When to use PLC ,DCS & SCADA | PLC vs DCS vs SCADA Selection Guide
Summary
TLDRThis informative video delves into the intricacies of automation, discussing the optimal use cases for Programmable Logic Controllers (PLCs), Distributed Control Systems (DCSs), and Supervisory Control and Data Acquisition (SCADA) systems. It explains that PLCs are ideal for controlling discrete I/Os in single processes and for safety interlocks due to their fast scan times. DCSs are recommended for large-scale plants with analog I/Os and where process failure could lead to significant damage. SCADA is highlighted for its role in data collection, transmission, and remote monitoring across vast industries, including power generation and oil & gas sectors. The video also emphasizes the redundancy and fault tolerance of DCS systems, and how PLCs can integrate within them. The discussion concludes with practical examples of SCADA applications, illustrating its versatility in remote monitoring and control across different units and locations.
Takeaways
- 🤖 PLCs are preferred for controlling single processes with many discrete I/Os and for applications requiring fast scan times and safety interlocks.
- 🏭 DCS systems are ideal for large production plants like fertilizer, chemical, and power plants where analog I/Os are needed for overall plant control.
- 🔄 In DCS, process failure can lead to significant damage, hence the use of multiple controllers including a main and redundant one for fault tolerance.
- 🔌 PLCs can be integrated into a DCS system to provide data on the network, showing the convergence of PLC and DCS technologies.
- 🛠️ Redundancy in DCS systems ensures that if one area controller fails, the process continues with a redundant controller without affecting other areas.
- 📊 SCADA is used for large industries requiring data collection, transmission, and remote monitoring, such as power generation, oil and gas, and chemical plants.
- 🖥️ SCADA HMI systems allow operators to remotely vary set points and monitor processes, enhancing control and efficiency.
- 🏜️ SCADA systems are beneficial in remote or harsh environments where on-site data collection is challenging, using RTUs for data transmission.
- 🌐 Centralized management of multiple plants located in different cities or countries is possible through SCADA, providing a unified control room experience.
- 🔄 SCADA transmits data and commands to PLCs and DCS to control specified processes, demonstrating its role as a communication bridge in industrial automation.
- 🎯 Understanding the differences and appropriate applications of PLCs, DCS, and SCADA is crucial for effective automation in various industrial scenarios.
Q & A
When is it preferable to use a PLC in an automation system?
-A PLC (Programmable Logic Controller) is preferable when you need to control a single process with a lot of discrete I/Os or when your industrial plant has extensive interlocking requirements. It is also best for safety interlocks due to its faster scan time and good processing power, making it ideal for manufacturing plants with numerous discrete I/Os.
What are the scenarios that require a SCADA system?
-SCADA (Supervisory Control and Data Acquisition) systems are required in large industries where there is a need for data collection, data transmission, and remote plant monitoring. It is commonly used in power generation and transmission units, oil and gas industries, and chemical plants where frequent monitoring is necessary. SCADA is also beneficial for managing plants located in different cities or countries from a central control room.
Under what conditions would a DCS system be the best choice?
-A DCS (Distributed Control System) is the best choice for big production plants such as fertilizer, chemical, cement, and power plants where there are many analog I/Os to control the entire plant. It is also used in situations where process failure could cause significant damage, providing a system where different process areas have their own controllers for redundancy and fault determination.
How does a PLC contribute to a DCS system?
-PLCs can be integrated into a DCS system to provide data on the DCS network. This integration allows for the collection of information from discrete I/Os controlled by the PLC, enhancing the overall control and monitoring capabilities of the DCS system.
What is the significance of redundancy in a DCS system?
-Redundancy in a DCS system is crucial as it ensures that if one area controller fails, the system's operation is not compromised. Each process area in a DCS system has multiple controllers, including a main controller and a redundant one. In the event of a failure, the redundant controller takes over, maintaining control and preventing disruption to the process.
