What is a PLC?...and a PAC?!?
Summary
TLDRIn this video, Henry explains the evolution of industrial automation, starting with relays and progressing to Programmable Logic Controllers (PLCs) and Programmable Automation Controllers (PACs). PLCs are robust, reliable computers designed for industrial automation, capable of controlling equipment like motors and pumps. Unlike home computers, they are built to withstand harsh conditions without crashing. PACs, an advancement over PLCs, offer greater flexibility, scalability, and networkability, making them suitable for complex and large-scale industrial applications. The video highlights how these technologies have transformed the industrial landscape, increasing efficiency and reliability.
Takeaways
- 🤖 A PLC (Programmable Logic Controller) is an industrial computer designed to control automation equipment like motors, pumps, and fans.
- 🛡️ PLCs are built to be more robust and reliable than standard computers, capable of withstanding harsh conditions without crashing.
- 🏭 The reliability of PLCs is crucial for manufacturers as machine downtime can lead to significant financial losses, especially in industries dealing with perishable goods.
- 💻 Unlike home computers, PLCs are not easily replaced or rebooted without impacting production lines, emphasizing the need for their high reliability.
- 🚀 The evolution from relays to PLCs has significantly reduced the need for physical wiring and increased the efficiency of automation systems.
- 🌐 PACs (Programmable Automation Controllers) are an advancement over PLCs, offering enhanced flexibility, networkability, and scalability.
- 💡 PACs utilize modern processors and electronics, allowing for more features and capabilities compared to traditional PLCs.
- 🔌 The spread of communication technology and the Industrial Internet of Things (IIoT) enables PACs to connect and control various network devices within a factory.
- 🔄 PACs are designed for scalability, with modular hardware that can be expanded as needed to meet the growing demands of applications.
- 🔗 The flexibility of PACs allows for a variety of input/output options and easy integration with other devices like sensors, actuators, and HMIs.
- 🌟 In complex industrial processes, multiple PACs can work together in a distributed system to solve large-scale automation challenges.
Q & A
What is a PLC and what does it stand for?
-A PLC is a Programmable Logic Controller, which is a specialized industrial computer designed to control various types of automation equipment such as motors, pumps, and fans.
Why can't a standard home computer be used as a PLC?
-Standard home computers are not designed to be as robust and reliable as PLCs. They can crash or freeze, which is unacceptable in industrial settings where continuous operation is critical for production.
How do PLCs handle environmental factors like high temperatures?
-PLCs are designed to withstand harsh conditions such as high temperatures and long run spans without crashing or failing, ensuring continuous operation in industrial environments.
What is the impact of a PLC failure on a manufacturing line?
-A PLC failure can halt the manufacturing process, leading to financial losses as production stops. This can be particularly costly in industries where products have a limited lifespan or are perishable, like in food and beverage manufacturing.
What is a PAC and how does it differ from a PLC?
-A PAC stands for Programmable Automation Controller. It differs from a PLC by offering enhanced flexibility, networkability, and scalability, often utilizing high-performance processors and modern electronics.
How has technology evolved from PLCs to PACs?
-Technology has evolved to include more advanced features in PACs, such as better communication capabilities, modular hardware design for scalability, and the ability to handle both small and large applications with ease.
What is the significance of the Industrial Internet of Things (IIoT) in relation to PACs?
-The IIoT allows PACs to reliably communicate and control many different network devices within a factory setting, enhancing the connectivity and efficiency of industrial operations.
How does the modular hardware design of PACs contribute to their flexibility?
-The modular hardware design of PACs allows for the addition of modules as needed, providing the ability to adapt to evolving requirements of an application and offering a variety of input and output options.
Can PACs handle very large and complex processes that are too much for one unit?
-Yes, PACs can work together in a large distributed system, combining their capabilities to solve complex problems that are beyond the scope of a single unit.
How has the transition from relays to PLCs and then to PACs impacted the efficiency of industrial processes?
-The transition has led to a decrease in the amount of wiring, increased scalability, and improved ease of operation for engineers and technicians, allowing for more efficient and capable industrial processes.
