Prop balanced to within the weight of a Dollar Bill! - Hartzell Factory All Access!
Summary
TLDRThis video takes viewers behind the scenes at Hartzell Propeller, one of the most established propeller manufacturers. It covers a detailed tour of their facilities, focusing on static and dynamic balancing, the precision of manufacturing processes, and testing for propeller safety and performance. The host explores the balance tuning on an RV-14 propeller, highlights Hartzell's advancements in robotic technology, and delves into the differences between aluminum and composite propellers. The video showcases the dedication and expertise of Hartzell's workforce in ensuring high-quality, safe aviation components.
Takeaways
- 🔧 The video explores the process of propeller manufacturing and balancing at Hartzell Propeller's facility.
- 🛠️ A single dollar bill is enough to throw the machine's balance off, highlighting the sensitivity of the equipment used.
- ⚙️ Dynamic balancing is performed after static balancing to ensure precision and smooth propeller performance.
- ✈️ The RV-14 plane featured in the video undergoes dynamic balancing after its service bulletin work is completed.
- 🏭 Hartzell utilizes advanced robotic technology to improve consistency and quality during the manufacturing process.
- 🛡️ Propeller blades are rigorously tested for structural integrity using techniques like dye penetrant inspection and strain gauges.
- 🔬 Vibrational testing is critical to ensure propellers can handle the stresses of high-frequency vibrations from rotating systems.
- 🛡️ Hartzell has shifted from primarily using aluminum blades to increasing their use of composite technology for modern propellers.
- 🔥 The video demonstrates the precision in applying small amounts of weight to balance propellers, down to the gram.
- 🎥 The host gained exclusive behind-the-scenes access to Hartzell’s testing and manufacturing processes, providing a comprehensive look at their operations.
Q & A
What is the purpose of dynamic and static balancing in propellers?
-Dynamic and static balancing ensure that propellers rotate smoothly without causing excessive vibrations. Static balancing adjusts the balance of the blades when stationary, while dynamic balancing addresses any imbalance during the propeller's rotation, leading to a smoother flight.
Why is Hartzell considered a leader in propeller manufacturing?
-Hartzell has been in operation since 1917 and has developed a reputation for producing high-quality, reliable propellers. They invest heavily in robotic technology, quality control, and research and development to ensure precision and safety in their products.
What kind of testing is performed on propellers at Hartzell?
-Hartzell conducts static and dynamic balancing tests, as well as vibrational compatibility tests. They use strain gauges to measure high-frequency vibrations and ensure the propellers can handle stress during flight. This thorough testing ensures both safety and performance.
How does Hartzell’s robotic technology improve the manufacturing process?
-Hartzell uses robotic technology to ensure precision and consistency in their propeller manufacturing. Robots handle processes like blade machining, removing machining marks, and grinding. This results in higher accuracy and repeatability, ensuring that each propeller meets strict quality standards.
What is the significance of composite technology in modern propeller manufacturing?
-Composite technology is becoming increasingly important in propeller manufacturing due to its lightweight and durable properties. Hartzell has a dedicated facility for producing composite propellers, which involves layering materials like carbon fiber at precise angles for strength and performance.
How does Hartzell perform quality control on their propellers?
-Hartzell uses tools like coordinate measuring machines (CMM) for precision checks, and they perform dye penetration inspections to detect any cracks or flaws in the materials. They also use static and dynamic balancing to fine-tune the performance of each propeller.
What are strain gauges and how are they used in propeller testing?
-Strain gauges are small electrical devices that measure the amount of bending or strain in propeller blades. Hartzell uses strain gauges to test for vibrational stress at various points on the propeller blades, ensuring that the propellers can handle the forces they will experience during operation.
Why is engine preheating important in cold weather conditions?
-Engine preheating is crucial in cold weather to thin the oil and allow it to circulate more easily through the engine. This prevents low oil pressure and ensures a better start in cold temperatures, as well as reduces wear on the engine.
What steps are involved in Hartzell's composite blade manufacturing process?
-The process begins with the preparation of a kit consisting of raw materials like foam cores and carbon fiber. Layers are precisely applied according to design specifications, after which the blades are placed in molds and heated in furnaces to form the final composite structure.
What is the significance of the dynamic balance testing for the RV-14 propeller in the video?
-The dynamic balance testing ensures that the propeller operates smoothly with minimal vibrations at cruise RPM. After taking baseline readings, small weights are added or removed to achieve optimal balance, improving the aircraft's performance and reducing wear on the engine.
