A Guided Tour of RETAL PA: Creating High-Quality, Responsible Packaging.
Summary
TLDRThis video offers a detailed virtual tour of Rittal's PA facility, guided by Matt Barker, the National Manager. It covers key areas like the visitor lobby, safety measures, PPE requirements, and various production areas. The tour highlights quality assurance processes, including machinery for testing caps, resin, and preforms. It showcases different production lines and equipment like injection molding machines, automated robots, and grinding systems for recycling plastic. Additionally, the video touches on Rittal's commitment to safety and quality through advanced monitoring systems, vision inspections, and environmentally conscious recycling processes.
Takeaways
- 👋 Welcome to the Rittal plant virtual tour led by Matt Barker, the National Manager.
- 🖥 Visitors must sign in using a touch screen kiosk, and the host will be notified via text or email.
- 📊 The Shot Scope monitoring system tracks real-time machine statuses, with color-coded indicators for operational status: green (running), red (down), and yellow (attention needed).
- 👔 The main office houses key staff, including the president, HR manager, supply chain manager, sales, finance, and planning teams.
- 👷♂️ Safety protocols include wearing PPE (toe covers, lab coats, beard nets, safety glasses) and no loose jewelry when entering the production area.
- 🔬 The quality assurance lab conducts tests on preforms and resin, using machines like the CMM, color spectrophotometer, and removal torque machine to ensure high-quality standards.
- 🏭 The plant’s PET production area uses 500 and 400 machines to produce parts, running multiple mold cavities and completing processes within seconds.
- 👁 The HDPE production area employs a vision system to ensure each piece meets quality standards before being packed.
- 🚂 Resin for production is delivered via rail cars and stored in silos, with each silo holding specific resin types.
- ♻ The plant uses a grinding system to recycle plastic scrap into reusable material, reducing waste and cutting costs.
Q & A
What is the primary purpose of the visitor kiosk in the lobby?
-The visitor kiosk is used for visitors to sign in using a touch screen. Once they sign in and select their host, the host will receive a text message or email indicating that the visitor is on-site.
What information does the Shot Scope monitoring system provide?
-The Shot Scope monitoring system tracks the real-time status of machines on the production floor. It shows whether machines are running (green), down (red), or need attention due to an issue (yellow).
What safety measures are required before entering the production floor?
-Visitors must wear appropriate PPE, which includes toe covers to prevent foot injuries, lab coats, beard nets, safety glasses, and hair nets. They are also required to wash their hands, and no loose jewelry is allowed except for a wedding ring.
What is the purpose of the quality assurance lab?
-The quality assurance lab tests preforms and caps for dimensional accuracy, clarity, color, gate thickness, and intrinsic viscosity. The lab also tests incoming resin samples to ensure they meet production standards.
What types of machines are used in PET production, and what is their function?
-In PET production, they use 500 and 400 injection molding machines. These machines can run different products and molds with various cavity configurations (e.g., 76 or 96 cavities). Each cycle produces 96 parts approximately every 9.5 seconds.
What is the process for ensuring quality in HDPE production?
-HDPE production involves a vision system that checks each piece for quality. The system ensures the parts are properly oriented, and any defects are detected before the parts move to final packaging.
How does the company apply ink to caps in the Desco top printing machine?
-The Desco top printing machine loads four different colored inks that are applied to the caps using heat. The caps are then checked by a vision system before being packaged.
What is the purpose of the laser etching machine?
-The laser etching machine is used to print under-the-cap codes for promotional purposes. The caps are loaded and oriented, and the codes are etched using a laser.
How does the company handle the resin unloading process from rail cars?
-Rail cars deliver resin, which is sampled and tested for quality before being unloaded. The resin is then stored in one of six silos, with the capability to load two silos simultaneously depending on production needs.
What is the role of the offline IMD resource system?
-The offline IMD resource system is used to inspect and sort suspended or quarantined totes from production. The system uses a vision system to detect defects like discoloration or contamination, and good parts are returned to the warehouse.
