AIRBUS HYDRAULIC SYSTEM how does it work? Explained by Captain Joe
Summary
TLDRIn this video, Captain Joe provides a comprehensive introduction to the Airbus A320 hydraulic systems, covering the roles of the Green, Blue, and Yellow systems in powering various aircraft components. He explains how the systems are designed for redundancy and reliability, including the use of pumps, pressure management, and backup features like the PTU (Power Transfer Unit). The video also explores failure scenarios, showing how the loss of a hydraulic system impacts flight operations and how backup systems ensure safe operation. This is a must-watch for aviation enthusiasts and aspiring pilots looking to understand hydraulic system mechanics in detail.
Takeaways
- π The Airbus A320 hydraulic system consists of three independent systems: Green, Blue, and Yellow, each with its own fluid reservoir and accumulator.
- π Each hydraulic system operates at a normal pressure of 3000 PSI (approximately 200 bars), much higher than car tire pressure.
- π The Green and Yellow systems have engine-driven pumps, with the Yellow system also having an electrical backup pump, while the Blue system relies on an electrical pump for normal and emergency operation.
- π In case of emergency, the Blue system can also use a secondary pump powered by a Ram Air Turbine.
- π The hydraulic system's status is monitored via the ECAM hydraulic page, which shows key data like reservoir levels, system pressure, and pump status.
- π The Green hydraulic system powers critical components like landing gear retraction, slats, flaps, reverser doors of Engine 1, and normal braking.
- π The Blue hydraulic system powers flight controls, and in case of total electrical power loss, the Ram Air Turbine helps provide hydraulic pressure and powers an emergency generator.
- π The Yellow hydraulic system drives flaps, alternate braking, reverser doors for Engine 2, and contributes to flight control actuators for rudder, stabilizer, elevators, slats, flaps, and ailerons.
- π In case of failure of one hydraulic system, the remaining systems provide backup pressure, ensuring reliability and redundancy in the hydraulic system.
- π The Power Transfer Unit (PTU) ensures system redundancy by transferring hydraulic pressure from the Yellow system to the Green system in case of engine failure, maintaining normal operation.
- π In case of a Green hydraulic system reservoir leak, emergency procedures include shutting off the PTU and the engine-driven pump, with the loss of the Green system affecting key functions like braking and flight controls, but the other systems provide backup.
Q & A
What are the three hydraulic systems on the Airbus A320, and how are they differentiated?
-The three hydraulic systems on the Airbus A320 are the Green, Blue, and Yellow systems. Each system is identified by a specific color, and each has its own hydraulic fluid reservoir and accumulator. The systems are independent and cannot transfer fluid between them.
What is the normal operating pressure for the A320 hydraulic systems, and how does it compare to everyday pressures?
-The normal operating pressure for each hydraulic system on the Airbus A320 is 3000 PSI, which is approximately 200 bars. This pressure is significantly higher than the pressure in a typical car tire, which ranges from 2 to 3 bars.
What type of pumps drive the hydraulic systems on the Airbus A320?
-The Green and Yellow hydraulic systems are driven by engine-driven pumps. The Yellow system also has an electrical backup pump. The Blue system is solely driven by an electrical pump for normal operation, with an emergency secondary pump powered by a ram air turbine.
How does the Power Transfer Unit (PTU) function in the case of a hydraulic failure?
-The PTU automatically activates when there is an engine failure, pressuring the Green hydraulic system by using the Yellow systemβs hydraulic pressure. This ensures that all hydraulic systems continue to function as normal, providing redundancy.
What happens if the Green hydraulic system experiences a low fluid level?
-If the Green hydraulic system experiences a low fluid level, the ECAM will display a warning. The affected components include nosewheel steering, normal braking, and landing gear retraction. A tow truck would be needed after landing, and alternate braking would be used from the Yellow system.
What are some key components driven by each hydraulic system on the A320?
