MANTENIMIENTO DE AEROGENERADORES
Summary
TLDRThis video delves into the efficient maintenance strategies for wind turbines, focusing on key aspects such as cost, labor, and inspection techniques. It explains that maintenance costs typically range from 1.5% of the turbine's total value per year, and labor requirements are minimal, with only a few technicians needed for routine inspections. The video highlights the shift from traditional systematic maintenance to condition-based maintenance (CBM), using advanced diagnostic tools like vibration sensors, oil analysis, and drones for blade inspections. This approach ensures greater efficiency, reduced costs, and increased turbine availability.
Takeaways
- π Wind turbine maintenance costs are generally 2-3% of the asset value annually.
- π For a 3 MW turbine worth approximately 2.5 million euros, annual maintenance costs range between 50,000 and 75,000 euros.
- π Due to more efficient strategies, actual maintenance costs are closer to 1.5% of the asset value, or around 35,000 euros annually.
- π Maintenance labor requirements are minimal, with about 2 people managing 20-25 turbines in a park.
- π A wind turbine park generally requires a supervisor and one additional technician for inspections and repairs.
- π Unlike conventional power plants, wind turbines use a condition-based maintenance (CBM) strategy instead of scheduled shutdowns.
- π In CBM, turbines are inspected regularly, and maintenance is only performed when issues are detected during inspections.
- π Three main inspection techniques are used: sensorial (visual, tactile, auditory), real-time instrumentation monitoring, and offline diagnostics.
- π Real-time instrumentation (e.g., vibration sensors, temperature monitoring) allows for remote monitoring of turbine health.
- π Portable tools for offline diagnostics, such as drone inspections and ultrasonic testing, help detect issues early and prevent costly repairs.
- π Despite technological advancements in sensor-based maintenance, technologies like cameras for internal turbine inspection are not yet widely implemented.
Q & A
What is the typical annual maintenance cost for a wind turbine?
-The typical annual maintenance cost for a wind turbine is between β¬50,000 and β¬75,000, depending on the turbine's size and the specific maintenance strategy employed.
How much of the turbine's total cost is spent on maintenance each year?
-Maintenance typically costs around 2-3% of the total cost of the turbine's assets. For a 3 MW turbine costing approximately β¬2.5 million, this would amount to around β¬50,000 to β¬75,000 annually.
How does the efficient maintenance strategy reduce the annual cost of wind turbine maintenance?
-An efficient maintenance strategy can reduce costs to around 1.5% of the turbine's value, lowering the annual maintenance cost to approximately β¬35,000.
How many people are typically involved in the maintenance of a wind turbine park?
-Typically, a wind farm with 20-25 turbines requires only around two personnel for maintenance, with each turbine being inspected once every six months.
What are the key differences between the maintenance strategy of wind turbines and conventional power plants?
-Wind turbines use a condition-based maintenance strategy, where maintenance is performed based on the findings from regular inspections. In contrast, conventional power plants use a systematic strategy, relying on scheduled shutdowns for maintenance.
How does condition-based maintenance contribute to higher efficiency and cost-effectiveness?
-Condition-based maintenance is more efficient because it reduces unnecessary downtime and maintenance costs. By addressing issues as they are detected, wind turbines experience higher availability and lower overall maintenance costs compared to systematic shutdowns.
What are the three main types of inspections performed on wind turbines?
-The three main types of inspections are: visual inspections (sensory checks), online instrumentation (real-time monitoring with sensors), and offline diagnostic techniques (such as oil analysis and vibration analysis).
What role does online instrumentation play in wind turbine maintenance?
-Online instrumentation involves using sensors to monitor turbine performance and key parameters (e.g., electrical output, temperature, vibrations) in real-time. This allows for remote monitoring and early detection of potential issues.
What is the importance of vibration monitoring in wind turbine maintenance?
-Vibration monitoring is essential for detecting mechanical issues, particularly with critical components like bearings, gearboxes, and generators. It helps predict failures before they cause serious damage, thus avoiding costly repairs and downtime.
How is oil analysis used in the maintenance of wind turbines?
-Oil analysis is used to monitor the condition of oils in key turbine components (e.g., gearbox, hydraulics). Sensors measure factors like particle count, moisture content, and gas chromatography to detect wear or contamination before a failure occurs.
