Surface hardening of steel | flame, induction, laser beam, case hardening and nitriding
Summary
TLDRThis video script delves into surface hardening techniques for steel, crucial for enhancing wear resistance in components like gear wheels. It explores various methods including flame, induction, laser hardening, and nitriding, each affecting the steel's microstructure differently. The script highlights the importance of achieving a hard surface layer while maintaining core toughness, and touches on the challenges of distortion and embrittlement. It also discusses the role of carbon content in hardenability and the unique benefits of case hardening and nitriding for specific applications.
Takeaways
- 🔧 Surface hardening of steel is crucial for increasing wear resistance in components that experience contact and sliding, like gear teeth.
- 🛠️ Hardening the entire component can reduce toughness and cause embrittlement, so surface hardening is preferred to maintain core toughness.
- 🔥 Flame hardening involves passing a torch flame over the material to induce a microstructural change, creating a hard martensitic surface layer.
- 💧 Water jets are used to quench the heated surface in flame hardening, leading to the formation of martensite and enhancing wear resistance.
- 🌀 Induction hardening uses electromagnetic induction to heat the surface rapidly, allowing for precise control of the hardening depth through frequency adjustment.
- 🌡️ Laser hardening provides extremely short heating times, reducing distortion and scaling, and can be done without additional quenching due to self-quenching.
- ⚙️ Case hardening is used for low carbon steels, where carbon is diffused into the surface to increase hardenability, followed by quenching to form a hard surface layer.
- 🔩 Nitriding is a surface hardening process that involves diffusing nitrogen into the steel surface to form hard nitrides, improving wear resistance without structural transformation.
- 🔩 The depth of the hardened layer in surface hardening processes can be controlled by factors such as the speed of the flame in flame hardening or the frequency in induction hardening.
- ⏱️ Heating times and the potential for distortion vary across hardening methods, with laser hardening offering the shortest heating times and reduced risk of distortion.
Q & A
Why is surface hardening of steel components important?
-Surface hardening of steel components is important to increase wear resistance, particularly for parts in contact with each other, like gear tooth flanks. It hardens only the surface layer while retaining the core's toughness to prevent unpredictable material failure.
What is the primary disadvantage of traditional heat treatment over surface hardening?
-The primary disadvantage of traditional heat treatment is the reduction in toughness and embrittlement of the steel, which can lead to unpredictable material failure. Surface hardening mitigates this by only hardening the surface, keeping the core tough.
How does flame hardening work?
-Flame hardening involves passing a torch flame over the material's surface to be hardened, causing a microstructural change. The high temperatures induce austenite formation, and water jets quench the surface rapidly, trapping carbon in the martensitic structure, forming hard martensite.
What is the role of the water jets in flame hardening?
-The water jets in flame hardening are used to quench the heated surface immediately after the flame passes, ensuring rapid cooling that traps carbon in the martensitic structure, leading to the formation of hard martensite.
How does the thickness of the hardened surface layer in flame hardening relate to the flame passing speed?
-The thickness of the hardened surface layer in flame hardening is controlled by the speed at which the flame is passed over the workpiece. A slower speed allows deeper heat penetration, affecting the microstructure more and resulting in a thicker hardened layer.
What is induction hardening and how does it differ from flame hardening?
-Induction hardening uses electromagnetic induction to generate high-frequency alternating currents that heat the workpiece's surface. It differs from flame hardening by providing more precise control over the hardening depth and is more suitable for complex geometries and smaller components.
How does the skin effect influence the hardening depth in induction hardening?
-The skin effect refers to the increase in current density towards the outer areas of a conductor with increasing frequency of alternating current. This allows for greater control over the hardening depth by adjusting the frequency; higher frequencies result in thinner hardness layers.
What are the advantages of laser hardening over other surface hardening processes?
-Laser hardening offers shorter heating times, reducing distortion and scaling. It also allows for precise control over the hardened area, is suitable for hard-to-reach areas, and avoids the need for water quenching due to self-quenching.
How does case hardening differ from other surface hardening processes?
-Case hardening involves diffusing carbon into the surface layer of a low carbon steel to increase its carbon content to a hardenable level, followed by quenching. This results in a hard, wear-resistant surface while the core remains tough and ductile.
What is nitriding, and how does it provide a solution for surface hardening without microstructural transformation?
-Nitriding is a process where nitrogen-containing gases or salts diffuse nitrogen atoms into the surface of specially alloyed steels, forming hard nitrides without a martensitic transformation. This results in increased surface hardness and wear resistance without the distortion or scaling associated with other hardening methods.
