P&ID CHECKING (COMMISSIONING)
Summary
TLDRThis video explores the critical process of Piping and Instrumentation Diagram (PNID) checks, which ensure that a plant's physical installation aligns with design specifications. It emphasizes the importance of a multi-disciplinary team, including commissioning, process, and safety engineers, in conducting thorough inspections. Key checkpoints include verifying piping, equipment, instrumentation, and safety measures. The video highlights the necessity of a punch list for tracking discrepancies and ensuring accountability throughout the commissioning process. Overall, it stresses that meticulous PNID checks are essential for successful plant commissioning and safe operations.
Takeaways
- 😀 PNID checks are essential for ensuring that the physical installation of a plant matches its design specifications.
- 🔍 A PNID check systematically verifies engineering and construction details to identify errors before commissioning.
- 👷♂️ A multi-disciplinary team, including engineers and safety experts, should perform PNID checks for thoroughness.
- ⚙️ Key areas to verify during PNID checks include piping, equipment, instrumentation, safety devices, and operational accessibility.
- 📋 Temporary identification tags and signs are crucial for marking unmarked equipment and lines during the commissioning process.
- ⏰ PNID checks should occur after construction handover, before pre-commissioning, during simultaneous checks for large systems, and after pre-commissioning.
- 📝 A punch list is vital for tracking discrepancies and ensuring that all issues are addressed before the plant goes live.
- 🔧 Proper documentation and structured tracking of issues prevent overlooking critical details that could affect safety and performance.
- 🚨 Skipping PNID walkthroughs can lead to installation errors, safety hazards, and increased costs due to last-minute corrections.
- 🤝 Thoroughness in PNID checks significantly impacts the smoothness of commissioning and operational readiness of the plant.
Q & A
What is the primary purpose of a P&ID check?
-The primary purpose of a P&ID check is to systematically verify that the physical installation of the plant matches the design specifications represented in the P&ID diagrams.
Who conducts the P&ID check?
-The P&ID check is conducted by a multi-disciplinary team that includes commissioning engineers, process engineers, mechanical, electrical and instrumentation engineers, HSSE experts, operations personnel, maintenance personnel, and construction teams.
What are some key elements to verify during a P&ID check?
-Key elements to verify include piping sizes, materials and routing, installation of valves and fittings, equipment orientation and accessibility, instrumentation positioning, safety device placements, and construction quality.
What is a punch list and its significance in P&ID checks?
-A punch list is a document used during the review and verification of P&IDs to track any issues or discrepancies identified during inspections, ensuring all problems are resolved before commissioning or operational phases.
When should P&ID checks be performed during the commissioning process?
-P&ID checks should be performed after handover from construction, before pre-commissioning activities, simultaneously for large systems, and finally after pre-commissioning activities are complete.
What role does color coding play in the P&ID walkdown?
-Color coding in the P&ID walkdown helps to visually organize and identify specific systems, making it easier to manage inspections and set boundaries during the check.
What are temporary identification tags and why are they used?
-Temporary identification tags are used to label equipment and lines that are not yet permanently marked, helping the team track specific pieces of equipment and piping without confusion.
What potential risks might arise from skipping the P&ID walkthrough?
-Skipping the P&ID walkthrough could lead to unnoticed installation errors, missing components, or incorrect configurations, which may result in safety hazards, operational inefficiencies, or costly delays during commissioning.
What is the importance of safety checks during a P&ID review?
-Safety checks ensure that all safety devices are properly placed and operational, escape routes are clear, and compliance with safety regulations is maintained, which is crucial for the overall safety of the plant.
How do operations and maintenance considerations factor into P&ID checks?
-Operations and maintenance considerations ensure that all critical operational points are accessible for safe and efficient use, and that equipment can be easily maintained or repaired, thereby enhancing operational reliability.
Outlines
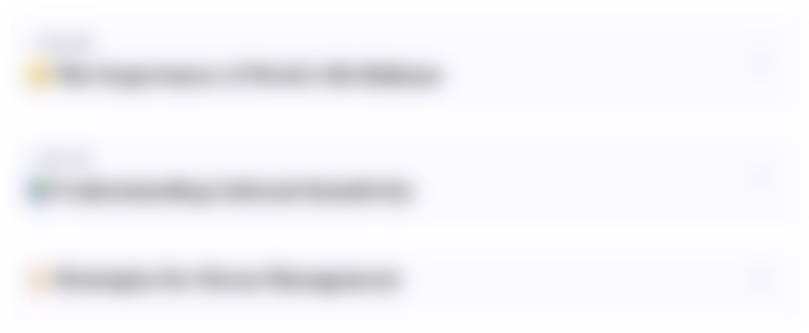
This section is available to paid users only. Please upgrade to access this part.
