4.2 Manufacturing of Crystalline Silicon
Summary
TLDRThis video explains the production of various types of silicon, starting with metallurgical silicon made from quartzite, followed by the production of polysilicon using chemical vapor deposition. It covers the creation of monocrystalline and multicrystalline ingots through methods like the Czochralski and float-zone processes, as well as silicon casting for multicrystalline ingots. The video also discusses wafer production, including sawing and the silicon ribbon approach, which eliminates kerf loss. The overall process shows how silicon is transformed into high-quality materials for use in solar cells.
Takeaways
- 😀 Metallurgical silicon is produced from quartzite, a rock of pure silicon oxide, using a submerged electrode arc furnace at 1900°C.
- 😀 The carbon source (coal, coke, and wood chips) reacts with silicon oxide to remove oxygen, forming molten silicon and carbon monoxide.
- 😀 70% of metallurgical silicon is used in the aluminum casting industry, while 30% is used in chemical products like silicones.
- 😀 Only around 1% of metallurgical silicon is used for making electronic-grade silicon, which is further purified into polysilicon.
- 😀 Polysilicon is produced from metallurgical silicon by reacting it with hydrogen chloride to form trichlorosilane, which is then distilled for purity.
- 😀 The purified trichlorosilane is deposited on rods using chemical vapor deposition (CVD) at temperatures between 850-1050°C.
- 😀 The Siemens process for polysilicon production consumes a lot of energy, while fluidized bed reactors (FBR) are more energy-efficient.
- 😀 Polycrystalline silicon can have a purity of up to 99.9999%, with just one impurity atom per million silicon atoms.
- 😀 Monocrystalline silicon ingots are produced using the Czochralski method, where a seed crystal is dipped into molten silicon to grow a single crystal ingot.
- 😀 The float-zone method produces monocrystalline silicon ingots with extremely low impurity densities by melting polycrystalline rods using radio-frequency heating.
- 😀 Multicrystalline silicon ingots are made by casting molten silicon into a cubic-shaped crucible, a process known as silicon casting or directional solidification.
- 😀 Wafers are typically made by sawing monocrystalline or multicrystalline silicon ingots, though this results in kerf loss (wasted silicon).
- 😀 The silicon ribbon method eliminates kerf loss by pulling silicon from a molten bath on a string, creating a continuous sheet that is then cut into wafers.
- 😀 Silicon ribbon produces lower electronic quality than monocrystalline silicon but avoids the kerf loss problem from sawing ingots.
- 😀 In summary, silicon for solar cells is produced from quartzite, purified into metallurgical and polysilicon, and processed into wafers using different methods, including sawing and ribbon techniques.
Q & A
What is metallurgical silicon, and how is it produced?
-Metallurgical silicon is the lowest quality form of silicon, produced by heating quartzite (a rock made of silicon oxide) in a submerged electrode arc furnace. The silicon oxide reacts with carbon at high temperatures, resulting in molten silicon and carbon monoxide, with a purity of about 98-99%.
What is the role of carbon in the production of metallurgical silicon?
-Carbon, sourced from materials like coal, coke, and wood chips, reacts with the silicon oxide in quartzite during the heating process. This reaction removes oxygen from the silicon oxide, leaving behind molten silicon.
How is polysilicon created from metallurgical silicon?
-Polysilicon is made by reacting metallurgical silicon with hydrogen chloride in a reactor at elevated temperatures. This forms trichlorosilane gas, which is distilled and used in chemical vapor deposition (CVD) to grow pure silicon rods.
What is the Siemens process, and how does it relate to polysilicon production?
-The Siemens process is a method for producing polysilicon by using chemical vapor deposition (CVD) of trichlorosilane onto rods at high temperatures. This energy-intensive process results in the growth of highly purified silicon material.
What are the advantages of the fluidized bed reactor (FBR) method over the Siemens process?
-The FBR method operates at lower temperatures and consumes much less energy compared to the Siemens process while still producing high-purity polysilicon.