Why is tempering often required after case hardening?
-Tempering is often required after case hardening to reduce the high residual stresses caused by the hardness differences between the surface and the core of the component. This helps to improve the component's dimensional stability and fatigue resistance.
Outlines
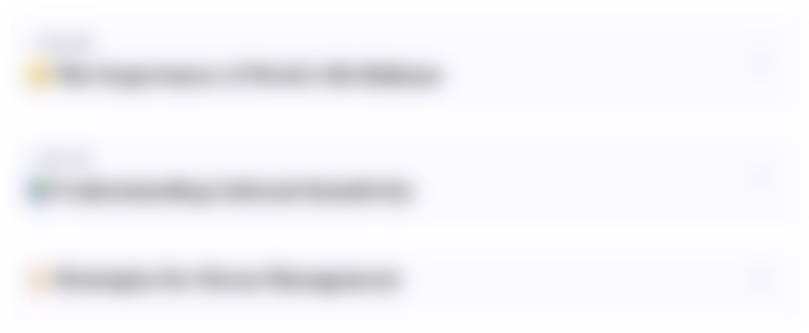
Cette section est réservée aux utilisateurs payants. Améliorez votre compte pour accéder à cette section.
Améliorer maintenantMindmap
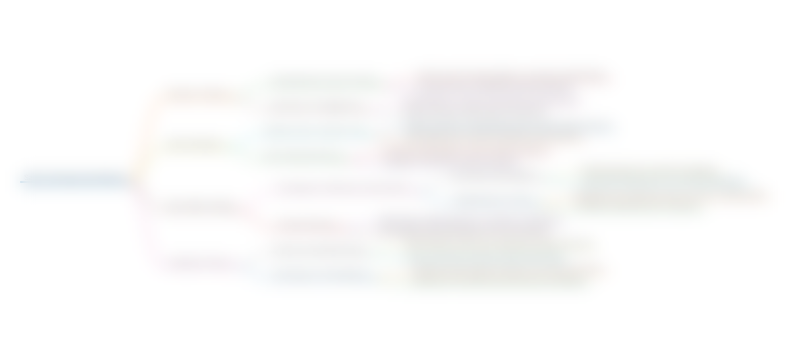
Cette section est réservée aux utilisateurs payants. Améliorez votre compte pour accéder à cette section.
Améliorer maintenantKeywords
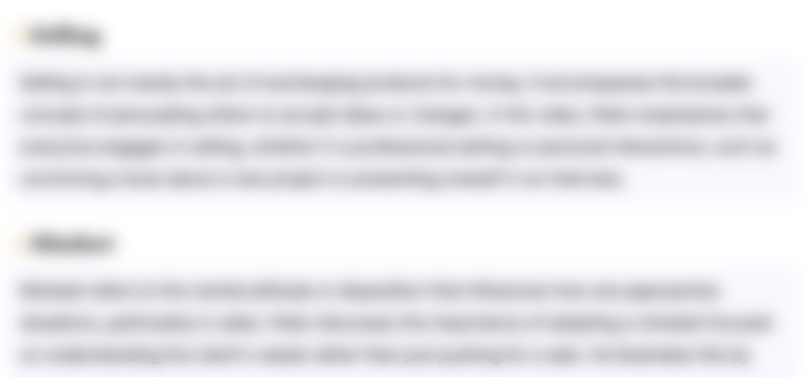
Cette section est réservée aux utilisateurs payants. Améliorez votre compte pour accéder à cette section.
Améliorer maintenantHighlights
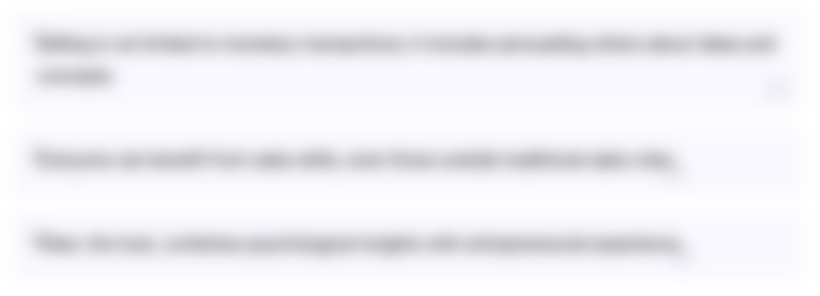
Cette section est réservée aux utilisateurs payants. Améliorez votre compte pour accéder à cette section.
