Andon System
Summary
TLDRThe video explains the concept of an Andon system, a signaling tool used in production environments to monitor and alert about the status of a production line. It uses visual signals, like green, amber, and red lights, to indicate whether the line is running smoothly, paused, or experiencing issues. The system can be connected to computers or databases for remote monitoring. Additionally, Andon boards display key performance metrics, such as production targets and shifts, helping management identify problems and optimize performance across various shifts and lines.
Takeaways
- 💡 Andon is a signal or alerting tool used to identify problems in production lines.
- 🚦 The Andon system typically uses a light system with green, amber, and red lights to indicate the status of a production line.
- ✅ A green light means the production line is running smoothly without any issues.
- ⏸️ An amber or yellow light signals that the line is paused, either by operator input or an automatic sensor.
- 🛑 A red light indicates a significant problem, and the production line may be stopped or shut down.
- 🖥️ Andon systems can be integrated with PLCs and computers, allowing remote monitoring of production line status.
- 🔄 Andon signals can be connected to databases for real-time updates and remote access for engineers or managers.
- 📊 Andon boards provide detailed production line data, such as shift targets and performance metrics.
- 🔍 Andon boards are useful for identifying issues, such as a shift not meeting its production target, prompting management to investigate.
- 📉 Different types of Andon boards can display specific statuses like 'line running,' 'jammed,' or 'needs material,' providing a clear overview of the production line health.
Q & A
What is an Andon system?
-An Andon system is a signal or alerting tool used in production environments to indicate the status of a process or machine. It can take the form of a light system or an Andon board.
What do the different colors of the Andon lights signify?
-In the Andon system, green indicates the production line is running well without issues, amber or yellow means the line is on hold or paused, and red signifies a larger problem, potentially shutting the line down completely.
How does an Andon system help in production management?
-The Andon system alerts workers or management when there are issues on the production line, allowing them to address problems quickly. It can also be linked to databases and computers, enabling remote monitoring of the line's status.
What might cause the Andon light to turn amber/yellow?
-An amber or yellow light typically indicates that the line is paused, possibly due to operator input, a sensor stopping the line temporarily, or issues like line balancing.
How does the Andon system support remote monitoring?
-The Andon system can be connected to databases or computers, allowing process engineers or management to monitor the production line remotely through software, even if they are in a different location.
What example is given to explain a red light on the Andon system?
-A red light in the Andon system indicates a larger issue where the production line may have stopped entirely, requiring immediate attention to resolve the problem.
What additional information can be displayed on an Andon board?
-An Andon board can display information such as shift targets, current production numbers, and line status (e.g., running, jammed, needs material), giving an overview of the production line's health.
What does the shift target information on the Andon board signify?
-The shift target information shows the expected number of units to be produced during each shift. It compares actual production to the target, indicating any discrepancies between planned and actual output.
How can an Andon system trigger problem-solving in management?
-The Andon system can highlight issues such as missed production targets or downtime, prompting management to investigate and address the root causes, such as underperformance on a specific shift.
What is one of the key benefits of using Andon systems in production environments?
-One of the key benefits of using Andon systems is the ability to quickly identify and resolve problems on the production line, minimizing downtime and improving overall efficiency.
Outlines
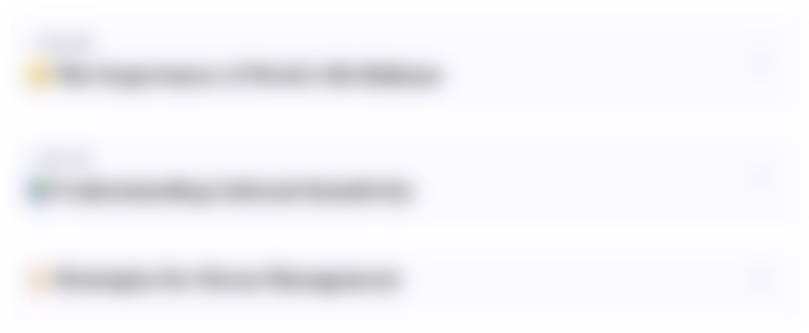
Esta sección está disponible solo para usuarios con suscripción. Por favor, mejora tu plan para acceder a esta parte.
