Tolerances Explained in CNC Machining (Defining for production)
Summary
TLDRThis episode of 'Mastering Manufacturing' delves deeper into tolerance issues in CNC machining. It addresses common challenges like design for assembly, where parts may not fit due to nominal diameters being the same. It also discusses the impracticality of overly tight tolerances like Β±0.02mm, which can be a nightmare for machinists and costly for customers. The video highlights the importance of focusing on critical dimensions rather than over-tolerancing, and the potential conflict between tight tolerances and surface finish requirements, suggesting masking as a solution.
Takeaways
- π§ The first issue discussed is design for assembly, emphasizing the importance of fitting parts together correctly.
- π A common problem arises when male and female parts have the same nominal diameter, leading to potential fitting issues.
- π Engineers often face challenges when customers request very tight tolerances, such as plus-minus 0.02 millimeters, which can be difficult and costly to achieve.
- π‘ It's suggested to only tolerance critical dimensions that affect assembly or function, rather than applying tight tolerances to the entire part.
- π οΈ The script highlights the potential conflict between surface finish requirements and tight tolerances, especially after processes like anodizing.
- π¨ The example of anodizing type 3 finish shows how tolerances might be affected and advises considering masking off areas with tight tolerances to protect them.
- π The video script emphasizes the need to balance cosmetic requirements with assembly and tolerance needs.
- π¦ An example of an electronics casing needing to fit a PCB inside an aluminum case illustrates assembly requirements.
- π₯ The script addresses the challenges faced by both machinists and customers when very tight tolerances are specified.
- π The video encourages viewers to subscribe for more content and invites feedback on topics of interest.
Q & A
What is the main topic discussed in the video?
-The main topic discussed in the video is the issues that engineers or designers may encounter when dealing with tolerances in manufacturing.
What was covered in the first episode of the series?
-In the first episode, they went over what tolerances are and what makes a tolerance in CNC machining.
What is one of the first issues mentioned in the industry regarding tolerances?
-One of the first issues mentioned is design for assembly, where parts may not fit together as intended due to tolerances.
Why might two parts with the same nominal diameter not fit together?
-Two parts with the same nominal diameter might not fit together if there is no margin for error in the tolerances, leading to both parts being at the maximum size and thus too large to assemble.
What is the significance of the tolerance example given with a diameter of 25 millimeters?
-The example with a 25-millimeter diameter illustrates that without a margin of error, parts are likely not to fit, emphasizing the importance of considering tolerances in design.
What assembly requirement issue is mentioned in the context of electronics casing?
-The issue mentioned is ensuring that an electronics casing can fit a PCB inside, which requires precise tolerances to be maintained.
Why is it challenging for manufacturers to meet an overall tolerance of plus or minus 0.02 millimeter?
-An overall tolerance of plus or minus 0.02 millimeter is very tight, making it difficult and potentially costly to maintain such precision across all features of a part.
What is the recommendation for tolerancing parts that are critical for assembly?
-The recommendation is to only tolerance the critical dimensions that are necessary for assembly or function, rather than over tolerancing the entire part.
What conflict might arise between surface finish requirements and tight tolerances?
-A conflict might arise because processes like anodizing can affect the tolerances of a part, even if it's assumed that tolerances remain the same before and after the process.
Why might masking off certain areas of a part be a good idea?
-Masking off areas where tight tolerances are required can prevent these tolerances from being impacted by surface finish operations, ensuring that they remain precise.
What does the video suggest doing if you want more information on the topic?
-The video suggests subscribing to the channel for notifications on new videos and providing feedback if you want to hear more on this or other topics discussed in previous videos.
Outlines
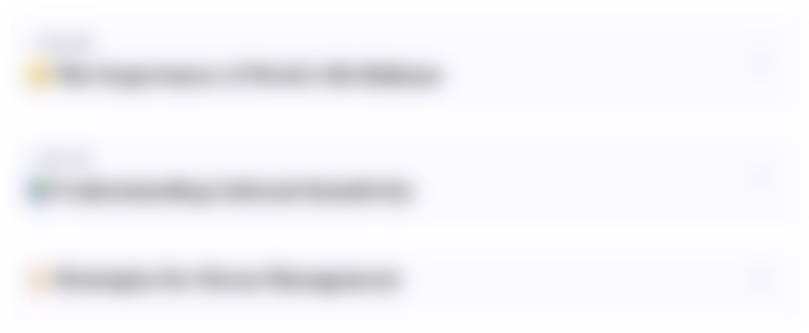
This section is available to paid users only. Please upgrade to access this part.
