Sistema ANDON
Summary
TLDRThe video explains how the Ander Automation system enhances productivity and reduces downtime in production environments. It highlights the system's ability to detect machine or material issues, alert support teams, and provide real-time monitoring using visual and audible indicators. The system allows for detailed electronic documentation of downtime, visible through a user-friendly web interface. By offering solutions for Lean Manufacturing and improving problem-solving efficiency, the Ander Automation system helps reduce operational costs and contributes to a return on investment over the medium term.
Takeaways
- ๐ค Automation systems help operators and machines work efficiently under normal conditions.
- โ๏ธ The system prepares users for unexpected situations like material shortages, machine malfunctions, safety issues, or human errors.
- ๐ Real-time monitoring is key to increasing production capacity and reducing downtime.
- ๐ Traditional methods to solve issues involve using radios, phones, or physically searching for assistance, which delays problem-solving.
- ๐จ The automation system provides real-time alerts with visual and audible cues to indicate the status of production stations.
- ๐ The system uniquely adapts to problems and can document details of downtimes, which are viewable through user-friendly web interfaces.
- ๐ง The system supports lean manufacturing and operates on solid, high-tech architecture with built-in contingencies.
- ๐ When a problem is detected, the system triggers audible and visual alarms to notify support areas.
- ๐ก The system reduces the time and effort needed to solve issues, improving equipment efficiency.
- ๐ธ In the medium term, this automation system helps reduce costs and contributes to return on investment.
Q & A
What is the main challenge discussed in the script?
-The main challenge is how to efficiently respond to problems such as material shortages, machine malfunctions, safety issues, or human errors in a production environment.
What are the traditional methods used to solve production issues without a specialized system?
-Traditional methods involve using radio, telephone, or physically searching for someone to help solve the issue, which often results in delayed responses.
How does the automation system help address production issues?
-The automation system reduces the effort needed to solve problems, increases productivity, and allows for real-time monitoring using graphical and audible indicators to display the production status and type of problem.
What are the benefits of using the automation system for real-time monitoring?
-It allows users to monitor production in real time, providing graphical and audible notifications that show the status of production stations and the nature of any issues, enabling faster responses.
How does the automation system help document and analyze downtime?
-The system electronically documents the details of downtime, which can be visualized as graphs through a user-friendly web interface.
What manufacturing methodology does the automation system support?
-The system supports lean manufacturing by implementing solutions that focus on minimizing waste and optimizing efficiency.
What happens when a problem is detected in the production station?
-An audible and visual event is triggered, notifying the support areas of the occurrence of downtime so that corrective actions or escalations can be taken to resolve the issue.
How does the automation system reduce the effort needed to solve problems?
-The system alerts support areas automatically, reducing the need for manual intervention and minimizing the time and effort people spend solving problems.
What impact does the automation system have on equipment efficiency and cost reduction?
-The system improves equipment efficiency by reducing downtime and the related costs, contributing to a better return on investment over the medium term.
How does the automation system's architecture contribute to its effectiveness?
-The system is built on a solid, high-tech architecture that supports contingency planning, ensuring reliable performance even in the face of challenges.
Outlines
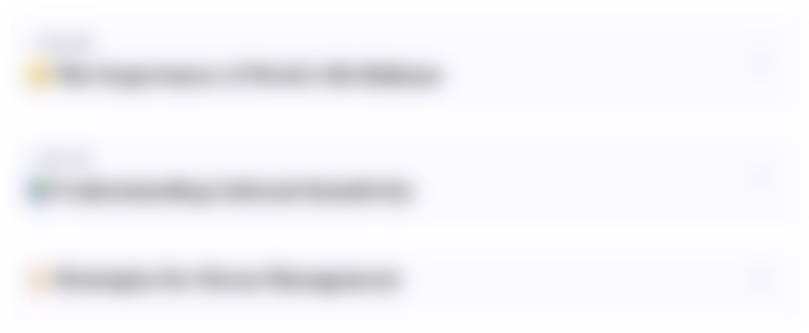
This section is available to paid users only. Please upgrade to access this part.
