Aircraft Gas Turbine Engines #03 - Introduction Part 3
Summary
TLDRThis script delves into the intricacies of gas turbine engines, detailing how air velocity and pressure adjustments are crucial for engine efficiency. It explains the role of duct shapes in managing kinetic and pressure energy transformations, and the significance of compressor and turbine design in various engine types like turbojets, turboprops, and turboshafts. The script also touches on bypass ratios and their impact on propulsive efficiency, highlighting the evolution of engine technology to meet the demands of modern aviation.
Takeaways
- 🌬️ The efficiency of an engine is influenced by how well it manages air's velocity and pressure changes through ducts of different shapes.
- 🔥 At the exhaust nozzle, pressure is reduced to ambient levels, leading to a significant increase in gas velocity.
- 📦 Divergent ducts are used post-compressor to increase air pressure without additional energy expenditure and to decrease velocity for easier combustion.
- ⏫ A convergent duct accelerates gas towards the turbine blades, enhancing torque transfer and engine efficiency.
- 🔩 In a spool setup, a compressor and turbine are on the same shaft, common in fighter aircraft for high-speed operations.
- 🔄 Turboprop engines convert gas stream energy into mechanical energy to drive both the compressor and the propeller, with minimal residual thrust.
- 🚀 Turboshaft engines, used in helicopters and power supply units, feature a free power turbine for a broader operating speed range.
- ⏏️ Modular construction in engines allows for easier maintenance by replacing engine sections rather than entire units.
- 🌀 Bypass engines, like the fan jet, offer high propulsive efficiency by using a large mass of air at lower velocities.
- 📉 Specific fuel consumption is lower in low and high bypass ratio engines compared to pure turbojets, making them more efficient for transport aircraft.
Q & A
What adjustments are necessary as air passes through the engine?
-As air passes through the engine, adjustments to its velocity and pressure must be made. This includes compressing the air during the compression stage without significantly increasing its velocity, and dropping the pressure to ambient levels at the exhaust nozzle to increase velocity.
How do different duct shapes affect the air within an engine?
-Different duct shapes are used to change the pressure and velocity of air within an engine. For instance, a divergent duct increases pressure without adding energy, while a convergent duct accelerates the gas to transfer more torque to the turbine.
What is the significance of the design of ducts in an engine?
-The design of ducts is crucial as it affects the efficiency of energy conversion between kinetic and pressure energy, which in turn reflects on the overall engine efficiency.
How does a divergent duct benefit the engine's operation?
-A divergent duct provides two benefits: it increases air pressure without the need for additional compressor energy, and it decreases air velocity, making combustion in the chamber more manageable.
What is the purpose of a convergent duct in the exhaust nozzle?
-A convergent duct is used to accelerate the gas, which increases the rate of gas flow into the turbine, thereby increasing the torque applied to the turbine blade.
What is a spool in the context of gas turbine engines?
-A spool refers to a unit where a compressor and turbine are joined on one shaft, such as in a single spool axial flow compressor turbojet engine.
How does a turboprop engine differ from a turbojet in terms of power handling?
-In a turboprop engine, almost all the energy in the gas stream is converted into mechanical energy to drive the compressor and propeller, with only a small amount of jet thrust available. In contrast, a turbojet uses virtually all remaining energy after the compressor for thrust.
What is the role of a centrifugal compressor in a turboshaft engine?
-In a turboshaft engine, a centrifugal compressor is used in the high-pressure stage to throw air out radially so it can enter the combustion chamber correctly, allowing for a shorter, stiffer, and lighter engine design.
What is the function of a free power turbine in a turboshaft engine?
-A free power turbine is a turbine not connected to any compressors, allowing it to operate at a wider speed range. It converts any remaining energy in the gas stream to mechanical energy for the attached load.
What is the significance of bypass ratio in engine design?
-The bypass ratio is the ratio of air bypassed around the engine's hot core to the air passing through it. Engines with higher bypass ratios are more efficient at lower speeds, offering better propulsive efficiency and lower specific fuel consumption.
How does the propulsive efficiency of different engine types compare?
-At lower speeds, turboprops have the highest propulsive efficiency, but this drops off above 350 mph. Turbojets have lower efficiency at low speeds but improve beyond 800 mph, where turboprops cannot match. Bypass engines, both low and high ratio, offer efficiencies between turboprops and pure turbojets at speeds typical for jet transport aircraft.