Upgrade NowMindmap
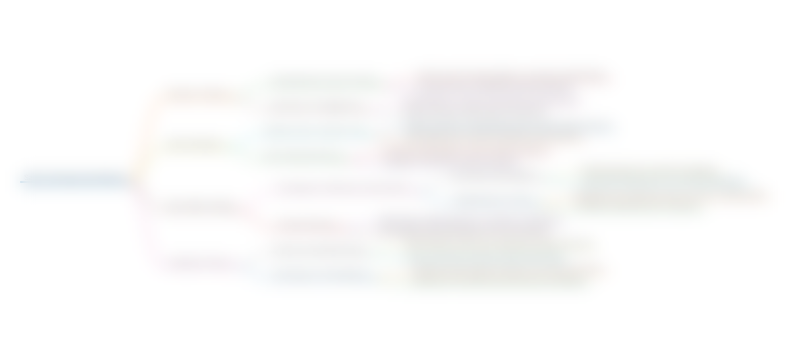
This section is available to paid users only. Please upgrade to access this part.
Upgrade NowKeywords
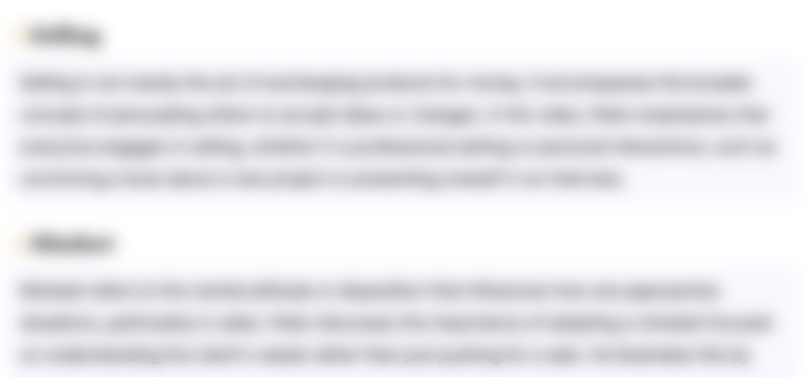
This section is available to paid users only. Please upgrade to access this part.
Upgrade NowHighlights
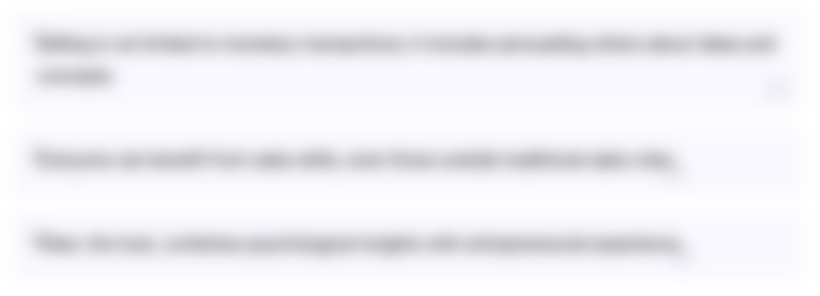
This section is available to paid users only. Please upgrade to access this part.
Upgrade NowTranscripts
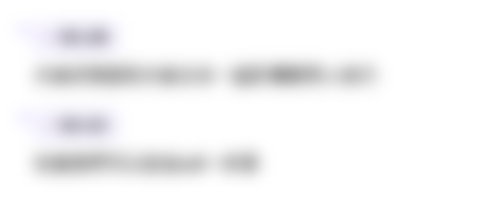
This section is available to paid users only. Please upgrade to access this part.
Upgrade NowBrowse More Related Video

HEAVY DUTY LATHES. Most Mesmerizing Collection of CNC Machine Processes.