Améliorer maintenantTranscripts
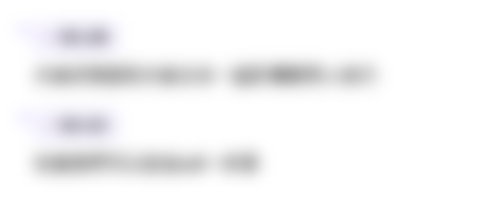
Cette section est réservée aux utilisateurs payants. Améliorez votre compte pour accéder à cette section.
Améliorer maintenantVoir Plus de Vidéos Connexes
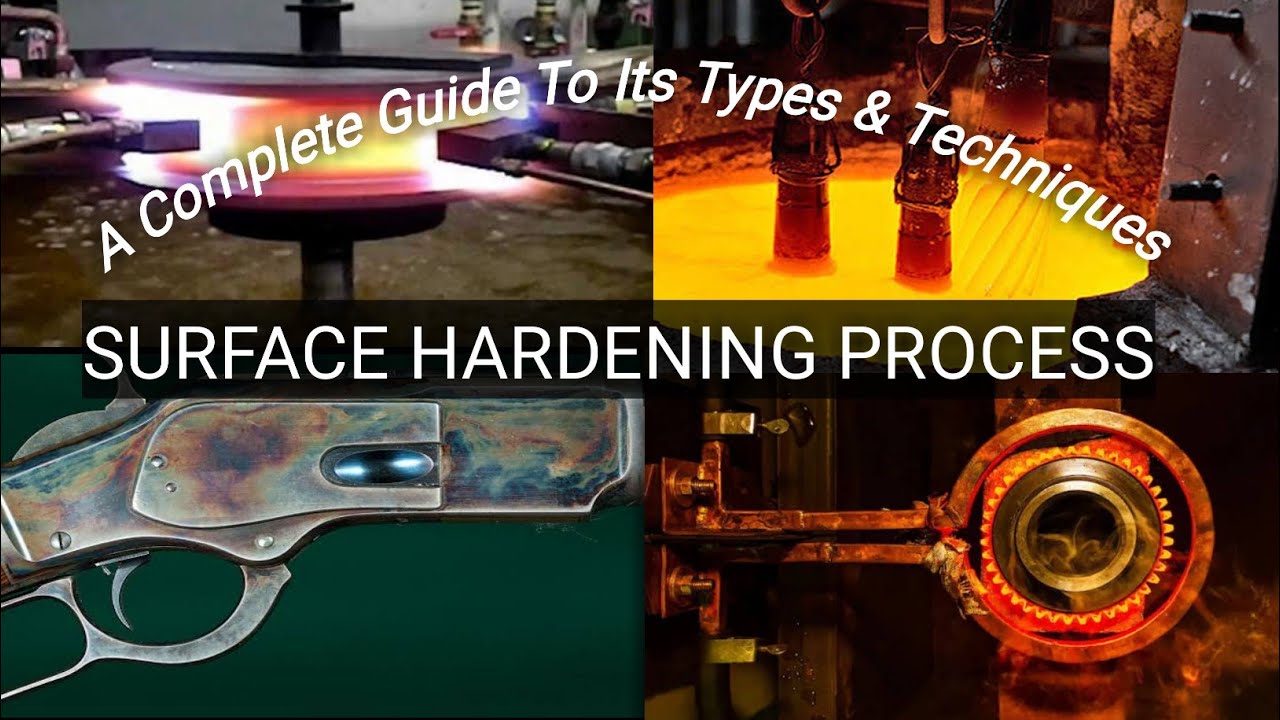
Surface Hardening Process | A Complete Guide To Its Types and Techniques.
