Pipe Rack Design for Piping : Essential Tips for Piping Engineers
Summary
TLDRThis video script discusses the critical role of pipe racks in industrial plants, which support pipes, electrical and instrument cables, and air coolers. It emphasizes the importance of pipe rack design in conjunction with piping design for operational efficiency, safety, and compliance. The script outlines the design process, including determining width, spacing, and elevations, and suggests reserving space for future growth. It also covers considerations for walkways, support spacing, and avoiding flat turns. The video concludes by highlighting the balance between structural integrity and efficient piping layout for safe and cost-effective systems.
Takeaways
- 🔩 Pipe racks are essential structures that carry pipes, electrical and instrument cables, and can also support air coolers.
- 🏗️ Proper design of piping within pipe racks is crucial for operational efficiency, safety, and regulatory compliance.
- 📐 Key elements for pipe rack design include P&ID flow diagrams, plot plans, layout specifications, client specifications, construction materials, fire protection requirements, and equipment details.
- 📏 A line routing diagram is necessary for preliminary piping routing, showing all pipeline cross-sections including line size, insulation, and line numbers.
- 🔄 Grouping pipes according to their systems is important to avoid designing overly wide pipe racks, with process lines typically at lower elevations and utility lines at upper elevations.
- 🌱 It's advisable to预留10%-20% space in pipe racks for future growth of piping lines.
- 🛗 The top level of pipe racks is generally reserved for electrical and instrumentation cable trays.
- 🚶♂️ Walkways on pipe racks serve multiple purposes, including cable pulling during construction and maintenance access during operation.
- 📏 Support spacing calculations are based on the average line size of pipes, influencing the choice of pipe rack column distances.
- 🚫 The use of flat turns should be avoided in favor of elevation differences for pipe track turns.
- 🔥 Fireproofing is typically required for pipe racks up to lower elevations, but must extend higher if equipment is located above the pipe rack.
Q & A
What is the primary function of pipe racks?
-Pipe racks are structures that carry pipes connecting process units and equipment. They also carry electrical and instrument cables and provide necessary supports for them. Additionally, they can be used to install air coolers.
What materials are pipe racks commonly made of?
-Pipe racks are generally made of steel, but they can also be made of concrete or a combination of concrete and steel.
Why is the design of piping within pipe racks important?
-Proper design of piping within pipe racks is crucial for ensuring operational efficiency, safety, and regulatory compliance.
What documents and details are needed to design a pipe rack?
-To design a pipe rack, one needs the P&ID flow diagram, plot plan, layout specification, client specification, construction material of the rack, fire protection requirement, and equipment details to be located around the Pipe Rack.
What is a line routing diagram and why is it important?
-A line routing diagram shows a preliminary piping routing between the equipment of the plant. It is important because it helps in grouping lines for process or fluid content and identifying the width of the Pipe Rack.
Why is it not advisable to line up all piping lines side by side in a pipe rack?
-Lining up all piping lines side by side would lead to designing a very wide pipe rack, which is neither financially nor technically correct. Instead, pipes should be grouped according to their systems.
What is the recommended practice for future growth of piping lines?
-It is suggested to keep 10% or 20% space for the possible growth of piping lines during the engineering phase of the project.
What is the purpose of the walkway on the top level of a pipe rack?
-The walkway can be used for cable pulling during construction, for maintenance requirements, and as an accessible path for passage through the pipe racks during operation.
How should the column distance of a pipe rack be determined?
-The column distance should be determined after deciding on the average line size and performing support spacing calculations based on that average size. It is also important to consult with civil and structural engineers.
What is the minimum height recommended for a pipe rack?
-The minimum height of the pipe rack should be decided according to the vehicle, forklift, or truck passing from the road under the pipe rack, generally not less than 3,600 mm.
How should pipe racks be designed to accommodate future expansion?
-Vertical risers should be kept away from the columns for horizontal expansions, and any piping line, cable tray, or support cannot be located over the pipe rack column due to future vertical expansion considerations.