CNC Lathe Basics: How CNC Lathe Turning Works
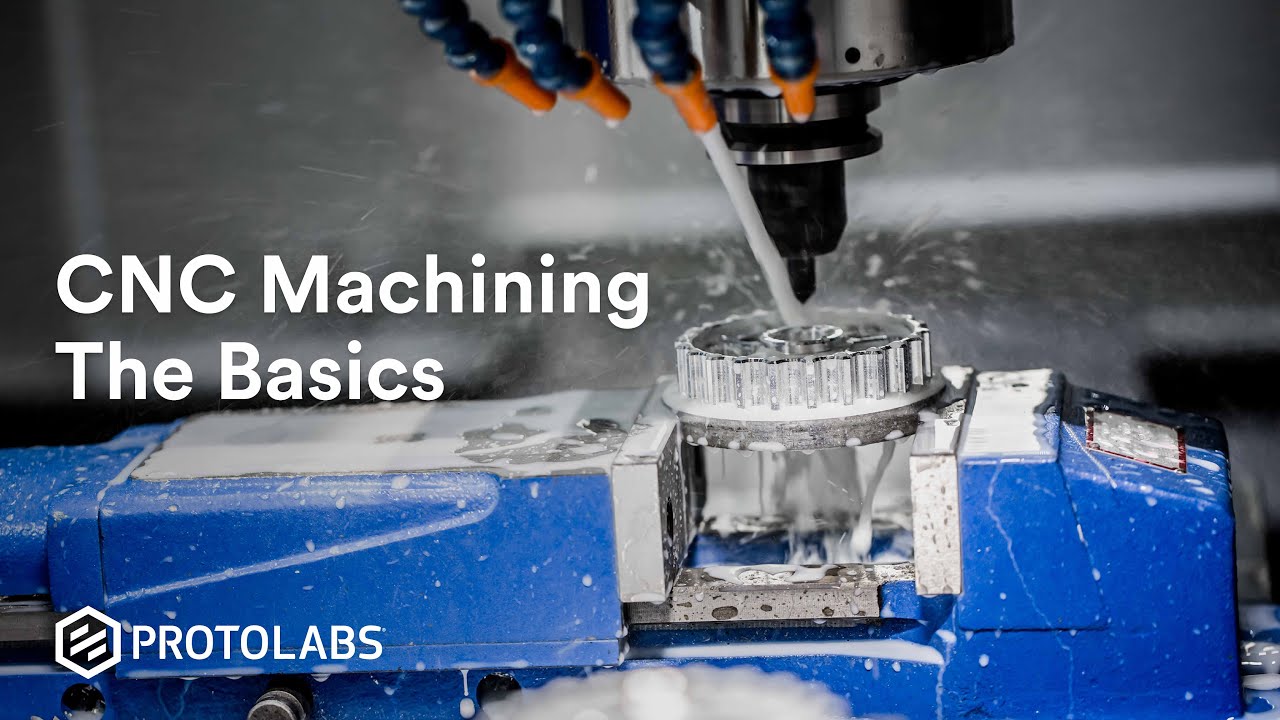
CNC machining - What is it and How Does it Work? (Must Know Basics)
