AWAL BELAJAR Ngobrol Santai Tentang PLC (Programmable Logic Controller)
Summary
TLDRIn this video, Eko Aris from the Mechatronics program at Universitas Sanata Dharma introduces the importance of Programmable Logic Controllers (PLCs) in industrial automation. He discusses how PLCs have replaced older, cumbersome relay-based control systems, improving efficiency and adaptability in automation processes. The video covers various types of PLCs, their components, and the essential role of programming in controlling automation systems. Aris highlights the importance of mastering PLCs for mechatronics students, especially in the context of Industry 4.0, where automation plays a central role in modern industries.
Takeaways
- 😀 PLCs (Programmable Logic Controllers) are the 'brain' of modern automation systems, controlling machines and processes in industries like food and beverage.
- 😀 Before PLCs, industries relied on relay-based control systems, which were cumbersome, required large spaces, and involved extensive wiring.
- 😀 Relay control systems were difficult to modify and repair, leading to long downtimes and complicated maintenance.
- 😀 PLCs replace traditional relay control systems by integrating components like timers and counters, making them more efficient and flexible.
- 😀 The introduction of PLCs in the 1970s allowed industries to streamline their automation processes, making system changes faster and more cost-effective.
- 😀 PLCs reduce the need for large amounts of wiring and external components, offering a compact and easily programmable solution for industrial control.
- 😀 Modern PLCs come in different types, including Smart PLCs for simple tasks, Compact PLCs for medium-scale applications, and Modular PLCs for complex, large-scale systems.
- 😀 PLCs can handle both digital and analog inputs/outputs, providing a flexible platform for various industrial needs.
- 😀 Programming PLCs involves using specialized software like Step 7 for Siemens PLCs or TIA Portal for the latest Siemens models.
- 😀 Understanding PLCs is crucial for students and professionals in mechatronics as they are central to the development and operation of automation systems in industries.
- 😀 PLCs improve the efficiency of industrial automation systems, enabling industries to adapt quickly to changing production requirements and technological advancements.
Q & A
What is the main topic of the video transcript?
-The main topic is the use of Programmable Logic Controllers (PLCs) in automation systems, specifically for controlling food and beverage processing in a mechatronics laboratory.
Why are PLCs important in automation systems?
-PLCs are important because they serve as the 'brain' of an automation system, replacing traditional methods like relays, timers, and counters with more compact, efficient, and programmable solutions.
What were the challenges with using relays in industrial automation before PLCs?
-Relays required significant space, were time-consuming to develop and troubleshoot, and the system logic was complex and difficult to change. Moreover, if something went wrong, it would take longer to fix due to the large number of cables and connections.
How does the use of PLCs improve the efficiency of automation systems?
-PLCs reduce the need for physical relays, timers, and complex wiring. They simplify system control by allowing logic to be programmed directly, making it easier to adjust and maintain systems.
What are the components of a PLC system?
-A PLC system includes inputs (such as sensors and buttons), logic (programming that processes input data), and outputs (like motors and lights that perform actions based on the logic).
What is the difference between digital and analog inputs in a PLC?
-Digital inputs receive binary signals (on/off), while analog inputs can receive a range of continuous values, allowing for more precise control in some applications.
What role does the Human-Machine Interface (HMI) play in modern PLC systems?
-The HMI allows operators to monitor and control the system through a graphical interface, replacing traditional physical buttons and lights with a digital interface for ease of use and space efficiency.
How do modular PLCs differ from compact PLCs?
-Modular PLCs allow for the addition of extra input/output units as needed, making them suitable for larger, more complex systems. Compact PLCs integrate both the CPU and input/output units into one unit, making them more compact and suitable for simpler systems.
What are the advantages of using Siemens S7-300 modular PLCs over compact PLCs?
-Siemens S7-300 modular PLCs offer the flexibility to expand the system with additional input/output units, making them ideal for larger and more complex automation needs.
How is PLC programming typically done, and what tools are needed?
-PLCs are programmed using specialized software. Simple PLCs may allow programming via physical buttons, while more complex systems require a computer with programming software like Siemens Step 7 or TIA Portal to create and upload programs to the PLC.