Outlines
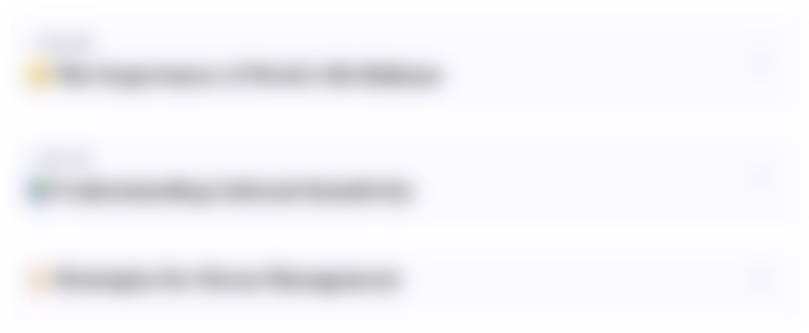
This section is available to paid users only. Please upgrade to access this part.
Upgrade NowMindmap
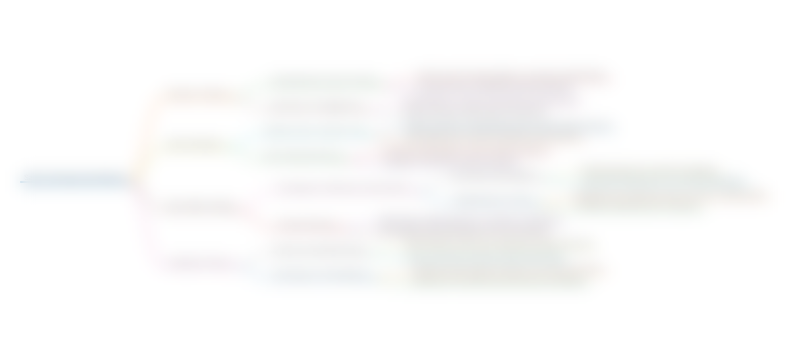
This section is available to paid users only. Please upgrade to access this part.
Upgrade NowKeywords
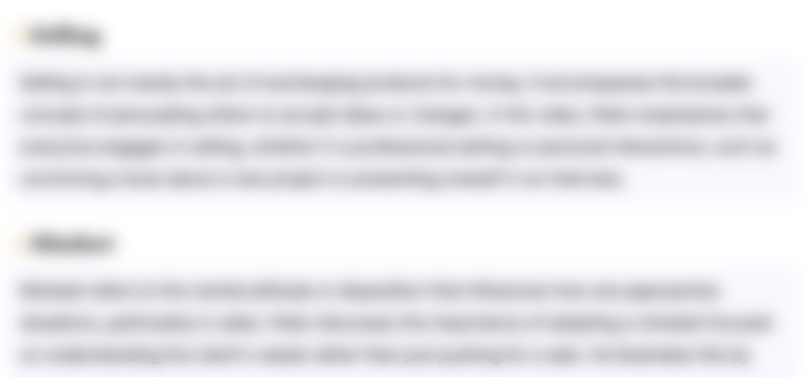
This section is available to paid users only. Please upgrade to access this part.
Upgrade NowHighlights
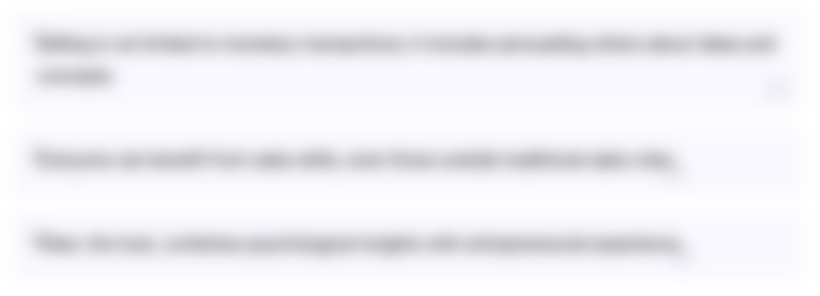
This section is available to paid users only. Please upgrade to access this part.
Upgrade NowTranscripts
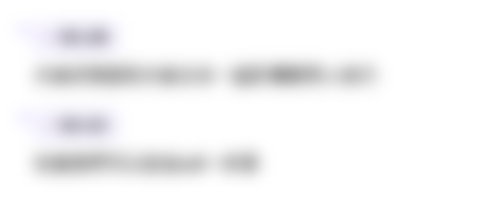
This section is available to paid users only. Please upgrade to access this part.
