Job Facing Master CAM Mill
Summary
TLDRThis video tutorial walks viewers through the process of creating a job for CNC machining using Mastercam. It covers setting up the milling machine, selecting the proper tool settings, and defining the workpiece dimensions (50mm x 50mm). The instructor demonstrates how to set up stock, adjust spindle speed, and use a face mill tool for surface leveling. The video also explains the process of running a simulation to visualize the machining steps, followed by generating the CNC program. By the end of the tutorial, viewers will have a comprehensive understanding of the process for creating a milling job using Mastercam.
Takeaways
- 😀 The tutorial begins by setting up the CNC machine coordinates (X and Y axes) by pressing F9.
- 😀 A rectangle is drawn using the 'rectangle' tool and positioned at the center by clicking the 'ansor center' toolbar.
- 😀 The dimensions of the rectangle are set to 50 mm for both length and width, based on the job requirements.
- 😀 The machine type is selected by clicking 'mill' and choosing the 'default' option, followed by adjusting the properties in the machine settings.
- 😀 Tool settings are adjusted to define spindle speed at 1000 RPM, which determines how fast the spindle rotates during the milling process.
- 😀 The 'stock setup' dialog is used to define the dimensions of the material being worked on, with height set to 50 mm.
- 😀 The program focuses on surface milling (facing), with a cutting depth (set) of 2 mm to ensure a smooth, even surface.
- 😀 The user is shown how to apply a milling tool (face mill) from the library, adjusting its diameter and setting cutting parameters.
- 😀 The tool is configured by adjusting parameters such as feed rate (100), spindle speed (1000 RPM), and step size for cutting.
- 😀 A simulation is performed to visualize the cutting process and ensure the settings are correct, showing four passes to achieve a 2 mm cut depth.
- 😀 After the simulation, the CNC program is generated, and users can save and view the CNC code that corresponds to the milling job.
Q & A
What is the first step in creating a CNC milling job in Mastercam as described in the video?
-The first step is to display the X and Y coordinates by pressing the F9 key, which will show the axis with the red lines on the screen.
How is the rectangle drawn in Mastercam for the milling job?
-To draw the rectangle, the 'Rectangle' command is used. After selecting the command, click at the origin (0,0) and use the 'Anchor Center' toolbar to center the rectangle before setting the dimensions, such as 50mm for both width and height.
What is the purpose of selecting the machine type in the process?
-Selecting the machine type ensures the correct setup for the milling machine. In the video, the 'Thaif' machine is selected, followed by the default option for the milling machine group.
What does setting the spindle speed to 1000 RPM mean?
-Setting the spindle speed to 1000 RPM means the spindle will rotate at 1000 revolutions per minute during the milling operation.
How is the stock setup configured in Mastercam?
-The stock setup is configured by selecting the 'Bounding Box' option, and then setting the dimensions for the stock (50mm x 50mm). The height of the stock is also set to 50mm, and the thickness for the cutting process is defined as 2mm.
What is the purpose of selecting the 'User-Defined' option for spindle speed?
-The 'User-Defined' option allows for custom spindle speed settings. In this case, the spindle speed was manually set to 1000 RPM for the milling operation.
What is the significance of the 2D Coolpad Vasing setting?
-The 2D Coolpad Vasing setting is used to define the tool path for milling. It helps ensure the correct cutting process is applied to the designated area of the part.
Why is it important to select the correct tool, like the face mill, in the CNC milling process?
-Selecting the correct tool, such as the face mill, ensures that the milling operation can be performed correctly and efficiently. The face mill is used for surface finishing, making it ideal for the vasing operation described.
How are the tool parameters, like diameter, set in the milling job?
-The tool parameters, such as the diameter, are set by choosing the correct size based on the available tools in the shop. For example, if the shop has a 20mm face mill, that diameter would be input into the tool settings.
What steps are involved in the simulation of the CNC milling process in Mastercam?