Outlines
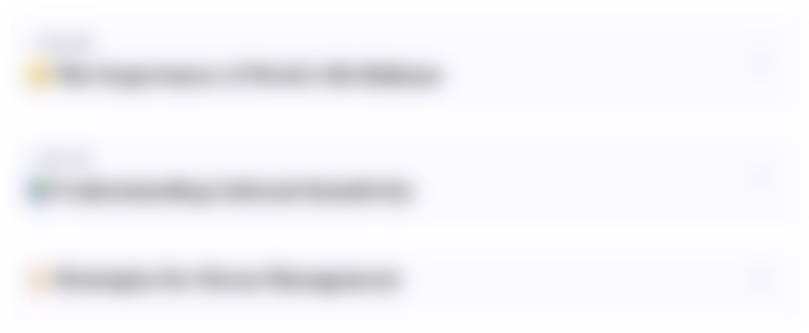
This section is available to paid users only. Please upgrade to access this part.
Upgrade NowMindmap
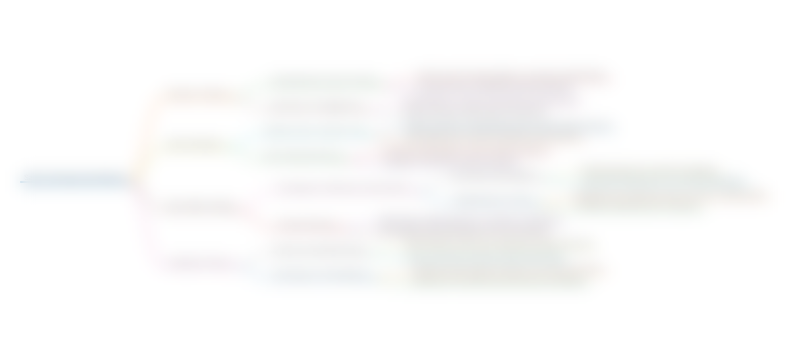
This section is available to paid users only. Please upgrade to access this part.
Upgrade NowKeywords
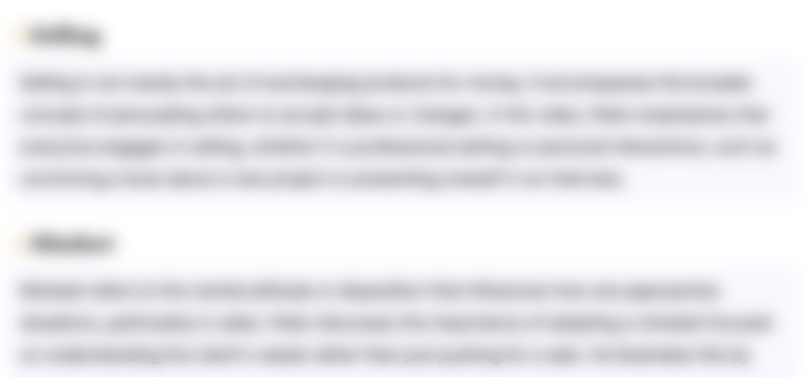
This section is available to paid users only. Please upgrade to access this part.
Upgrade NowHighlights
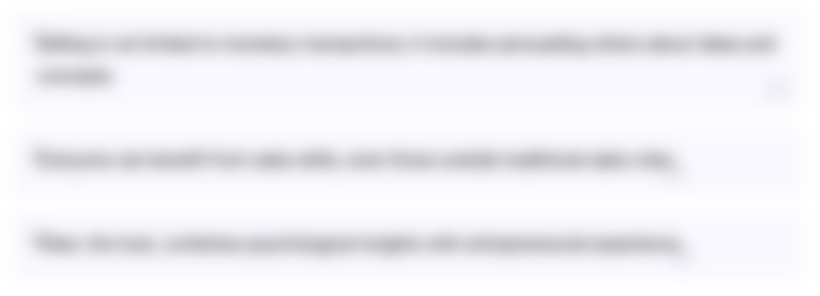
This section is available to paid users only. Please upgrade to access this part.
Upgrade NowTranscripts
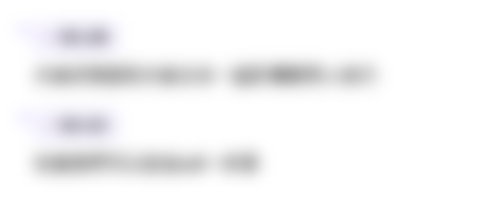
This section is available to paid users only. Please upgrade to access this part.
Upgrade Now5.0 / 5 (0 votes)