Pengajian Perniagaan Semester 1: Pengeluaran (alat kawalan inventori: EOQ dan ROP)
Summary
TLDRThe video script discusses economic order quantity (EOQ), a vital concept for businesses to minimize inventory costs. It covers the basics of EOQ, including its relation to demand, ordering costs, and holding costs. The script provides examples of applying EOQ in various scenarios, such as a shoe store owner calculating the optimal order quantity for branded shoes and a fan seller determining the monthly order to meet consistent demand. It also touches on the importance of understanding consistent demand and the benefits of EOQ in reducing costs and improving inventory management.
Takeaways
- π The script discusses the importance of economic order quantity (EOQ) in managing inventory and minimizing costs.
- π’ It mentions the use of intelligence and formulas to determine the ideal order quantity and frequency to reduce storage costs.
- π The concept of EOQ is applied in various business scenarios, such as purchasing and stocking goods to meet consistent demand.
- π The script explains how to calculate EOQ using specific examples, including a shoe store and a fan shop.
- π‘ It highlights the need for consistency in demand to effectively utilize the EOQ model for inventory management.
- π The importance of understanding the demand pattern, such as daily, weekly, or monthly, is emphasized for accurate EOQ calculations.
- π The script provides a step-by-step approach to calculating EOQ, including determining the cost of goods sold and the reorder point.
- πΌ It explains the benefits of using EOQ, such as reducing ordering costs and improving cash flow management.
- π The script also touches on the impact of EOQ on lead time and safety stock, which are crucial for inventory planning.
- π An example of calculating EOQ for a watch store is given, illustrating the process of determining the economic order quantity.
- π The takeaway is that EOQ is a valuable tool for businesses to optimize inventory levels and reduce costs associated with ordering and holding inventory.
Q & A
What is the main topic discussed in the script?
-The main topic discussed in the script is the concept of economic order quantity and its application in inventory management.
What does the term 'economic order quantity' refer to?
-Economic order quantity (EOQ) refers to the ideal quantity of an item to be ordered in order to minimize the total inventory costs, which include ordering costs and holding costs.
What are the factors considered in determining the economic order quantity?
-The factors considered in determining the EOQ include the cost of placing an order, the cost of holding inventory, the demand rate for the item, and the unit cost of the item.
Why is it important to minimize the ordering cost and holding cost?
-Minimizing ordering cost and holding cost is important because it helps businesses to reduce their overall inventory costs and improve their financial performance.
What is the significance of knowing consistent demand in inventory management?
-Knowing consistent demand is significant because it allows businesses to predict the quantity of items needed and plan their orders accordingly, ensuring that they do not run out of stock or hold excess inventory.
How can a business calculate the economic order quantity?
-A business can calculate the EOQ using the EOQ formula, which is \( \text{EOQ} = \sqrt{\frac{2DS}{H}} \), where D is the demand rate, S is the ordering cost per order, and H is the holding cost per unit per year.
What is the impact of not ordering the optimal quantity on a business?
-Not ordering the optimal quantity can lead to higher inventory costs, potential stockouts, and inefficiencies in inventory management.
Can you provide an example of how to apply the EOQ concept in a real-life scenario?
-An example would be a shoe store owner who knows that the consistent demand for a certain brand of shoes is 100 pairs per month. By calculating the EOQ, the owner can determine the optimal quantity to order to minimize costs.
What are some common mistakes businesses make when ordering inventory?
-Some common mistakes include ordering too much or too little inventory, not considering the holding and ordering costs, and not adjusting orders based on changes in demand.
How can a business adjust its ordering strategy based on changes in demand?
-A business can adjust its ordering strategy by continuously monitoring demand patterns and using tools like the EOQ model to calculate the optimal quantity to order as demand changes.
What is the role of technology in modern inventory management?
-Technology plays a crucial role in modern inventory management by providing tools for real-time tracking of inventory levels, demand forecasting, and automated ordering systems that can help businesses maintain optimal inventory levels.
Outlines
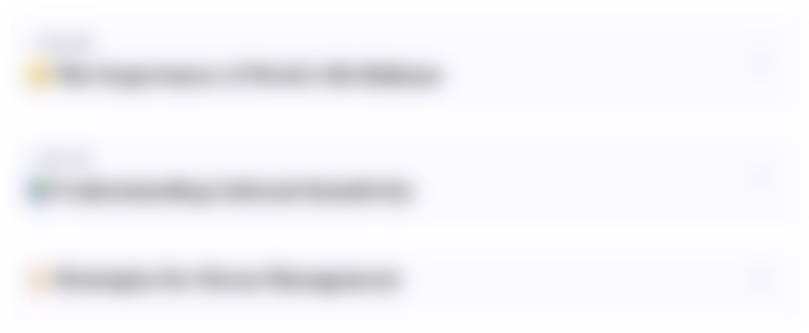
This section is available to paid users only. Please upgrade to access this part.