-To simulate the CNC milling process, the 'Verify Selected Option' is clicked, and the simulation is played at a slow speed. This allows users to observe the material removal process and ensure everything works as expected.
Outlines
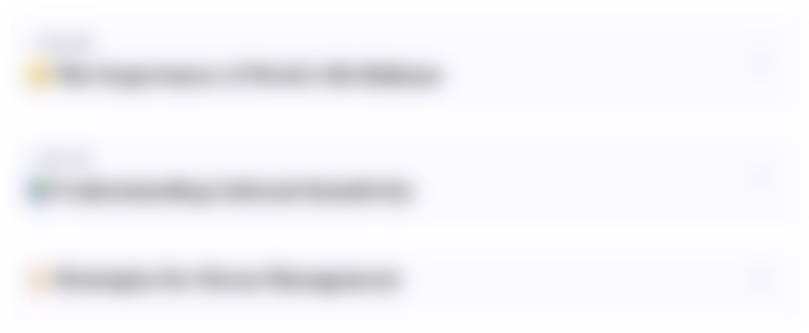
This section is available to paid users only. Please upgrade to access this part.
Upgrade NowMindmap
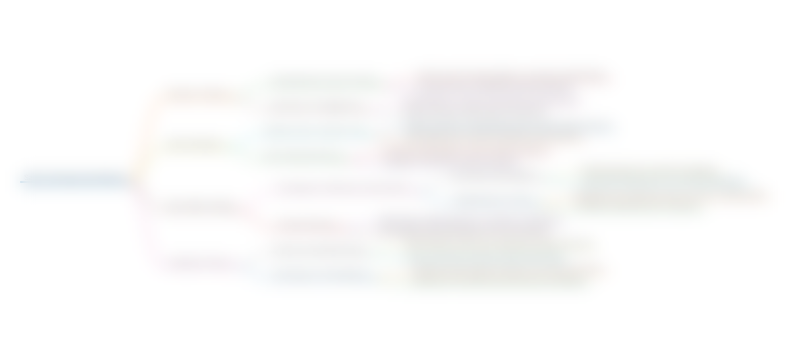
This section is available to paid users only. Please upgrade to access this part.
Upgrade NowKeywords
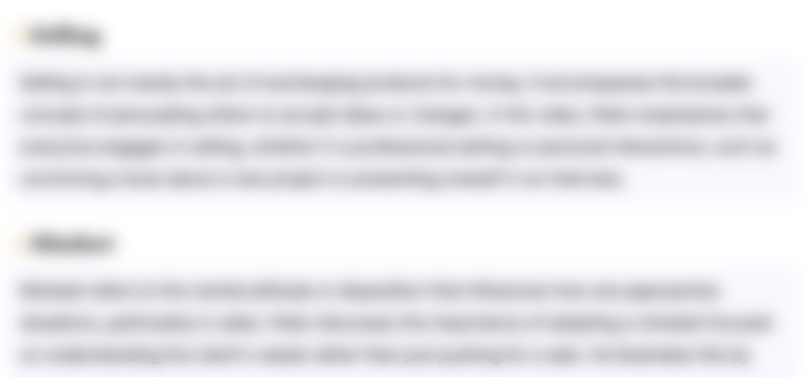
This section is available to paid users only. Please upgrade to access this part.
Upgrade NowHighlights
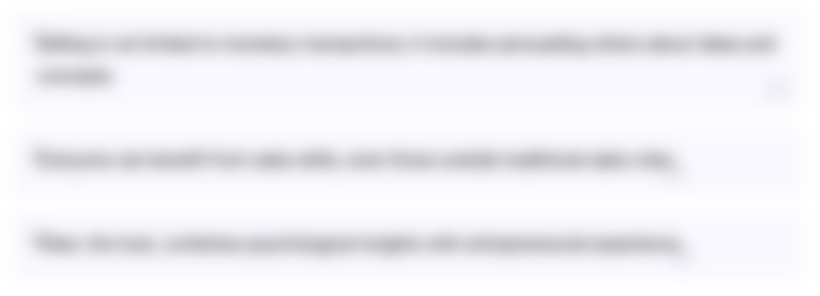
This section is available to paid users only. Please upgrade to access this part.