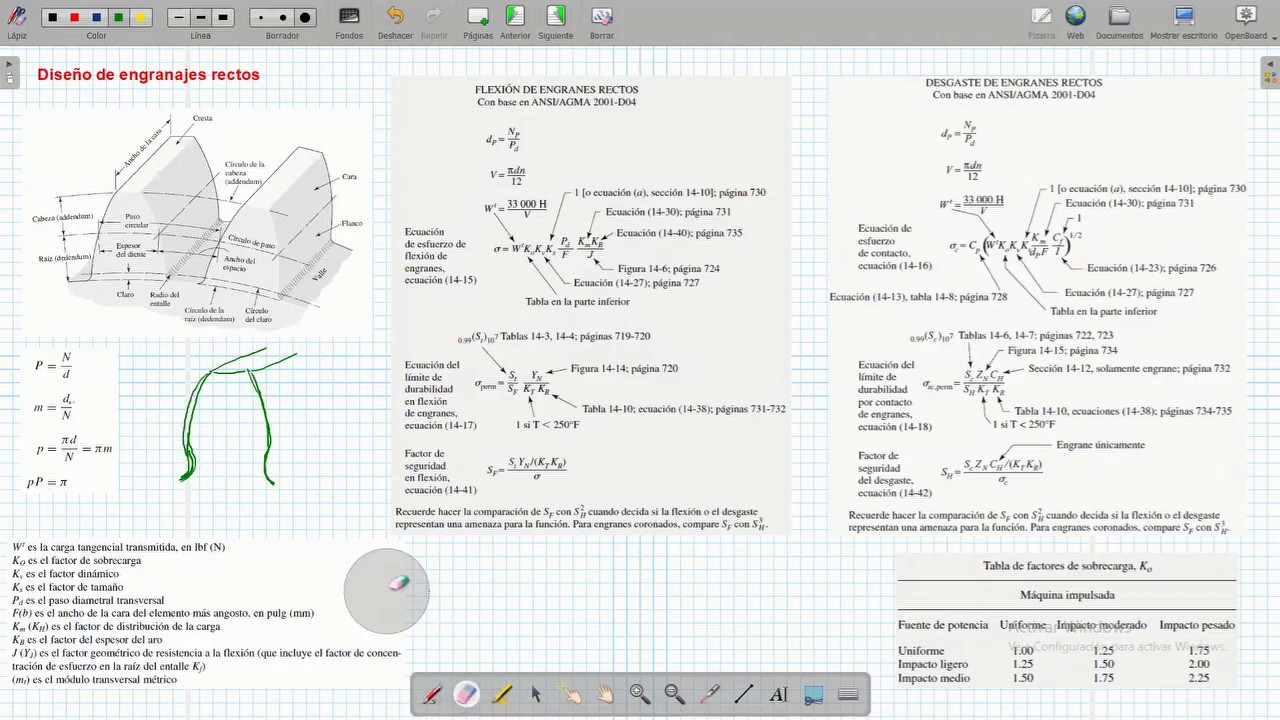
Metodología ANSI/AGMA para diseño de engranes rectos y helicoidales parte 1
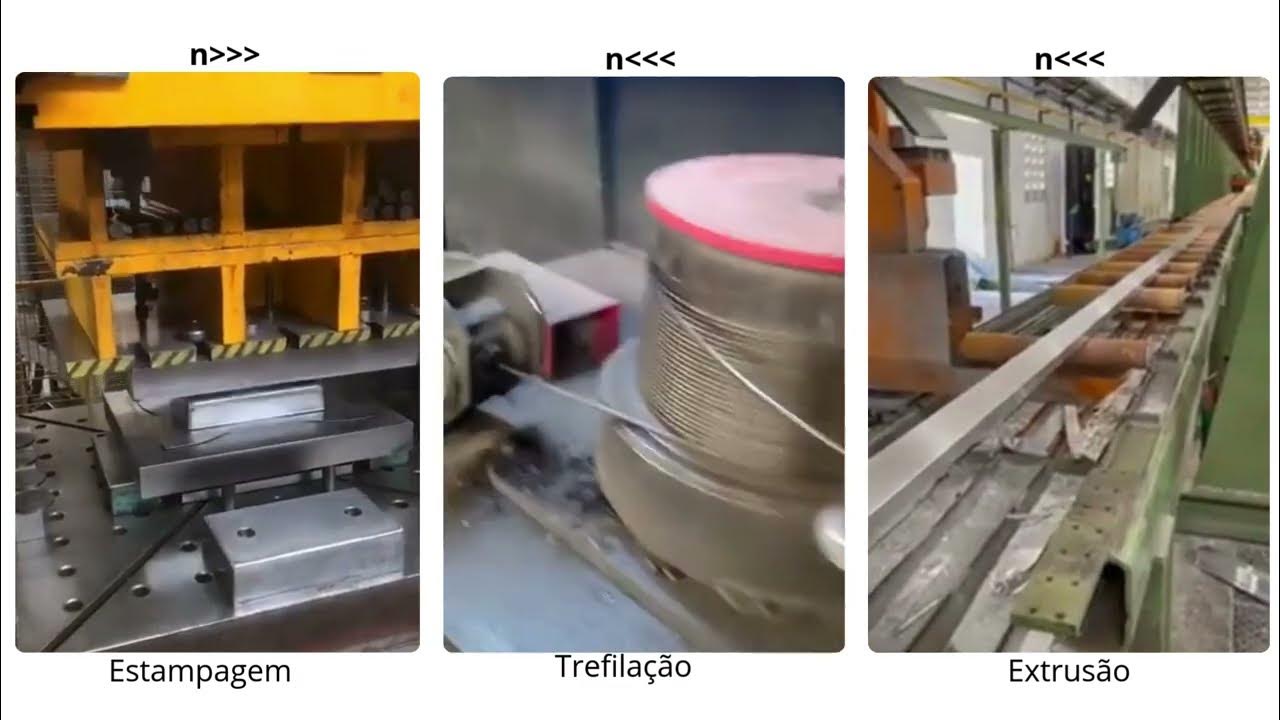
Pitch sobre Curva de Escoamento

BEGINI TAHAPAN PROSES PEMBUATAN RODA KERETA API DI PABRIK MODERN
