Introduction to Flexible Manufacturing System (FMS)
Summary
TLDRThis video introduces Flexible Manufacturing Systems (FMS), which are automated, interconnected machine cells controlled by a distributed computer system. FMS is ideal for mid-volume and mid-variety production, offering adaptability to changes in design, schedule, and volume. It comprises workstations, material handling systems, human resources, and computer control. The video discusses the history of FMS, its types, layout configurations, benefits, and considerations for implementation, positioning FMS as a key player in the shift towards Industry 4.0.
Takeaways
- 😀 Flexible Manufacturing Systems (FMS) are highly automated systems that combine processing stations, material handling, and storage systems, all controlled by a distributed computer system.
- 🛠️ FMS is designed for mixed-model, medium volume production, capable of handling 100 to 10,000 units per year.
- 🔄 The 'flexibility' in FMS allows for processing different part styles simultaneously and adjusting production quantities and designs according to customer demand.
- 🤖 The system can quickly adapt to changes in design, schedule, or production volume, both predictable and unpredictable.
- 🏭 The four basic components of FMS include workstations, automated material handling and storage systems, human resources, and a computer control system.
- ⚙️ Workstations in FMS typically consist of CNC machines for machining, assembly stations, welding stations, and stations for cleaning, inspection, and painting.
- 🚜 Material handling and storage systems are crucial for moving workpieces between workstations, providing temporary storage, and facilitating easy loading and unloading.
- 👷 Human resources in FMS manage and maintain the system, perform tasks that machines cannot do, and are involved in quality inspection, programming, and tool changing.
- 💻 The computer control system serves as an interface for human interaction, coordinates production traffic, and provides performance monitoring and diagnostics.
- 🔍 To qualify as an FMS, a system must pass tests on its ability to process different parts, adapt to changes, recover from malfunctions, and introduce new parts.
- 🏗️ FMS has evolved from the Industrial Revolution and is now an integral part of the move towards Industry 4.0, characterized by cyber-physical systems, smart factories, and AI.
Q & A
What is a Flexible Manufacturing System (FMS)?
-A Flexible Manufacturing System (FMS) is a highly automated group technology machine cell that includes one or more processing stations, typically CNC machines, interconnected by automated material handling and storage systems, and controlled by a distributed computer system.
Why is the system referred to as 'flexible'?
-The system is called 'flexible' because it can process different part styles simultaneously at various workstations and can adjust the design and quantities of production according to customer demand patterns. It can also quickly react to changes in design, schedule, or production volume.
What are the four basic components of an FMS?
-The four basic components of an FMS are: 1) Workstations, 2) Automated material handling and storage system, 3) Human resources, and 4) Computer control system.
What types of workstations are typically found in an FMS?
-Typically found workstations in an FMS include machining stations with CNC machines, loading and unloading stations, assembly stations or welding stations, and stations for cleaning, inspection, and painting.
How does the material handling and storage system function in an FMS?
-The material handling and storage system in an FMS is responsible for moving workpieces between workstations, handling various workpiece configurations, serving as a temporary storage system, and providing convenient access for loading and unloading at workstations.
What roles do human resources play in an FMS?
-Human resources in an FMS are responsible for managing and maintaining the system, performing tasks that cannot be done by machines, making complex decisions, quality inspection, programming, planning operations, and performing tasks like loading and unloading workpieces and tool changing.
What is the function of the computer control system in an FMS?
-The computer control system in an FMS serves as an interface between humans and other system components, coordinates inputs by human supervisors, controls production traffic and movement of workpieces, and provides performance monitoring and reporting. It can also conduct full diagnostics for the system.
How can a manufacturing system be qualified as an FMS?
-A manufacturing system can be qualified as an FMS if it can process different part styles in mixed model mode, readily accept changes in production schedule and quantities, recover quickly from equipment malfunctions or breakdowns, and introduce new parts with relative ease.
What are the three types of FMS categorized by the number of machines?
-The three types of FMS categorized by the number of machines are: 1) Single machine cell, 2) Flexible manufacturing cell, and 3) Flexible manufacturing system.
What are the key differences between the three types of FMS?
-The key differences between the three types of FMS are the number of machines, adaptability to change, ability to recover from breakdowns, and the ease of introducing new parts. The more machines a system has, the faster the cycle time and the higher the total volume of product that can be produced, but this also leads to higher investment costs.
What are the five categories of FMS layout?
-The five categories of FMS layout are: 1) Linear type or progressive type, 2) Loop type, 3) Letter type, 4) Open field type, and 5) Robot-centered type.