Upgrade NowMindmap
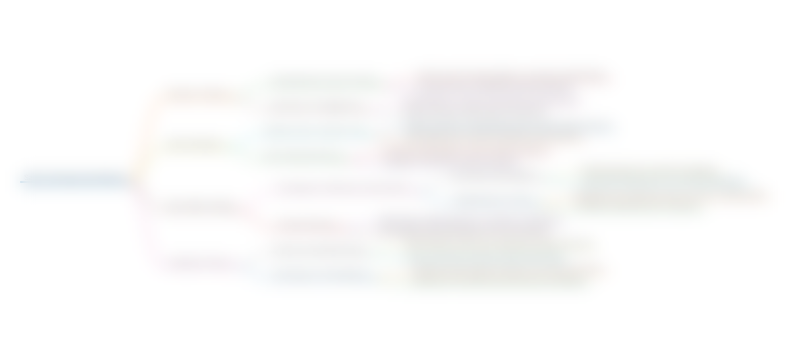
This section is available to paid users only. Please upgrade to access this part.
Upgrade NowKeywords
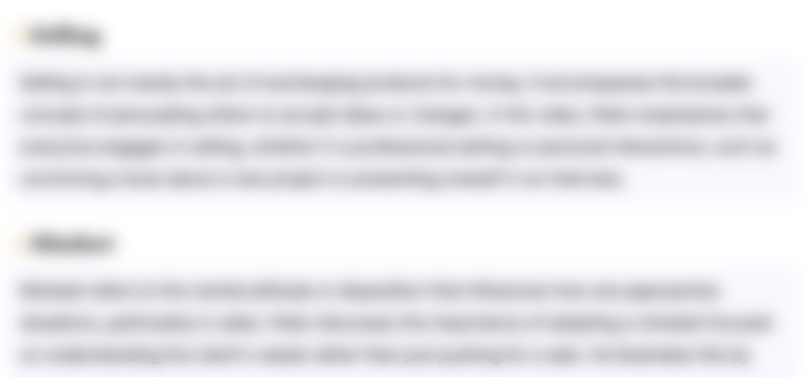
This section is available to paid users only. Please upgrade to access this part.
Upgrade NowHighlights
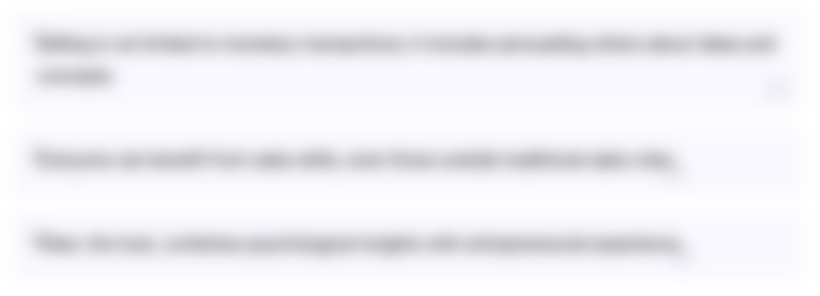
This section is available to paid users only. Please upgrade to access this part.
Upgrade NowTranscripts
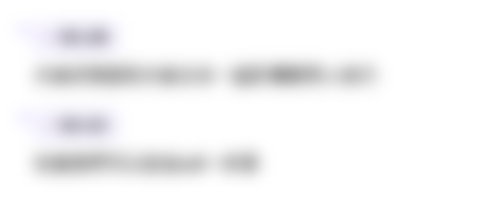
This section is available to paid users only. Please upgrade to access this part.