Upgrade NowBrowse More Related Video
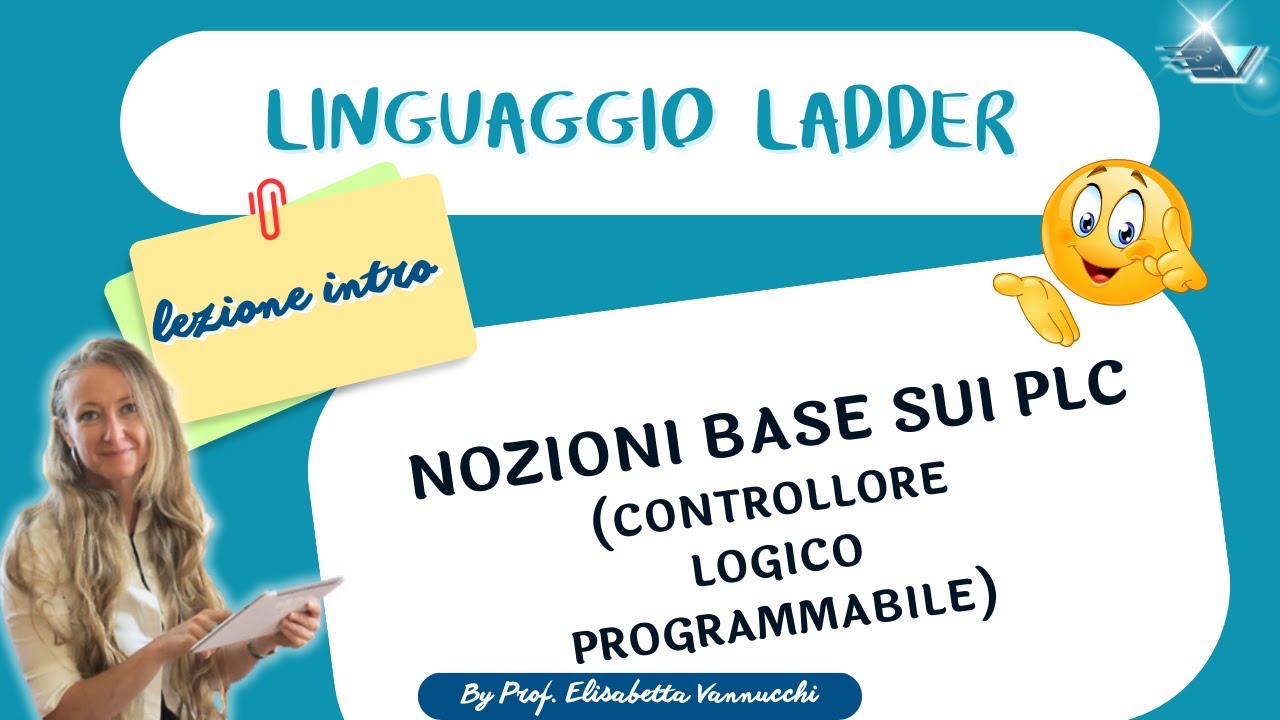
Nozioni base sui PLC ( Controllore Logico Programmabile)
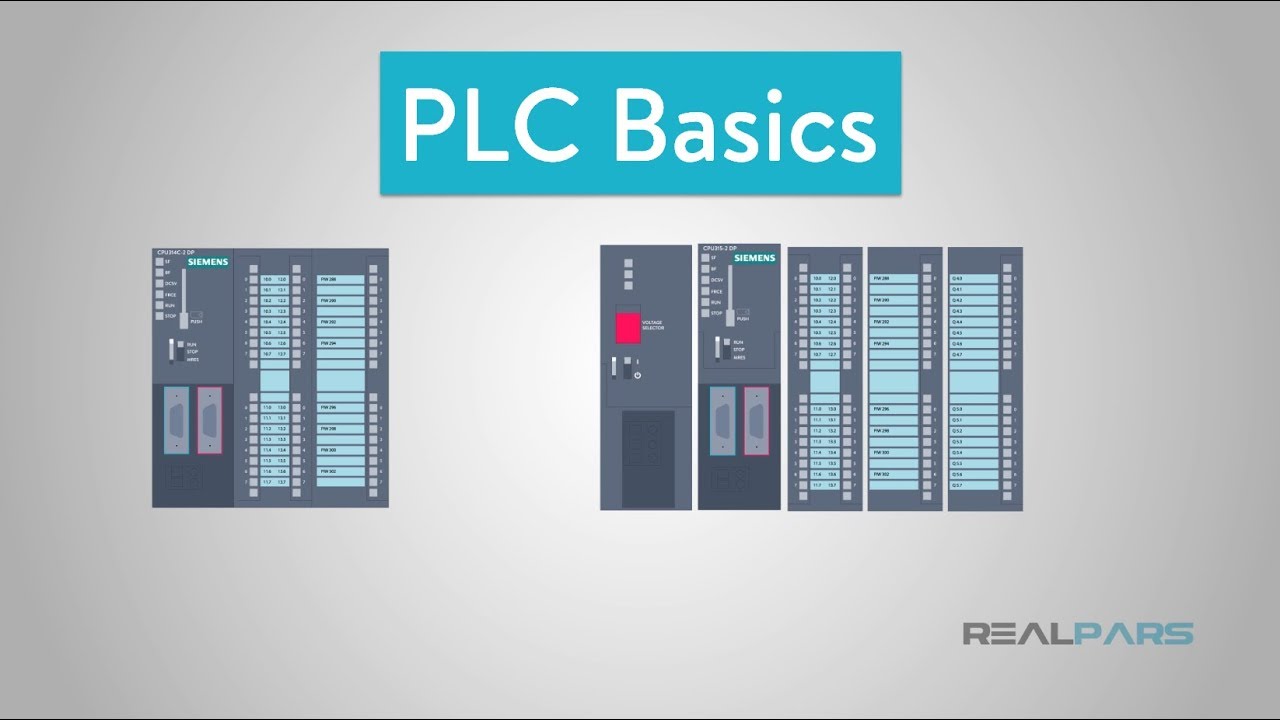
PLC Basics | Programmable Logic Controller

Introduction to Industrial Automation | Introduction and History