How does SCADA transmit data and commands to PLCs and DCSs?
-SCADA systems transmit data and commands to PLCs and DCSs to control specified processes. This communication allows for the efficient operation and monitoring of industrial processes, enabling adjustments and control from a remote location.
What is the role of an RTU in a SCADA system?
-A Remote Terminal Unit (RTU) in a SCADA system is responsible for collecting data from remote locations, such as a wellhead in a harsh environment. The RTU sends this data to a safe location through radio or other transmission mediums, allowing for the monitoring and control of remote operations.
How does the scan time of a PLC impact safety interlocks?
-The faster scan time of a PLC is beneficial for safety interlocks because it allows for quicker detection and response to changes in the system. This rapid response is critical in preventing accidents and ensuring the safety of the industrial process.
What is the main advantage of having multiple controllers in a DCS system?
-The main advantage of having multiple controllers in a DCS system is that it provides a high level of fault tolerance. If one controller fails, the system can continue to operate using the redundant controller, ensuring that the process is not disrupted and maintaining the integrity of the plant's operations.
How does a SCADA HMI system help operators in controlling industrial processes?
-A SCADA Human-Machine Interface (HMI) system allows operators to visualize and interact with the process. They can adjust parameters such as set points for flow rates and monitor the status of various processes from a central location, improving efficiency and response times.
What is the role of industrial networking in the integration of PLCs and DCSs?
-Industrial networking plays a crucial role in the integration of PLCs and DCSs by facilitating communication between different parts of the system. This enables the sharing of data and control commands, allowing for a more cohesive and efficient operation of the entire industrial process.
Outlines
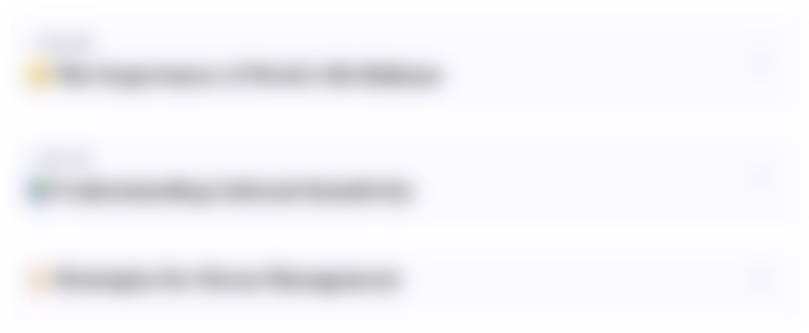
This section is available to paid users only. Please upgrade to access this part.
Upgrade NowMindmap
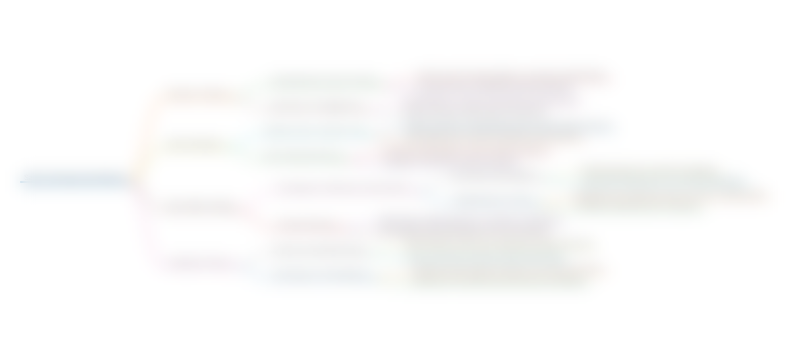
This section is available to paid users only. Please upgrade to access this part.
