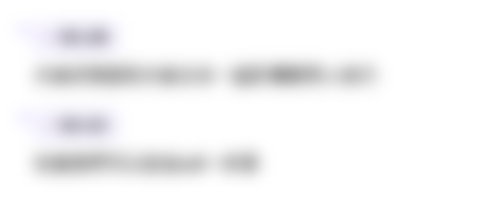
Cette section est réservée aux utilisateurs payants. Améliorez votre compte pour accéder à cette section.
Améliorer maintenantVoir Plus de Vidéos Connexes
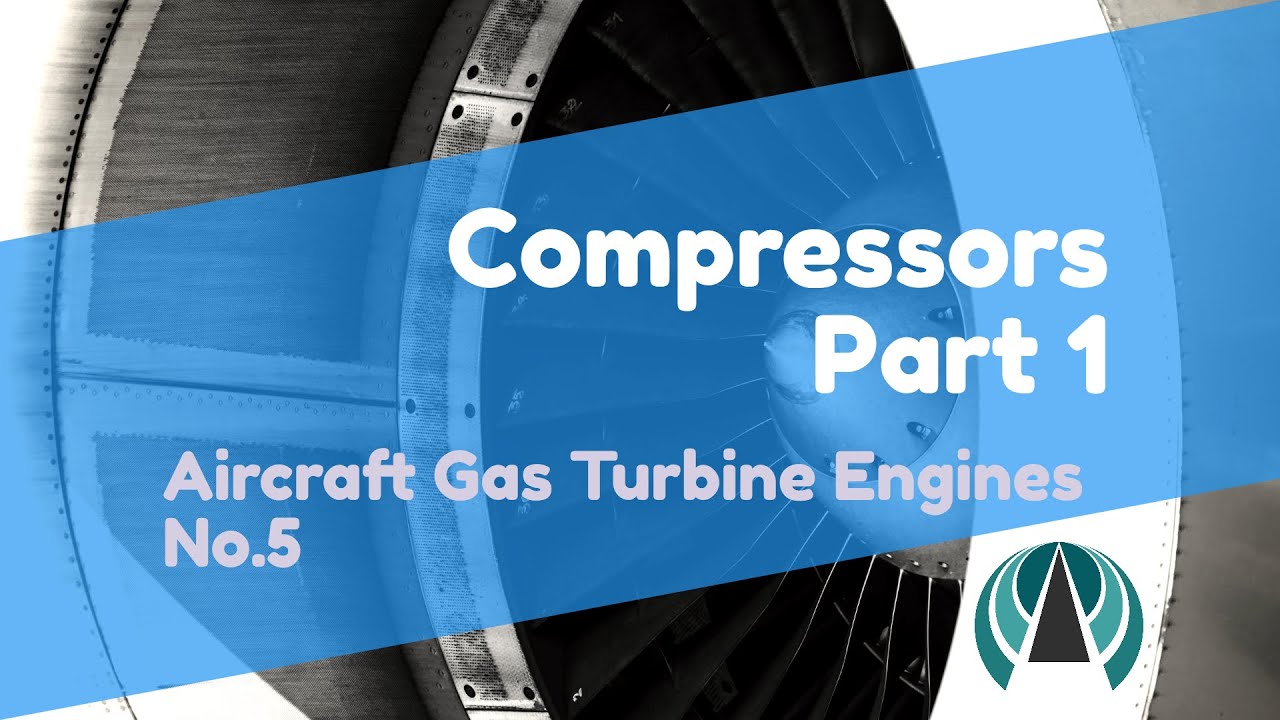
Compressors Part 1 - Aircraft Gas Turbine Engines #05
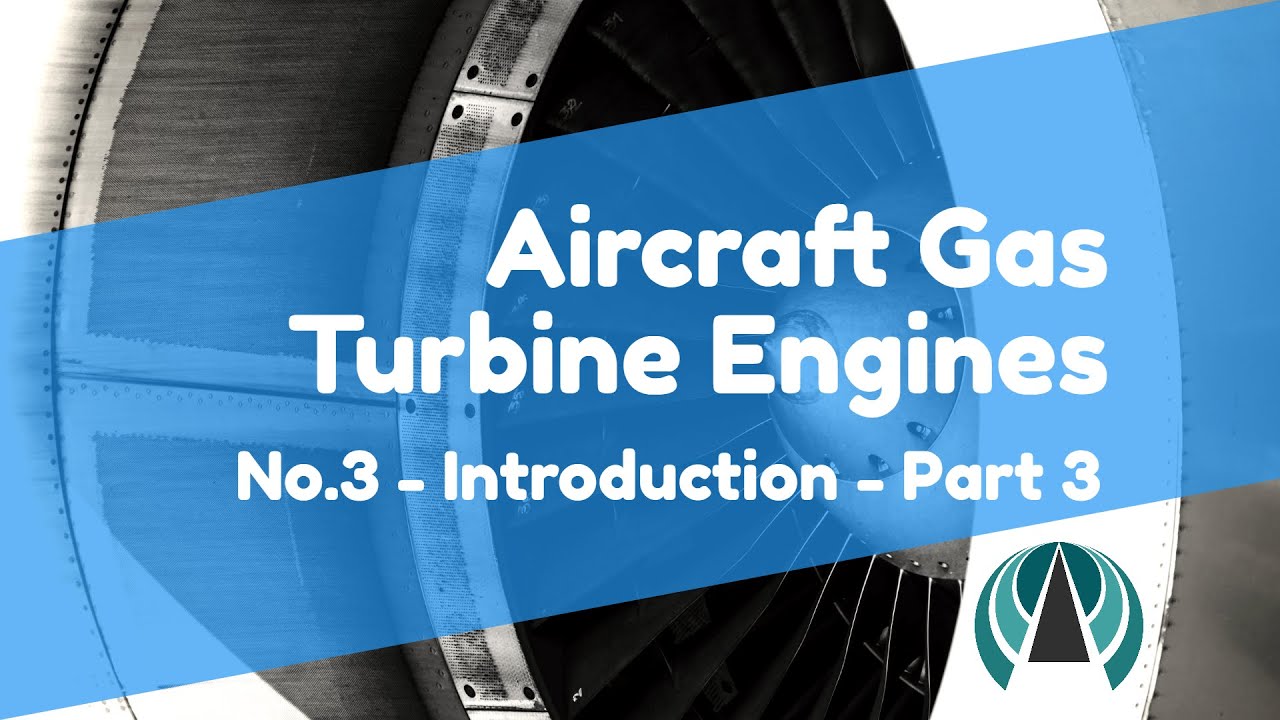
Aircraft Gas Turbine Engines #03 - Introduction Part 3