-The Green hydraulic system controls the landing gear, slats, flaps, engine 1 reverser doors, and normal braking. The Blue system drives the slats and flight controls, and in case of electrical power loss, it uses the ram air turbine to power the hydraulic system and an emergency generator. The Yellow system controls engine 2 reverser doors, alternate braking, and also provides pressure for the flight control actuators.
How does the Airbus A320 ensure redundancy in its hydraulic system?
-The A320 ensures redundancy by having three independent hydraulic systems. If one system fails, the other two can provide backup. Additionally, the Green and Yellow systems can share pressure through the PTU, further enhancing the systemβs reliability.
What are the consequences of a hydraulic Green system failure during a flight?
-In the case of a Green system failure, components such as nosewheel steering, auto brake, and normal braking will be inoperative. Additionally, spoilers 1 & 5 will not function, requiring alternate braking from the Yellow system. The landing gear will also need to be manually extended and cannot be retracted after landing.
What does the ECAM show when a hydraulic system failure occurs?
-When a hydraulic system failure occurs, the ECAM will automatically display the hydraulic page, indicating the affected system with a failure message, such as 'Hydraulic Green Reservoir Low Level'. It also shows secondary failures, such as inoperative flight controls or braking systems, helping the crew assess the situation.
How are the Airbus A320's hydraulic system components monitored and controlled by the crew?
-The hydraulic system components on the Airbus A320 are monitored through the ECAM display, which shows the status of each system. The crew can control the hydraulic pumps using push-buttons on the overhead panel, where they can select them to be ON, AUTO, or OFF depending on the situation.
Outlines
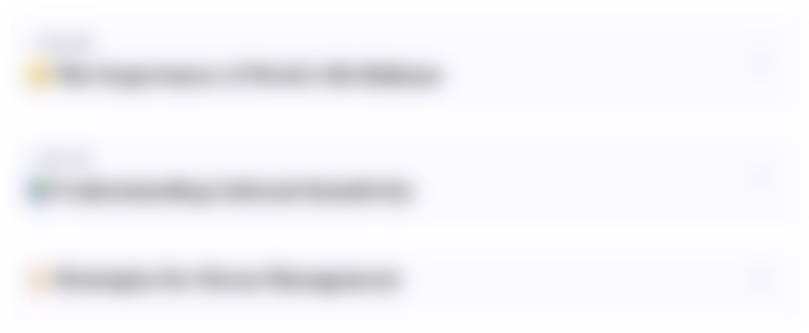
This section is available to paid users only. Please upgrade to access this part.
Upgrade NowMindmap
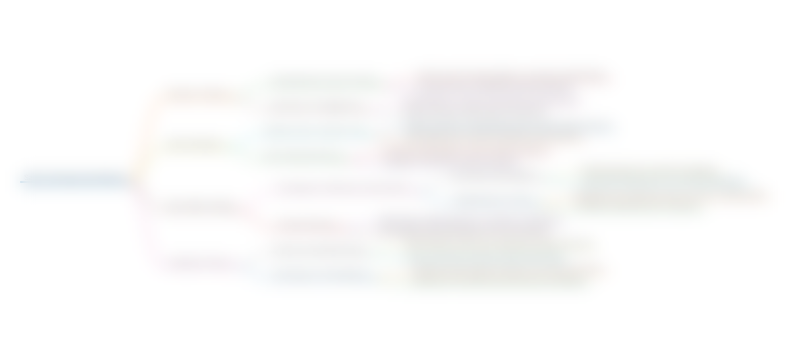
This section is available to paid users only. Please upgrade to access this part.
