Tutorial / Cara Bubut Rata
Summary
TLDRIn this instructional video, the presenter explains the technique of flat turning, a machining process used to reduce the diameter of a workpiece by scraping the side surface. The video outlines the necessary tools, including the workpiece, cutting tool, and various wrenches. The presenter demonstrates how to set up the machine, establish a zero point, and make precise adjustments to achieve the desired diameter. With clear visuals and measurements, viewers gain insight into the process of achieving specific dimensions, highlighting the importance of accuracy in machining.
Takeaways
- 😀 The video explains the technique of flat turning in lathe machining.
- 🛠️ Flat turning involves reducing the diameter of a workpiece by machining the side surface.
- 📏 The process differs from face turning, which reduces the length of the workpiece.
- 🔧 Essential tools for flat turning include the workpiece, cutting tool, chuck key, and coolant.
- ⚙️ The lathe machine's rotation must be set in the correct direction for safe operation.
- 📐 Before machining, it's important to find the zero point of the cutting tool against the workpiece.
- 📉 The initial diameter of the workpiece is measured using a digital caliper for accuracy.
- 🔍 After turning, the diameter is measured again to assess the reduction achieved.
- 📝 The aim is to achieve desired dimensions according to the workpiece's technical drawings.
- 🙌 The video concludes with a brief summary of the flat turning process and thanks viewers.
Q & A
What is flat turning in machining?
-Flat turning is a machining technique that involves cutting the side surface of a workpiece to reduce its diameter.
How does flat turning differ from face turning?
-Flat turning reduces the diameter of the workpiece, while face turning decreases the length.
What tools are necessary for flat turning?
-The essential tools for flat turning include the workpiece, a cutting tool, a chuck key, a tailstock key, a caliper for measurement, and optional tools like a hammer and coolant.
Why is it important to ensure the lathe machine rotates in the correct direction?
-It's crucial to have the lathe rotate in the correct direction to prevent damage to the workpiece and the cutting tool.
What is the purpose of establishing a zero point with the cutting tool?
-Establishing a zero point allows for precise machining by ensuring that the cutting tool begins at a known reference position on the workpiece.
How much material is typically removed in one pass during flat turning?
-In the provided example, the cutting tool was moved 0.04 mm per pass to gradually reduce the diameter of the workpiece.
How is the success of flat turning measured?
-The success of flat turning can be measured by using a caliper to check the diameter before and after the machining process.
What was the initial diameter of the workpiece in the demonstration?
-The initial diameter of the workpiece was 24.601 mm.
What was the final diameter of the workpiece after flat turning?
-The final diameter of the workpiece after flat turning was 24.000 mm.
What are some applications of flat turning in machining?
-Flat turning is commonly used in manufacturing parts that require precise diameter specifications, such as shafts, spacers, and other cylindrical components.
Outlines
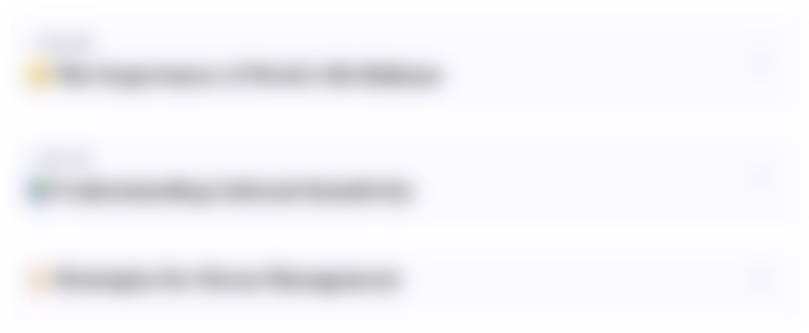
このセクションは有料ユーザー限定です。 アクセスするには、アップグレードをお願いします。
今すぐアップグレードMindmap
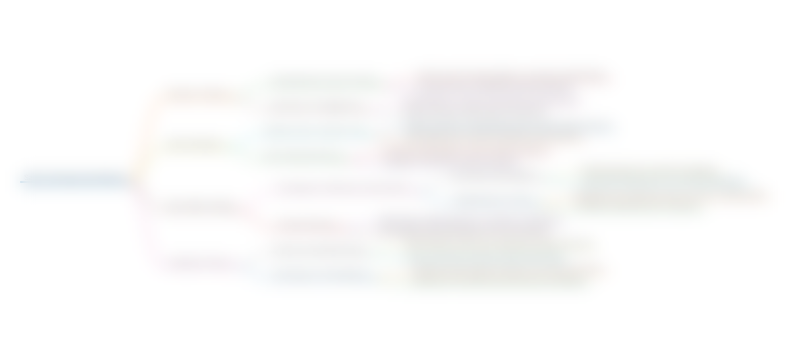
このセクションは有料ユーザー限定です。 アクセスするには、アップグレードをお願いします。
今すぐアップグレードKeywords
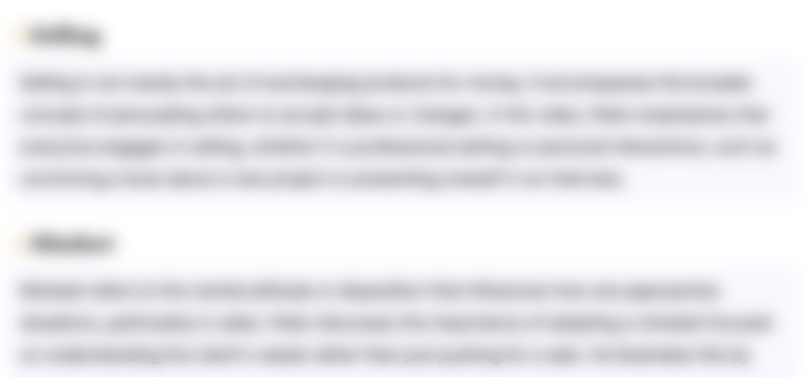
このセクションは有料ユーザー限定です。 アクセスするには、アップグレードをお願いします。
今すぐアップグレードHighlights
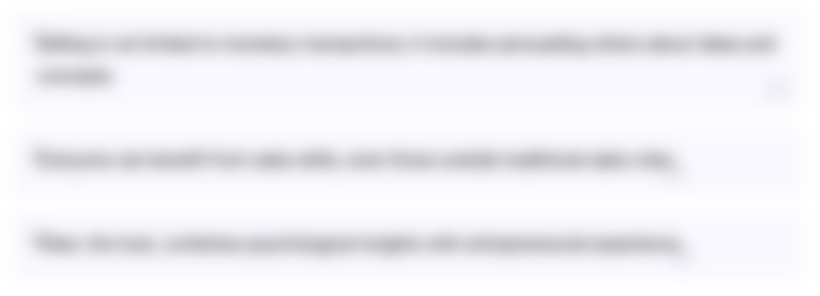
このセクションは有料ユーザー限定です。 アクセスするには、アップグレードをお願いします。
今すぐアップグレードTranscripts
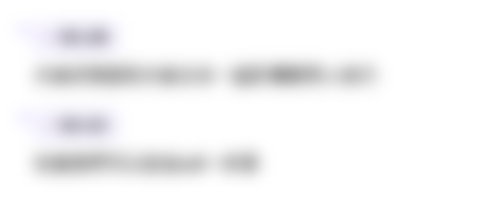
このセクションは有料ユーザー限定です。 アクセスするには、アップグレードをお願いします。
今すぐアップグレード5.0 / 5 (0 votes)