Procurement Management (Purchase Order)
Summary
TLDRThis video outlines the process of managing purchase orders within a software platform, from material request creation to purchase booking. The site team raises material requests, which are approved by the admin, and the procurement team generates purchase orders. After approval, materials are delivered to the site, where quantities are confirmed, and any discrepancies are adjusted. Finally, the office team processes the vendor's bill, accounting for payments and balances. This streamlined system ensures efficient procurement management, providing transparency and control at every stage of the process.
Takeaways
- 😀 The purchase order management process begins with the site team raising a material request for a specific project.
- 😀 Material requests must be approved by the Admin team before proceeding to the next steps in the procurement process.
- 😀 Once approved, the procurement team can create a purchase order (PO) for the requested materials.
- 😀 The system automatically fetches the material quantities from the approved requests when raising a purchase order.
- 😀 The procurement team can adjust the unit rates, taxes, and apply discounts during PO creation.
- 😀 After creating the PO, the Admin team must approve it before it can be sent to the vendor.
- 😀 Once the PO is approved, the vendor delivers the materials to the site, and the site team logs the received items.
- 😀 If any discrepancies exist in the quantity or type of materials received, the site team can adjust the details in the system.
- 😀 The office team receives the vendor bill, enters purchase booking details, and records any advance payments made.
- 😀 Once all materials are received and the bill is recorded, the purchase order is considered complete and the remaining balance is tracked.
- 😀 The process is systematic and ensures that all material requests, approvals, purchase orders, deliveries, and billing are well-managed through the software.
Q & A
What is the first step in the procurement process described in the script?
-The first step is the site team raising a material request for the required items, such as aggregates or stone, within a specific project.
Who approves the material requests raised by the site team?
-The admin is responsible for approving the material requests raised by the site team before they proceed to the next stage of the procurement process.
How does the procurement team create a purchase order (PO) in the system?
-The procurement team creates a purchase order by selecting the approved material requests from the system, choosing the vendor, entering quantities, unit rates, taxes, and any additional discounts or charges, and then saving the PO.
What needs to happen before the purchase order is sent to the vendor?
-Before the purchase order can be sent to the vendor, it must be approved by the admin.
How does the system handle discrepancies in the material quantities received?
-If there are discrepancies in the quantities received (e.g., fewer items than requested), the site team can adjust the received quantities in the system to reflect what was actually delivered.
What information is captured when the site team receives materials on-site?
-The site team records the materials received, such as the vendor name, items received, quantities, any discrepancies, and optionally uploads related documents like bills or images.
What role does the office team play in the purchase order process?
-The office team handles the purchase booking once the vendor sends the bill. They verify the received materials and reconcile the details in the system, adjusting for any advance payments and finalizing the purchase transaction.
Can the procurement team change the PO number or purchase order date?
-Yes, the procurement team can edit the PO number and the purchase order date before saving the order in the system.
What happens after the material purchase order is approved?
-Once the purchase order is approved, the vendor is notified, and the materials are delivered to the site where the site team receives and records them in the system.
How does the system track material requests after a purchase order is raised?
-The system tracks the material requests by moving them into the 'Ordered' section, where it reflects whether the requested materials have been fully or partially ordered based on the purchase orders raised.
Outlines
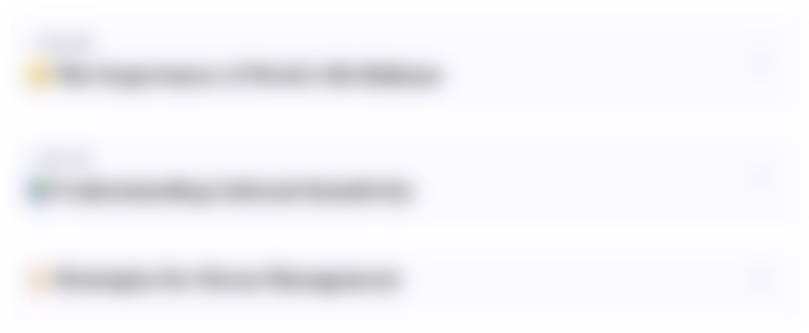
Dieser Bereich ist nur für Premium-Benutzer verfügbar. Bitte führen Sie ein Upgrade durch, um auf diesen Abschnitt zuzugreifen.
