What is Predictive Maintenance? - Introduction to Condition Monitoring & Condition Based Maintenance
Summary
TLDRThis lecture introduces the concept of predictive maintenance, also known as condition-based maintenance, which involves monitoring the condition of equipment using sensors to predict potential failures. Key to this method is condition monitoring, where data like vibration, temperature, and pressure are collected to assess the health of machinery. For example, in industrial pumps, vibration levels indicate pump condition, with deviations signaling the need for maintenance. The system alerts maintenance teams when issues are predicted, enabling proactive repair or replacement to prevent failure. This process can be applied to various equipment, with the chosen monitoring method tailored to each machine's characteristics.
Takeaways
- đ Predictive maintenance (condition-based maintenance) involves taking proactive maintenance actions based on predictions of potential equipment failures.
- đ Maintenance actions in predictive maintenance are initiated when a system predicts that a machine is about to fail.
- đ Condition monitoring is the most common method used for predictive maintenance, relying on real-time data collection to assess equipment health.
- đ Sensors and measuring devices are installed on equipment to monitor parameters like vibration, temperature, and pressure to identify faults.
- đ Vibration is a key indicator for rotary equipment like pumps, as high vibrations often indicate degrading components.
- đ A vibration sensor connected to a computer system allows for continuous monitoring of equipment health, generating real-time data.
- đ If vibration readings exceed defined normal ranges, the system alerts the maintenance team to take action, such as replacing a bearing.
- đ Other operational parameters like temperature and pressure can be monitored for different types of machinery, depending on the failure indicators.
- đ The choice of what to measure in condition monitoring depends on the specific equipment and the most reliable predictor of failure.
- đ Predictive maintenance helps reduce unplanned downtime and prevent costly equipment failures by addressing issues before they escalate.
- đ The main goal of predictive maintenance is to enhance equipment reliability by using data-driven insights to predict and prevent problems.
Q & A
What is predictive maintenance?
-Predictive maintenance is a type of maintenance where actions are taken based on predictions of equipment failure. Maintenance is performed when a predictive system signals that a machine is likely to fail soon.
Why is predictive maintenance also called condition-based maintenance?
-It is called condition-based maintenance because it typically relies on monitoring the condition of equipment using various sensors and predictive systems to determine when maintenance is needed.
What is the main method used in predictive maintenance?
-The main method used in predictive maintenance is condition monitoring, which involves installing sensors and measuring devices on equipment to gather data that indicates the equipmentâs health.
What types of data are commonly collected in condition monitoring?
-Common types of data collected in condition monitoring include measurements of vibration, temperature, pressure, and other operating parameters of the equipment.
How does condition monitoring work for an industrial pump?
-For an industrial pump, the most relevant parameter to monitor is vibration. A pump in good condition will have low and stable vibrations. Any increase in vibrations can indicate potential failure, allowing for early intervention.
Why are vibrations considered a good measure of a pump's condition?
-Vibrations are a good measure of a pumpâs condition because they directly correlate with the internal components' health. A pump in good condition will have minimal vibrations, whereas degraded components lead to higher vibrations.
How is vibration data used in predictive maintenance for pumps?
-A vibration sensor is installed on the pump, sending real-time vibration data to a computer system. The system monitors the data, comparing it to predefined normal limits. If the vibrations exceed these limits, it triggers a message for maintenance action.
What action is taken when a pump's vibration exceeds the normal limits?
-When the pumpâs vibration exceeds the normal limits, the system alerts the maintenance department to inspect the pumpâs bearings and replace them to prevent failure.
Are vibrations the only parameter monitored in predictive maintenance?
-No, other parameters like temperature and pressure may also be monitored, depending on the type of equipment and the specific variables that best predict potential failures.
How does the system decide what parameter to monitor for a particular piece of equipment?
-The system selects the most relevant parameter to monitor based on the type of equipment and the operating conditions that are most likely to indicate a failure, ensuring accurate predictions of maintenance needs.
Outlines
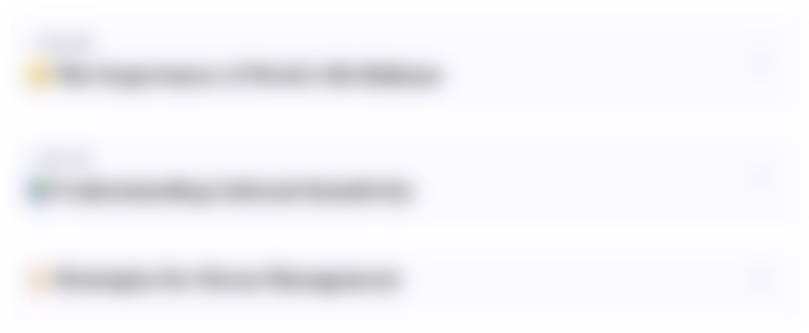
Cette section est réservée aux utilisateurs payants. Améliorez votre compte pour accéder à cette section.
