Hydraulic Training Series - Chapter 5 - Directional Valves
Summary
TLDRThis training video, part of an eight-part series on hydraulics, focuses on directional valves. It explains various valve types, including poppet, rotary, and sliding spool valves, and their functions in hydraulic systems. The video delves into how these valves control fluid flow, with detailed explanations of open and closed center configurations, and various spool designs that optimize energy use. Additionally, it covers the use of pilot-operated solenoid control valves and their role in modern hydraulic machinery. The video provides a comprehensive understanding of directional valves, their operation, and their applications in hydraulic systems.
Takeaways
- 😀 Directional valves in hydraulics control the flow direction in a hydraulic system.
- 😀 The three main types of directional valves are poppet type, rotary type, and sliding spool type.
- 😀 A poppet-type check valve prevents reverse flow by using a poppet held on its seat by a spring.
- 😀 A restriction check valve has a small orifice through the poppet, allowing free flow in one direction and restricted flow in the other.
- 😀 A pilot-operated check valve uses a plunger to unseat the poppet when pilot pressure is applied.
- 😀 Rotary valves are less common but are used to interconnect ports to control the flow to cylinders or hydraulic motors.
- 😀 Sliding spool valves are versatile and have multiple flow paths depending on the position of the spool.
- 😀 Open-center spools allow oil to flow freely between all ports when centered, making the pump flow available for other operations.
- 😀 Closed-center spools block all ports in neutral, raising the system pressure unless oil is used elsewhere in the system.
- 😀 Type 1 spools support a load while unloading the pump, saving energy, and Type 3 spools allow the pump flow to be used elsewhere in the system.
- 😀 Solenoid-operated valves are commonly used in modern machinery for controlling larger valves, especially in pilot-operated control systems.
Q & A
What are the three main types of hydraulic directional valves mentioned in the script?
-The three main types of hydraulic directional valves are poppet type, rotary type, and sliding spool type.
How does the poppet type check valve work?
-The poppet type check valve uses a spring to hold the poppet on its seat. Flow into the outlet port increases the spring load, preventing reverse flow, while flow to the inlet port overcomes the spring force and allows free flow.
What is a restriction check valve, and how does it differ from a standard check valve?
-A restriction check valve has a small orifice through the poppet, allowing free flow in one direction and restricted flow in the other, unlike a standard check valve that allows free flow in one direction and prevents reverse flow entirely.
What is the function of a pilot-operated check valve?
-A pilot-operated check valve includes a plunger that unseats the poppet when pilot pressure is applied, allowing reverse flow through the check valve.
What is the purpose of a rotary valve in hydraulic systems?
-A rotary valve is used to control the direction of flow to extend and retract a cylinder or drive and reverse a hydraulic motor. It has pressure, tank, and cylinder ports and interconnecting passages through the rotor.
How do sliding spool valves work, and what are their two shifted positions?
-Sliding spool valves have a spool that shifts between two positions to control flow to cylinder ports. In one position, pressure is directed to port A and port B is connected to tank, and vice versa in the other position.
What happens when the spool of a sliding valve is in the centered position?
-When the spool is centered, all ports are open to tank, allowing oil to flow freely between the ports. This condition is important for managing system pressure and flow.
What is the difference between open center and closed center spool valves?
-An open center spool valve allows oil to flow freely between all ports when centered, reducing system pressure to just what is needed for pump flow. A closed center spool valve blocks all ports in the neutral position, raising system pressure to the relief valve setting.
What is a tandem center spool, and how is it used in hydraulic systems?
-A tandem center spool has a hollow center land that blocks both cylinder ports but allows oil to flow from the pressure port to the tank port. This configuration enables valves to be piped in tandem, where oil flows freely back to the tank when the spools are neutral.
How are solenoids used to control hydraulic valves in modern systems?
-Solenoids are used to control larger valves hydraulically, with small solenoid-operated valves used to control pilot-operated valves. This allows for precise control of large valves, and the pilot pressure is typically supplied from the valve’s pressure port or an external source.
Outlines
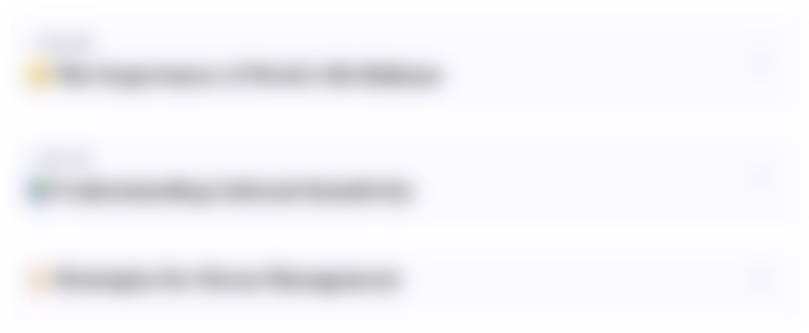
Esta sección está disponible solo para usuarios con suscripción. Por favor, mejora tu plan para acceder a esta parte.