Upgrade NowKeywords
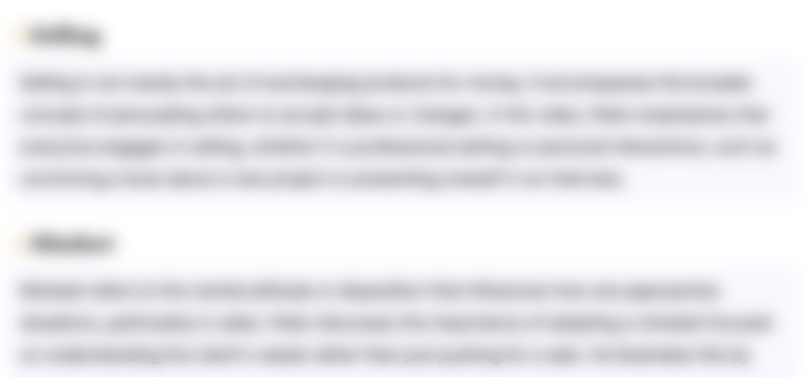
This section is available to paid users only. Please upgrade to access this part.
Upgrade NowHighlights
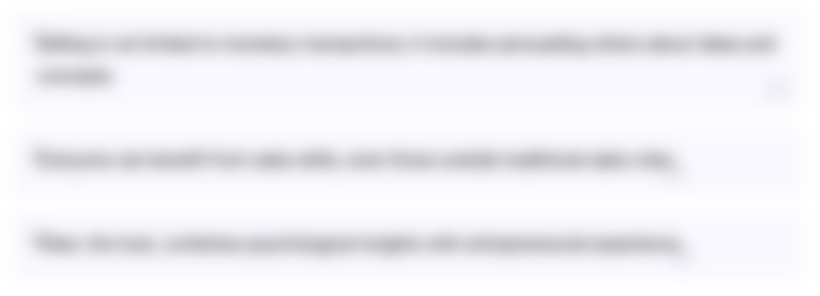
This section is available to paid users only. Please upgrade to access this part.
Upgrade NowTranscripts