Upgrade NowTranscripts
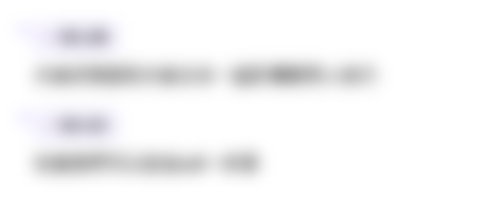
This section is available to paid users only. Please upgrade to access this part.
Upgrade NowBrowse More Related Video
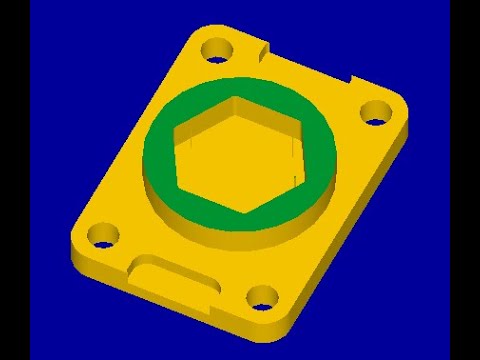
Tutorial Mastercam X5 CNC Mill / Fraish

Program CNC Turning Menggunakan MasterCAM X9 (Pembuatan PIN)
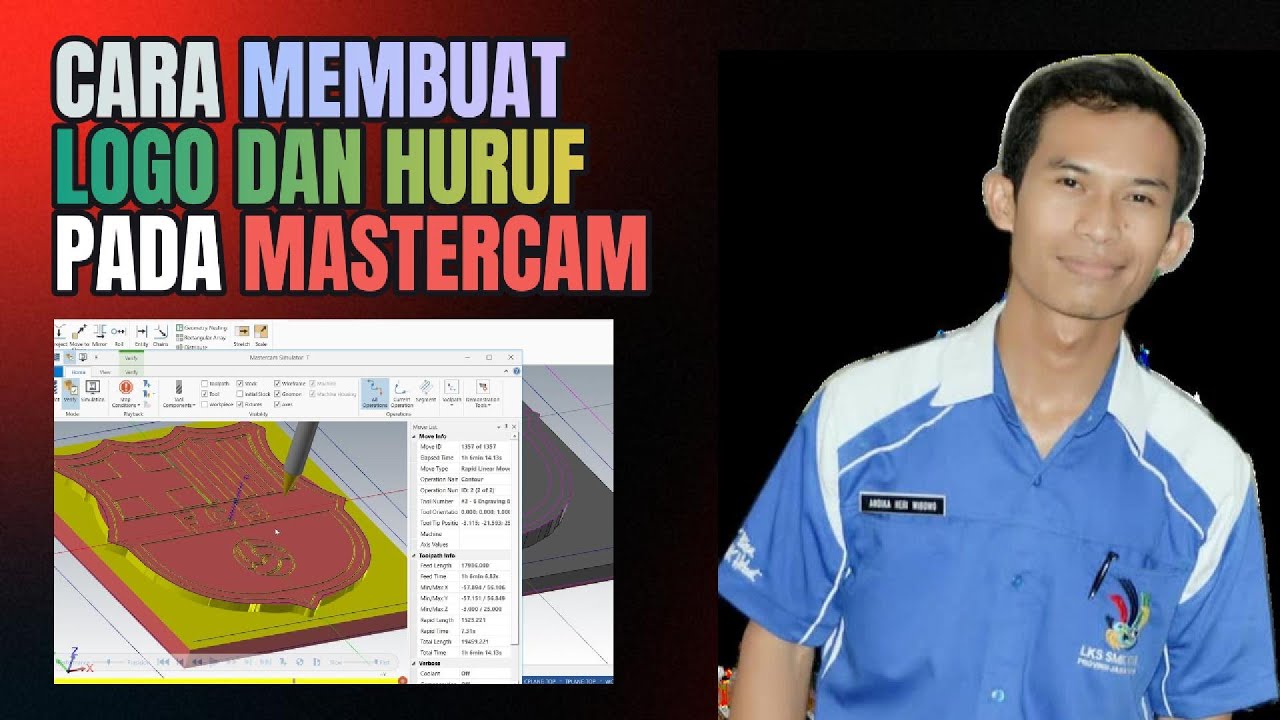
Cara membuat LOGO dan Tulisan pada software Mastercam 2017 - Logo Barcelona
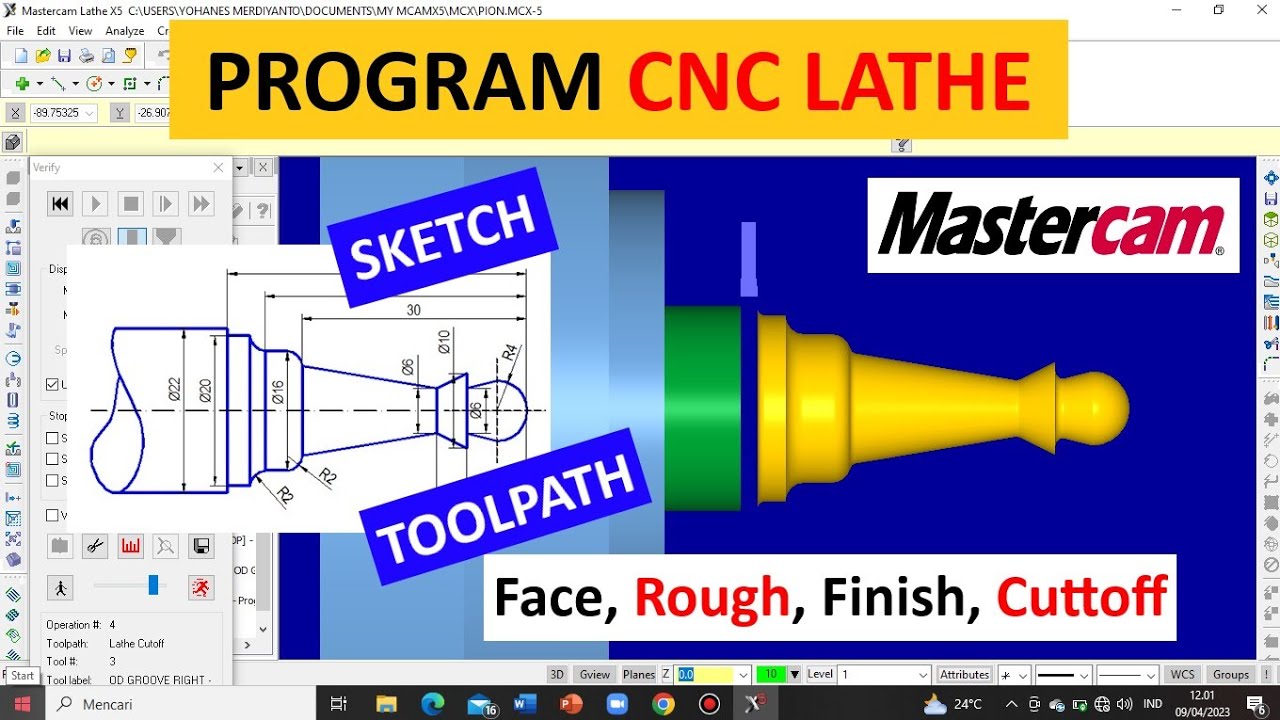
TUTORIAL MASTERCAM X5 MEMBUAT PION || CNC Turning (Lathe) || Simpel & Mudah dipahami !!