Upgrade durchführenMindmap
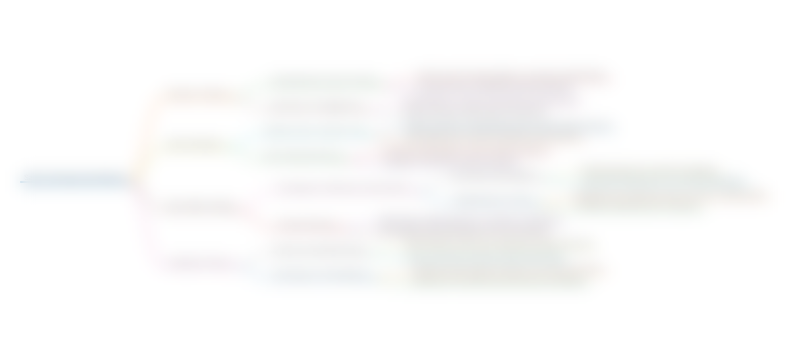
Dieser Bereich ist nur für Premium-Benutzer verfügbar. Bitte führen Sie ein Upgrade durch, um auf diesen Abschnitt zuzugreifen.
Upgrade durchführenKeywords
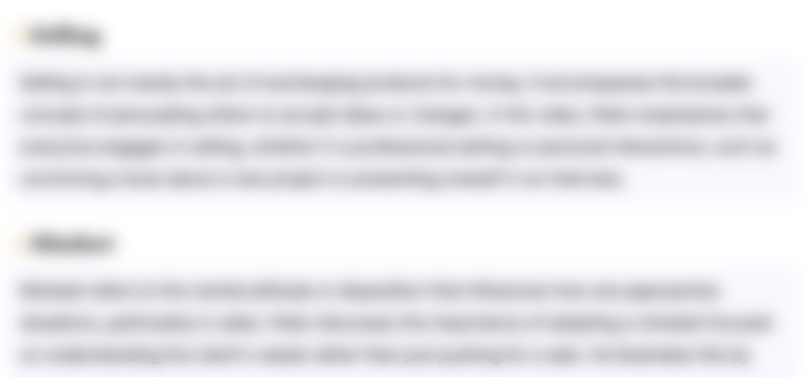
Dieser Bereich ist nur für Premium-Benutzer verfügbar. Bitte führen Sie ein Upgrade durch, um auf diesen Abschnitt zuzugreifen.
Upgrade durchführenHighlights
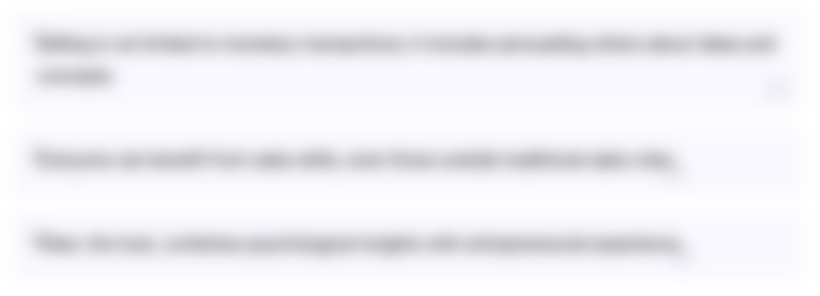
Dieser Bereich ist nur für Premium-Benutzer verfügbar. Bitte führen Sie ein Upgrade durch, um auf diesen Abschnitt zuzugreifen.
Upgrade durchführenTranscripts
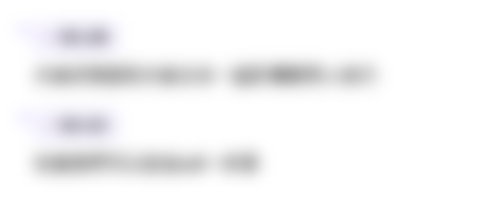
Dieser Bereich ist nur für Premium-Benutzer verfügbar. Bitte führen Sie ein Upgrade durch, um auf diesen Abschnitt zuzugreifen.