Upgrade NowBrowse More Related Video
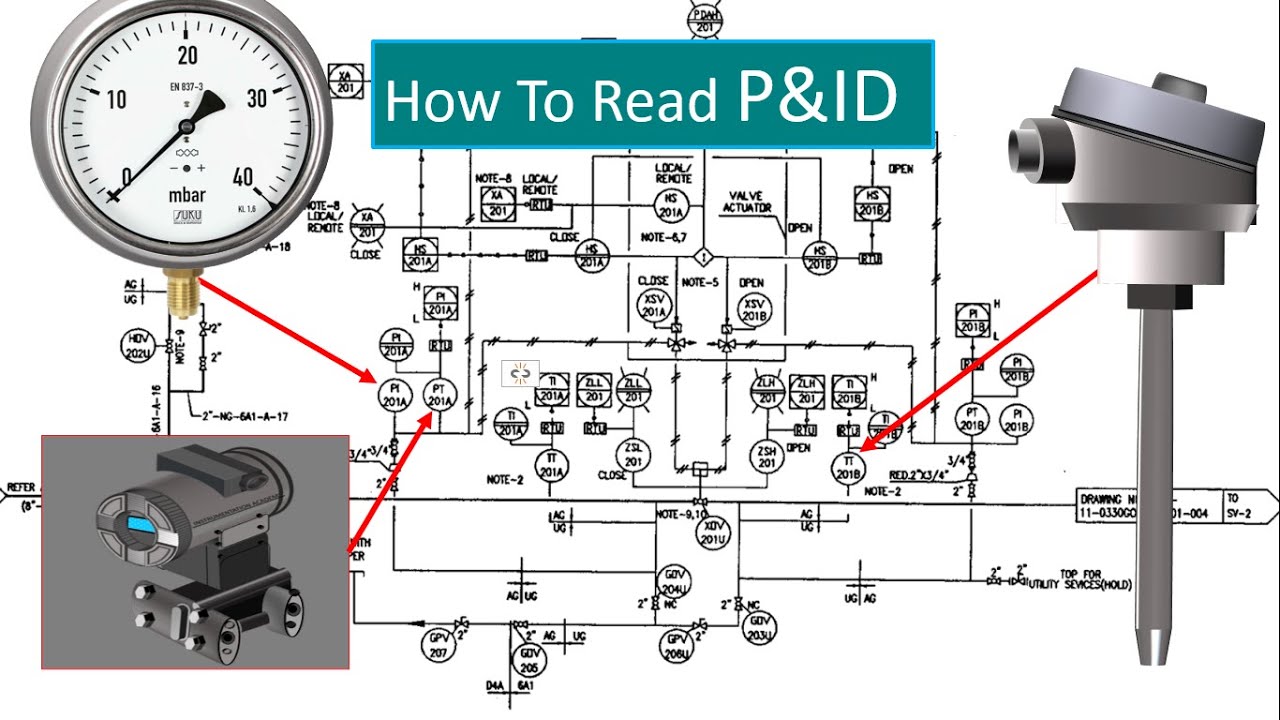
P & ID Diagram. How To Read P&ID Drawing Easily. Piping & Instrumentation Diagram Explained.

Key P&ID Details for HAZOPS - A HAZOP Crash Course

Daikin Sensira FTXF vs FTXC Inverter air conditioners | Brief comparison