What are the benefits of using an FMS?
-Benefits of using an FMS include maximizing machine utilization, reducing factory workspace, increased responsiveness to changes, reduced inventory requirements, fewer machines needed for production, lower manufacturing lead time, reduced labor requirements, and the opportunity for unattended production.
What are the factors to consider when implementing an FMS?
-Factors to consider when implementing an FMS include the high capital investment required, the need for substantial pre-planning, the necessity for highly skilled labor for setup and maintenance, and the suitability of the system for group technology products.
Outlines
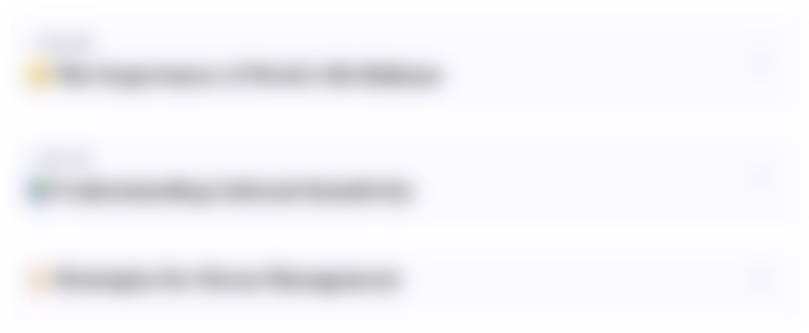
Этот раздел доступен только подписчикам платных тарифов. Пожалуйста, перейдите на платный тариф для доступа.
Перейти на платный тарифMindmap
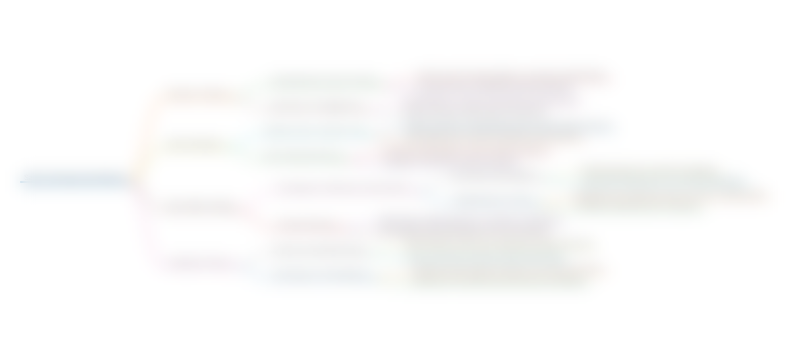
Этот раздел доступен только подписчикам платных тарифов. Пожалуйста, перейдите на платный тариф для доступа.
Перейти на платный тарифKeywords
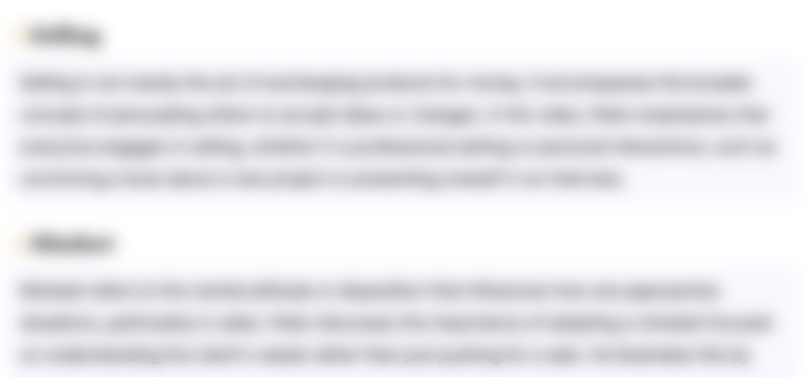
Этот раздел доступен только подписчикам платных тарифов. Пожалуйста, перейдите на платный тариф для доступа.
Перейти на платный тарифHighlights
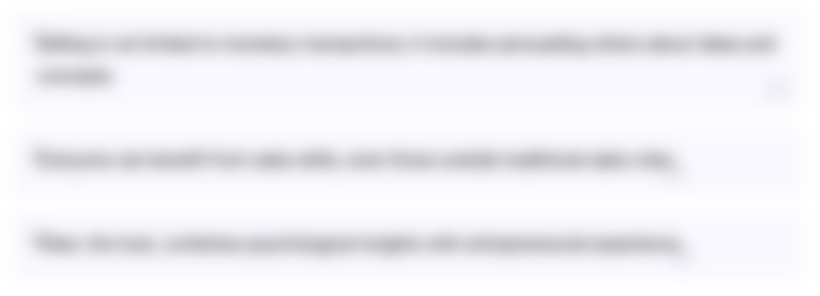
Этот раздел доступен только подписчикам платных тарифов. Пожалуйста, перейдите на платный тариф для доступа.