Upgrade NowMindmap
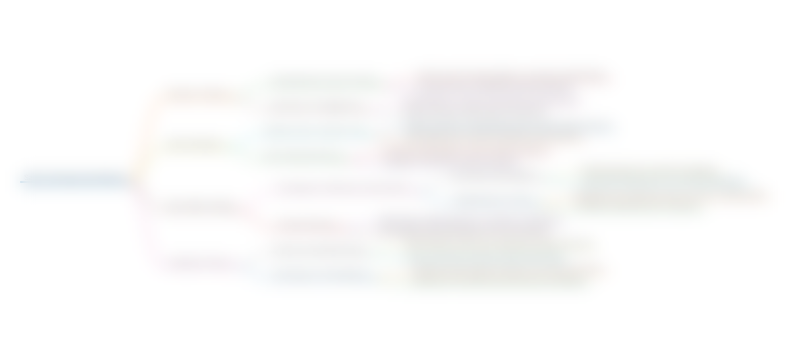
This section is available to paid users only. Please upgrade to access this part.
Upgrade NowKeywords
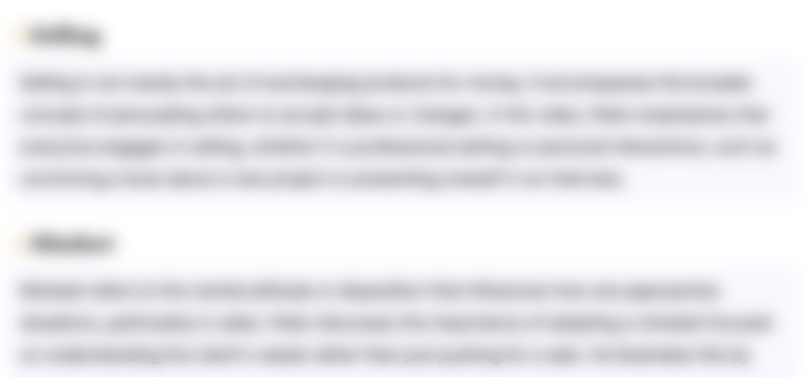
This section is available to paid users only. Please upgrade to access this part.
Upgrade NowHighlights
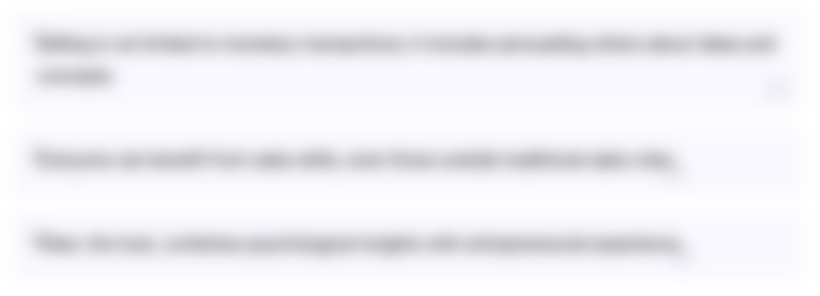
This section is available to paid users only. Please upgrade to access this part.
Upgrade NowTranscripts
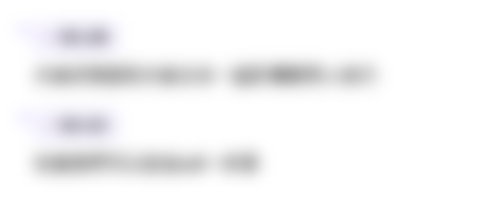
This section is available to paid users only. Please upgrade to access this part.