Outlines
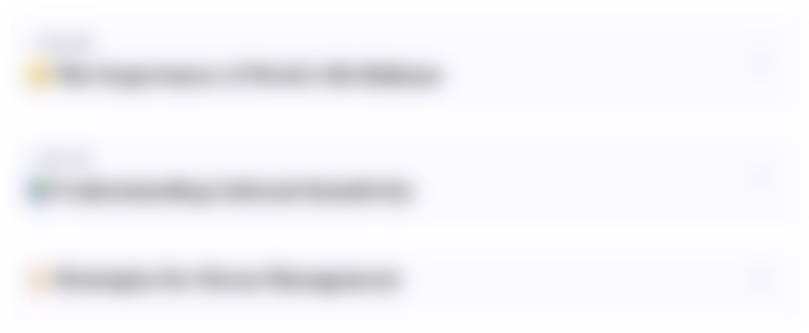
このセクションは有料ユーザー限定です。 アクセスするには、アップグレードをお願いします。
今すぐアップグレードMindmap
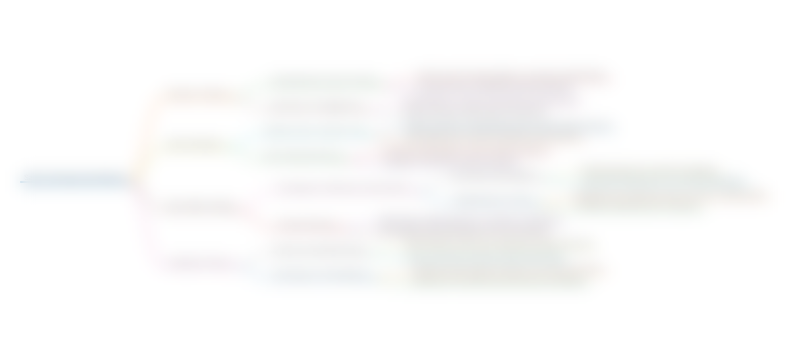
このセクションは有料ユーザー限定です。 アクセスするには、アップグレードをお願いします。
今すぐアップグレードKeywords
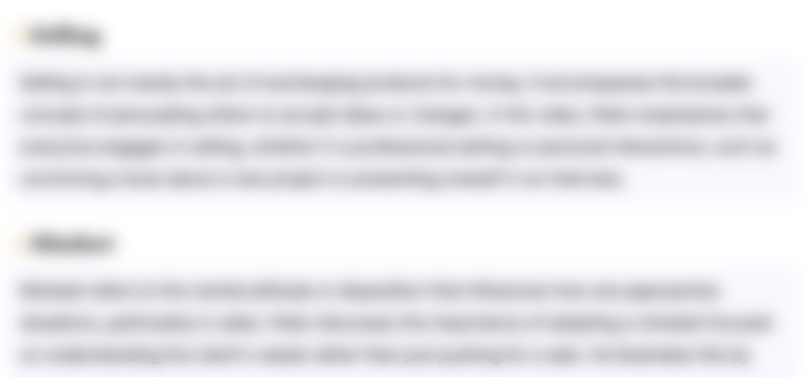