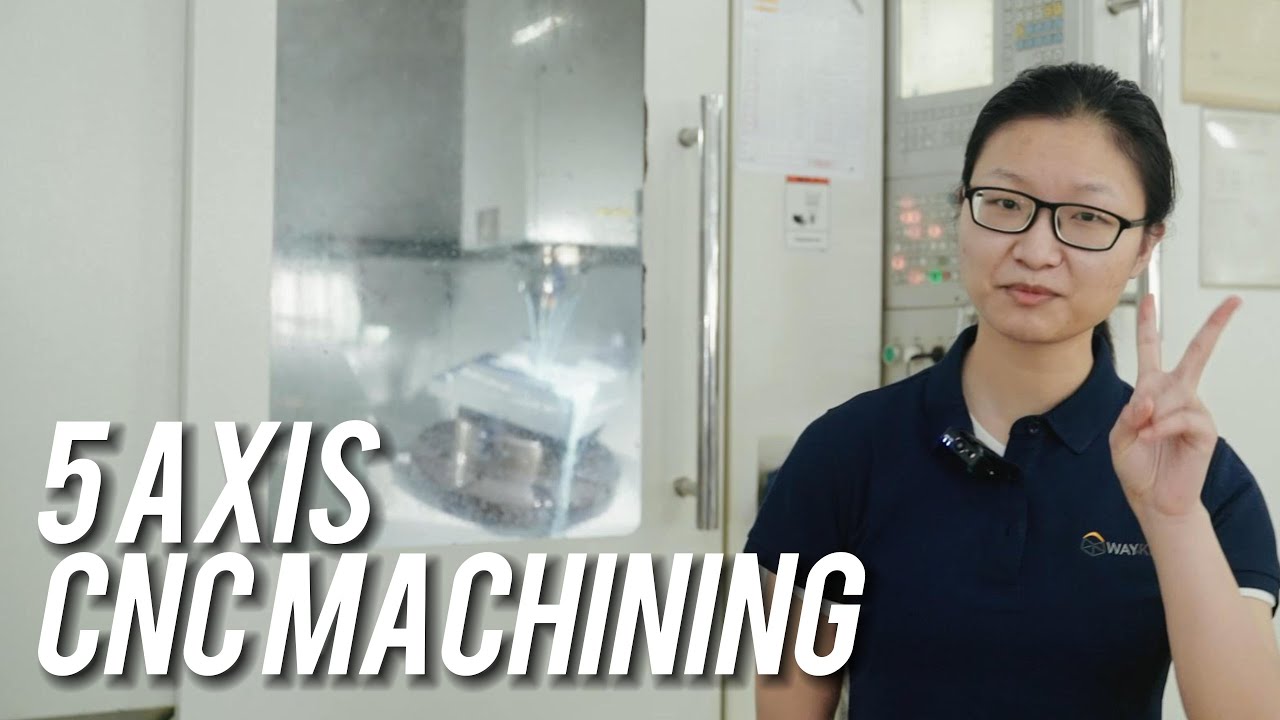
5 Axis CNC Machining For Your Parts | WayKen Rapid Manufacturing
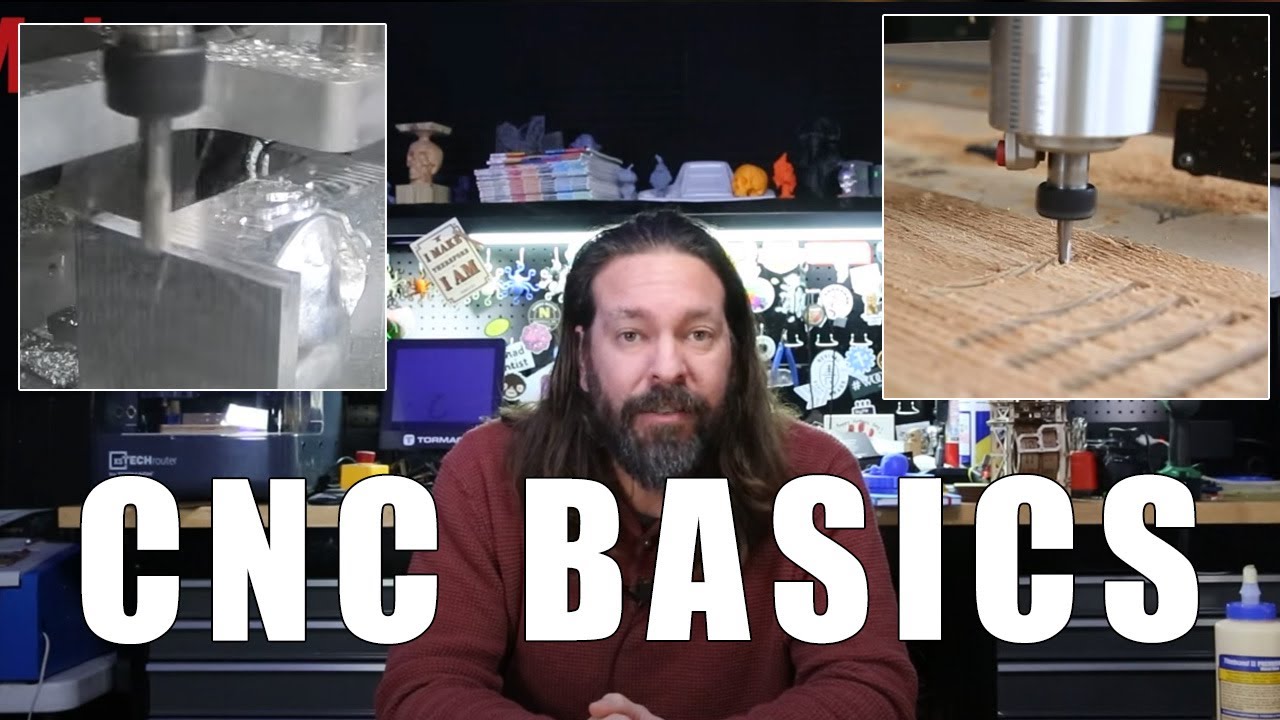