Outlines
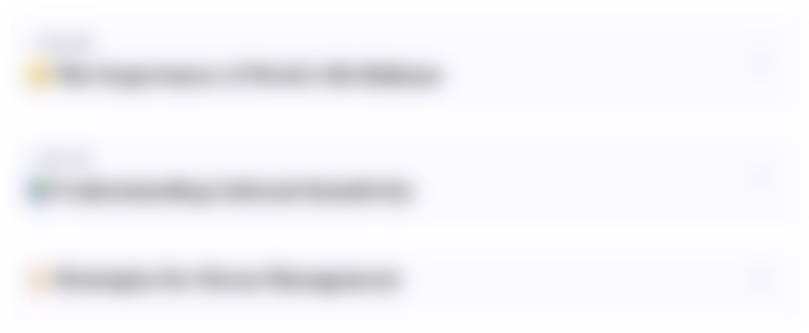
This section is available to paid users only. Please upgrade to access this part.
Upgrade NowMindmap
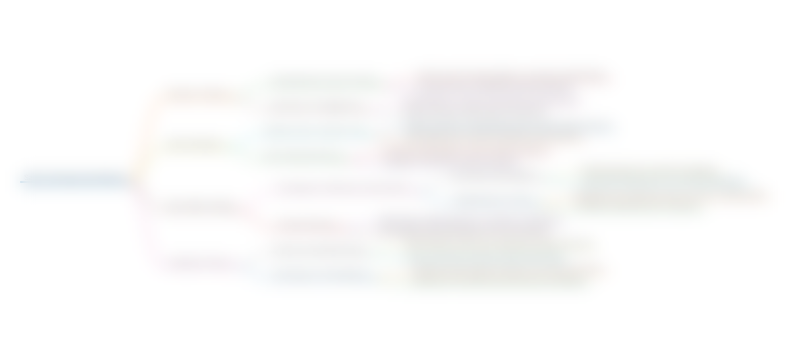
This section is available to paid users only. Please upgrade to access this part.
Upgrade NowKeywords
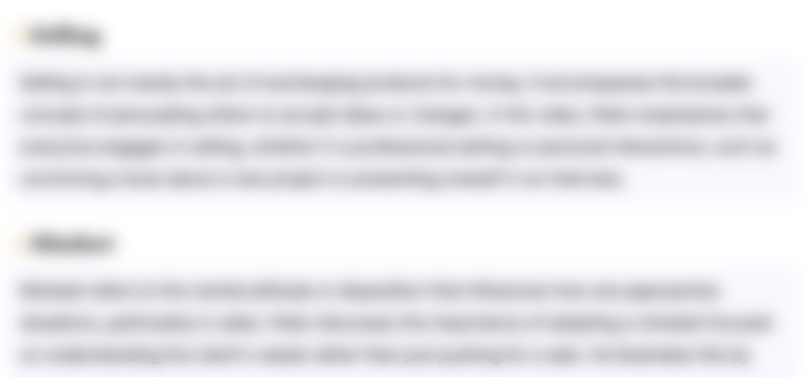
This section is available to paid users only. Please upgrade to access this part.
Upgrade NowHighlights
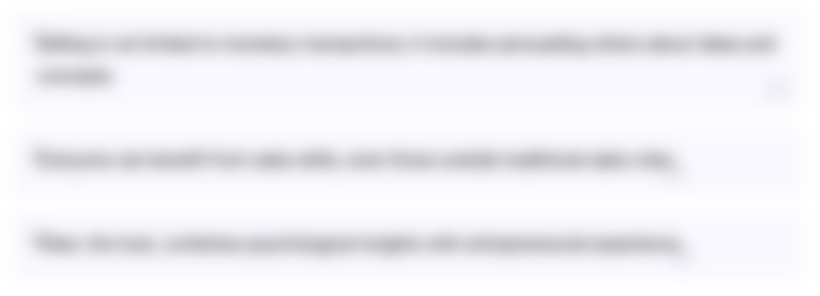
This section is available to paid users only. Please upgrade to access this part.