このセクションは有料ユーザー限定です。 アクセスするには、アップグレードをお願いします。
今すぐアップグレードHighlights
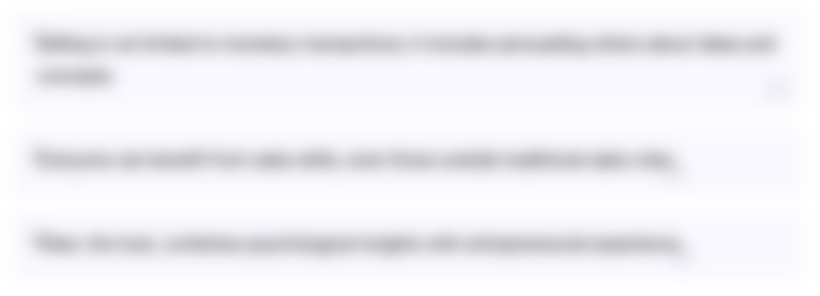
このセクションは有料ユーザー限定です。 アクセスするには、アップグレードをお願いします。
今すぐアップグレードTranscripts
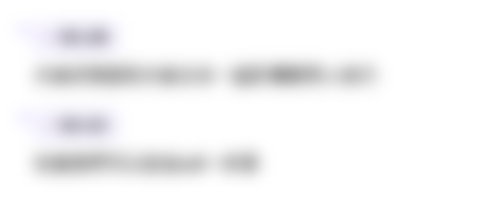
このセクションは有料ユーザー限定です。 アクセスするには、アップグレードをお願いします。