What is the float-zone process for producing monocrystalline silicon, and how does it differ from the Czochralski method?
-The float-zone process involves heating a polycrystalline silicon rod with a radiofrequency coil, melting part of the rod, and using a seed crystal to grow a single-crystal ingot. It avoids contact with quartz crucibles, reducing oxygen contamination, unlike the Czochralski method, where the silicon melt is in contact with a quartz crucible.
Why is the Czochralski process significant in the production of monocrystalline silicon?
-The Czochralski process is significant because it allows for the controlled growth of large, high-quality single-crystal silicon ingots by precisely controlling the temperature, pulling speed, and rotation of the seed crystal.
What is the main disadvantage of the sawing process in wafer production?
-The main disadvantage of the sawing process is 'kerf loss,' which refers to the silicon material lost due to the thickness of the saw wire. This can result in significant material wastage, particularly when cutting wafers as thin as 150 to 200 microns.
How does the silicon ribbon method for wafer production eliminate kerf loss?
-In the silicon ribbon method, a string is pulled from a molten silicon bath, and the silicon solidifies onto the string as a continuous sheet. This method eliminates the need for sawing, thus avoiding kerf loss.
What are the purity levels of monocrystalline silicon compared to multicrystalline silicon?
-Monocrystalline silicon typically has a higher purity level, often over 99.999%, compared to multicrystalline silicon, which generally has lower purity due to the presence of multiple small crystalline grains.
Outlines
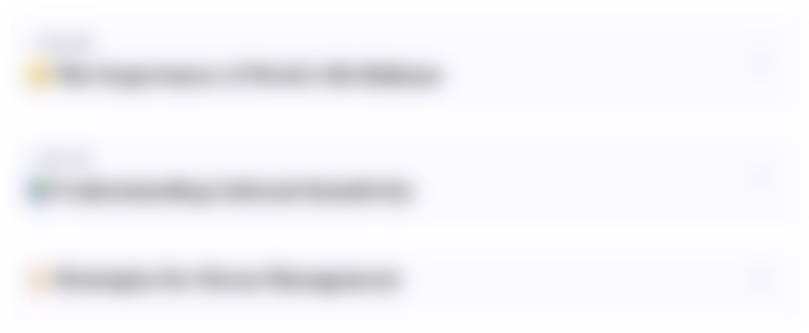
This section is available to paid users only. Please upgrade to access this part.
Upgrade NowMindmap
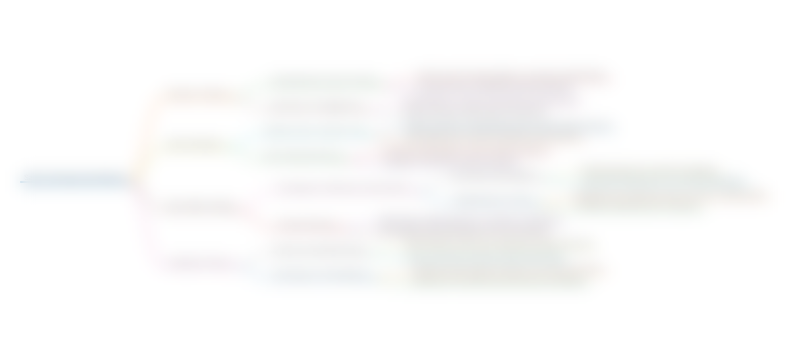
This section is available to paid users only. Please upgrade to access this part.