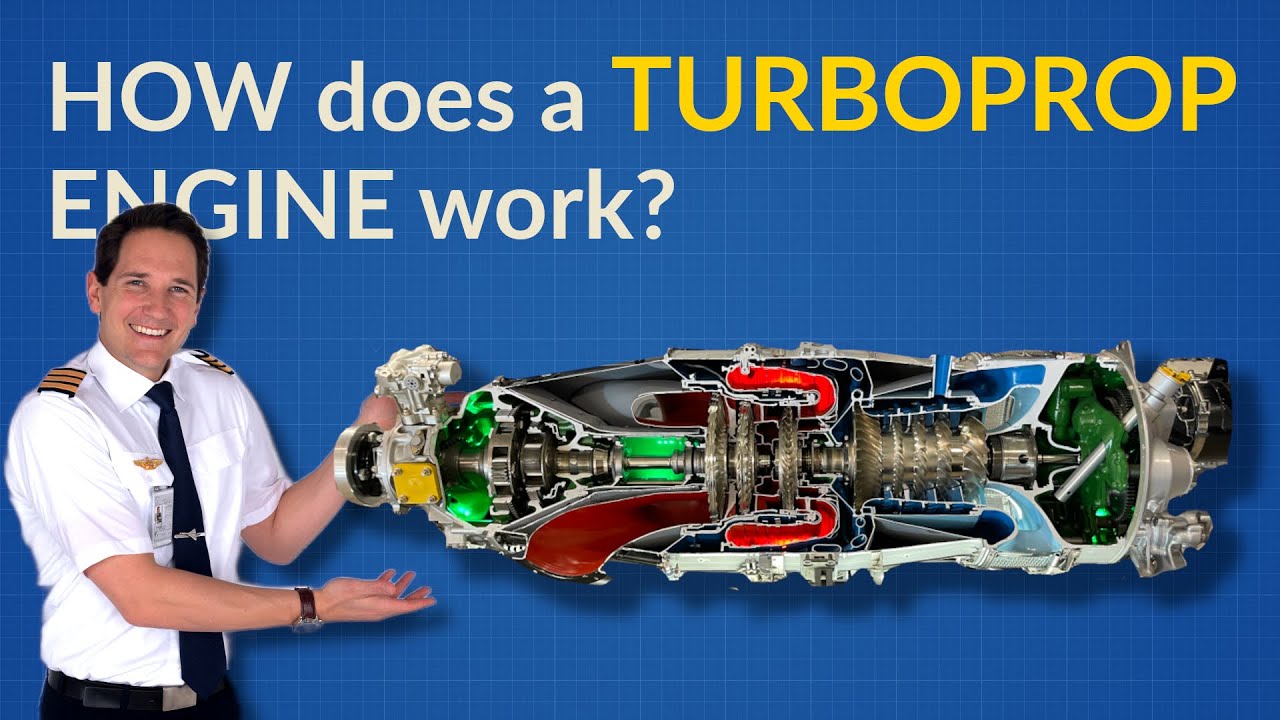
The BEST TURBOPROP explanation video! By Captain Joe and PRATT & WHITNEY

01 ATPL Training Gas Turbine Engines #01 Introduction Part 1
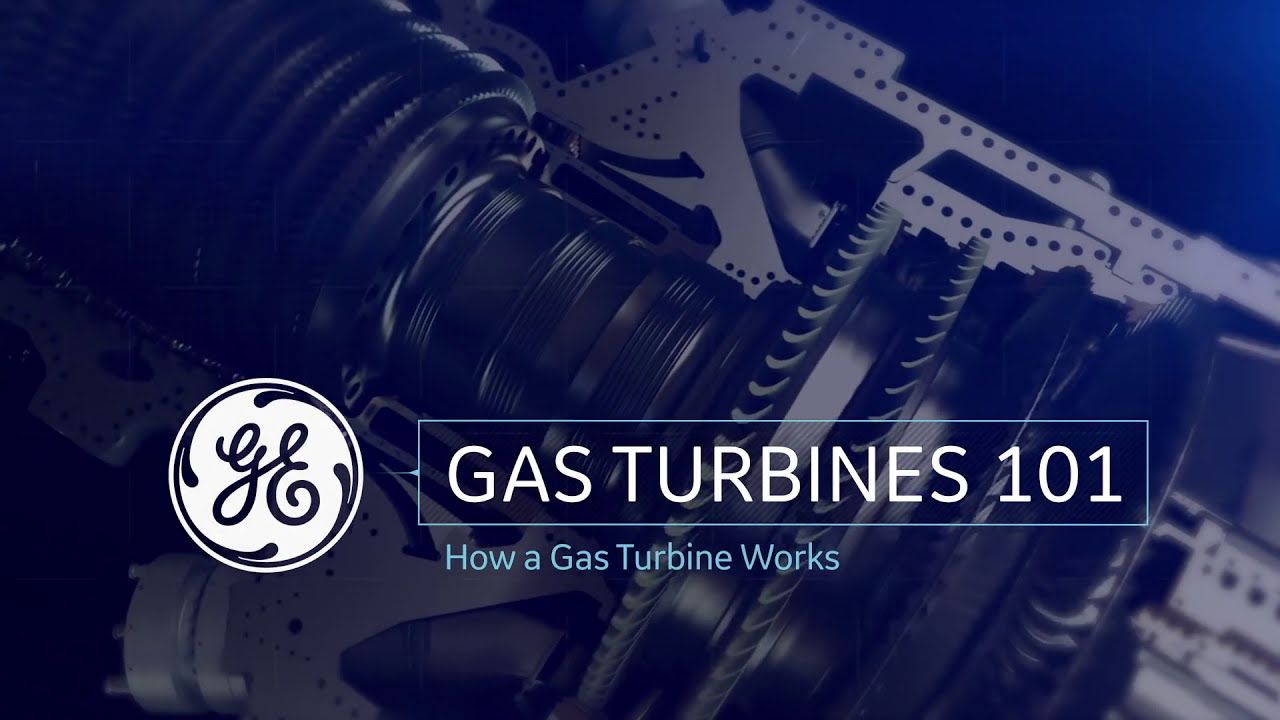
