Lean Manufacturing - Pull Systems
Summary
TLDRLean manufacturing focuses on eliminating waste and producing only what is demanded by customers. It operates on a pull system where production and distribution are driven by actual customer orders rather than forecasts. This approach minimizes work in process (WIP) and inventory. Pull systems can be sequential, where parts are pulled in the order of production, or replenishment, similar to a supermarket model. Kanban, a lean tool, uses signals to manage the flow of parts and tasks, helping to prioritize and prevent overloading, thus maintaining a smooth and efficient workflow.
Takeaways
- ⚙️ Lean manufacturing focuses on reducing or removing waste from systems or processes.
- 📦 Lean companies produce only enough products to meet real customer demands, avoiding inventory of finished goods.
- 🔄 A pull-based system is demand-driven and not dependent on forecasts.
- 📉 The pull system limits the amount of work in process (WIP) within the system.
- 💡 Production and replenishment are triggered by actual customer orders.
- ✔️ In a pull system, work items can only be in process if there's a demand for them.
- 🛠️ Sequential pull involves downstream personnel pulling parts in sequence, limiting inventory between steps.
- 🏭 One-piece flow aims to move sub-assemblies from step to step with minimal WIP inventory.
- 🏬 Replenishment pull systems, like supermarkets, use signals to request parts when needed.
- 📋 Kanban systems use visual signals, like cards, to manage the flow of supplies in a pull system.
Q & A
What is the primary goal of lean manufacturing?
-The primary goal of lean manufacturing is to reduce or eliminate waste within a system or process, ensuring efficiency by meeting real customer demands.
How does a pull-based system differ from a forecast-reliant system?
-A pull-based system is demand-driven, meaning production is based on actual customer orders, while a forecast-reliant system produces based on predicted demand.
What is 'work in process' (WIP) in the context of lean manufacturing?
-WIP refers to the amount of work that is actively being processed at any given time. A pull system limits WIP to avoid overproduction and inefficiencies.
How is production replenishment determined in a pull-based system?
-Production replenishment in a pull-based system is determined by actual customer orders that have been received, ensuring that only the necessary products are made.
What are the two types of pull systems, and how do they differ?
-The two types of pull systems are sequential pull and replenishment pull. In a sequential pull, downstream personnel pull parts from upstream in sequence, limiting inventory between process steps. In a replenishment pull, parts are pulled from a storage location based on need, similar to a supermarket system.
What is one-piece flow, and why is it ideal in lean manufacturing?
-One-piece flow refers to moving sub-assemblies from one step to the next one piece at a time, or in small batches, minimizing WIP inventory. It is ideal because it improves efficiency and reduces waste.
What is Kanban, and how does it work in a pull system?
-Kanban, which means 'signal' in Japanese, is a system that uses cards or signals to manage the flow of materials. In a pull system, Kanban signals when more supplies are needed to replenish stock.
How does a pull system help employees prioritize their tasks?
-A pull system allows employees to pull their next task only if they have the capacity to start it, preventing overload and helping them focus on executing work efficiently.
What is an example of a pull system in manufacturing?
-An example is when an operator at station 4 removes a sub-assembly, which signals the operator at station 3 to replenish it. This limits the amount of WIP between these stations and controls the flow of production.
What is the role of signals in a pull system, and what happens when a WIP limit is reached?
-Signals, such as cards, lights, or other prompts, trigger replenishment actions in a pull system. When the WIP limit is reached, such as when half a box of components is consumed, it signals the need to bring more supplies.
