Pipe Manufacturing Process for Welded Pipe (SAW & ERW)
Summary
TLDRIn this video, Varun Patel explains the process of manufacturing welded pipes, covering techniques such as SAW, ERW, EFW, and HFW. He walks viewers through the stages of pipe formation, welding, heat treatment, and inspection, detailing how pipes are formed from plates or coils and welded using different methods. The video also highlights the differences between pipe types and their applications, including the use of filler material and various welding techniques. Throughout, Varun emphasizes the importance of quality checks, including non-destructive testing and hydro testing, before the pipes are packaged for use.
Takeaways
- 😀 Welded pipes are manufactured from plates or coils by forming them into circular sections and then welding them together.
- 😀 There are various welding methods for creating welded pipes, such as SAW (Submerged Arc Welding), ERW (Electric Resistance Welding), EFW (Electric Fusion Welding), and HFW (High-Frequency Welding).
- 😀 Welded pipes are more affordable compared to seamless pipes but tend to be weaker due to the weld joint.
- 😀 Welded pipes can be produced in large sizes without upper restrictions.
- 😀 Filler materials can be used in the welding process to produce long-radius bends and elbows.
- 😀 The rolling process for welded pipes involves applying pressure to form plates into circular sections, which can then be welded.
- 😀 SAW pipes can be manufactured with a single or double seam, with welding done both inside and outside of the pipe.
- 😀 Spiral SAW pipes, produced by forming a plate into a spiral loop, are used for low-pressure services, while straight SAW pipes are used for medium to high-pressure applications.
- 😀 After welding, pipes undergo heat treatment, non-destructive testing (NDT), and hydro testing to ensure their strength and leak-proof capability.
- 😀 ERW, EFW, and HFW pipes are welded using continuous rolling methods, where flat metal strips are formed into pipes and welded without filler material, though filler material can be used in the EFW process.
- 😀 Localized heat treatment, such as post-annealing, is carried out to restore the microstructure of the welded zone, ensuring optimal material properties.
Q & A
What are the main welding methods used in welded pipe manufacturing?
-The main welding methods used in welded pipe manufacturing are Submerged Arc Welding (SAW), Electric Resistance Welding (ERW), Electric Fusion Welding (EFW), and High-Frequency Welding (HFW).
How are welded pipes formed from a metal plate or coil?
-Welded pipes are formed by rolling a metal plate or continuous coil into a circular shape. The plate is either bent using rollers or processed with a point pressing method (UO method) to form a circular section, after which the pipe is welded.
What is the difference between single seam and double seam SAW pipes?
-In single seam SAW pipes, welding is done with the submerged arc welding process on a single seam. In double seam SAW pipes, two weld seams are created opposite each other, with both seams welded from the inside and outside of the pipe.
What is the purpose of heat treatment in the welded pipe manufacturing process?
-Heat treatment is performed after welding to relieve stresses, improve the mechanical properties of the weld, and ensure the pipe's strength. It may be done on the weld area or the entire body of the pipe, depending on the pipe thickness.
What are the non-destructive testing (NDT) methods used in welded pipe manufacturing?
-The non-destructive testing (NDT) methods used in welded pipe manufacturing include Radiographic Testing (RT) and Ultrasonic Testing (UT). These methods ensure the integrity and soundness of the weld material.
Why are welded pipes generally cheaper than seamless pipes?
-Welded pipes are cheaper than seamless pipes because they are produced by welding a rolled plate or coil, whereas seamless pipes require more complex processes to form a continuous pipe without seams.
What is the primary advantage of welded pipes in terms of size production?
-Welded pipes can be manufactured in large sizes without upper restrictions, making them more versatile for different applications compared to seamless pipes.
What is the key difference between spiral SAW pipes and straight SAW pipes?
-Spiral SAW pipes are formed by rolling steel plates into a spiral shape and are typically used for low-pressure services, while straight SAW pipes are used for medium to high-pressure services. Spiral pipes are less costly than straight pipes.
How does the ERW welding process work in welded pipe production?
-In ERW welding, two copper electrodes apply pressure and high current to a flat metal strip, heating the joint to its melting point. The semi-molten surfaces fuse together, creating a strong weld without the need for filler material.
What is the purpose of post-annealing in welded pipe manufacturing?
-Post-annealing is a localized heat treatment applied to the welded zone to restore the microstructure of the pipe after welding, helping to reduce the negative effects of the welding process.
Outlines
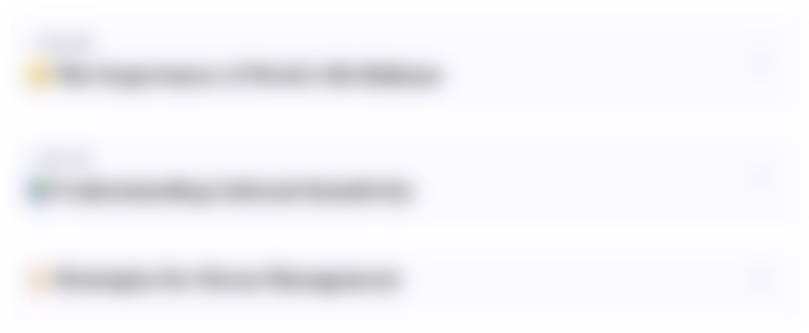
This section is available to paid users only. Please upgrade to access this part.
