Pipe Inspection and Testing requirements.
Summary
TLDRIn this video, Varun Patel provides a comprehensive overview of the various testing and inspection processes performed on pipes during and after manufacturing. The video covers heat treatment, non-destructive testing (NDT), destructive testing, metallurgical analysis, hydrostatic testing, and visual & dimensional inspection. It also touches on special tests for aggressive environments and concludes with a discussion on proper pipe marking requirements. Viewers are encouraged to watch additional related videos, subscribe for regular updates, and explore further resources on the Hardhat Engineer website.
Takeaways
- đ Heat treatment for pipes depends on whether they are hot finished or cold finished, with cold finished pipes requiring treatment according to ASTM standards.
- đ Non-Destructive Testing (NDT) methods ensure the soundness of pipes by checking for defects like cracks, porosity, or lack of fusion in welds and pipe bodies.
- đ Common NDT methods include Magnetic Particle Test, Eddy Current, Ultrasonic Testing, Radiography, and Positive Material Identification.
- đ Destructive testing is performed to assess the mechanical properties of the pipe, including tensile, bend, impact, and creep tests.
- đ Metallurgical tests, including micro and macro analysis, are conducted to ensure the pipe material complies with chemical and alloying element standards.
- đ Special tests are required for materials used in aggressive environments, including tests like Intergranular Corrosion (IGC) and Sulfide Stress Corrosion Cracking (SSC).
- đ Hydrostatic tests ensure that pipes are leak-proof and can withstand pressure, with test pressure determined by pipe dimensions and wall stress.
- đ Visual inspection is an important quality control method, checking for surface imperfections and weld defects like porosity and uneven beads.
- đ Dimensional inspection checks parameters like diameter, length, thickness, and straightness to ensure the pipe meets the applicable standards or purchaserâs specifications.
- đ After passing all tests, pipes are marked with essential information such as the manufacturer logo, material grade, size, and special markings like 'WR' for weld repair or 'NH' for non-hydro tested pipes.
Q & A
What types of tests are performed on pipes during and after manufacturing?
-Various tests are conducted during and after pipe manufacturing to ensure quality. These include Heat Treatment, Non-Destructive Testing (NDT), Destructive Testing, Metallurgical Testing, Hydrostatic Testing, Visual & Dimensional Inspections, and Marking.
What is the difference between heat treatment for hot finished and cold finished pipes?
-Hot finished pipes do not require heat treatment as the temperature remains within the required range during manufacturing. In contrast, cold finished pipes require heat treatment as they are either cold drawn or the temperature is not maintained in the hot finish range.
What are some common methods used for Non-Destructive Testing (NDT)?
-Common NDT methods include Flux Leakage Examination, Eddy Current Testing, Ultrasonic Testing, Radiography (only for welds), Magnetic Particle Testing for pipe ends and weld seams, and Positive Material Identification (PMI).