Outlines
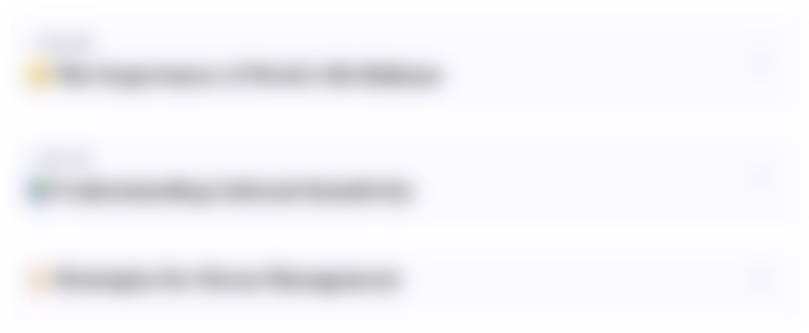
Dieser Bereich ist nur für Premium-Benutzer verfügbar. Bitte führen Sie ein Upgrade durch, um auf diesen Abschnitt zuzugreifen.
Upgrade durchführenMindmap
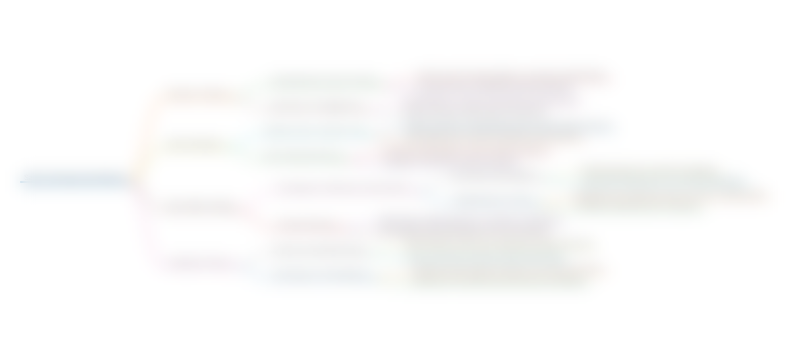
Dieser Bereich ist nur für Premium-Benutzer verfügbar. Bitte führen Sie ein Upgrade durch, um auf diesen Abschnitt zuzugreifen.
Upgrade durchführenKeywords
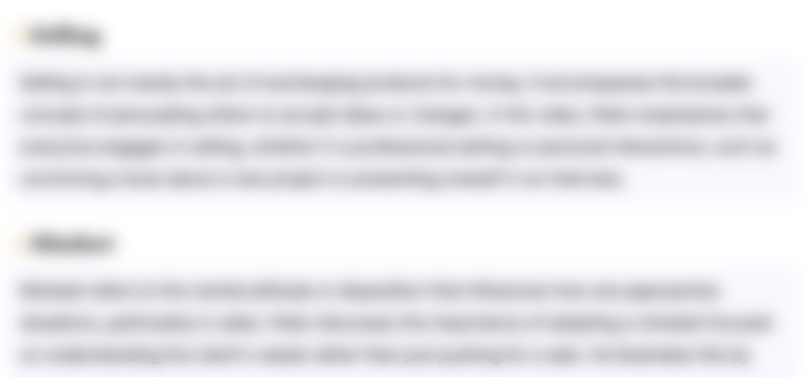
Dieser Bereich ist nur für Premium-Benutzer verfügbar. Bitte führen Sie ein Upgrade durch, um auf diesen Abschnitt zuzugreifen.
Upgrade durchführenHighlights
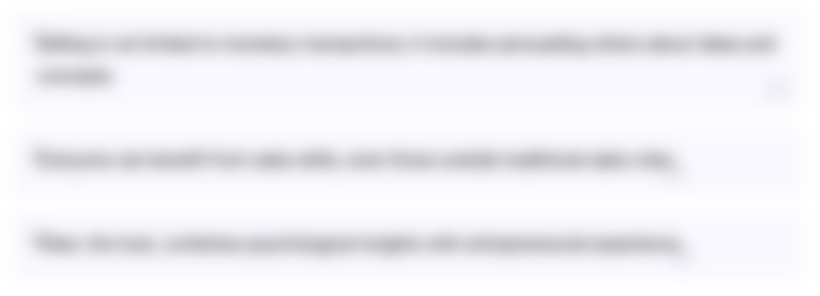
Dieser Bereich ist nur für Premium-Benutzer verfügbar. Bitte führen Sie ein Upgrade durch, um auf diesen Abschnitt zuzugreifen.