Améliorer maintenantMindmap
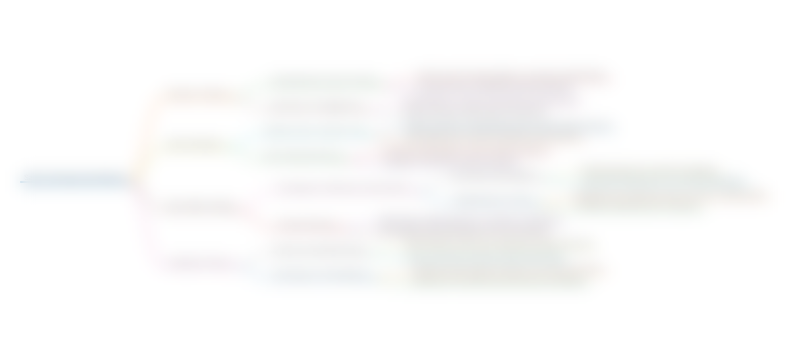
Cette section est réservée aux utilisateurs payants. Améliorez votre compte pour accéder à cette section.
Améliorer maintenantKeywords
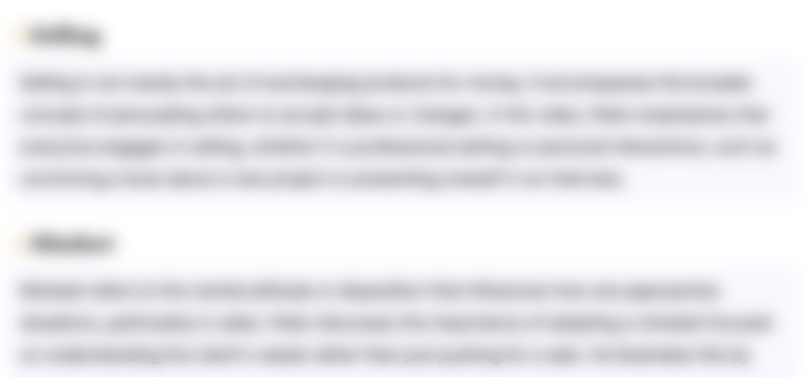
Cette section est réservée aux utilisateurs payants. Améliorez votre compte pour accéder à cette section.
Améliorer maintenantHighlights
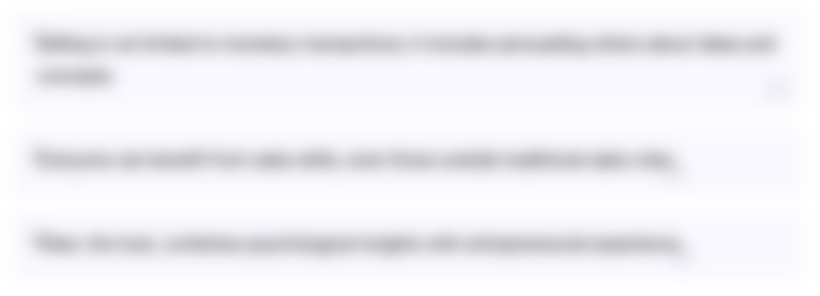
Cette section est réservée aux utilisateurs payants. Améliorez votre compte pour accéder à cette section.
Améliorer maintenantTranscripts
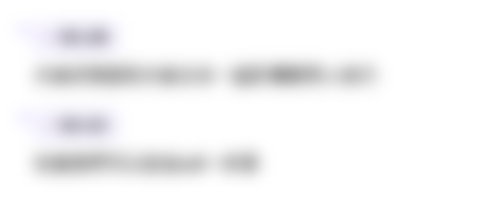
Cette section est réservée aux utilisateurs payants. Améliorez votre compte pour accéder à cette section.