Outlines
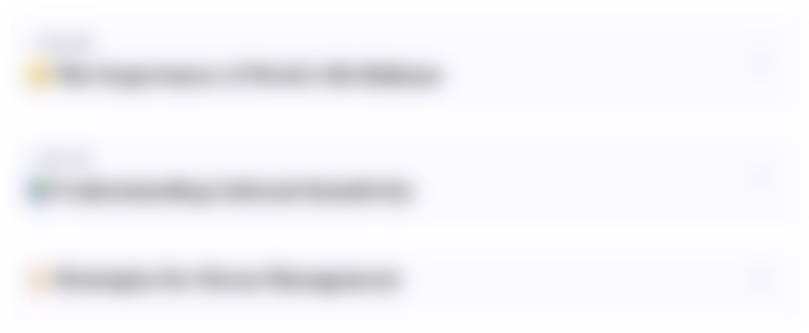
このセクションは有料ユーザー限定です。 アクセスするには、アップグレードをお願いします。
今すぐアップグレードMindmap
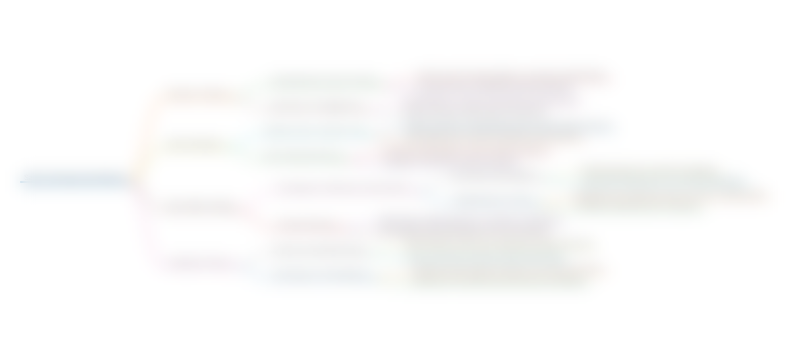
このセクションは有料ユーザー限定です。 アクセスするには、アップグレードをお願いします。
今すぐアップグレードKeywords
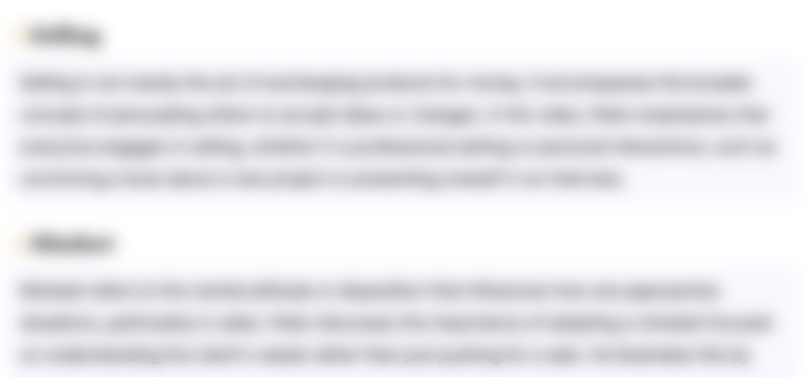
このセクションは有料ユーザー限定です。 アクセスするには、アップグレードをお願いします。
今すぐアップグレードHighlights
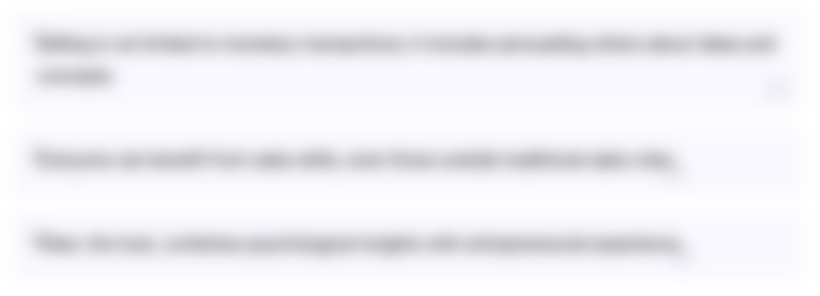
このセクションは有料ユーザー限定です。 アクセスするには、アップグレードをお願いします。
今すぐアップグレードTranscripts
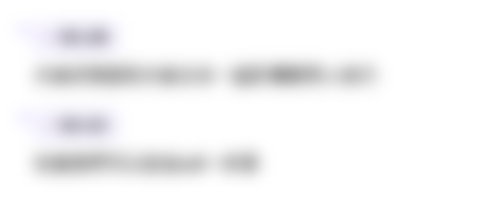
このセクションは有料ユーザー限定です。 アクセスするには、アップグレードをお願いします。
今すぐアップグレード5.0 / 5 (0 votes)