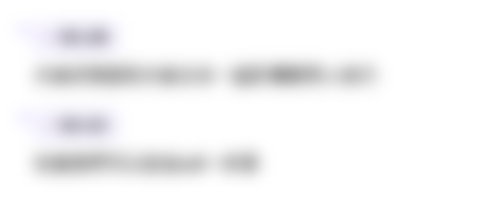
This section is available to paid users only. Please upgrade to access this part.
Upgrade NowBrowse More Related Video

Airbus A320 Auxiliary Power Unit (APU) start
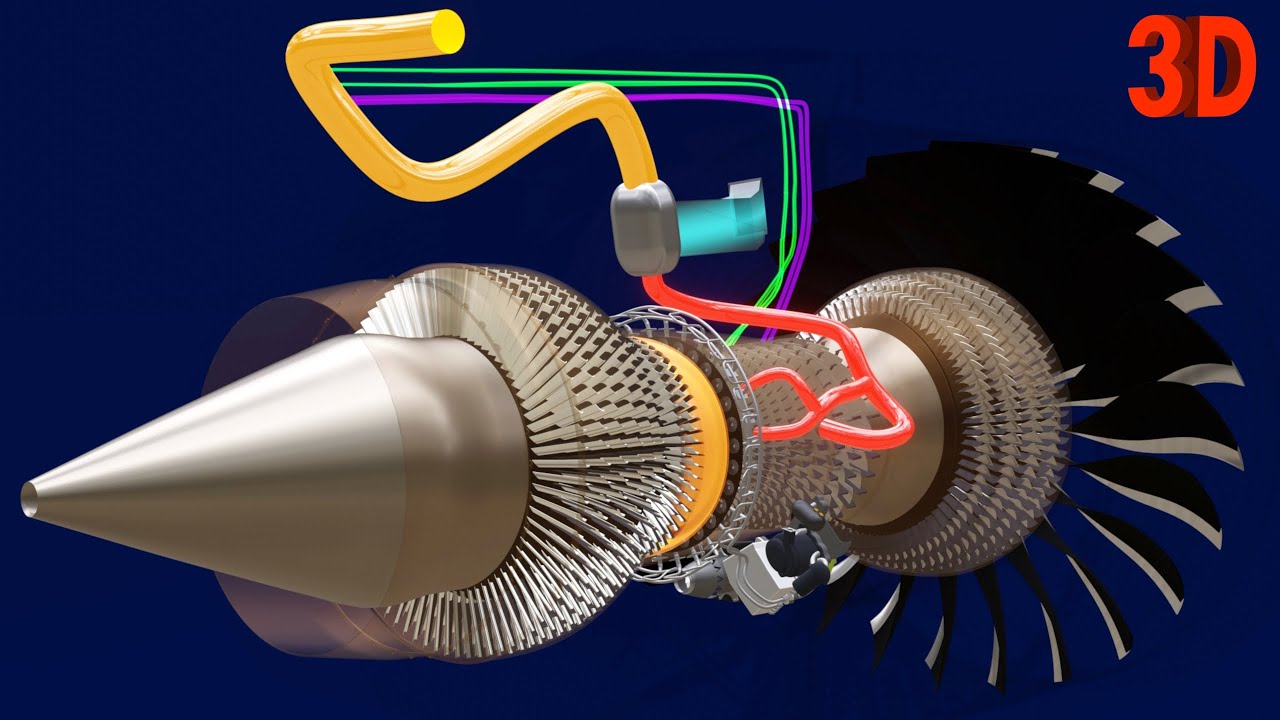
How Jet Engine Works | Part 2 : Outputs
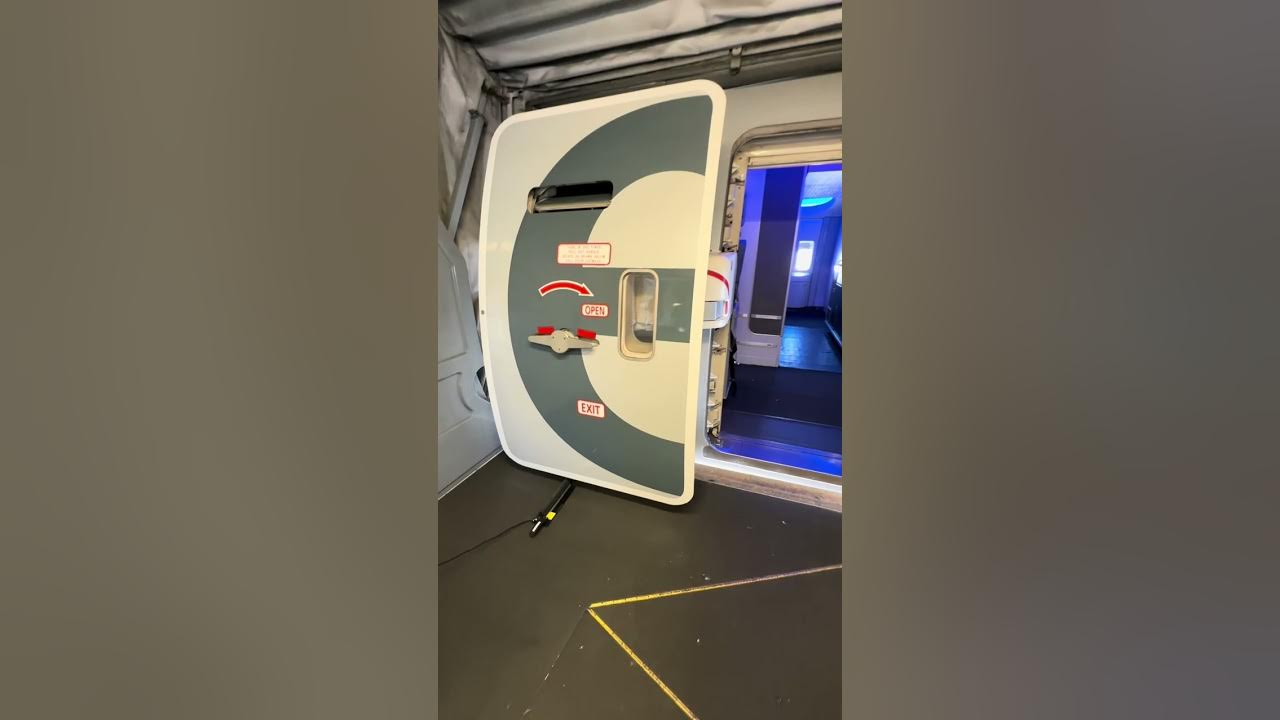