Перейти на платный тарифTranscripts
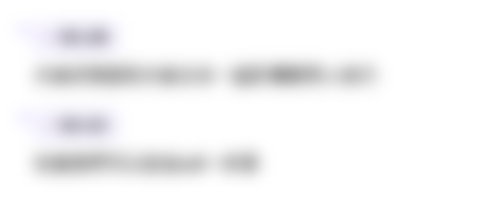
Этот раздел доступен только подписчикам платных тарифов. Пожалуйста, перейдите на платный тариф для доступа.
Перейти на платный тарифПосмотреть больше похожих видео
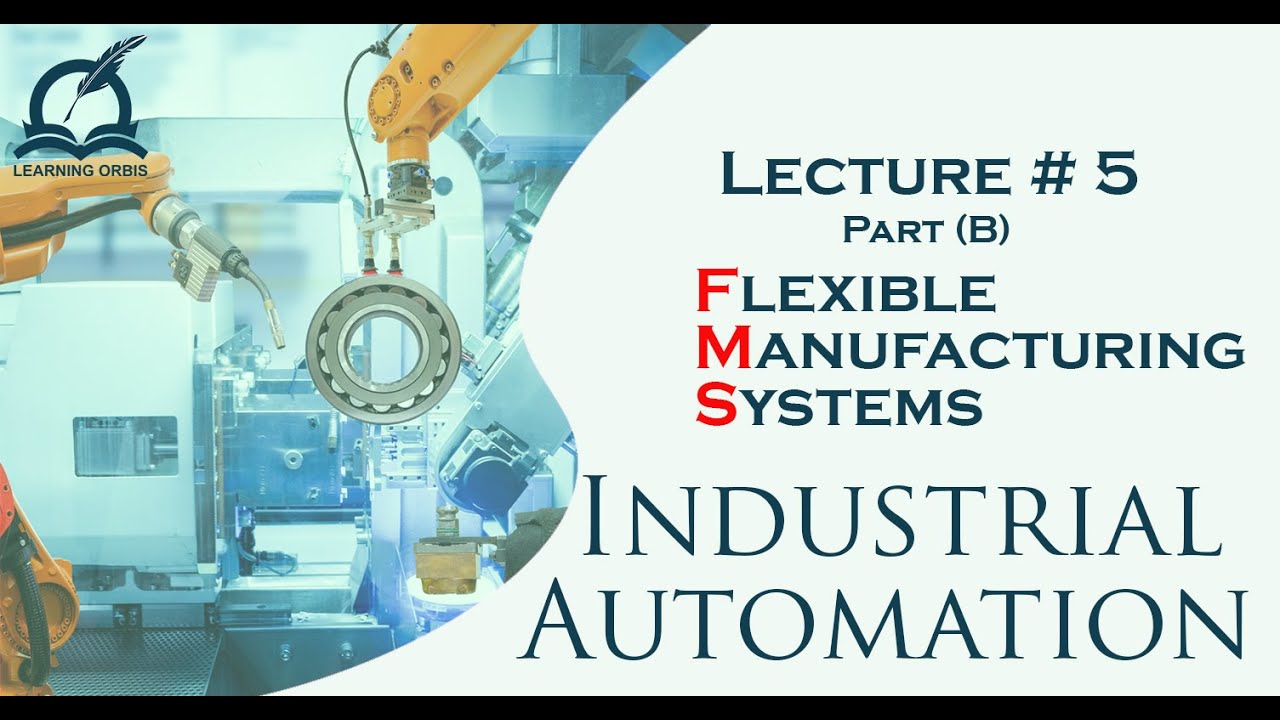
Flexible Manufacturing Systems | FMS | Industrial Automation
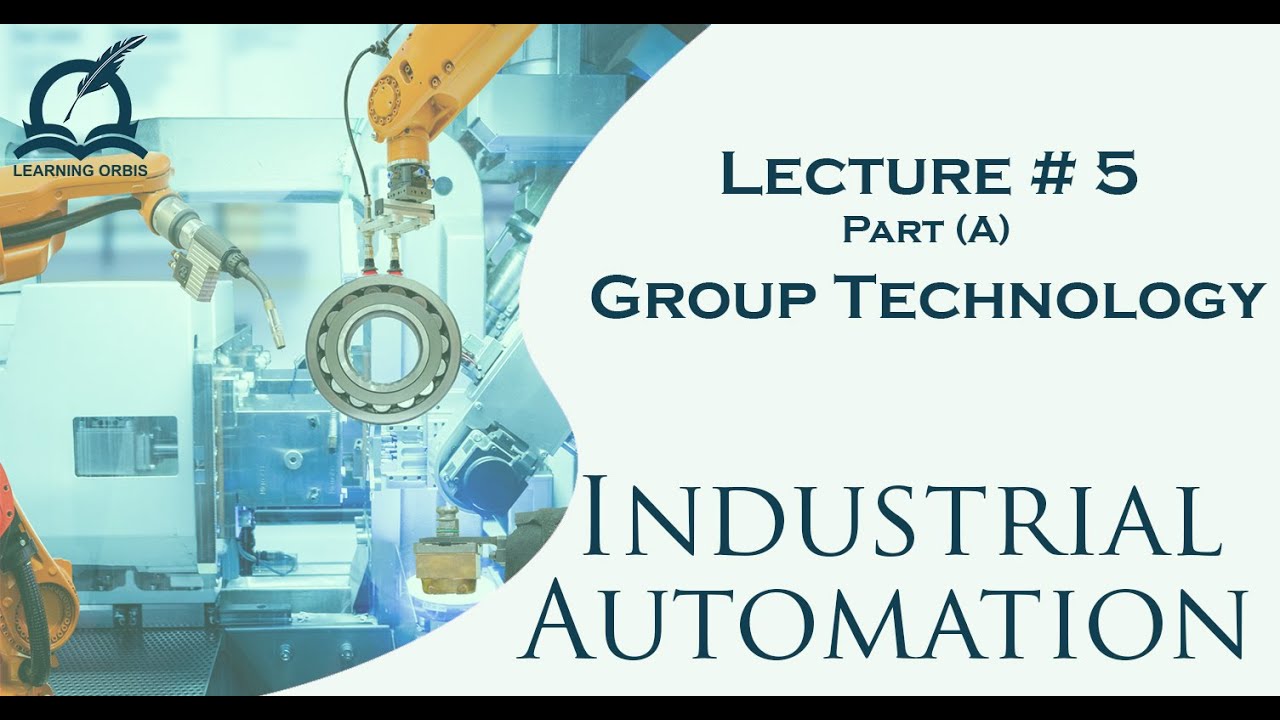
Group Technology | Industrial Automation
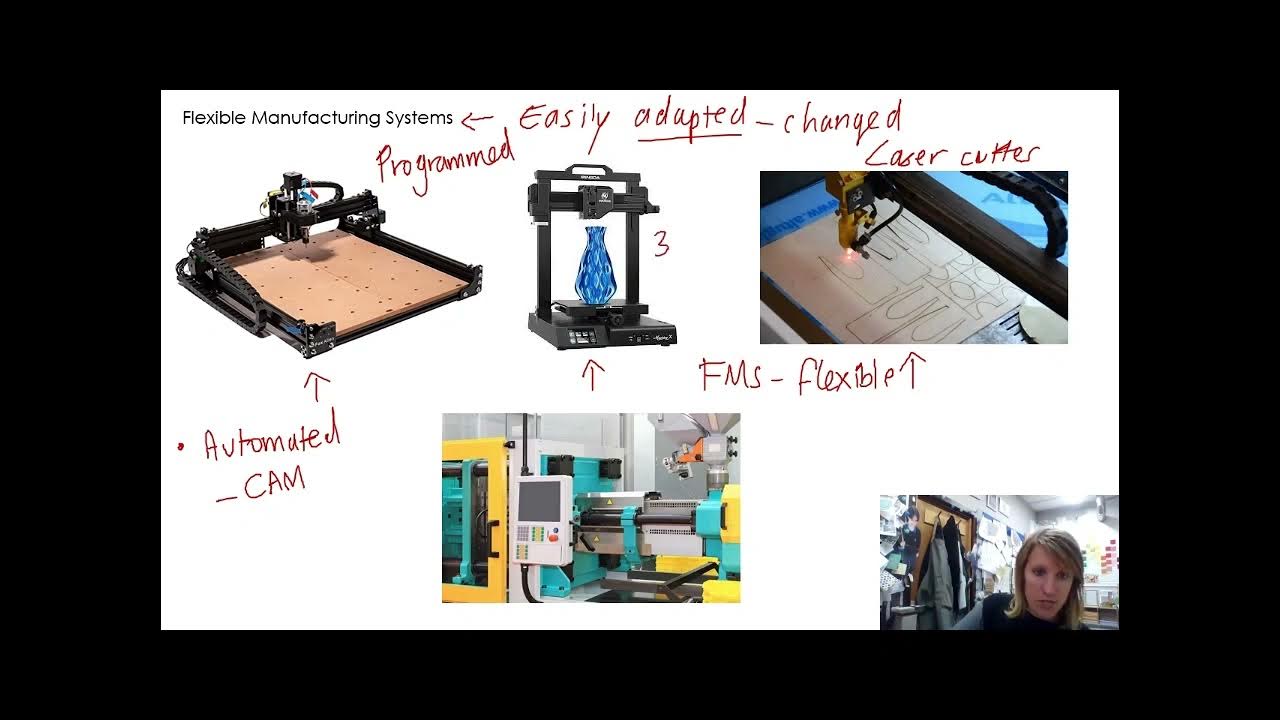
Video 2 - Flexible and Lean Manufacturing