CNC Basics - Everything a Beginner Needs To Know
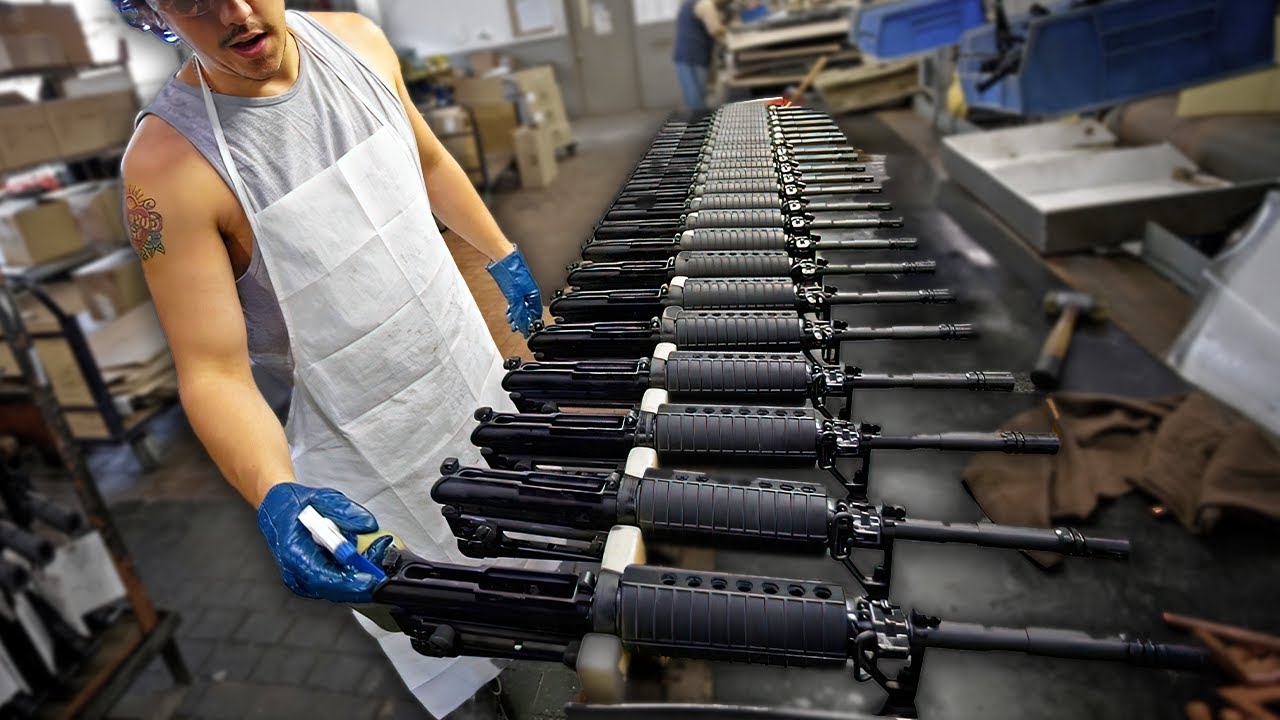
How It's Made: Guns
5.0 / 5 (0 votes)