Améliorer maintenantVoir Plus de Vidéos Connexes
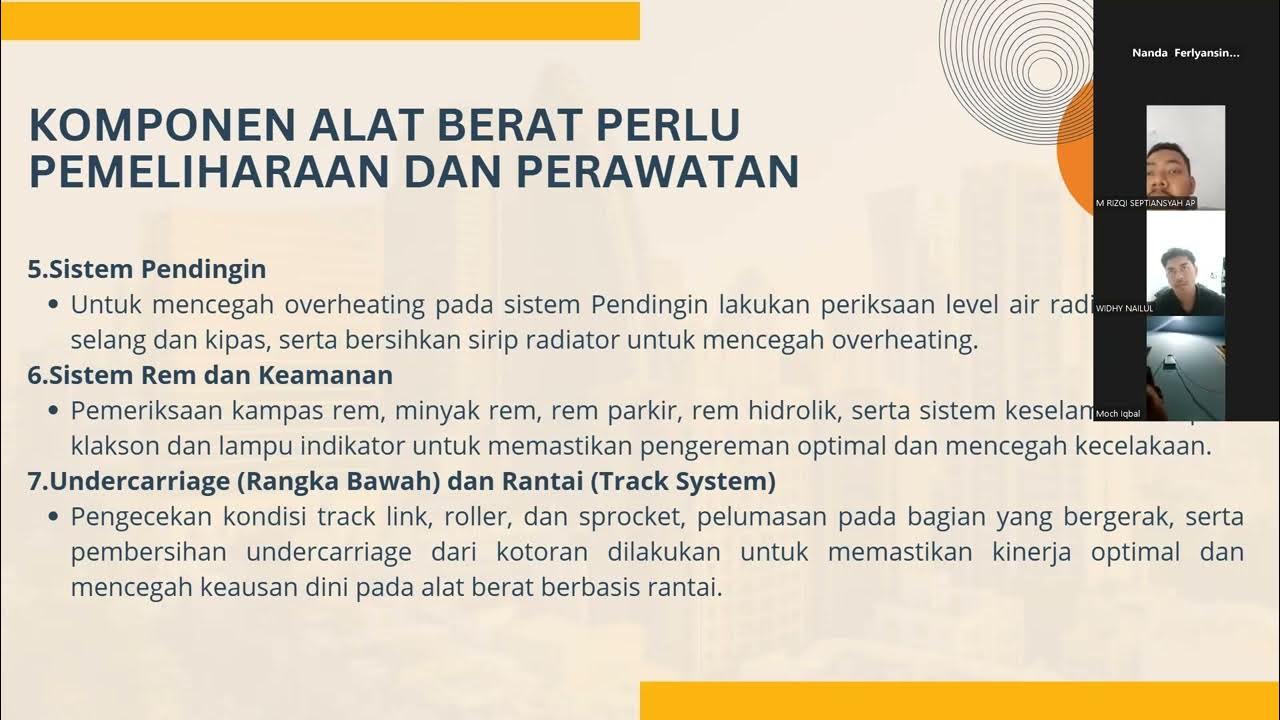
Video Presentasi Kelompok 7 Pemeliharaan dan Perawatan pada Alat Berat
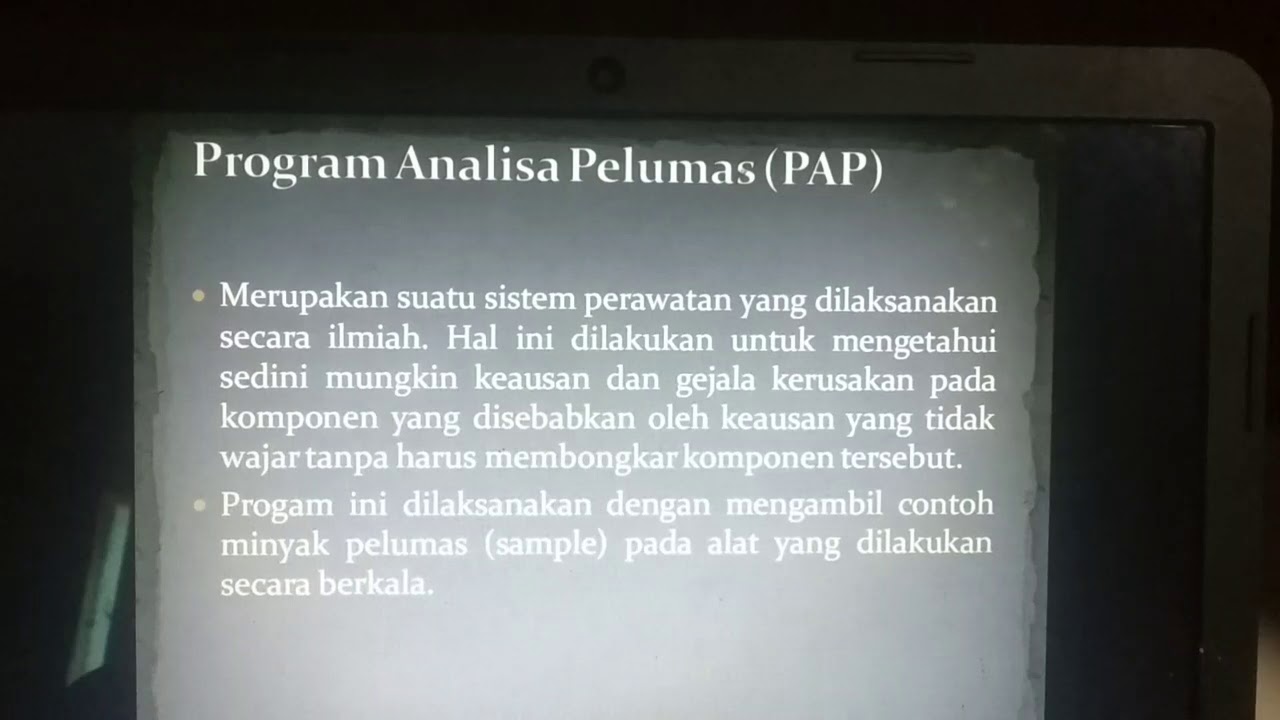
PREVENTIVE MAINTENANCE PADA UNIT ALAT BERAT.

1444 Dynamix Condition Monitoring

Exploring Different Types of Machine Sensors in Manufacturing: Uses, Pros & Cons

9.6 PEMELIHARAAN SARANA DAN PRASARANA KANTOR

MANTENIMIENTO DE AEROGENERADORES
5.0 / 5 (0 votes)