What is the purpose of destructive testing in pipe inspection?
-Destructive testing confirms the mechanical properties of the pipe. Tests like tensile, bend, flattening, impact, and creep tests evaluate the pipe's performance under stress, temperature, and deformation conditions.
What does metallurgical testing involve in pipe inspection?
-Metallurgical testing involves Micro and Macro analysis to ensure the chemical composition and fusion of the material meet the standards. It includes chemical analysis of raw material, product, and weld to confirm the alloying elements, and macro analysis to check proper weld fusion.
What is a Hydrostatic Test, and why is it performed?
-A Hydrostatic Test is conducted to ensure that the pipe is leak-proof and can withstand the required pressure. The test pressure is calculated based on pipe diameter, thickness, and wall stress, and it ensures the pipeâs strength under high-pressure conditions.
What is the significance of visual inspection in pipe manufacturing?
-Visual inspection is crucial to assess the overall finish of the pipe, checking for surface imperfections like mechanical marks, tears, or weld defects such as porosity and undercuts. This method ensures the visual quality of the product.
How are dimensional inspections of pipes conducted?
-Dimensional inspections involve measuring the pipe's diameter, length, thickness, straightness, ovality, and weight to ensure they conform to the required standards such as ASME B36.10 for welded and seamless pipes or ASME B36.19 for stainless steel pipes.
What types of markings are required on pipes after passing inspection?
-Once a pipe passes inspection, it must be marked with the manufacturer's logo, ASTM material code, material grade, size, thickness (schedule number), length, heat number, and any special markings like WR for weld repair or NH for non-hydro tested pipe.
What are the specific requirements for marking pipes based on material type?
-For carbon steel pipes, no hard punching is allowed below 6 mm thickness, while for stainless steel pipes, hard punching is prohibited below 12 mm thickness. Stenciling is also used for marking stainless steel pipes.
Outlines
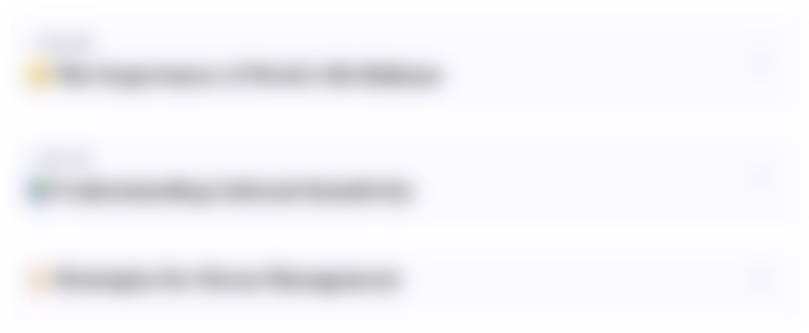
Cette section est réservée aux utilisateurs payants. Améliorez votre compte pour accéder à cette section.
Améliorer maintenantMindmap
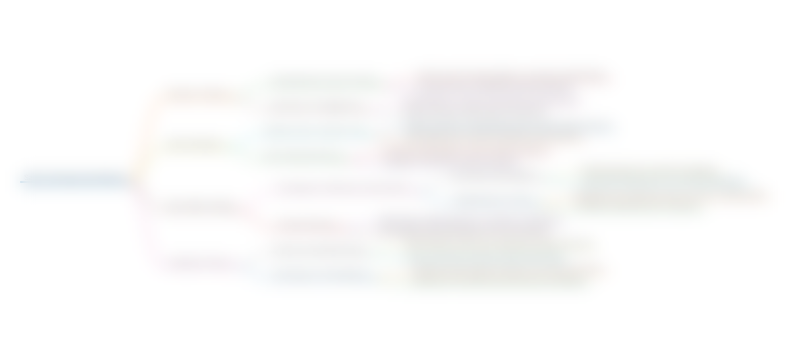
Cette section est réservée aux utilisateurs payants. Améliorez votre compte pour accéder à cette section.
Améliorer maintenantKeywords
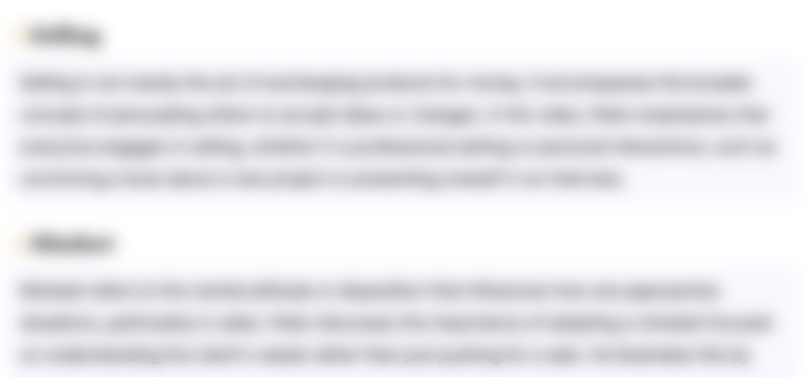
Cette section est réservée aux utilisateurs payants. Améliorez votre compte pour accéder à cette section.
Améliorer maintenantHighlights
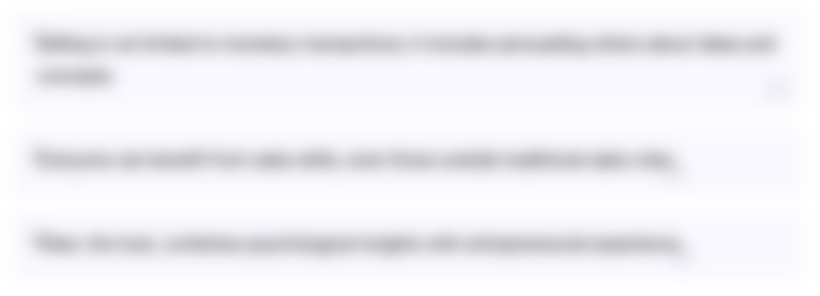
Cette section est réservée aux utilisateurs payants. Améliorez votre compte pour accéder à cette section.
Améliorer maintenantTranscripts
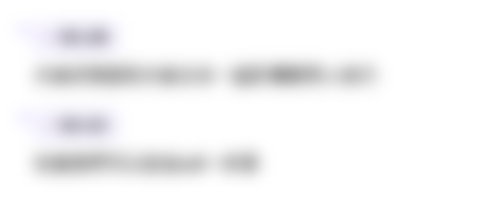
Cette section est réservée aux utilisateurs payants. Améliorez votre compte pour accéder à cette section.
Améliorer maintenantVoir Plus de Vidéos Connexes