How a Gas Turbine Works | Gas Power Generation | GE Power
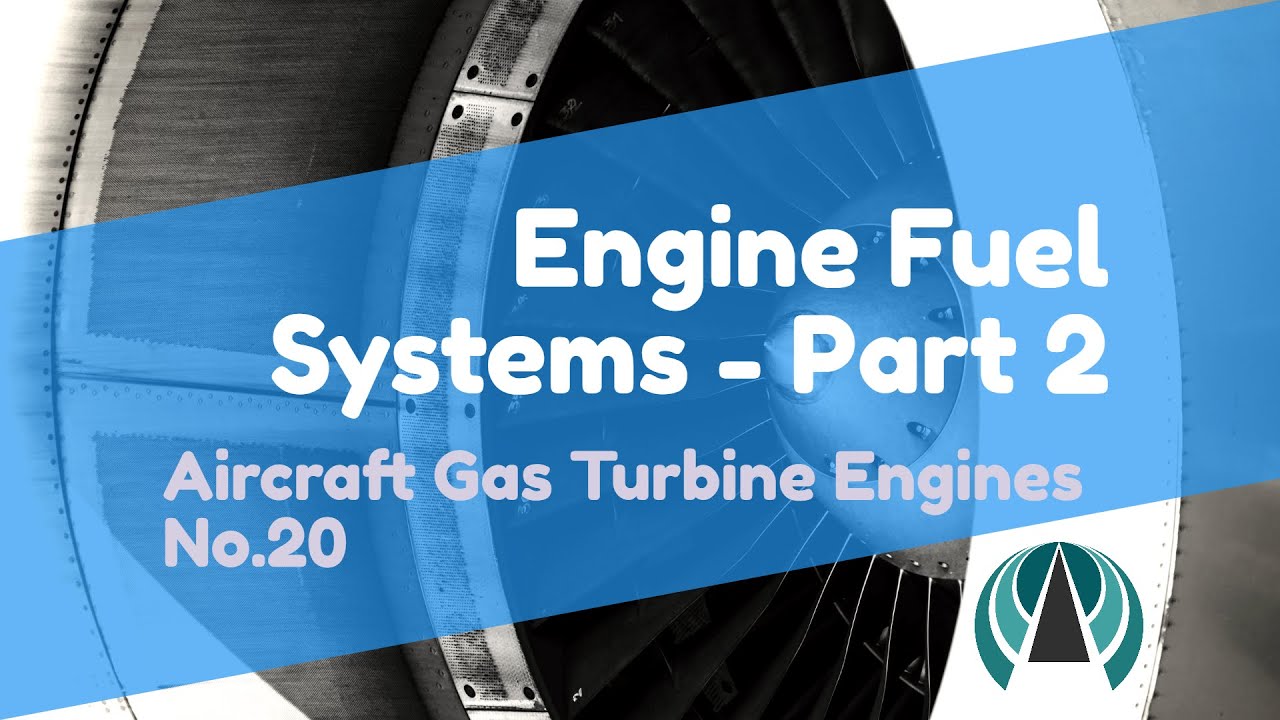
Engine Fuel Systems Part 2 - Aircraft Gas Turbine Engines #20
5.0 / 5 (0 votes)