Mejorar ahoraMindmap
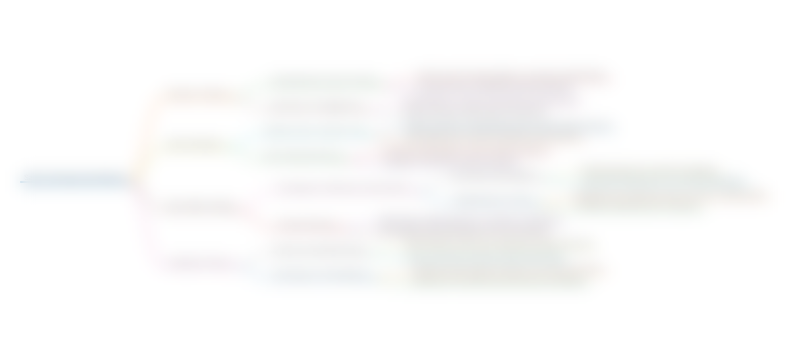
Esta sección está disponible solo para usuarios con suscripción. Por favor, mejora tu plan para acceder a esta parte.
Mejorar ahoraKeywords
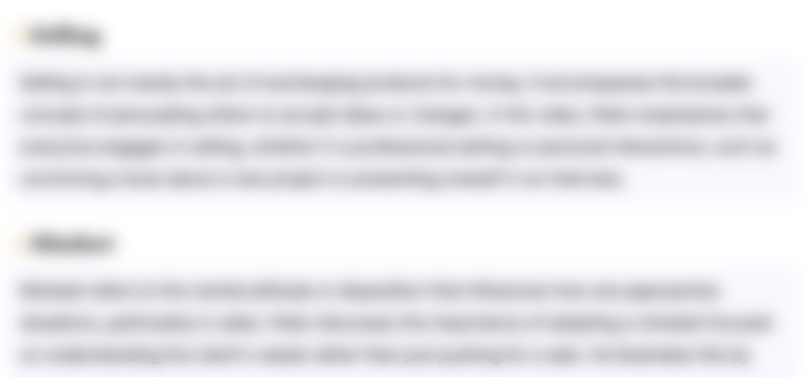
Esta sección está disponible solo para usuarios con suscripción. Por favor, mejora tu plan para acceder a esta parte.
Mejorar ahoraHighlights
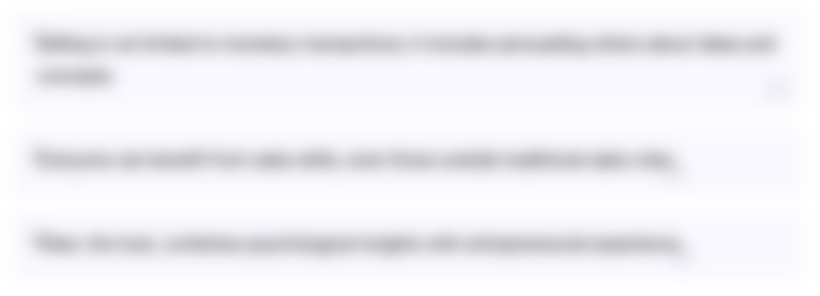
Esta sección está disponible solo para usuarios con suscripción. Por favor, mejora tu plan para acceder a esta parte.
Mejorar ahoraTranscripts
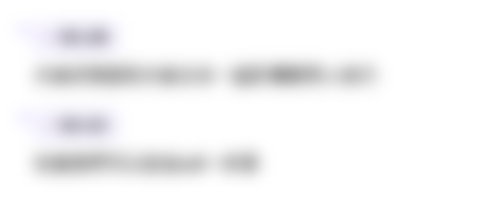
Esta sección está disponible solo para usuarios con suscripción. Por favor, mejora tu plan para acceder a esta parte.
