Topic 6: Fracture Mechanisms Lecture 4
Summary
TLDRThis lecture delves into the microscopic examination of how materials fracture, distinguishing between brittle and ductile fractures. It illustrates ductile fractures with the classic cup and cone appearance and brittle fractures with flat, reflective surfaces. The lecture also covers various fracture types in materials like steel, carbon fiber composites, and polystyrene. It discusses fatigue, where cracks initiate at the surface and propagate, leading to failure. Additionally, it explores pressure vessel design strategies, 'yield before break' and 'leak before break,' to prevent catastrophic failures, emphasizing the importance of material selection based on fracture toughness and yield strength.
Takeaways
- 🔬 Fracture mechanisms are categorized into brittle and ductile fractures, with brittle fractures occurring suddenly and ductile fractures happening slowly over a period of plastic deformation.
- 📏 Ductile fractures exhibit necking, where the material narrows before breaking, while brittle fractures do not neck down and snap directly.
- 🔍 Visualizing fractures involves examining the cross-section of a tensile bar; a jagged appearance indicates moderate ductility, while a smooth, flat surface indicates brittleness.
- 🗜️ Ductile fractures in steel show a 'cup and cone' pattern, with the cup representing the necked region and the cone the final fracture area, often characterized by a dull, fibrous surface.
- 🔬 Microscopically, ductile fractures are marked by micro voids, which are small voids that form in the material, sometimes with material precipitates at the bottom.
- 📐 Brittle fractures are characterized by flat, shiny surfaces with little to no necking, and the crack propagation can be either trans granular or inter granular.
- 🖼️ Different materials exhibit unique fracture patterns; for example, LCDs show aligned polymer chains, carbon fiber composites reveal individual fibers, and Kevlar shows fractures along fiber lengths.
- 🔁 Fatigue fractures typically initiate at the surface and progress until they reach a critical size, leading to rapid failure, with the fracture surface showing a tortuous and bumpy pattern.
- 💥 The pressure vessel example illustrates the importance of understanding fracture mechanics in design, with strategies like 'yield before break' and 'leak before break' to prevent catastrophic failures.
- ⚙️ Material selection for pressure vessels is critical, with steels generally offering high strength and fracture toughness, making them suitable for these applications.
Q & A
What are the two main categories of fracture mechanisms?
-The two main categories of fracture mechanisms are brittle fractures, which happen suddenly, and ductile fractures, which happen slowly over a period of plastic deformation.
How can you visually distinguish between ductile and brittle fractures?
-Ductile fractures exhibit necking and a jagged, tortuous appearance, while brittle fractures do not neck down and snap in half with a flat surface. Ductile fractures often have a dull gray surface due to plastic deformation, whereas brittle fractures are typically bright because they reflect light back.
What is the classic appearance of a ductile fracture in steel?
-A ductile fracture in steel typically forms a 'cup and cone' fracture. The cup region shows where necking occurred, and the cone is where the brittle final fracture happens.
What is a micro void, and how does it relate to ductile fractures?
-A micro void is a small void that forms on the surface of a fractured sample, indicating a ductile fracture. These voids are often accompanied by chunks of material at their base.
What are the two modes of brittle failure in materials?
-The two modes of brittle failure in materials are trans granular cleavage, where the crack propagates across the grains, and inter granular decohesion, where the crack travels along grain boundaries.
How does a fatigue fracture differ from other types of fractures?
-Fatigue fractures usually initiate at the surface and exhibit a shiny, flat initiation site. The crack then propagates at a stable rate, forming visible lines on the material's surface, until it becomes unstable and fracture occurs rapidly.
What is the 'yield before break' design approach for pressure vessels?
-The 'yield before break' design approach for pressure vessels aims to have the material yield (showing a bulge) before the crack propagates all the way through the sidewall, providing a visible indication of failure before rupture.
What is the 'leak before break' design approach for pressure vessels?
-The 'leak before break' design approach allows the crack to grow through the wall until pressure can escape, preventing catastrophic failure by providing a warning sign such as steam leakage before the vessel ruptures.
What are the minimum acceptable yield strength and fracture toughness values for pressure vessel materials?
-The minimum acceptable yield strength for pressure vessel materials is about 300 mega Pascals, and the minimum acceptable fracture toughness is about 10 mega Pascals square root meters.
Why are steels often preferred for pressure vessels over aluminum?
-Steels are often preferred for pressure vessels over aluminum because they have both high strength and high fracture toughness, making them more suitable for the 'yield before break' and 'leak before break' design approaches.