Aircraft Doors and Door assist ATA 52
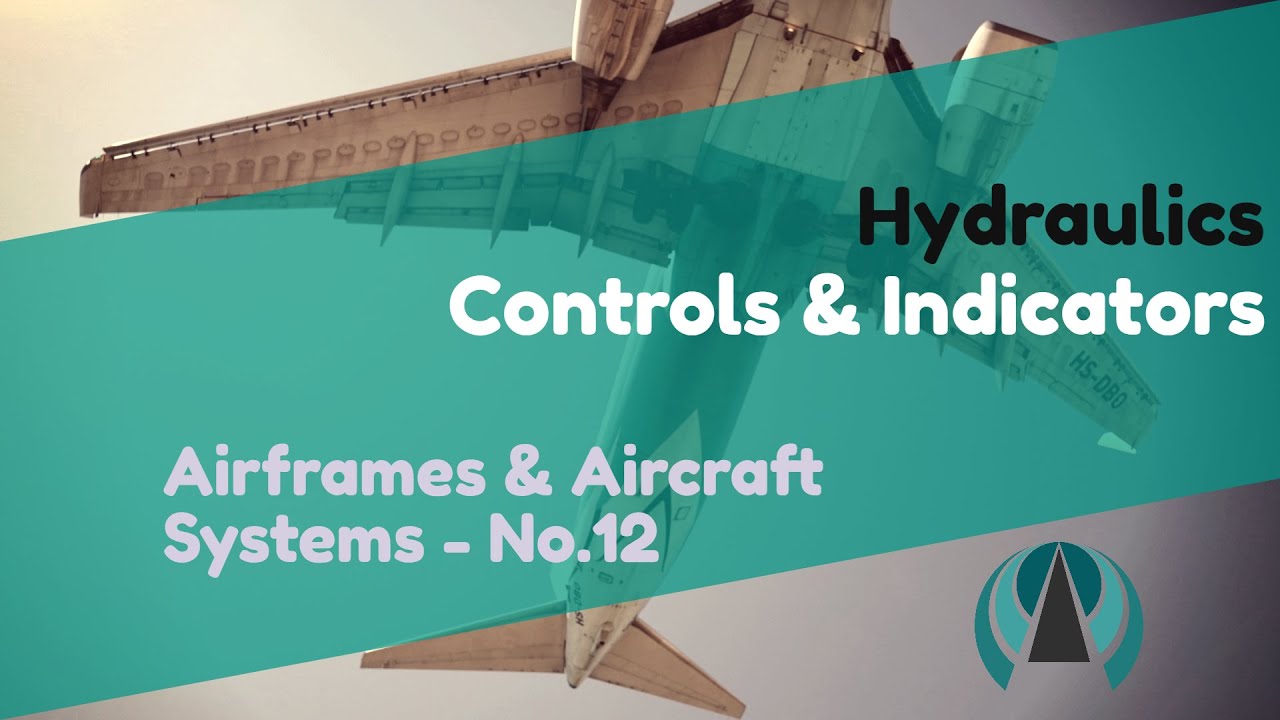
Controls & Indicators - Hydraulics - Airframes & Aircraft Systems #12

Hydraulics - Basic Principles of Hydromechanics - Airframes & Aircraft Systems #4

How does the AIRBUS FUEL SYSTEM work? Explained by CAPTAIN JOE
5.0 / 5 (0 votes)