Mejorar ahoraVer Más Videos Relacionados
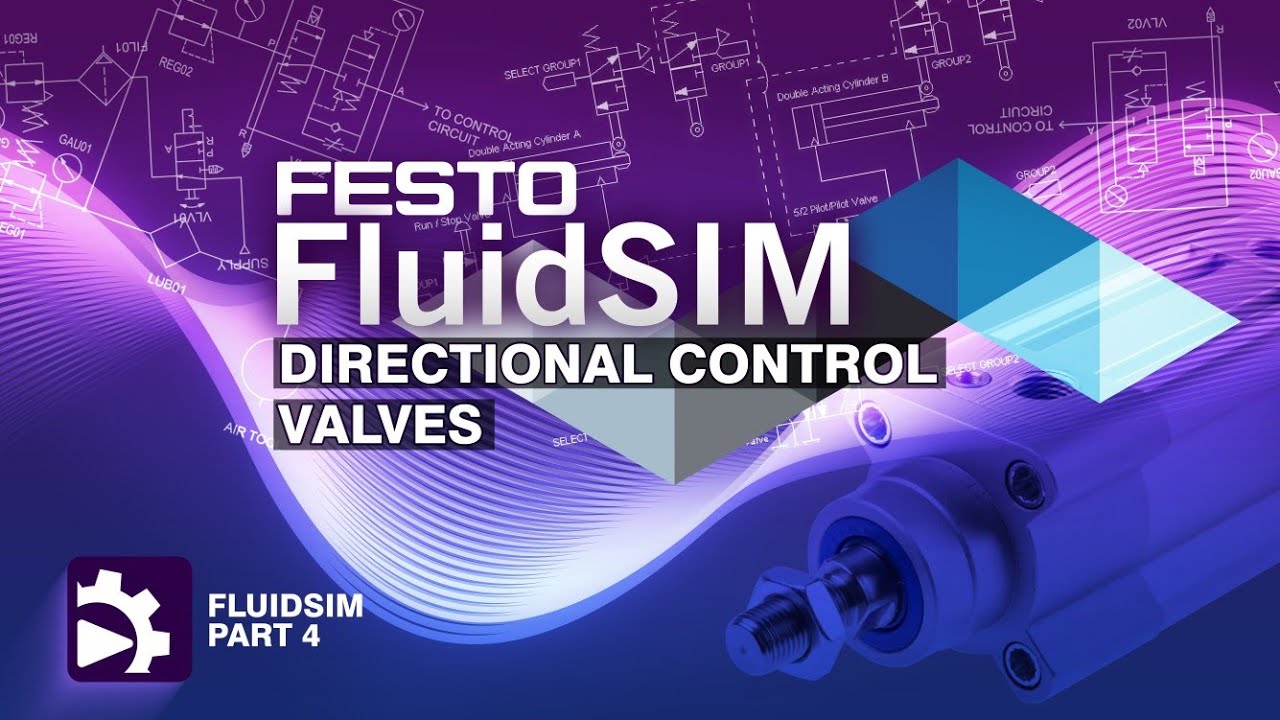
Understanding Directional Control Valve Basics & Symbols | Introduction to FluidSIM | Tutorial 4
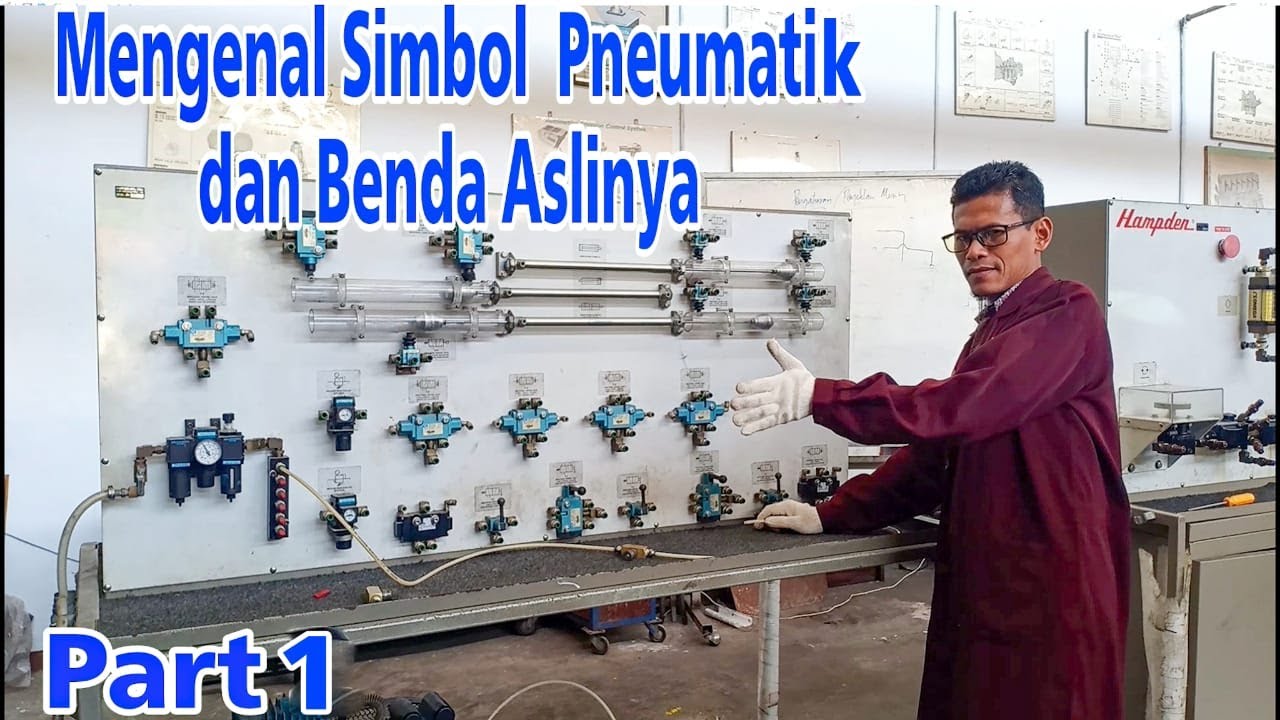
Mengenal Simbol Pneumatik dan Benda Aslinya #waginothok