Upgrade NowKeywords
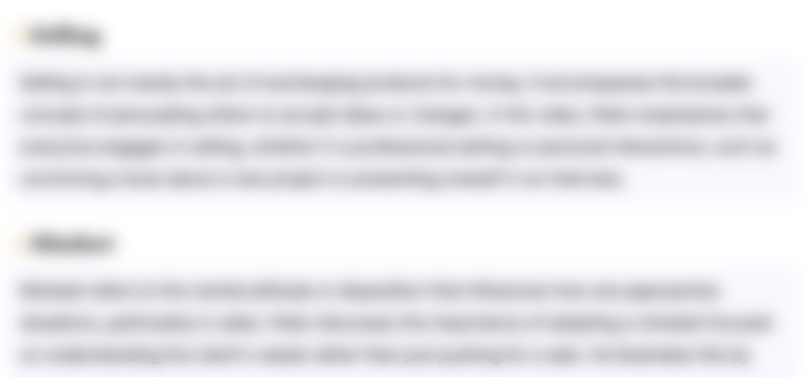
This section is available to paid users only. Please upgrade to access this part.
Upgrade NowHighlights
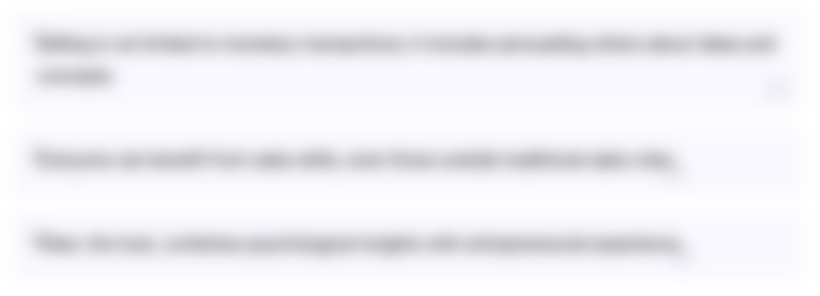
This section is available to paid users only. Please upgrade to access this part.
Upgrade NowTranscripts