Upgrade NowKeywords
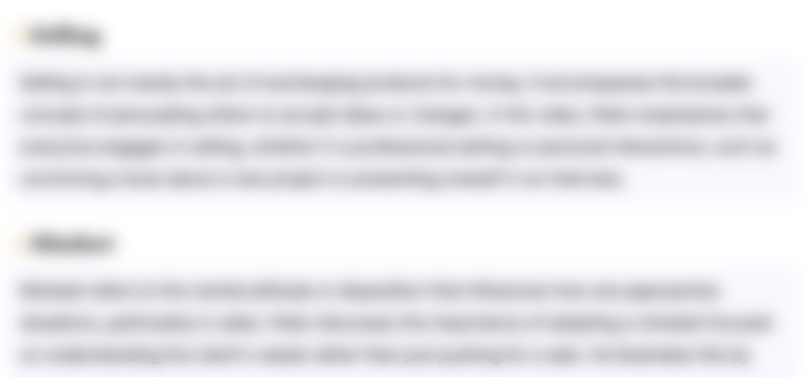
This section is available to paid users only. Please upgrade to access this part.
Upgrade NowHighlights
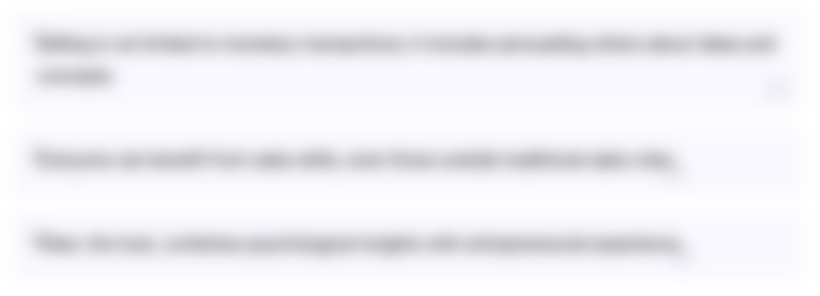
This section is available to paid users only. Please upgrade to access this part.