Upgrade NowBrowse More Related Video
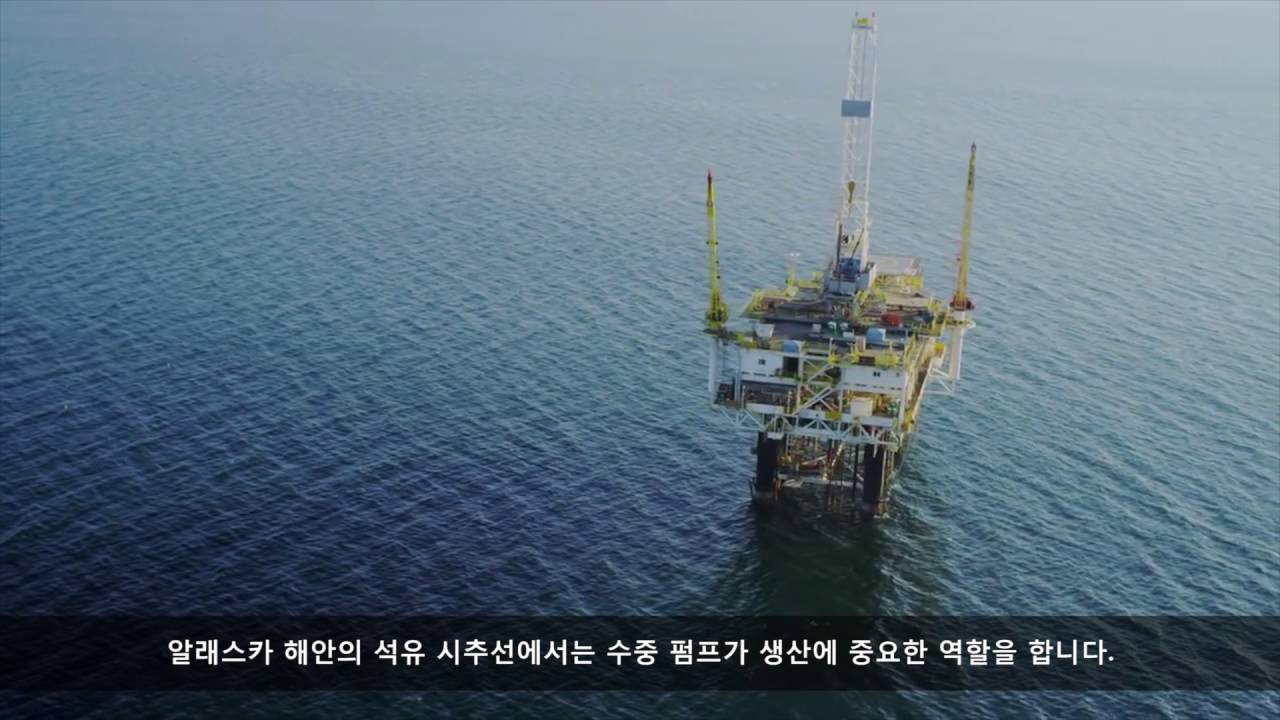
Rockwell Automation fuels the oil and gas industry with IoT subtitled
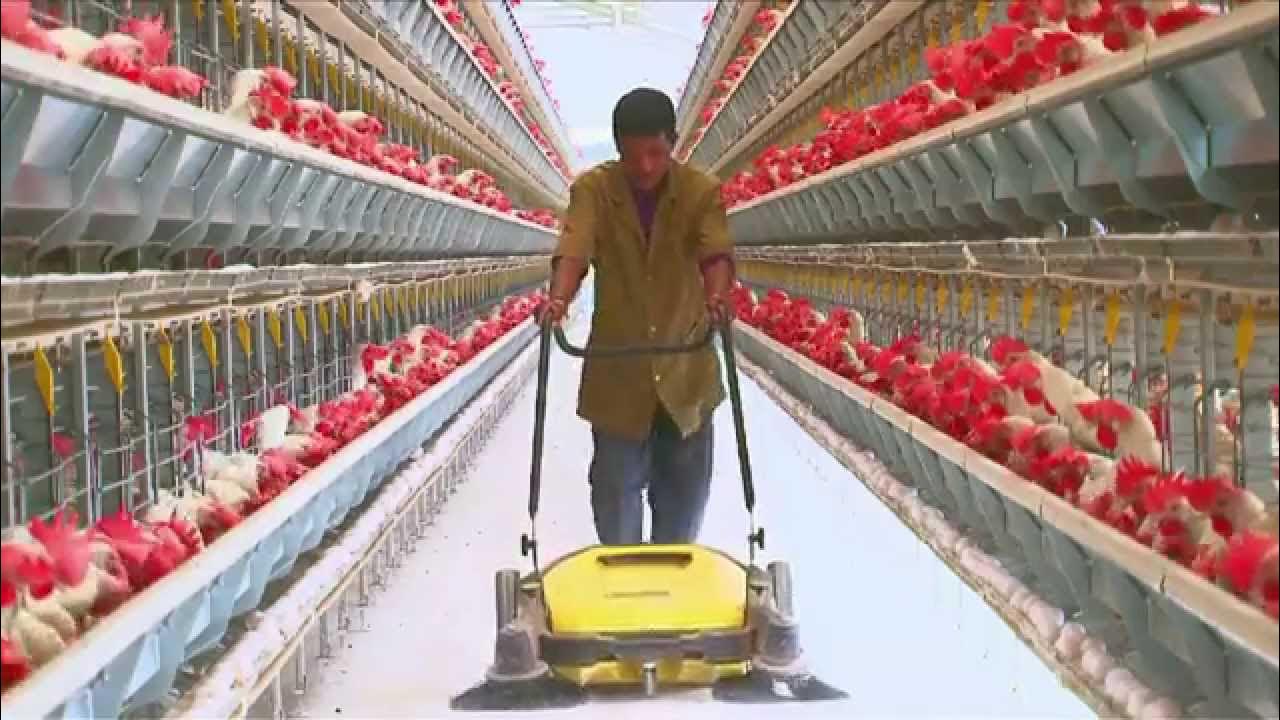