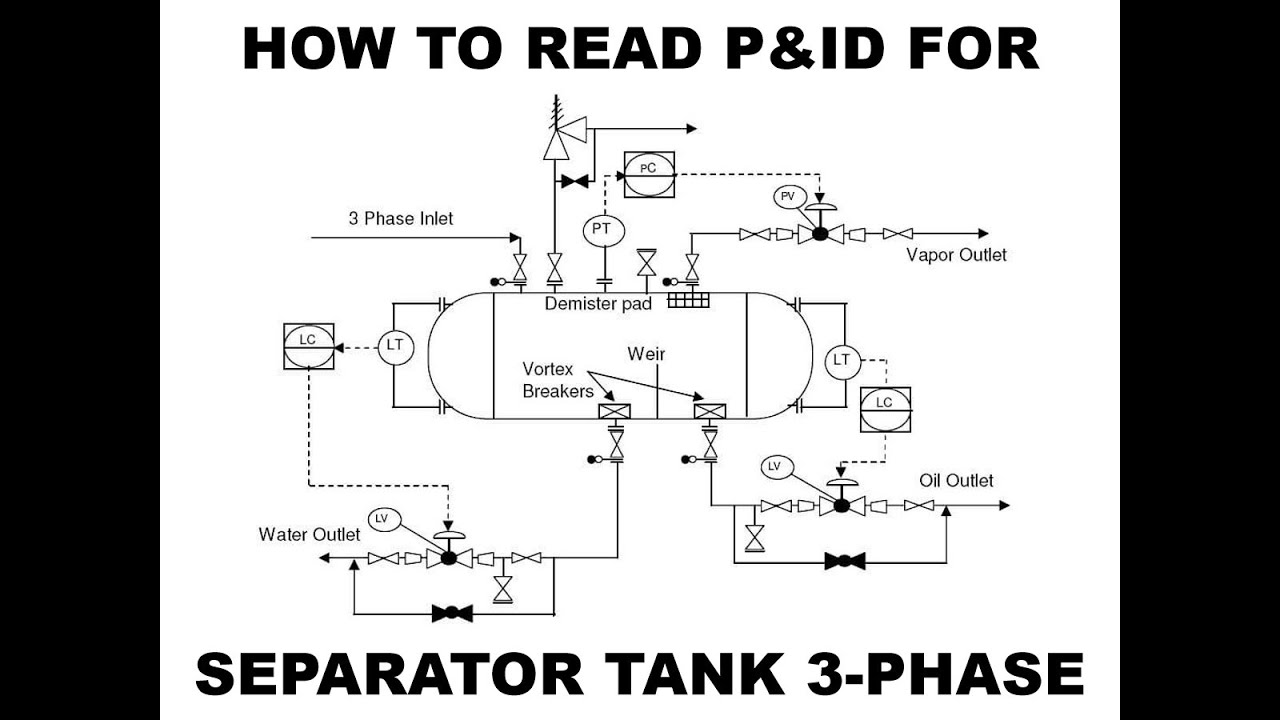
How To Read P&ID Diagram for Separator Tank (3-Phase) in Malay - Nazmi Ismail

What is Quality Control and meaning?
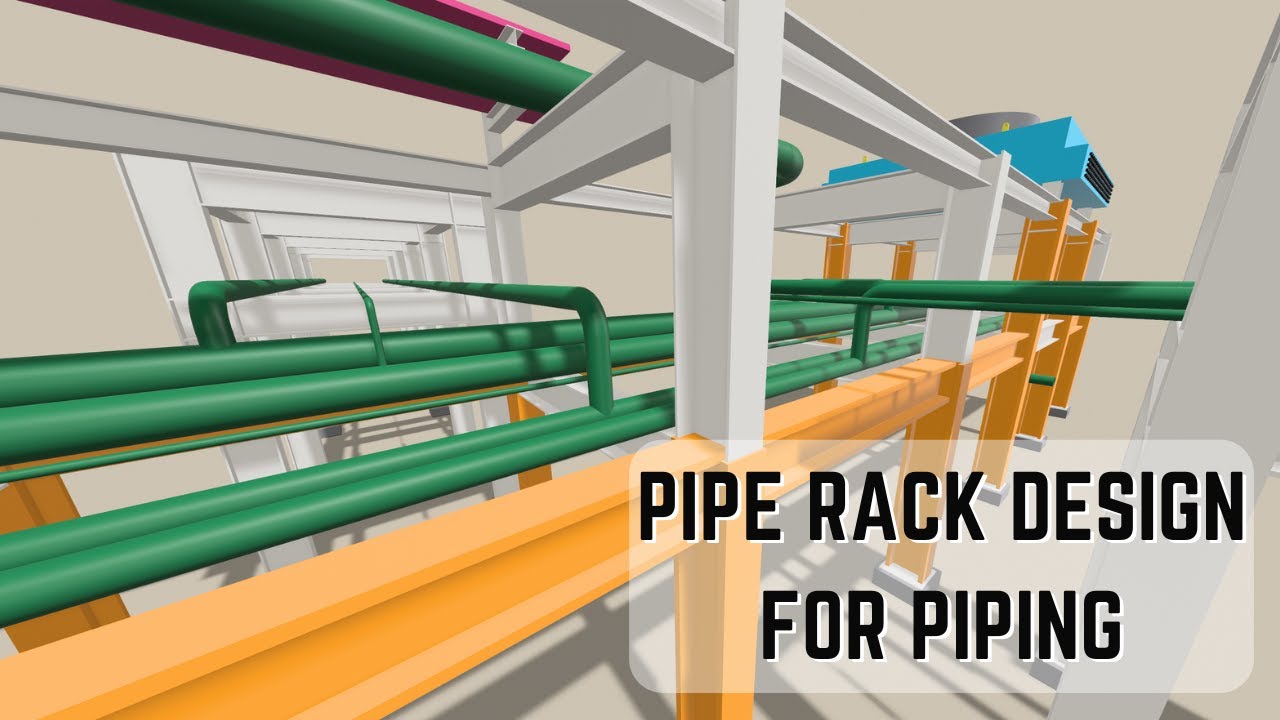
Pipe Rack Design for Piping : Essential Tips for Piping Engineers
5.0 / 5 (0 votes)