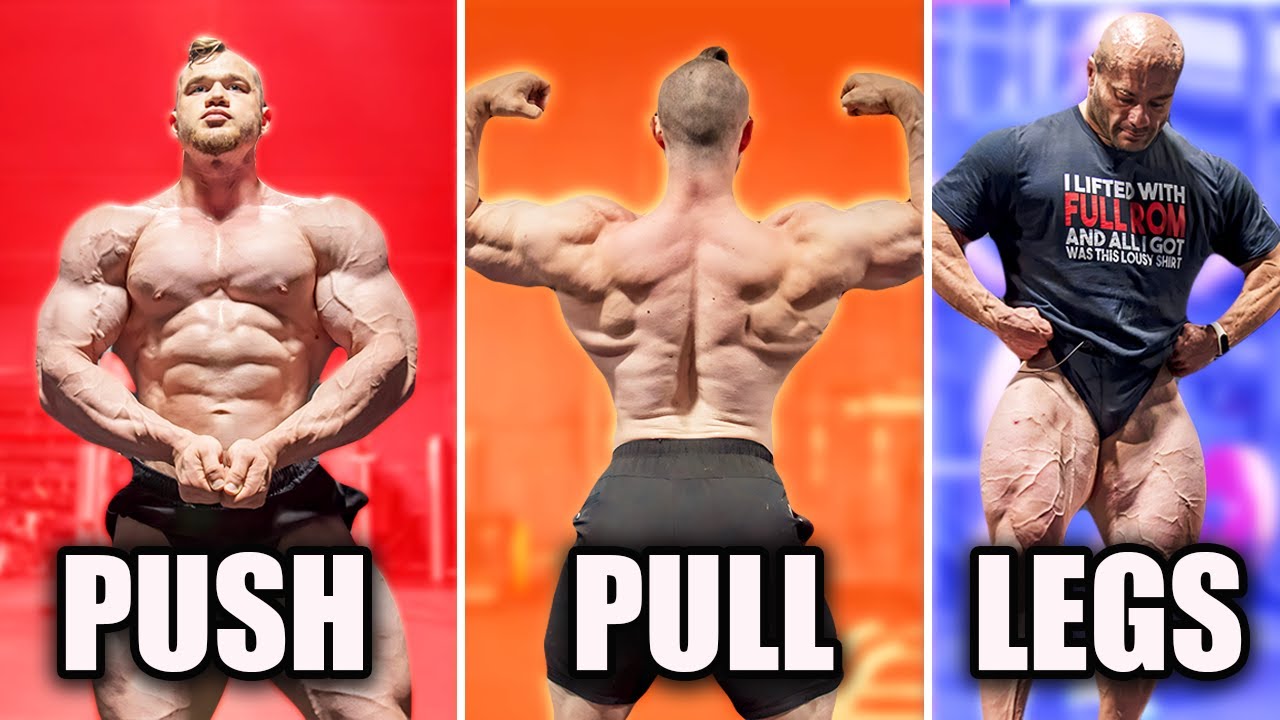
How To Design An Amazing Muscle Growth Training Split (ft. RP Hypertrophy App)

FULL TOEFL ITP LISTENING: Practice Test With Answers | Listening Practice

Blue Team Training Course - Introduction

How To Set Valve Lash On A 6.6 Duramax Diesel Engine
5.0 / 5 (0 votes)