Poultry Farming | Open House Battery Cage System | Egg Production in India
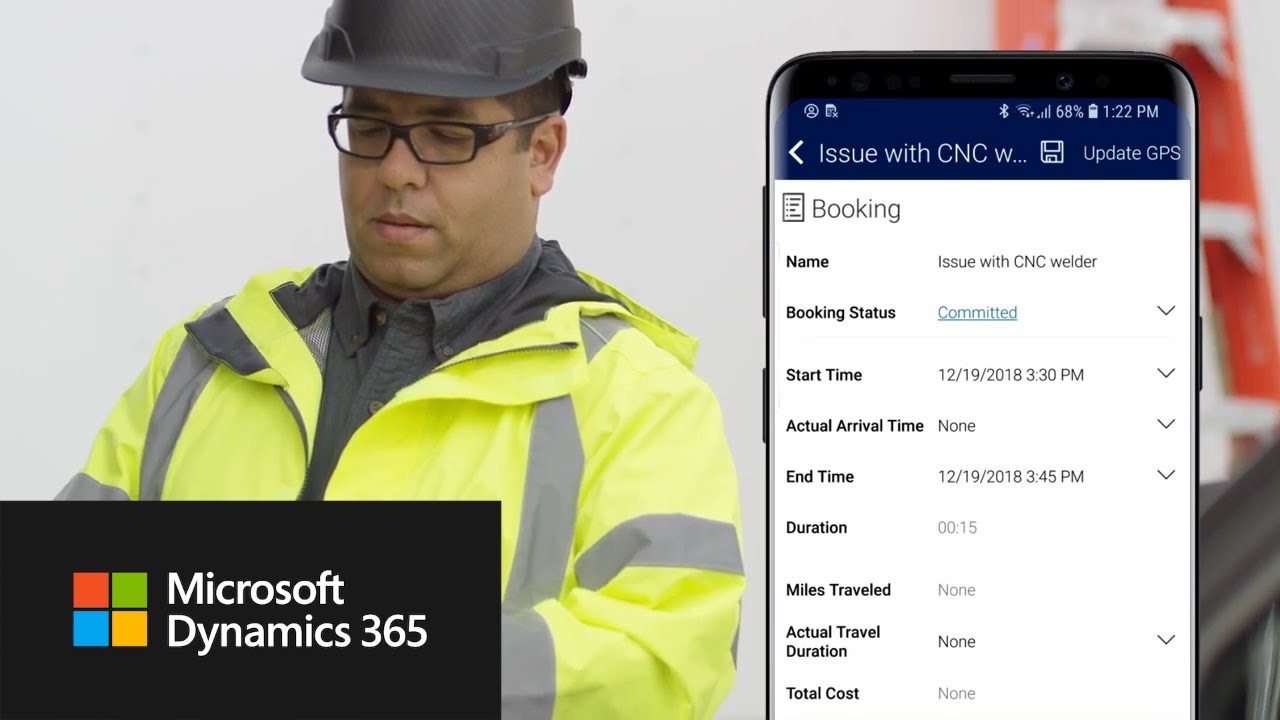
Optimize resource scheduling | Dynamics 365 Field Service

Vanadium Recovery from Stone Coal with Sunresinโs SMB Solution