Upgrade NowTranscripts
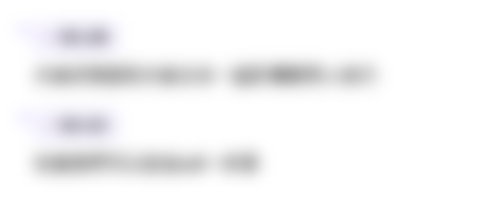
This section is available to paid users only. Please upgrade to access this part.
Upgrade NowBrowse More Related Video
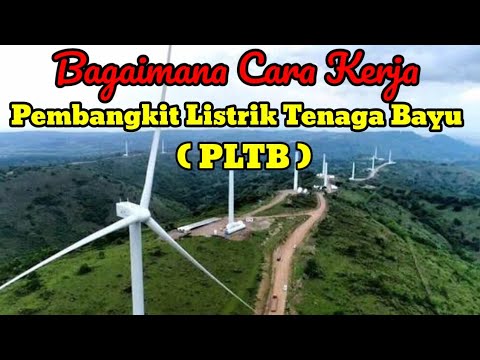
PLTB || Sejarah, Komponen Utama dan Cara Kerja Pembangkit Listrik Tenaga Bayu (Angin)
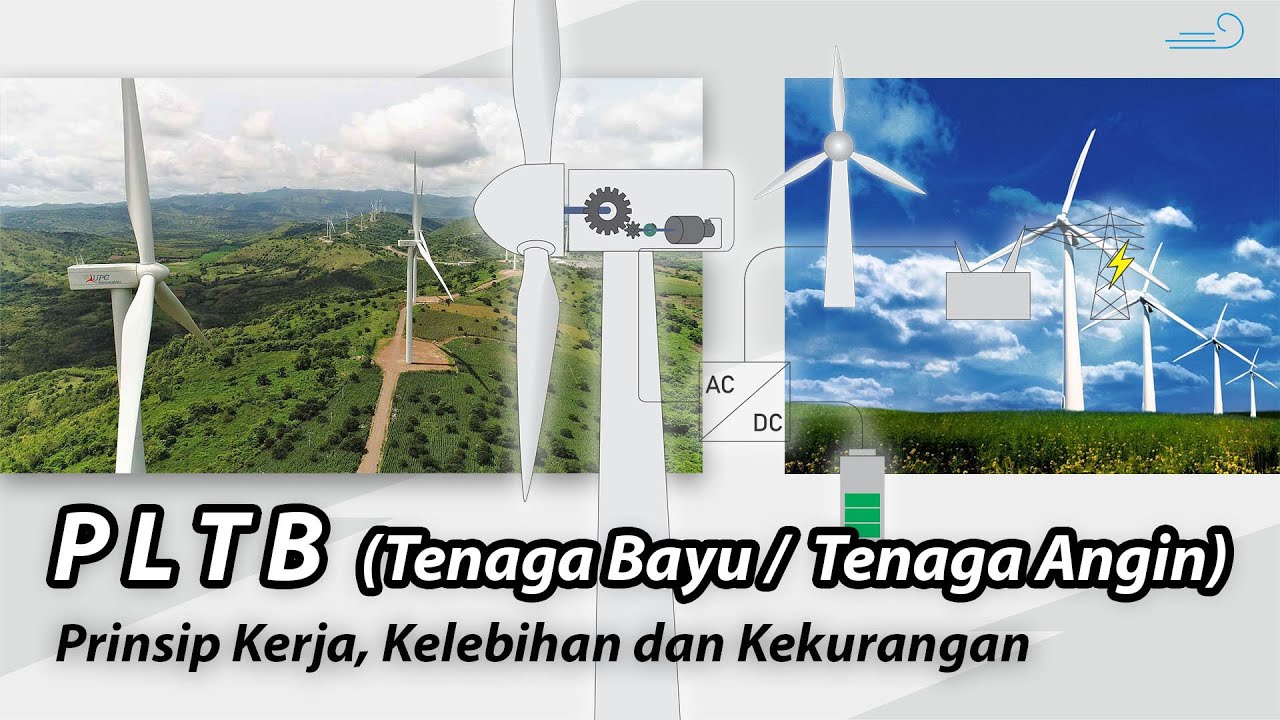
Pembangkit Listrik Tenaga Bayu / Tenaga Angin (PLTB) - Prinsip Kerja, Kelebihan dan Kekurangan