Upgrade NowTranscripts
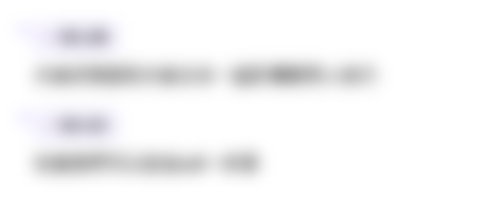
This section is available to paid users only. Please upgrade to access this part.
Upgrade NowBrowse More Related Video
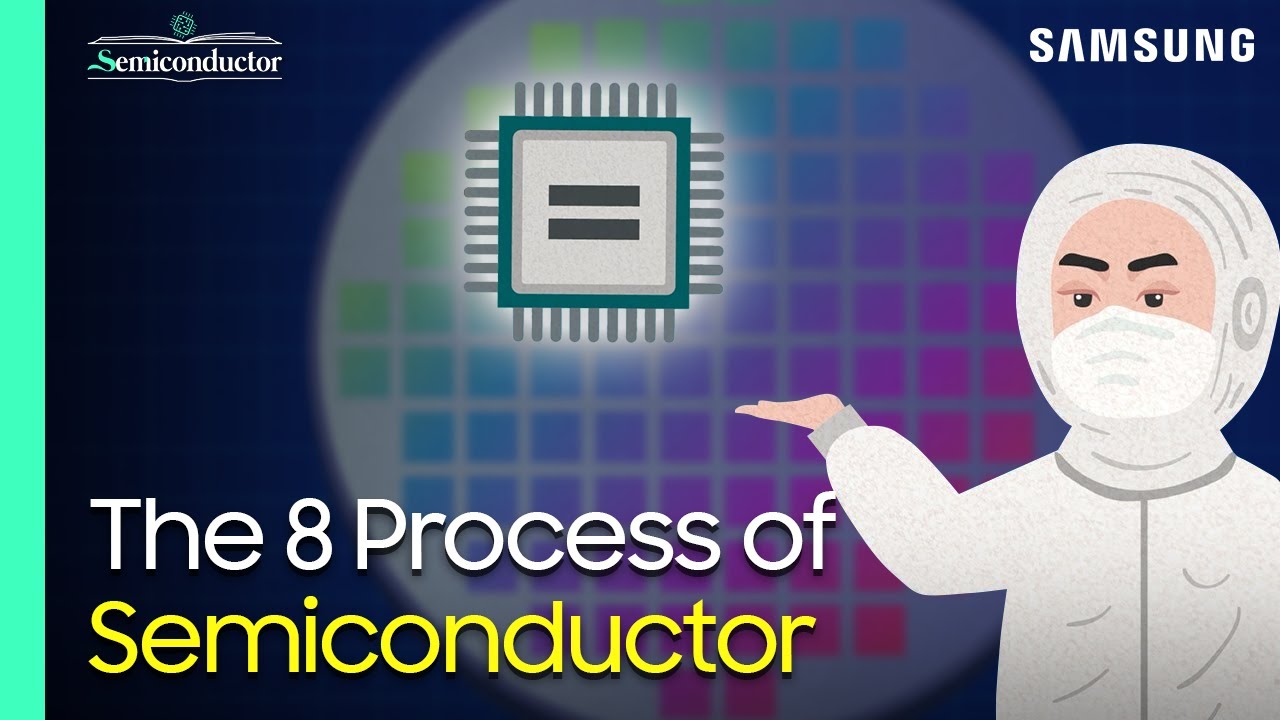
‘Semiconductor Manufacturing Process’ Explained | 'All About Semiconductor' by Samsung Semiconductor
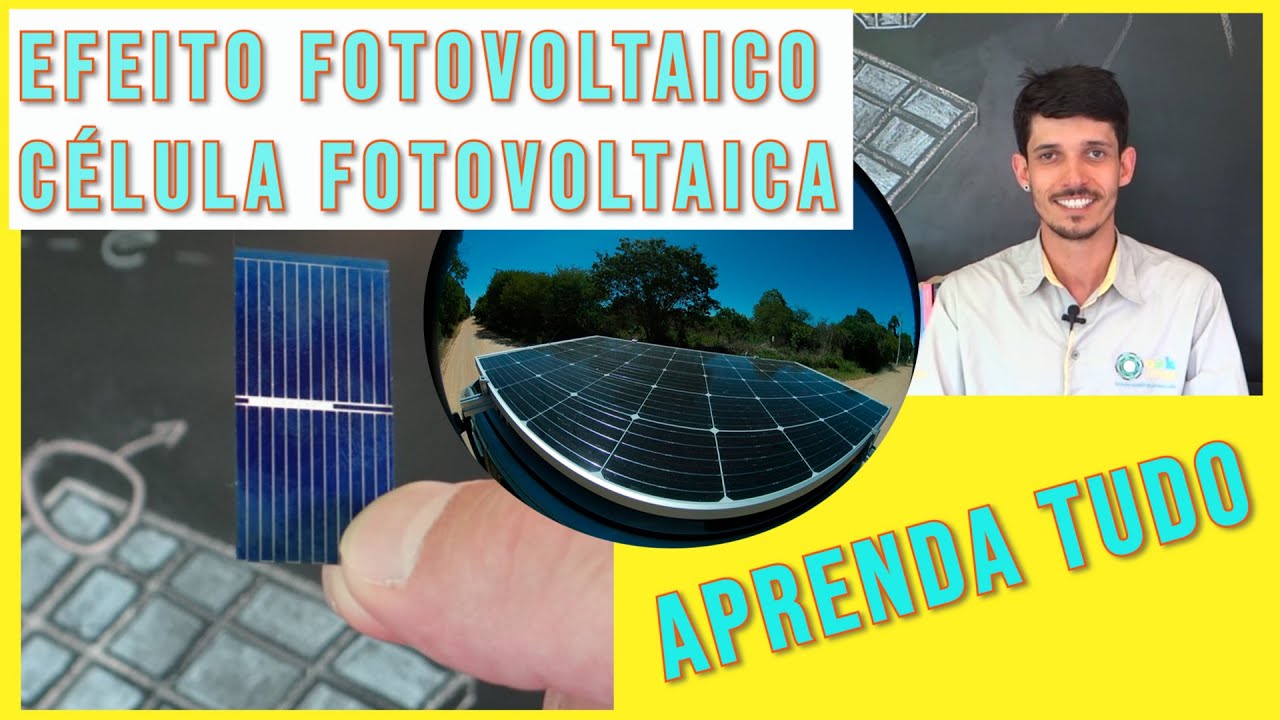
O que é efeito fotovoltaico e como funciona uma célula fotovoltaica
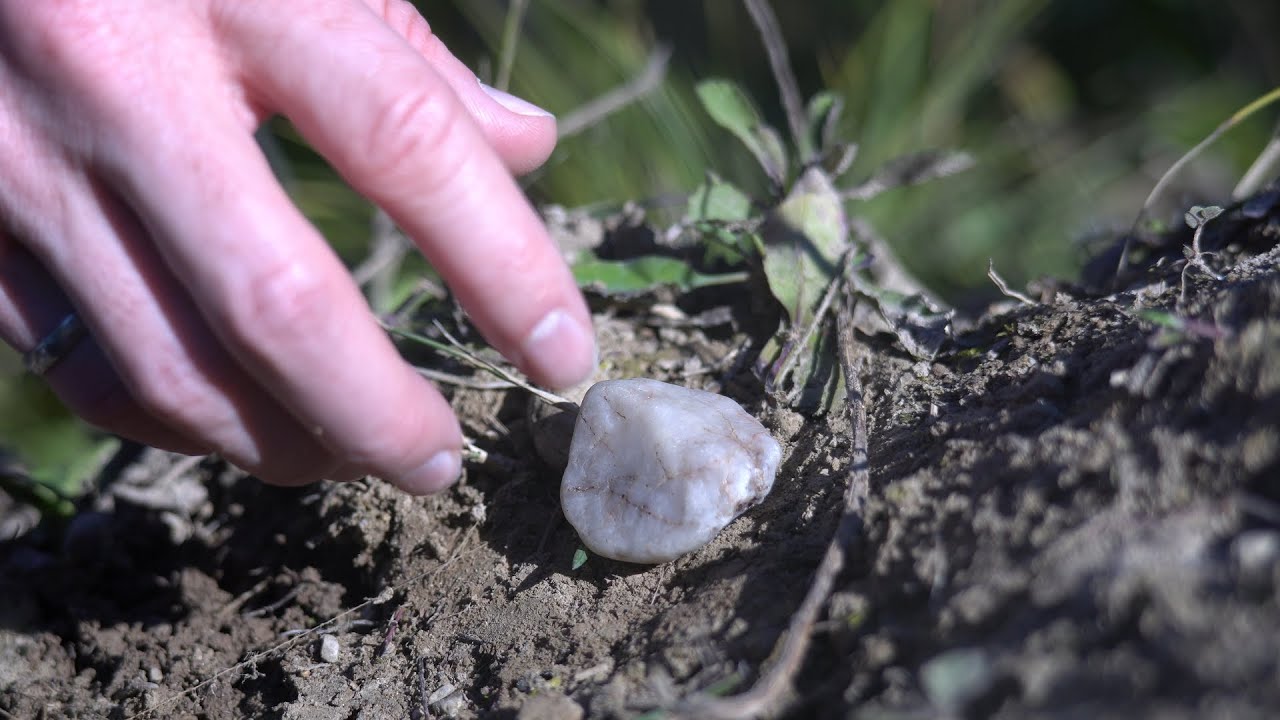
How To Make A CPU
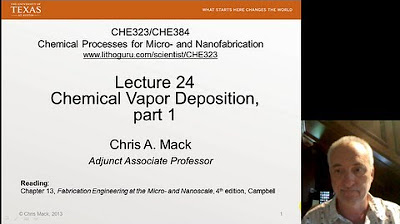