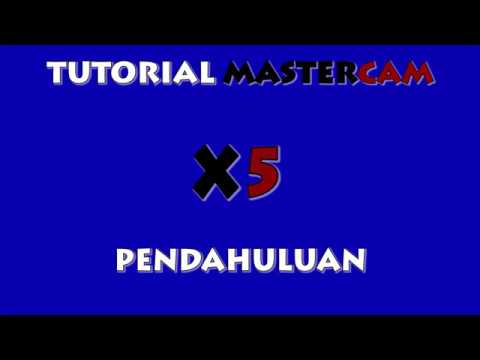
#1 - Pengenalan MasterCam
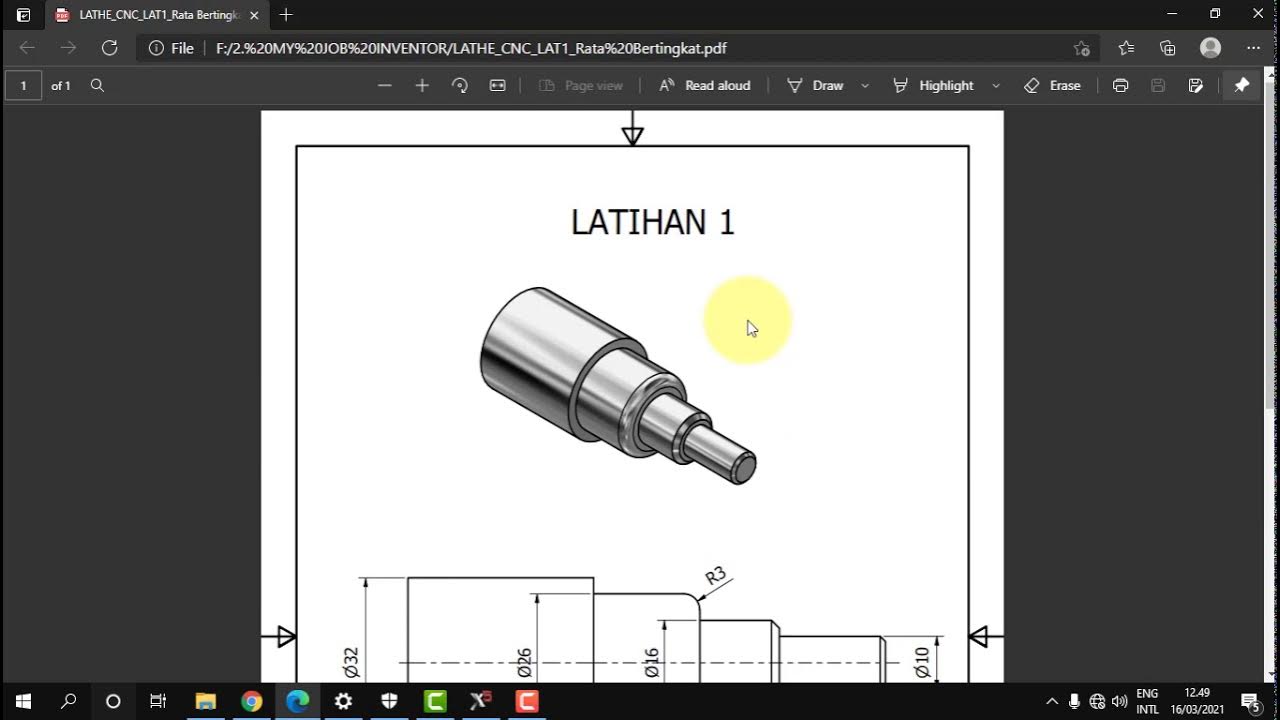
MASTERCAM X5_BUBUT DASAR BIDANG BERTINGKAT
5.0 / 5 (0 votes)