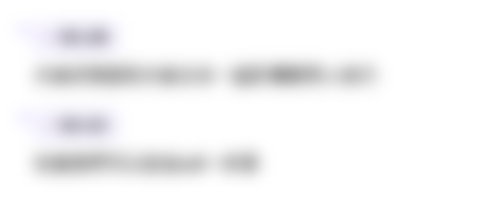
This section is available to paid users only. Please upgrade to access this part.
Upgrade NowBrowse More Related Video
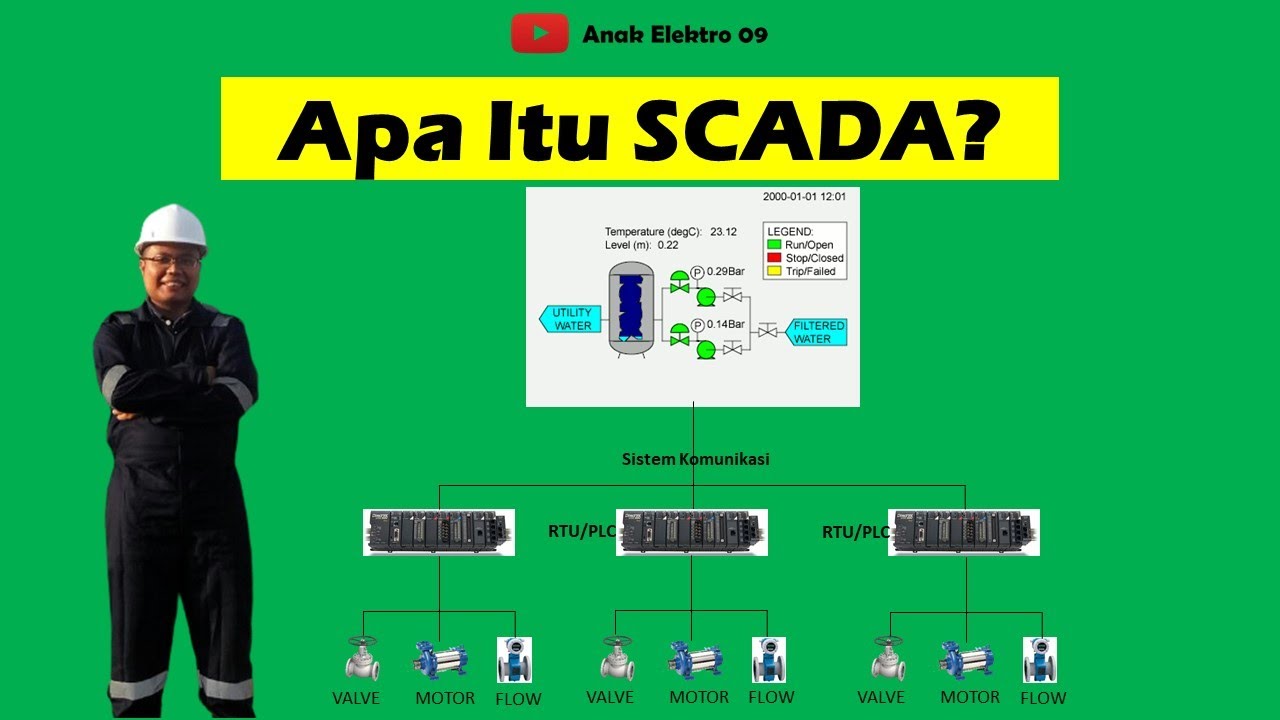
Pengenalan SCADA (Supervisory Control And Data Acquisition)
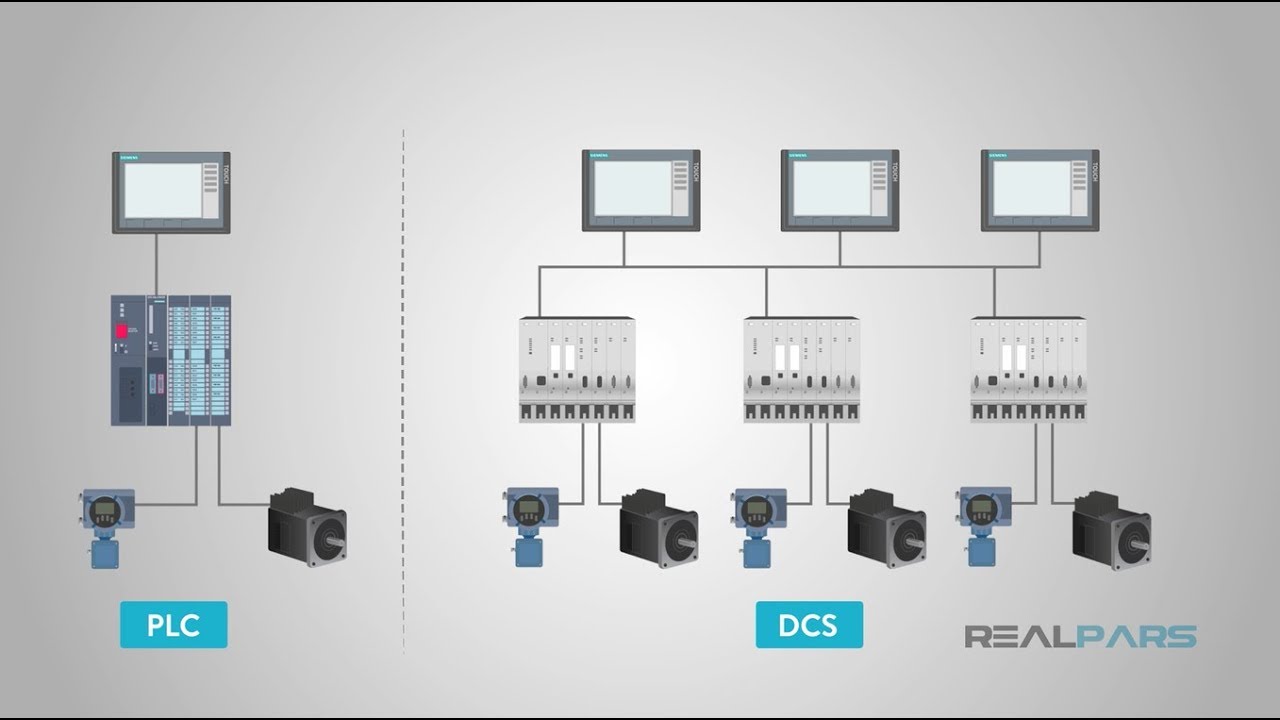
What is the Difference Between PLC and DCS?