Upgrade NowMindmap
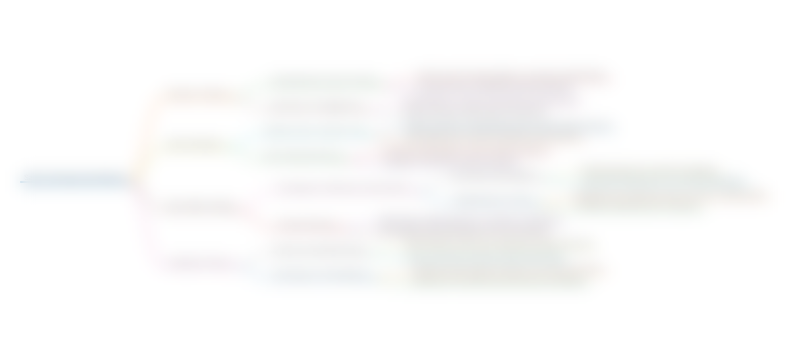
This section is available to paid users only. Please upgrade to access this part.
Upgrade NowKeywords
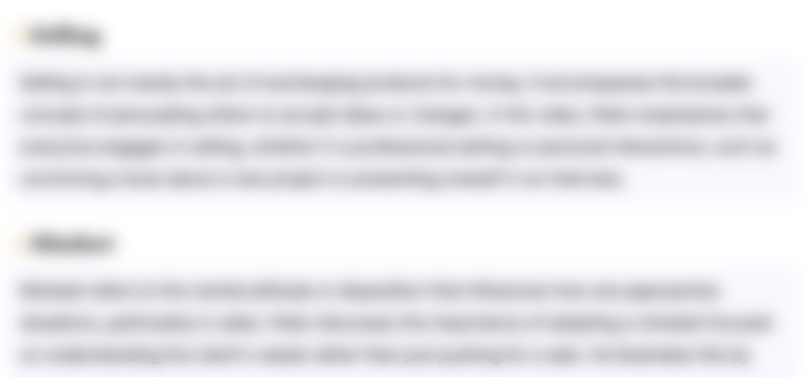
This section is available to paid users only. Please upgrade to access this part.
Upgrade NowHighlights
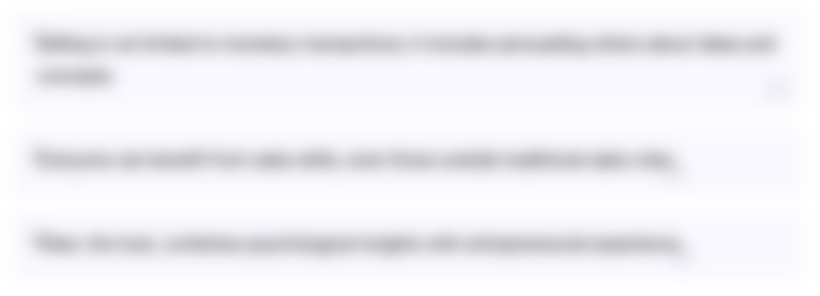
This section is available to paid users only. Please upgrade to access this part.
Upgrade NowTranscripts
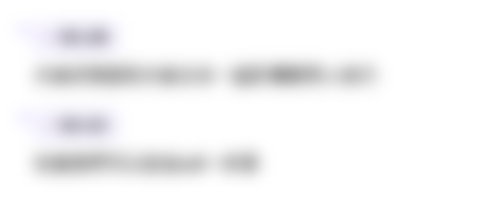
This section is available to paid users only. Please upgrade to access this part.