Outlines
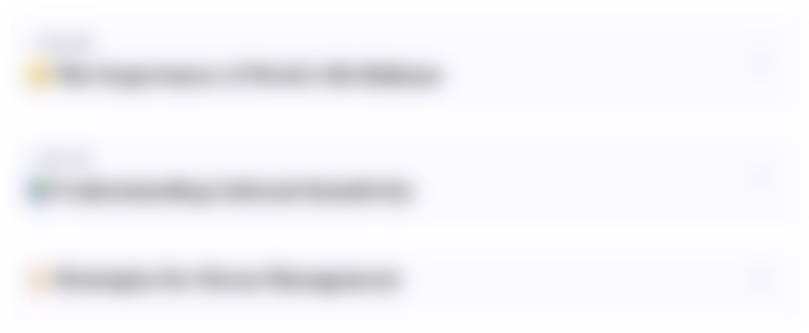
This section is available to paid users only. Please upgrade to access this part.
Upgrade NowMindmap
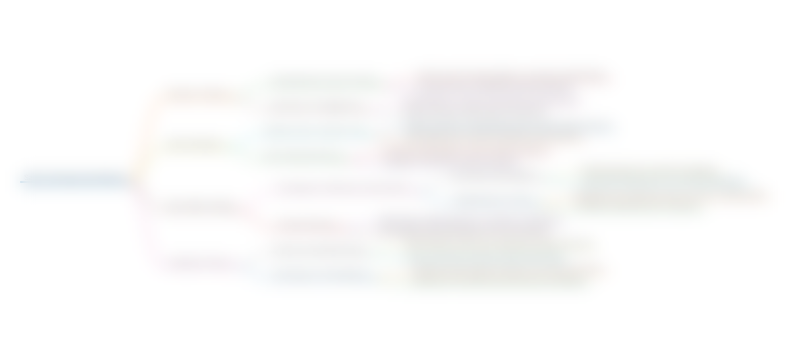
This section is available to paid users only. Please upgrade to access this part.
Upgrade NowKeywords
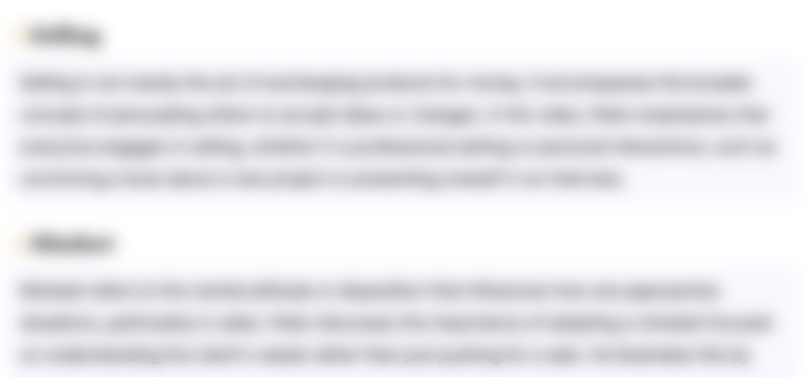
This section is available to paid users only. Please upgrade to access this part.
Upgrade NowHighlights
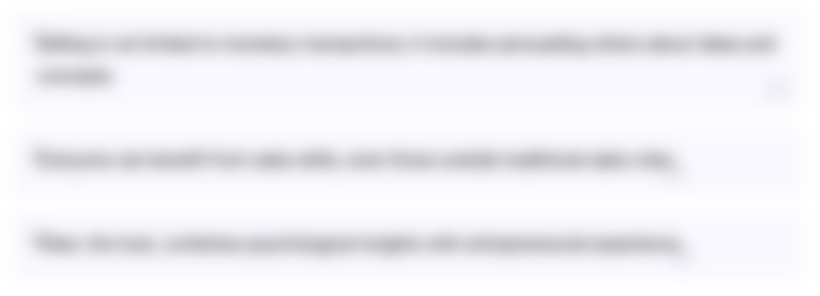
This section is available to paid users only. Please upgrade to access this part.