Upgrade NowMindmap
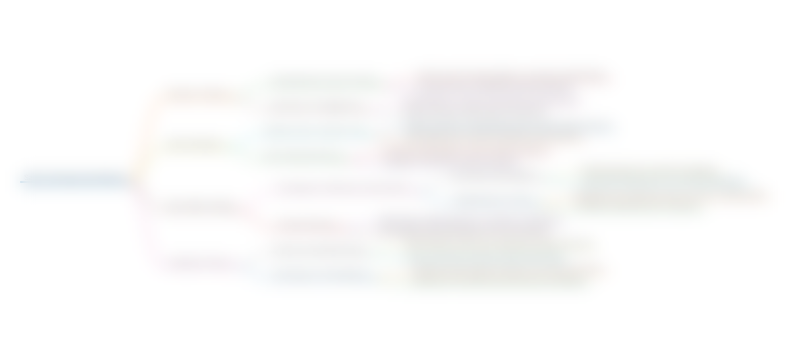
This section is available to paid users only. Please upgrade to access this part.
Upgrade NowKeywords
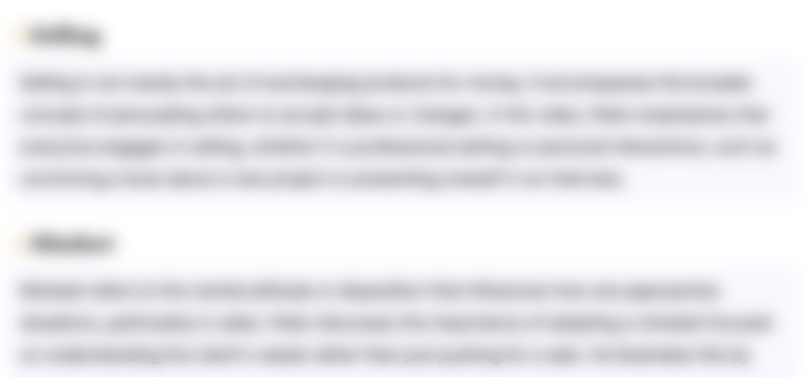
This section is available to paid users only. Please upgrade to access this part.
Upgrade NowHighlights
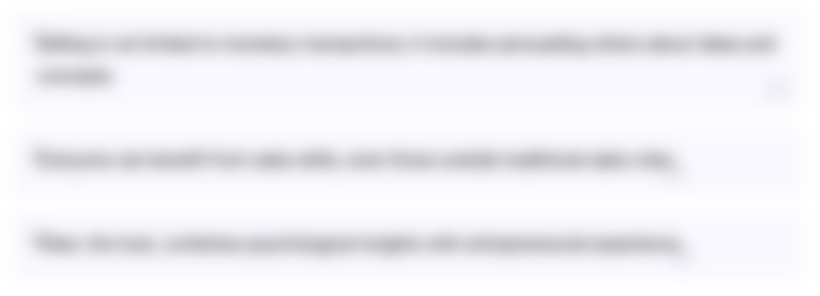
This section is available to paid users only. Please upgrade to access this part.
Upgrade NowTranscripts
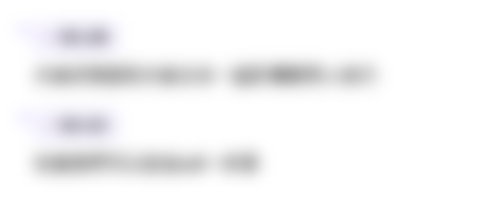
This section is available to paid users only. Please upgrade to access this part.