Mejorar ahoraMindmap
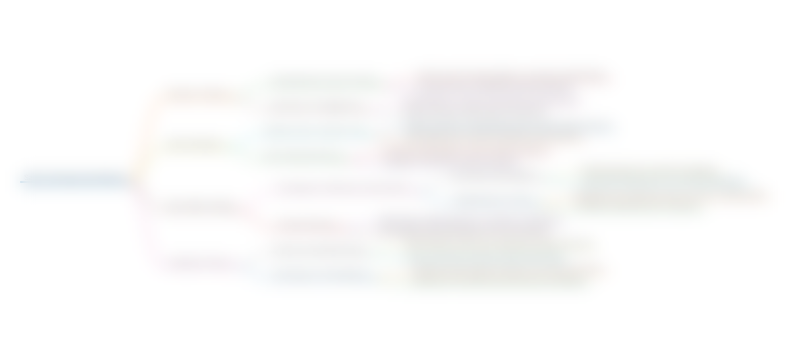
Esta sección está disponible solo para usuarios con suscripción. Por favor, mejora tu plan para acceder a esta parte.
Mejorar ahoraKeywords
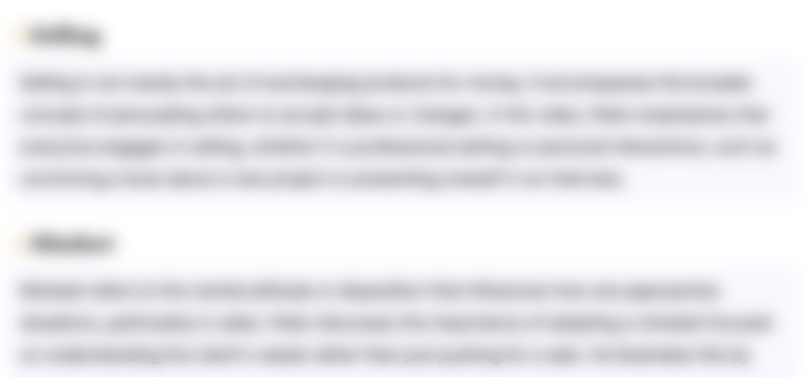
Esta sección está disponible solo para usuarios con suscripción. Por favor, mejora tu plan para acceder a esta parte.
Mejorar ahoraHighlights
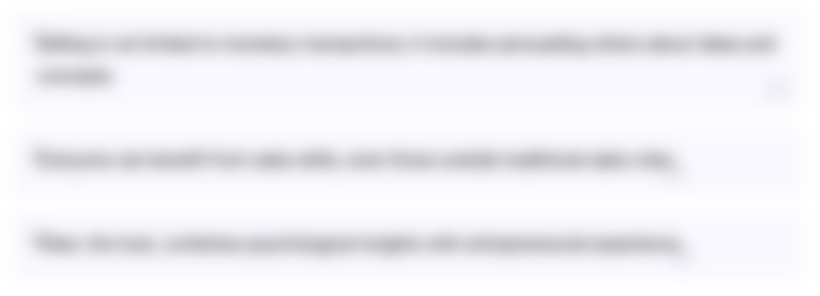
Esta sección está disponible solo para usuarios con suscripción. Por favor, mejora tu plan para acceder a esta parte.
Mejorar ahoraTranscripts
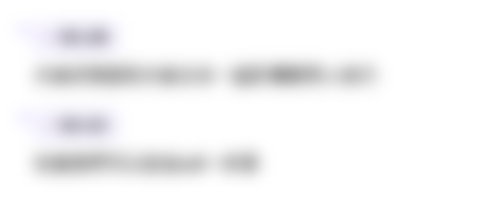
Esta sección está disponible solo para usuarios con suscripción. Por favor, mejora tu plan para acceder a esta parte.
Mejorar ahora5.0 / 5 (0 votes)