Upgrade NowTranscripts
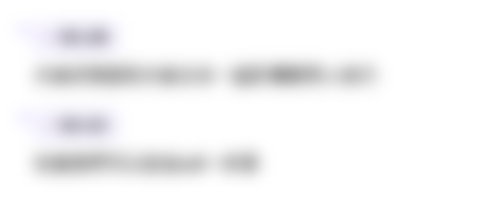
This section is available to paid users only. Please upgrade to access this part.
Upgrade NowBrowse More Related Video
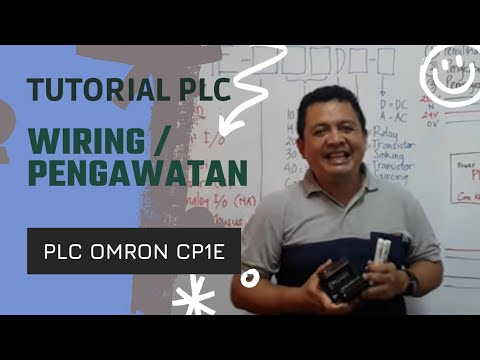
WIRING CP1E Panduan Praktis Basic Wiring PLC OMRON CP1E untuk Pemula!
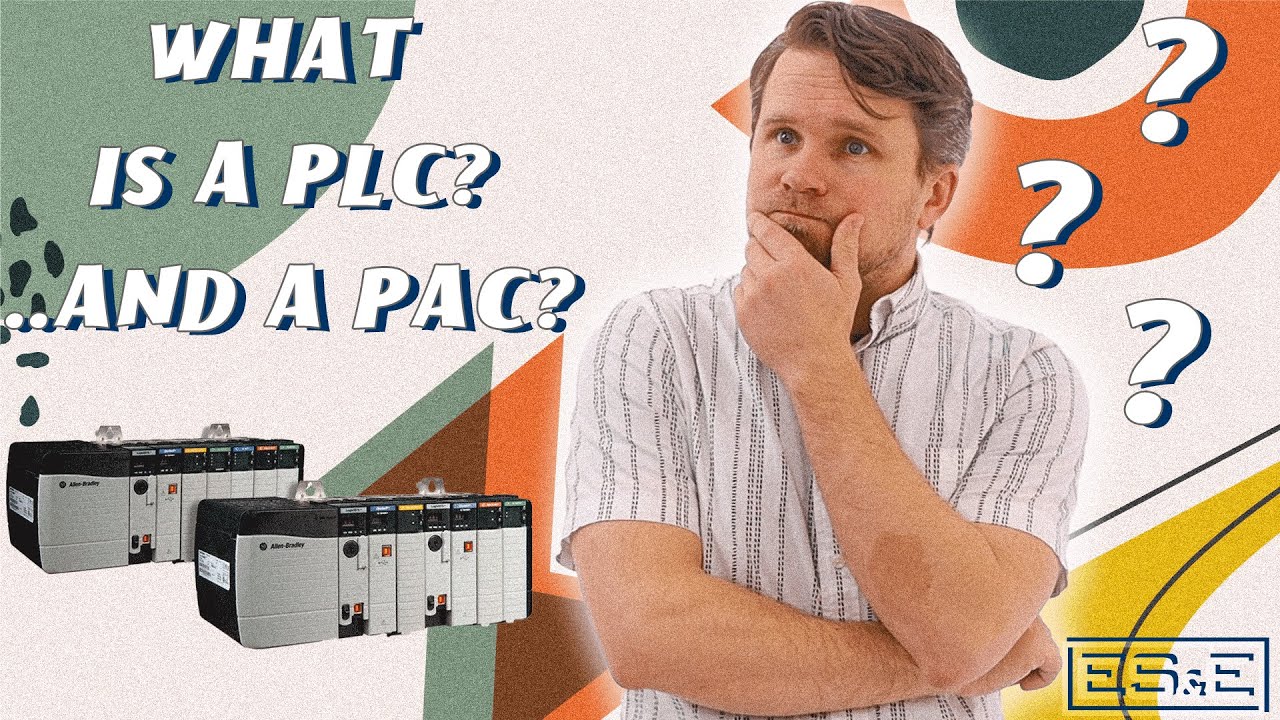
What is a PLC?...and a PAC?!?