Upgrade NowBrowse More Related Video

Seamless Pipe Manufacturing Processes – Explained

Fundamental of Pipe (Pipeline) for Oil & Gas Engineer - Revised
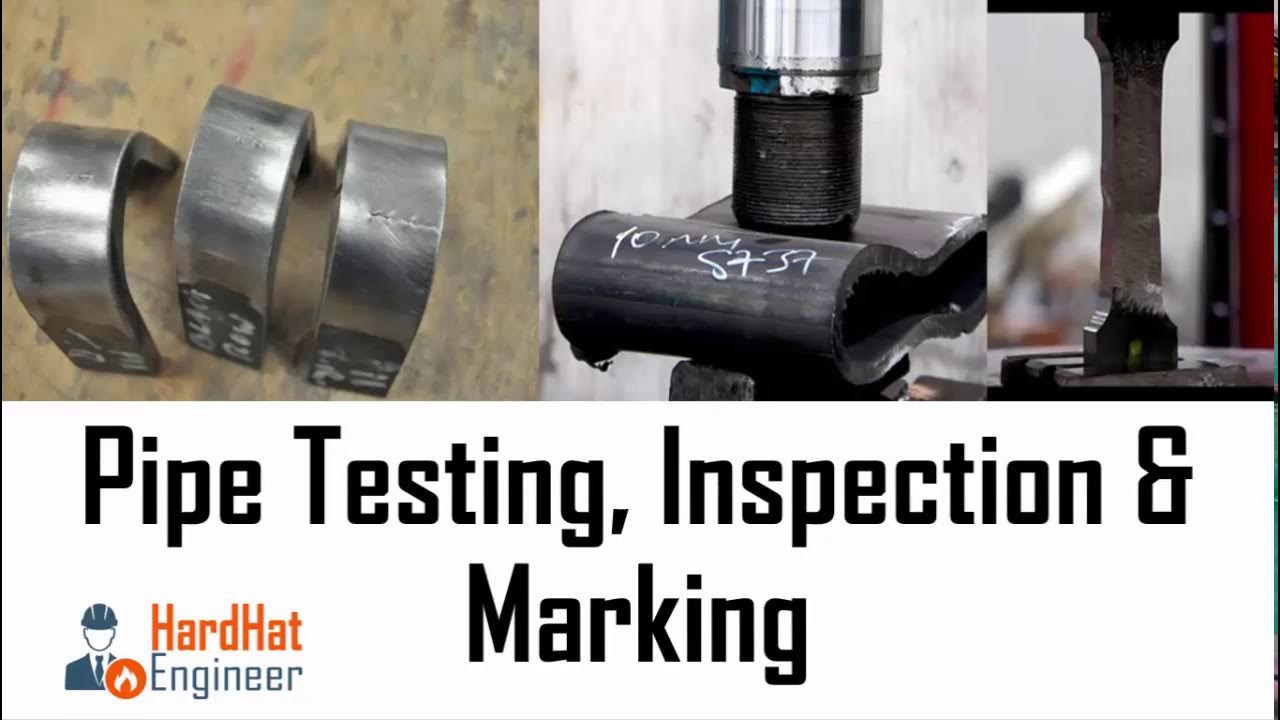
Pipe Inspection and Testing requirements.

How to Read Process Flow Diagrams (PFDs/PFS) - A Complete Tutorial
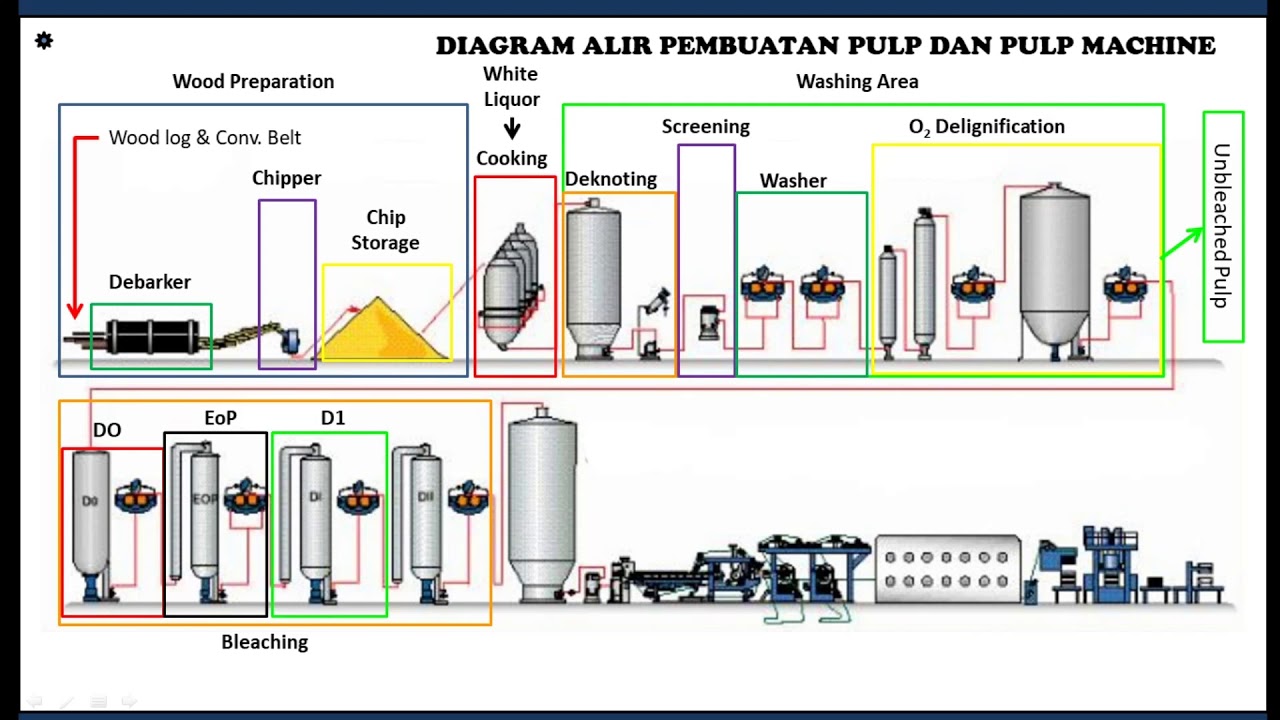
Kimia Industri - Pembuatan Pulp dan Kertas (Diagram Alir proses) (Bag. 2 - Akhir)

Weld metal-1
5.0 / 5 (0 votes)