Upgrade durchführenWeitere ähnliche Videos ansehen
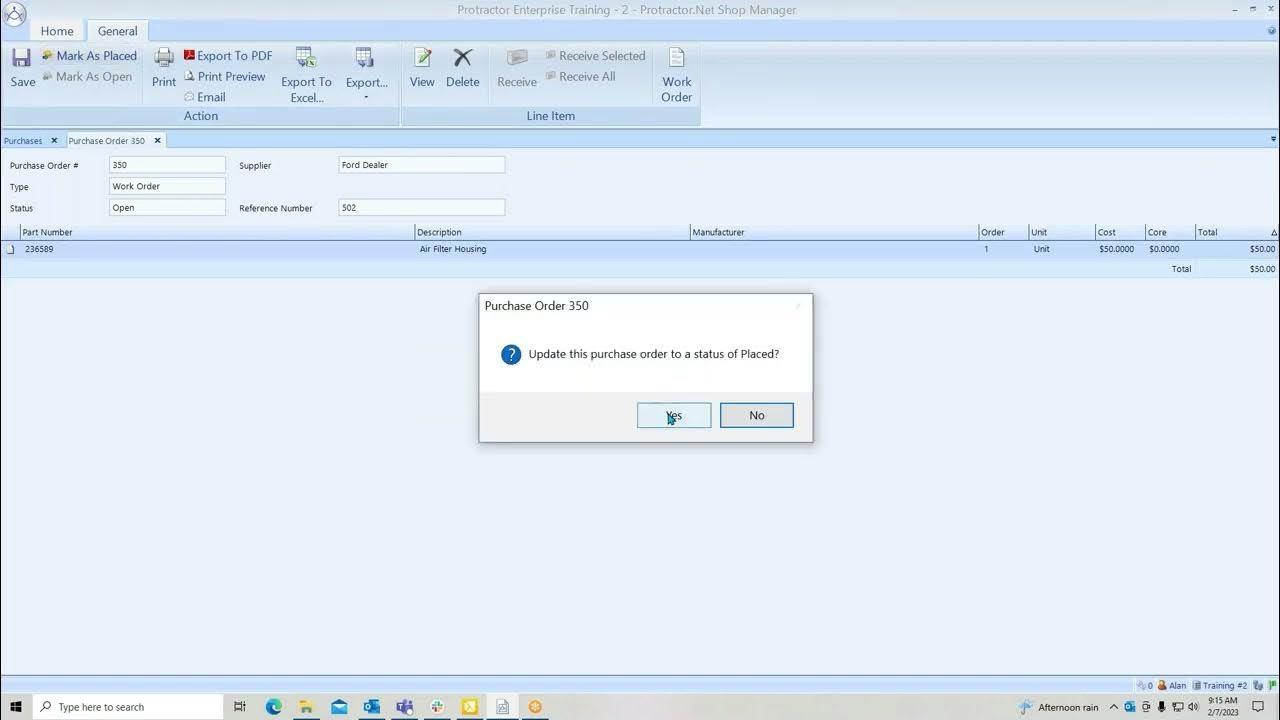
Purchase Orders
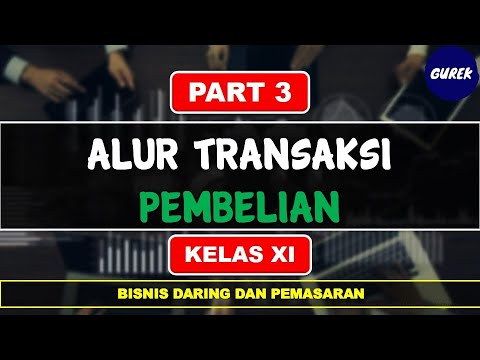
Administrasi Transaksi Kelas XI - (Part 3) - Alur Transaksi Pembelian