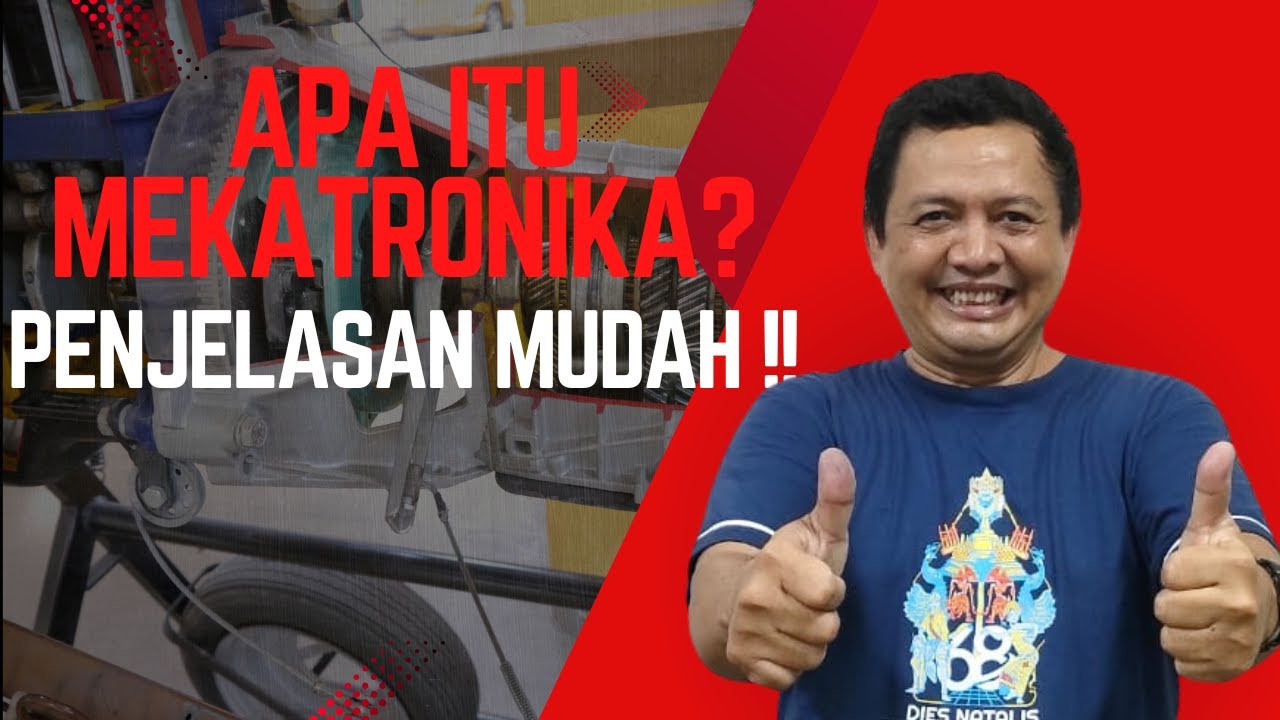
What is Mechatronics? Let's Get to Know the Basic Components and How They Work! Simple Tutorial E...
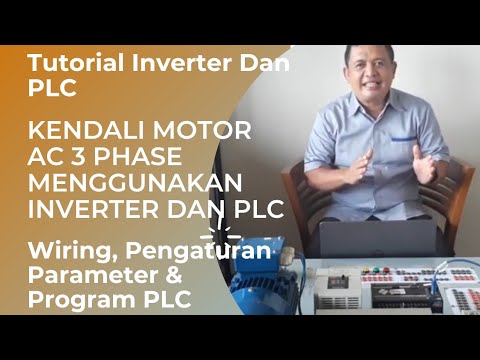
7.1 Menaklukkan Kendali Motor AC 3 Fase: Kisah Seru dengan Inverter Panasonic VF0 dan PLC Omron CP1E

Introduction to Industrial Automation | Introduction and History

Electrical Review - PLC Basics Part 1
5.0 / 5 (0 votes)