What is SCADA? Supervisory Control and Data Acquisition

Introduction To SCADA System

AWAL BELAJAR Ngobrol Santai Tentang PLC (Programmable Logic Controller)
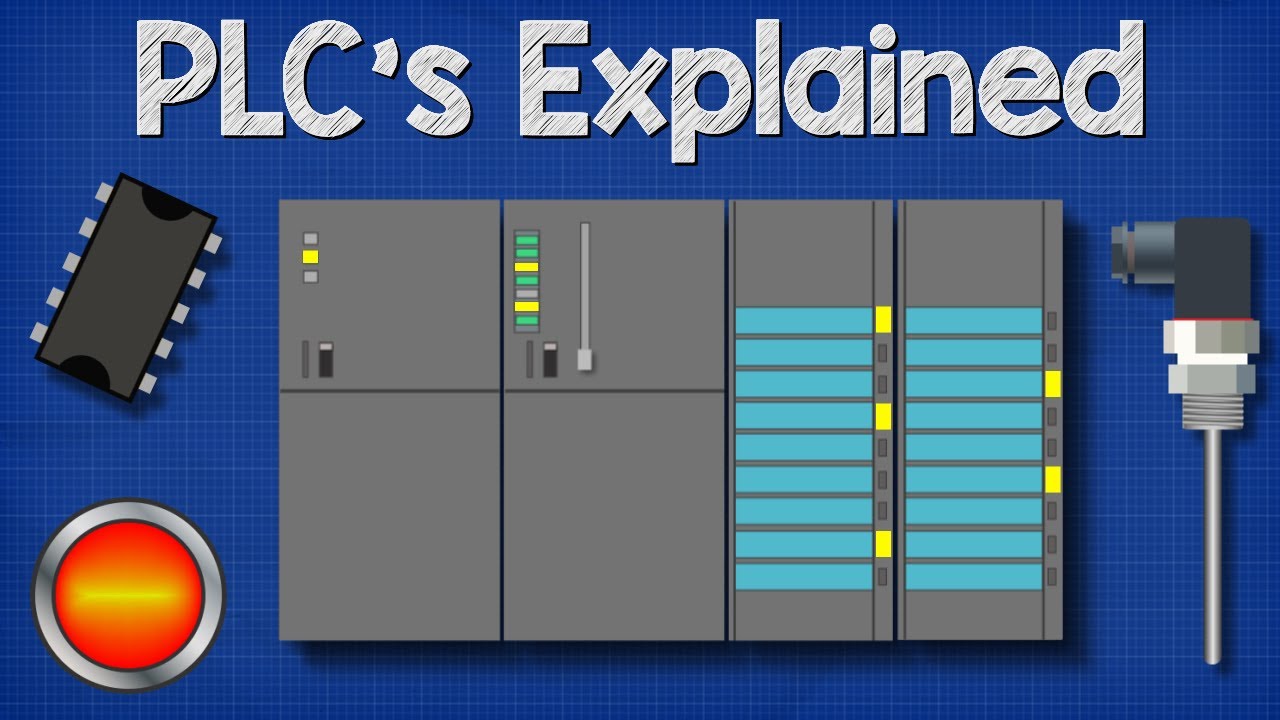
Programable Logic Controller Basics Explained - automation engineering
5.0 / 5 (0 votes)