Outlines
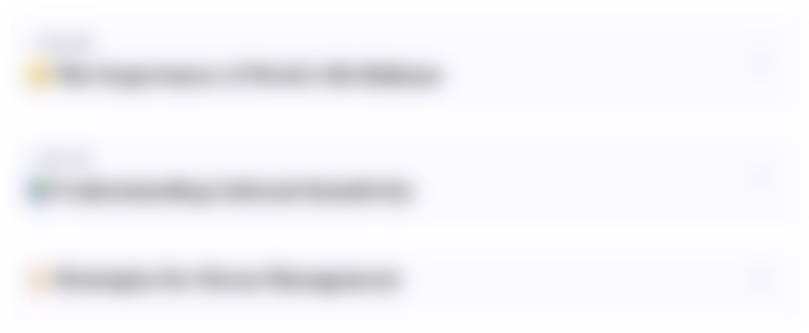
This section is available to paid users only. Please upgrade to access this part.
Upgrade NowMindmap
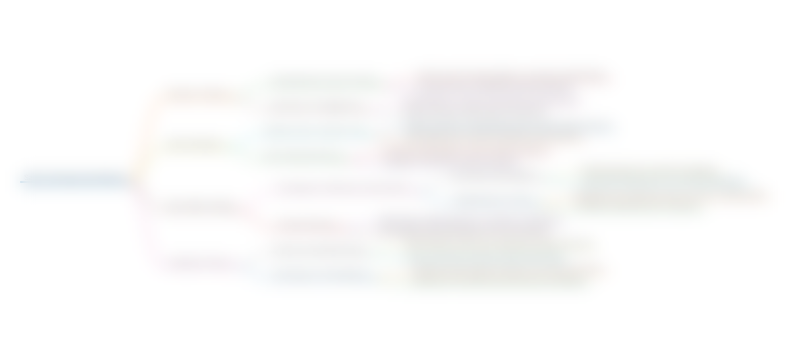
This section is available to paid users only. Please upgrade to access this part.
Upgrade NowKeywords
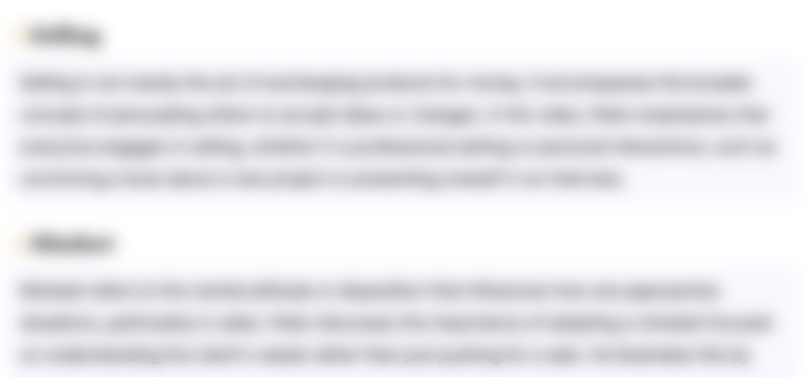
This section is available to paid users only. Please upgrade to access this part.
Upgrade NowHighlights
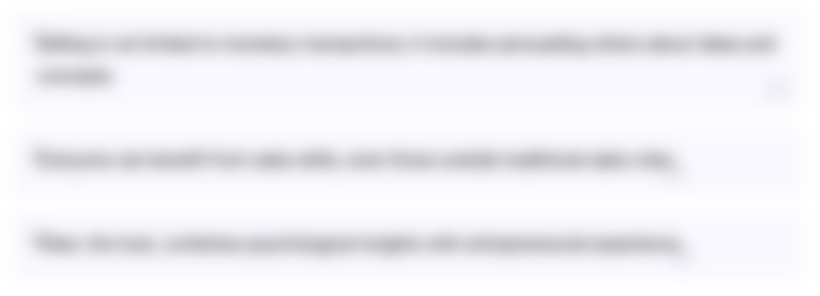
This section is available to paid users only. Please upgrade to access this part.
Upgrade NowTranscripts
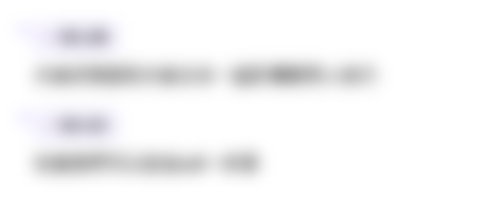
This section is available to paid users only. Please upgrade to access this part.
Upgrade NowBrowse More Related Video
5.0 / 5 (0 votes)