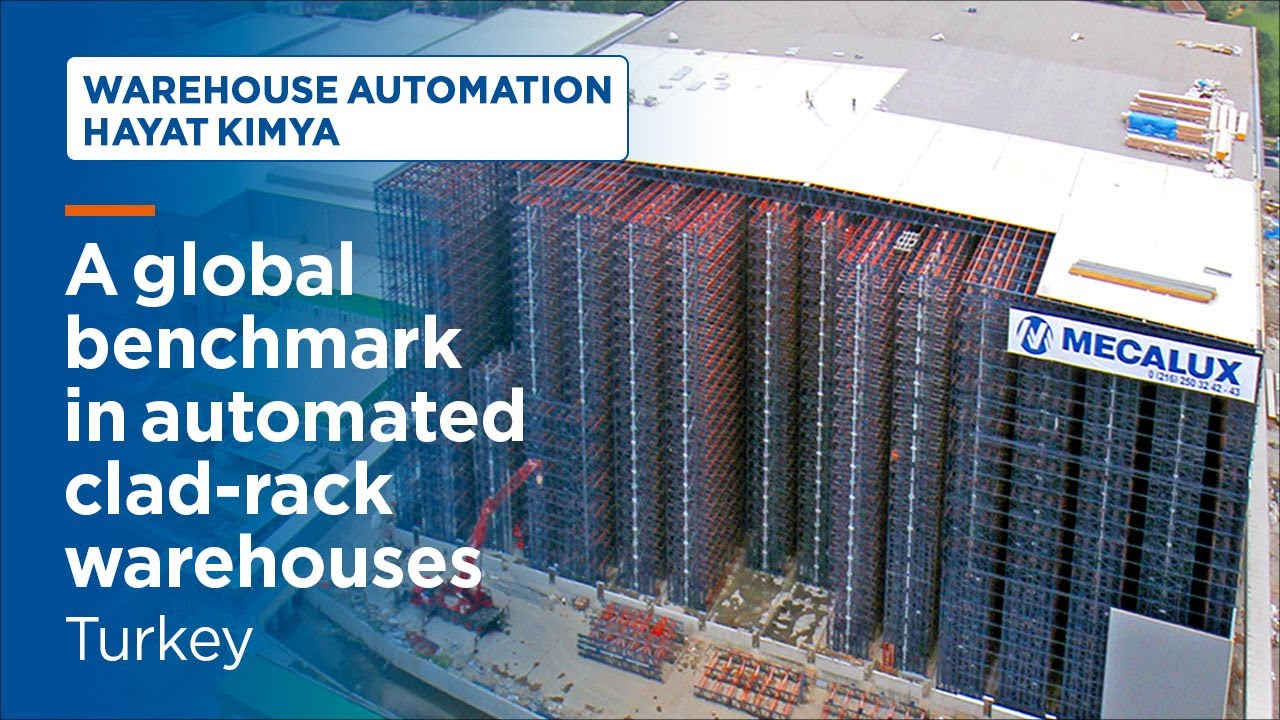
Hayat Kimya, a global benchmark in automated clad-rack warehouses

Penerapan IoT di Bidang Manufaktur - Indobot Academy
5.0 / 5 (0 votes)