今すぐアップグレード関連動画をさらに表示
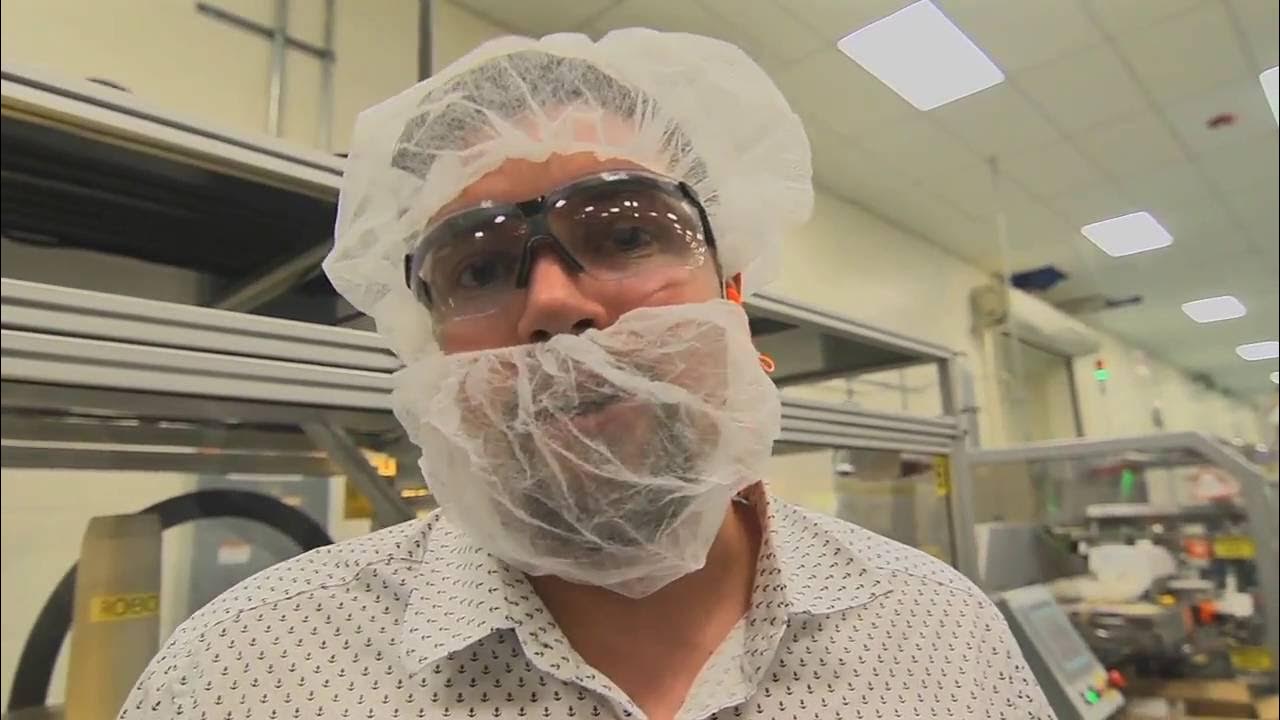
Medtronic
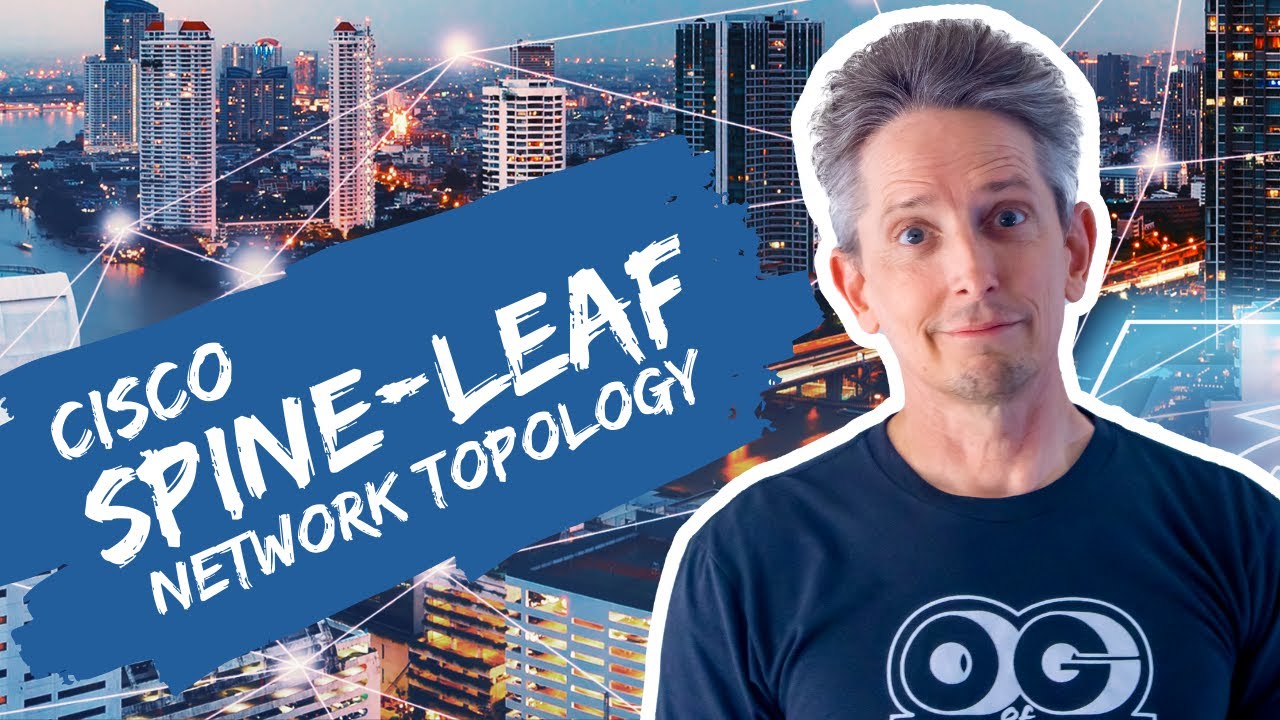
Cisco Spine-leaf Network Topology | Cisco CCNA 200-301

Lean Manufacturing - Lean Factory Tour - FastCap