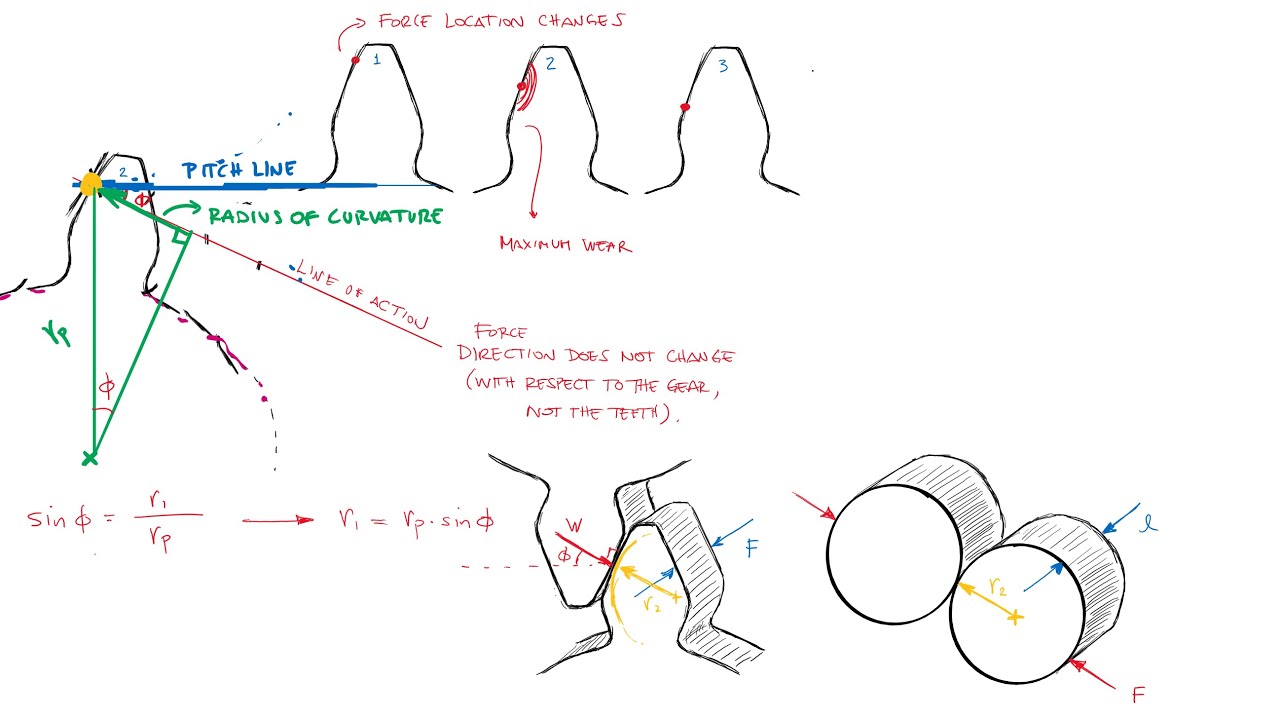
Gear PITTING - Surface Contact Stress Fatigue Failure in Just Over 10 Minutes!
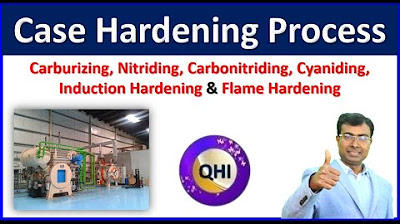
Case Hardening and 6 Types of Case Hardening || Heat Treatment Process
5.0 / 5 (0 votes)