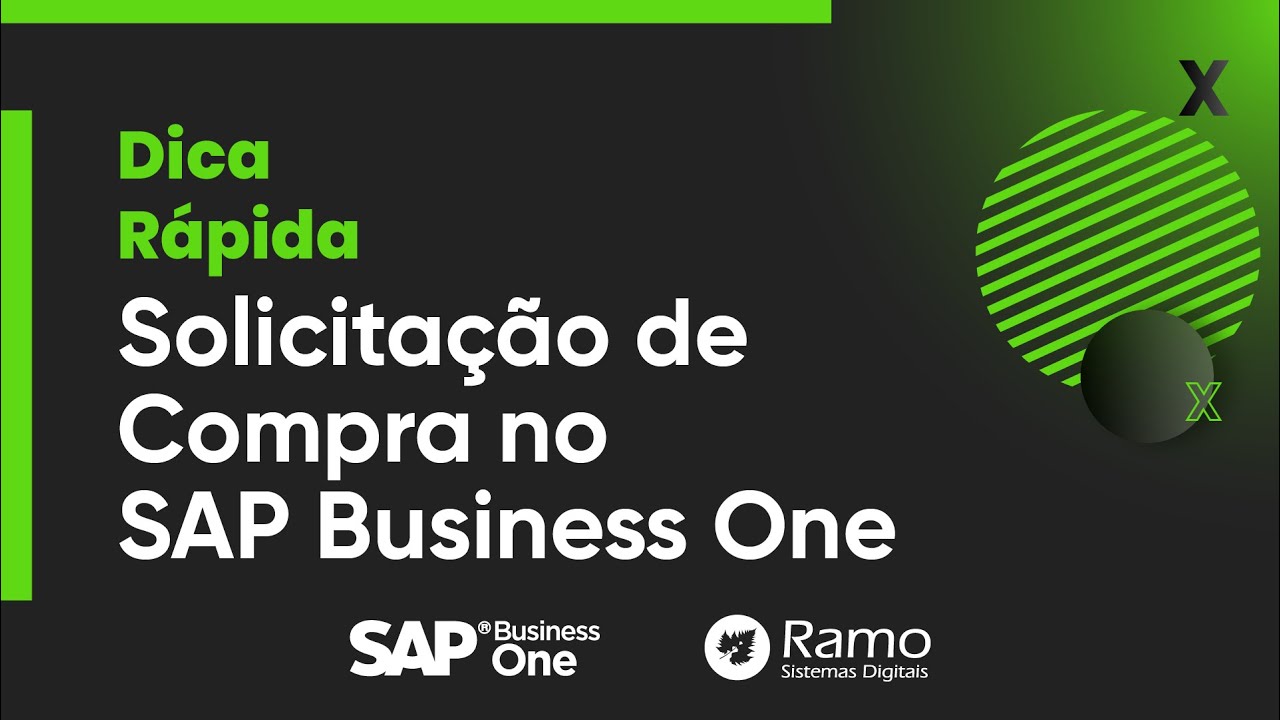
Solicitação de Compra no SAP Business One
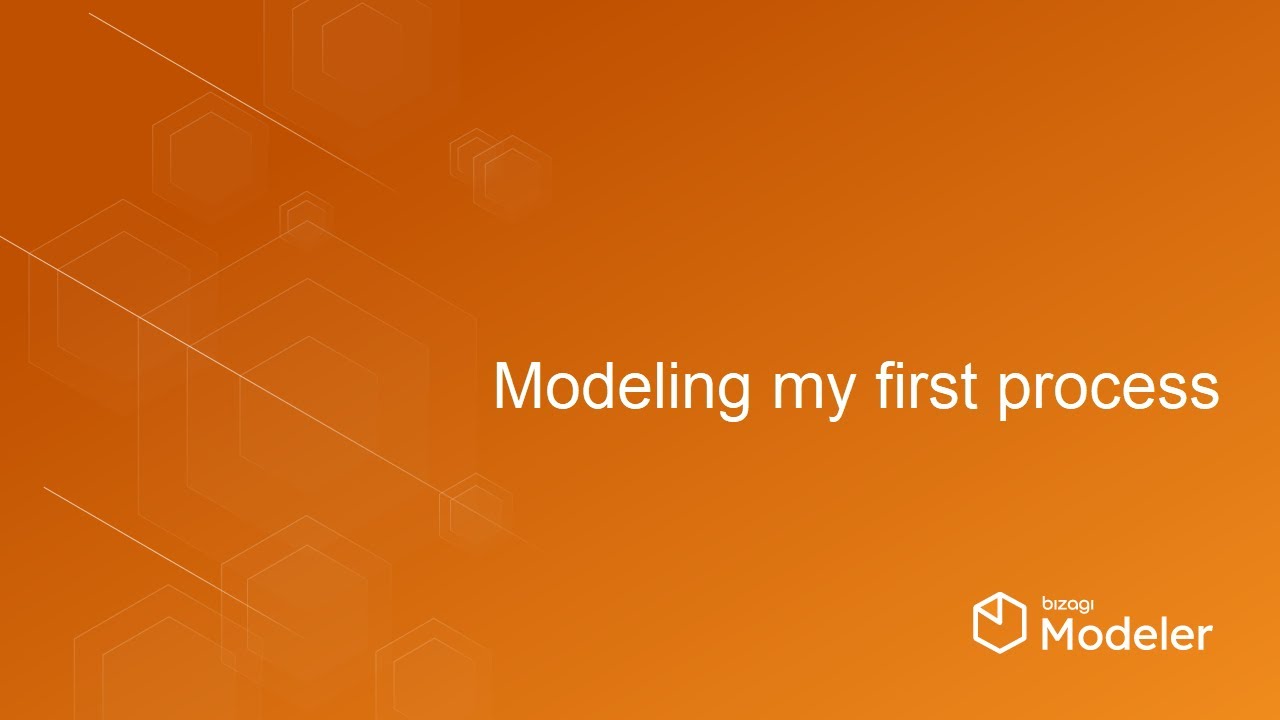
Bizagi Modeler - Modeling my first process
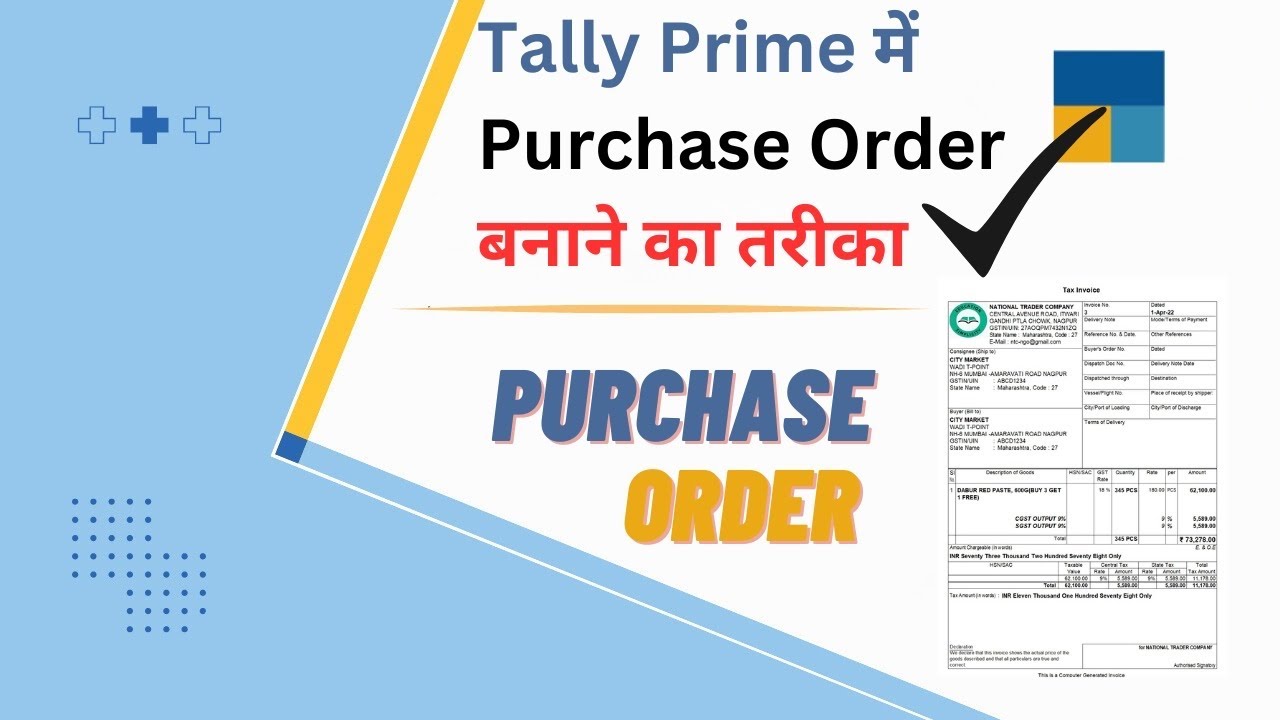
How to make Purchase order in Tally Prime | Tally me purchase order kaise banaye | #purchaseorder
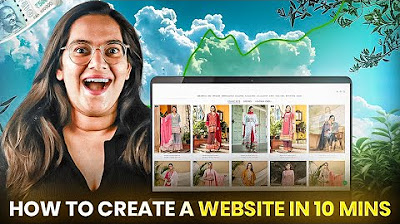
How to Create a WordPress Website in 10 Mins 🚀 (Watch Me Live 🔴)
5.0 / 5 (0 votes)