Upgrade NowBrowse More Related Video

[PRESENTASI] TEKNIK PERSEDIAAN METODE JIT (JUST IN TIME) DAN EOQ (ECONOMIC ORDER QUANTITY)

OM (Practicum/Project) - Economic Order Quantity (EOQ)

Pertemuan 6 : Penentuan Tingkat Persedian (lanjutan)

Model Inventori EOQ Deterministik (Pendahuluan)
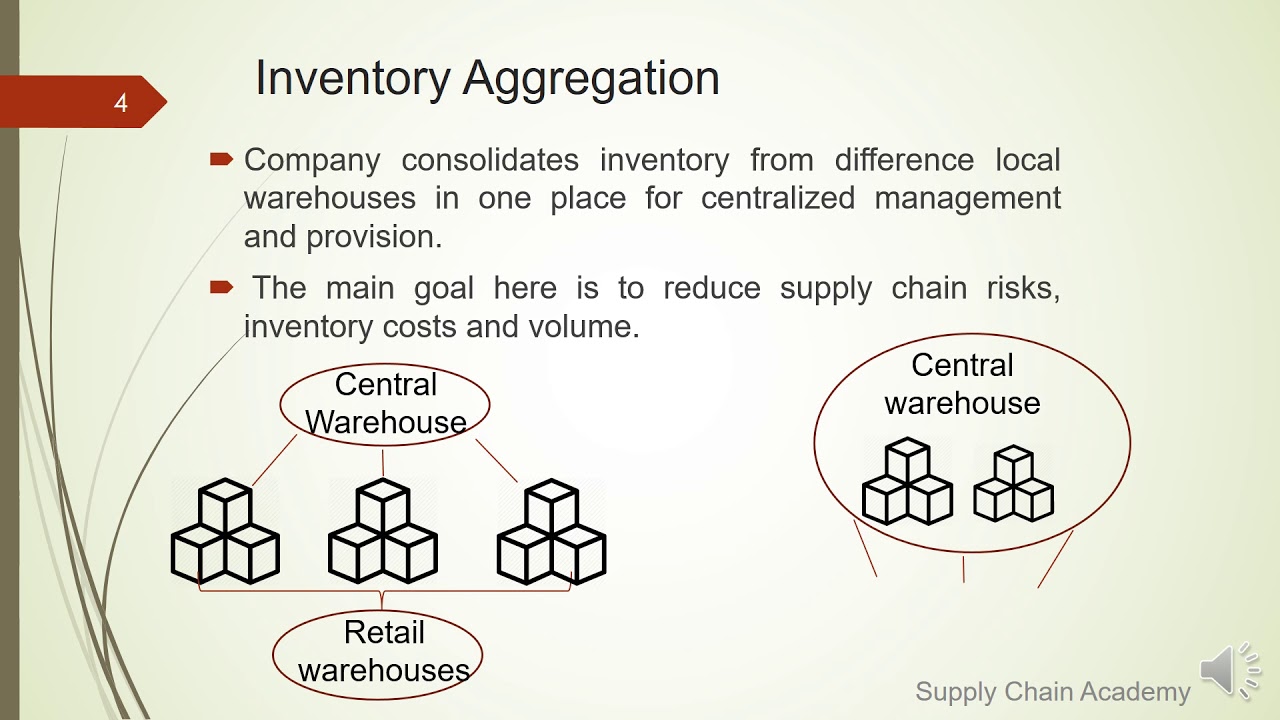
Inventory Management Lesson 2/3 Placement and quantity calculations ENG
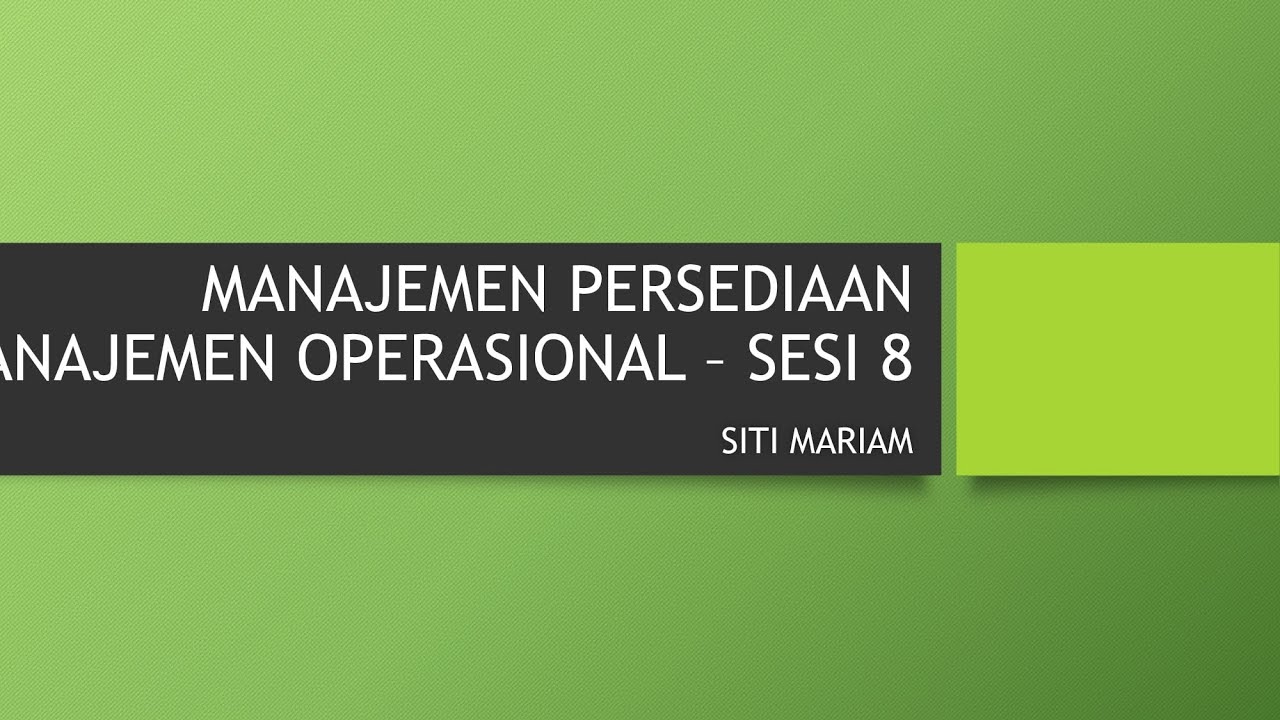
E learning : Manajemen Operasional - Sesi 8, Manajemen Persediaan | by Siti Mariam
5.0 / 5 (0 votes)