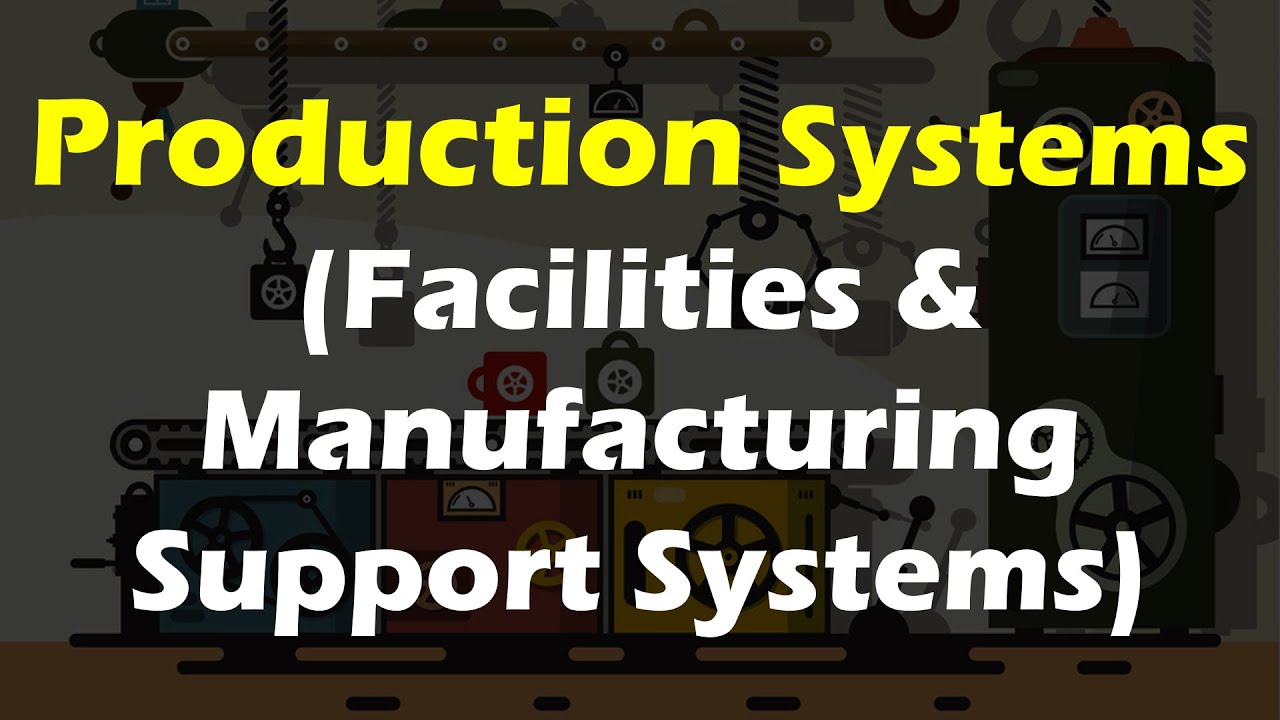
Production Systems - Facilities & Manufacturing Support Systems

Manufacturing Systems | Industrial Automation

AutoBill - An AI Powered Instant Checkout System | Edge Impulse | Raspberry Pi | Coders Cafe
5.0 / 5 (0 votes)