Lecture 24 (CHE 323) CVD, part 1
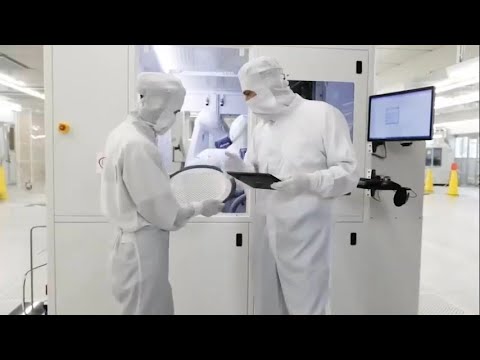
Fabricação de Chips - Como Microchips são feitos? - Infineon (Tradução e dublagem: Matteo Reis)
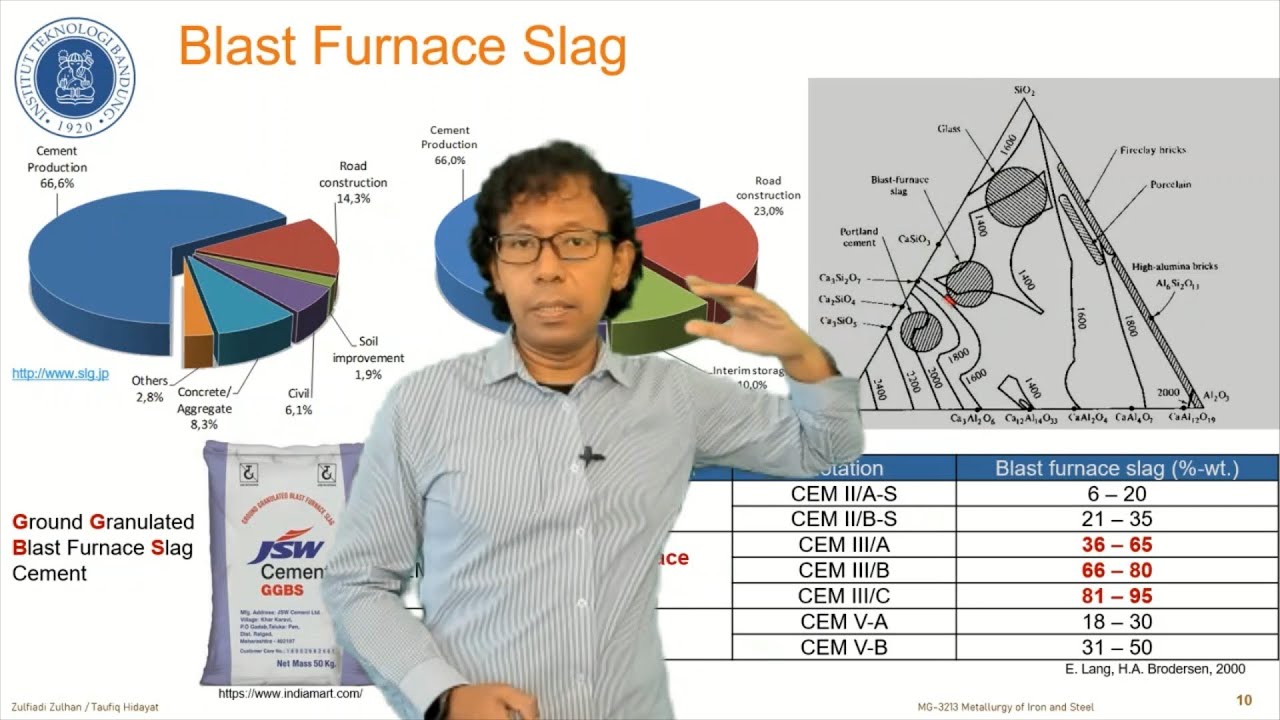
03. Metalurgi Besi Baja, S05 - Blast Furnace Slag, Cement
5.0 / 5 (0 votes)