How is Paper Recycled? Learn About the Recycling Process at Pratt Industries
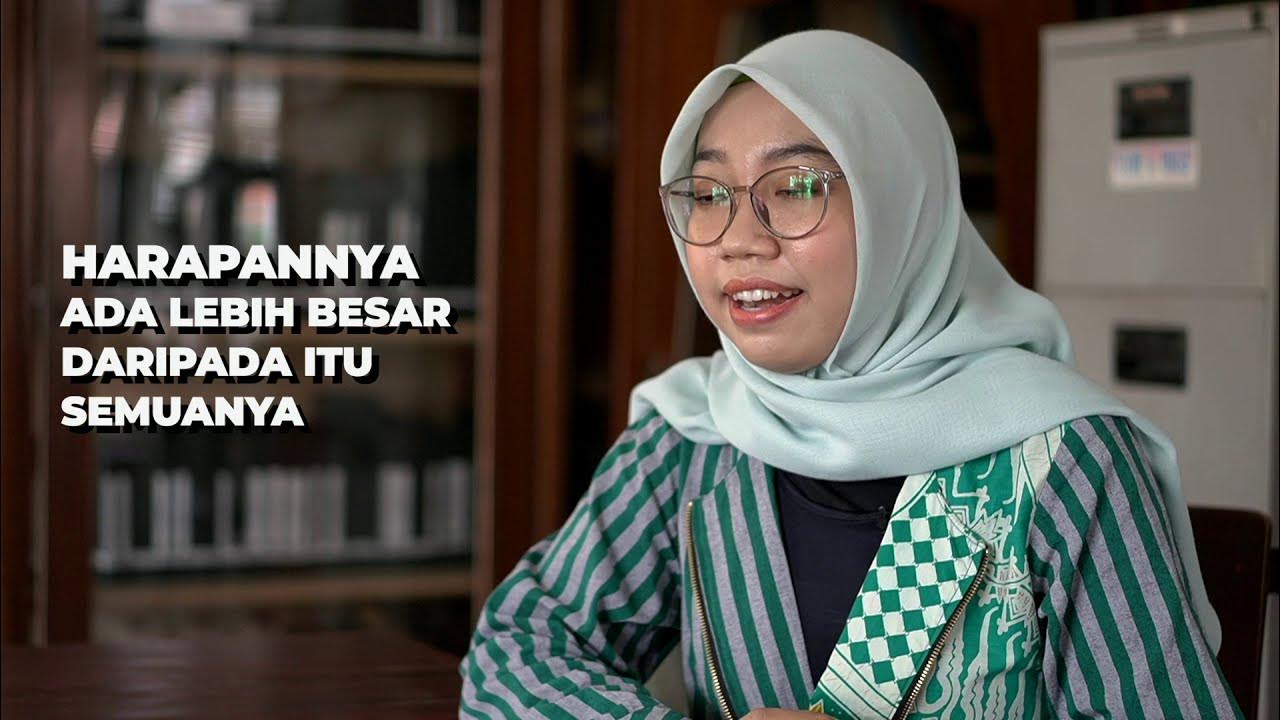
Virtual Tour Museum Ki Hajar Dewantara - Lumi Pictures
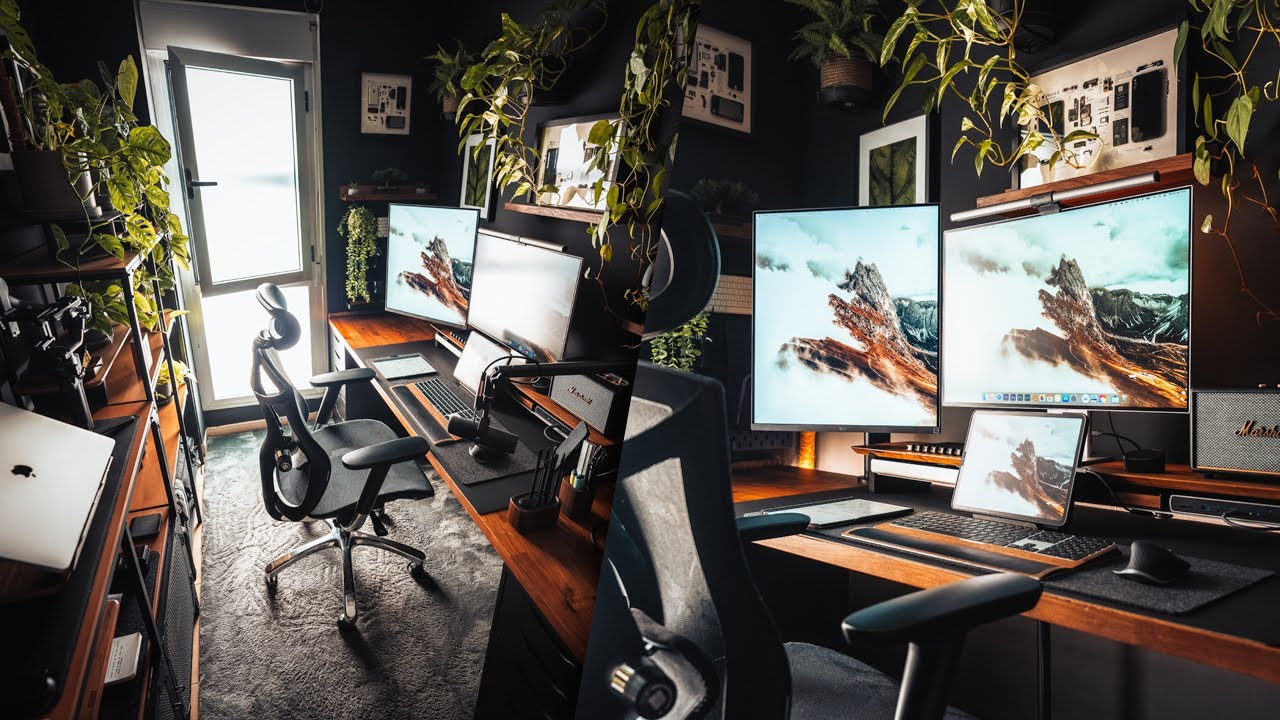
My 2023 Dark Aesthetic Home Office | Part 1: Desk Setup Tour
5.0 / 5 (0 votes)