Outlines
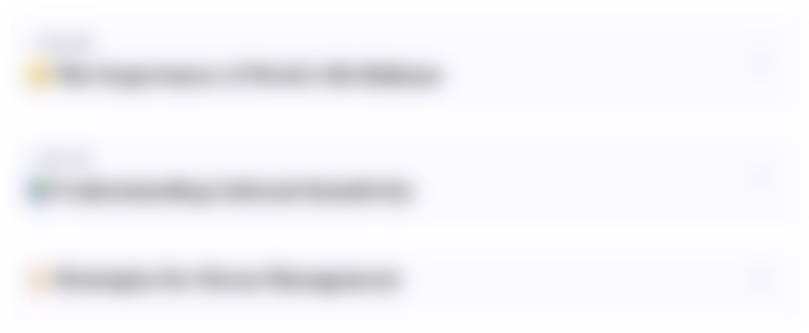
This section is available to paid users only. Please upgrade to access this part.
Upgrade NowMindmap
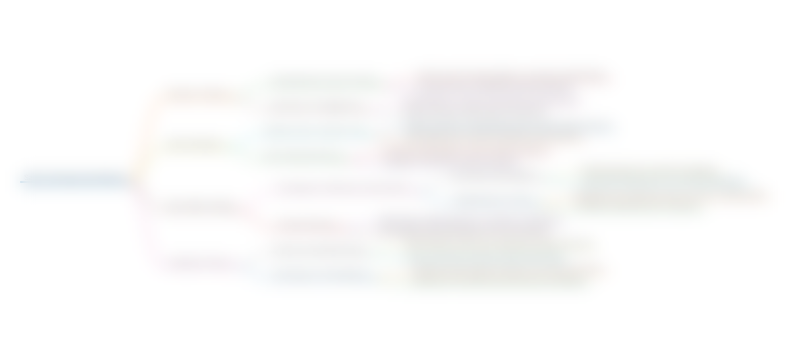
This section is available to paid users only. Please upgrade to access this part.
Upgrade NowKeywords
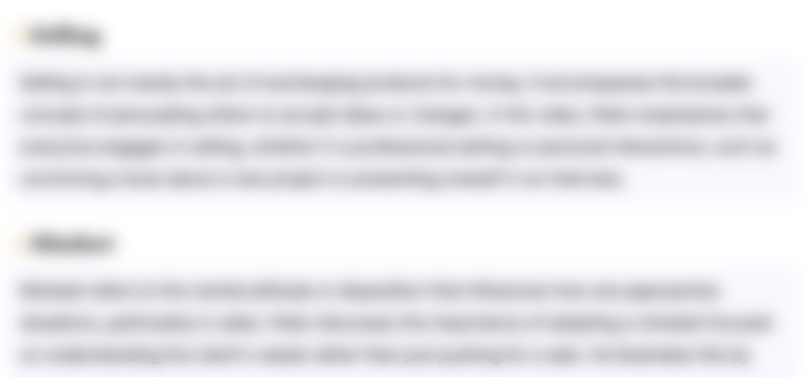
This section is available to paid users only. Please upgrade to access this part.
Upgrade NowHighlights
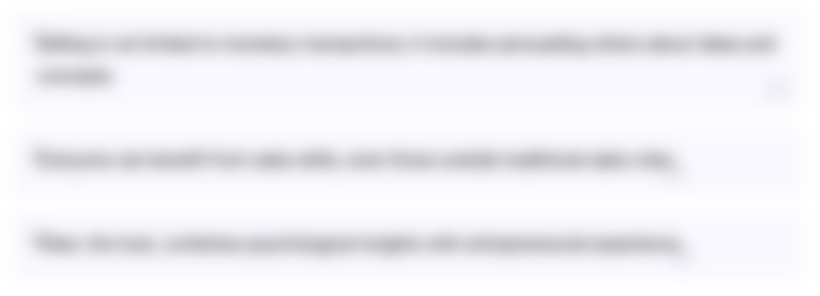
This section is available to paid users only. Please upgrade to access this part.
Upgrade NowTranscripts
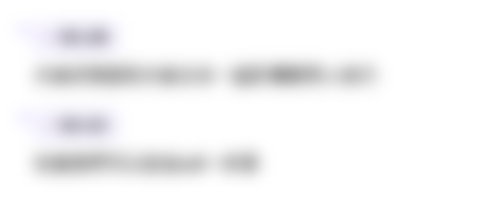
This section is available to paid users only. Please upgrade to access this part.
Upgrade NowBrowse More Related Video
5.0 / 5 (0 votes)