Electrical Review - PLC Basics Part 1

AWAL BELAJAR Ngobrol Santai Tentang PLC (Programmable Logic Controller)
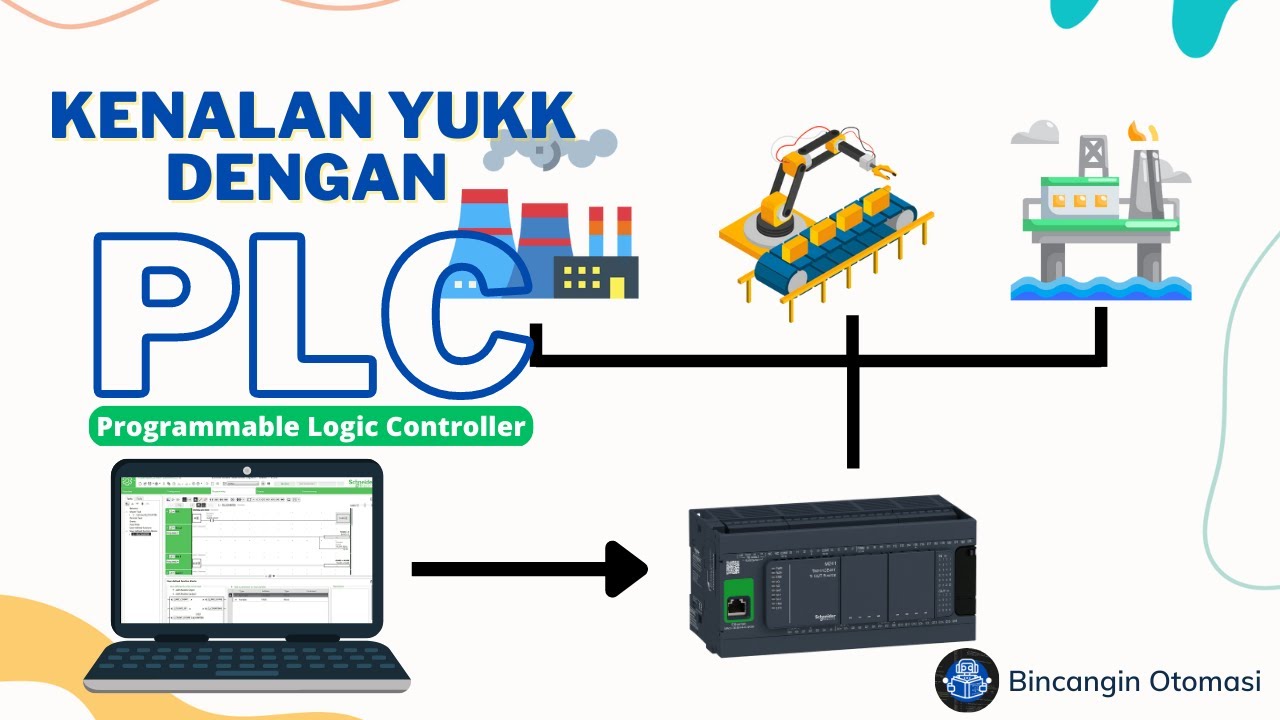
Belajar PLC | Pengenalan Programmable Logic Controller #1
5.0 / 5 (0 votes)