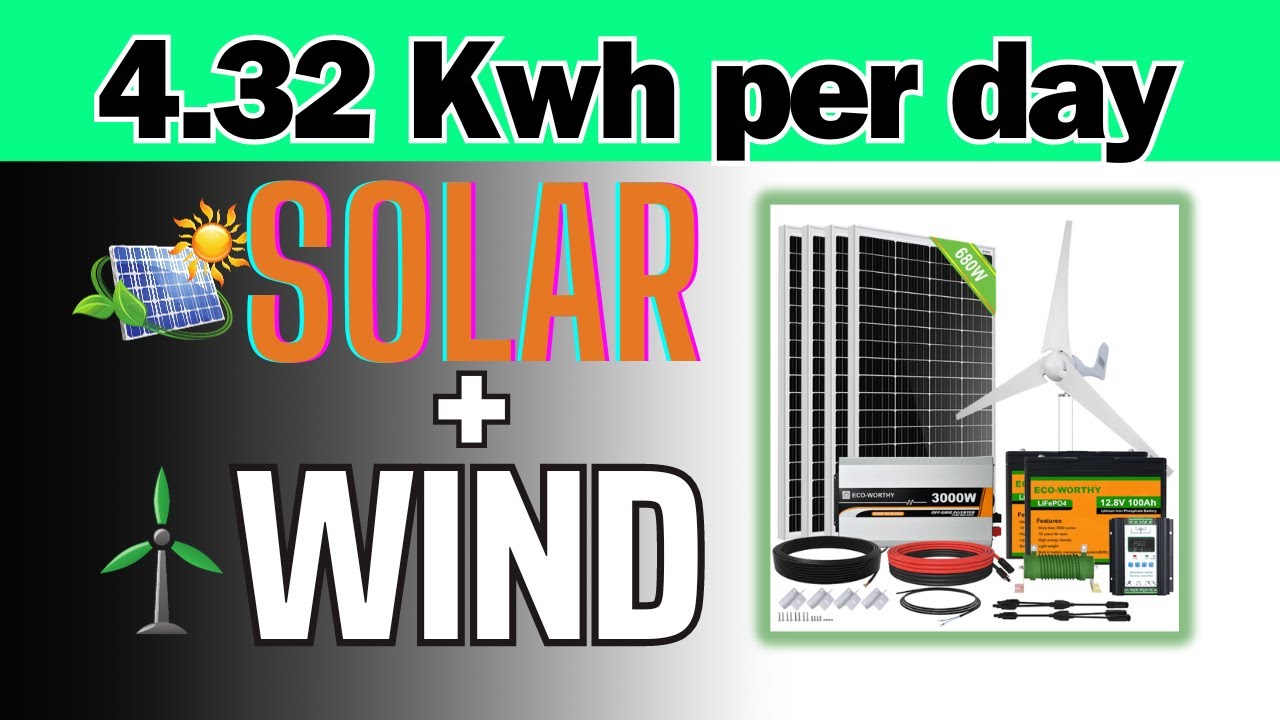
Solar Wind Hybrid System can generate more energy for you | ECO-WORTHY

Tugas vidio Presentasi Kelompok 4 (Anggaran Tenaga Kerja) Mata kuliah Budgeting
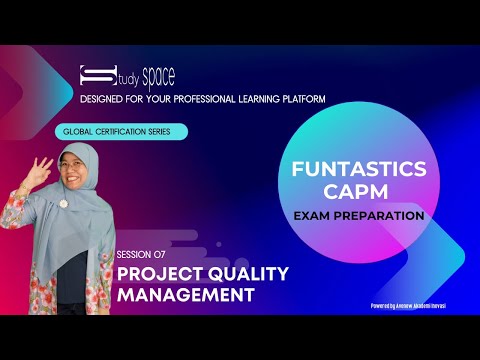
StudySpace | CAPM 7 - Project Quality Management

Arborikultur: Penanaman dan Pemeliharaan Pohon (Silvikultur) dalam Hutan Kota
5.0 / 5 (0 votes)