Pipe Manufacturing Process for Welded Pipe (SAW & ERW)

Seamless Pipe Manufacturing Processes â Explained

Fundamental of Pipe (Pipeline) for Oil & Gas Engineer - Revised
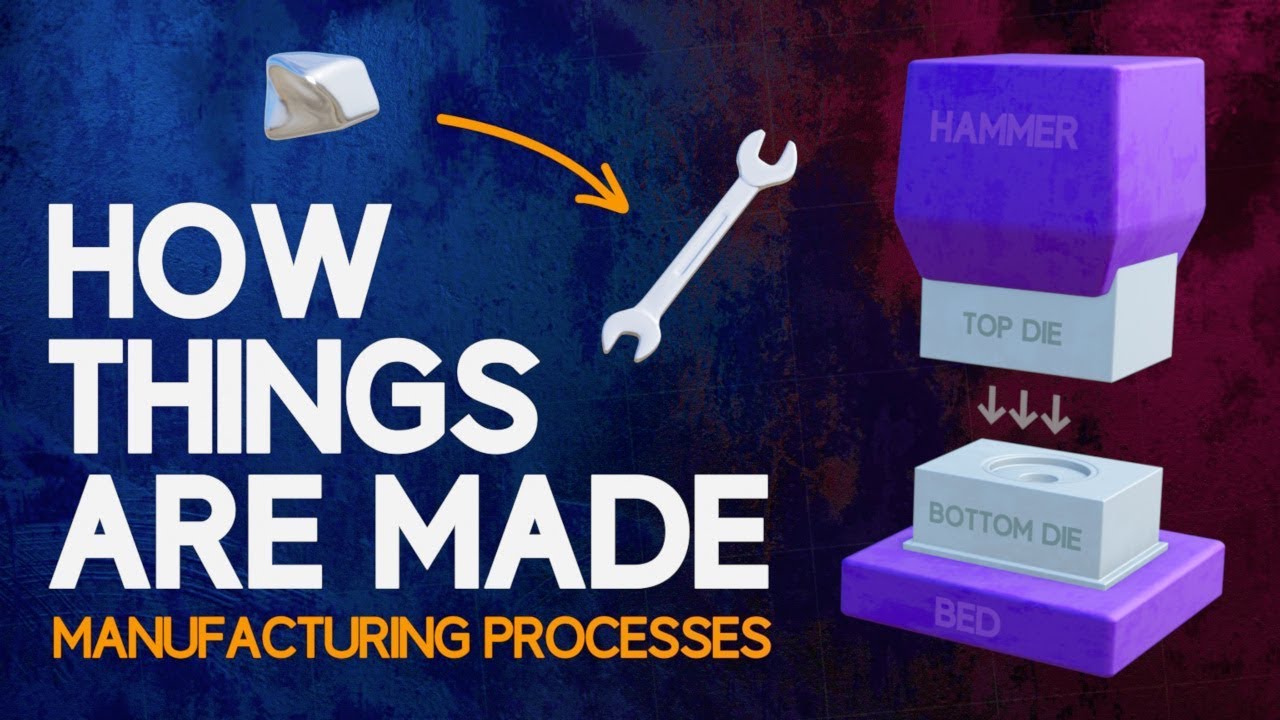
How Things Are Made | An Animated Introduction to Manufacturing Processes

Future Pipe Industries Manufacturing Facility Virtual Tour

Hardness Testing
5.0 / 5 (0 votes)