Upgrade durchführenTranscripts
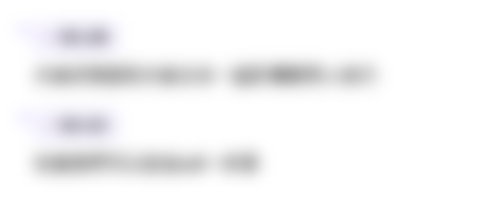
Dieser Bereich ist nur für Premium-Benutzer verfügbar. Bitte führen Sie ein Upgrade durch, um auf diesen Abschnitt zuzugreifen.
Upgrade durchführenWeitere ähnliche Videos ansehen

Toyota’s Lean Supply Chain: The Secret Behind JIT Manufacturing Success | MBA Case study analysis
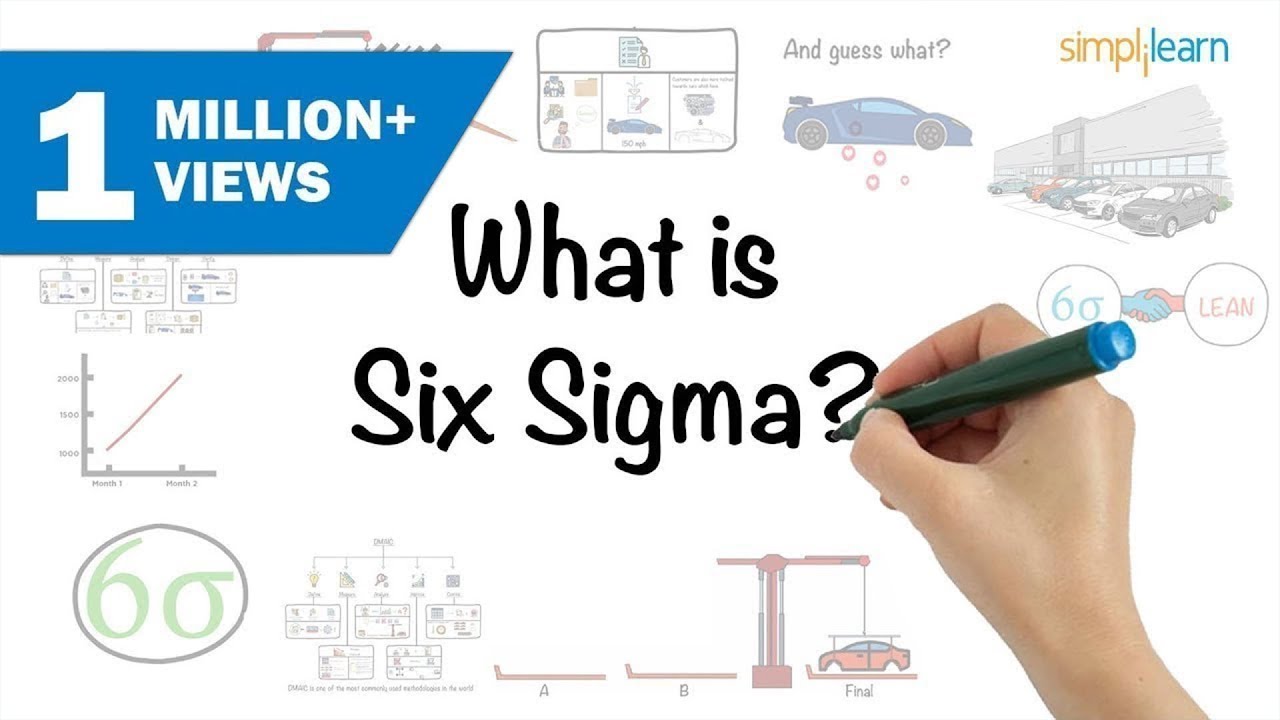
Six Sigma In 9 Minutes | What Is Six Sigma? | Six Sigma Explained | Six Sigma Training | Simplilearn
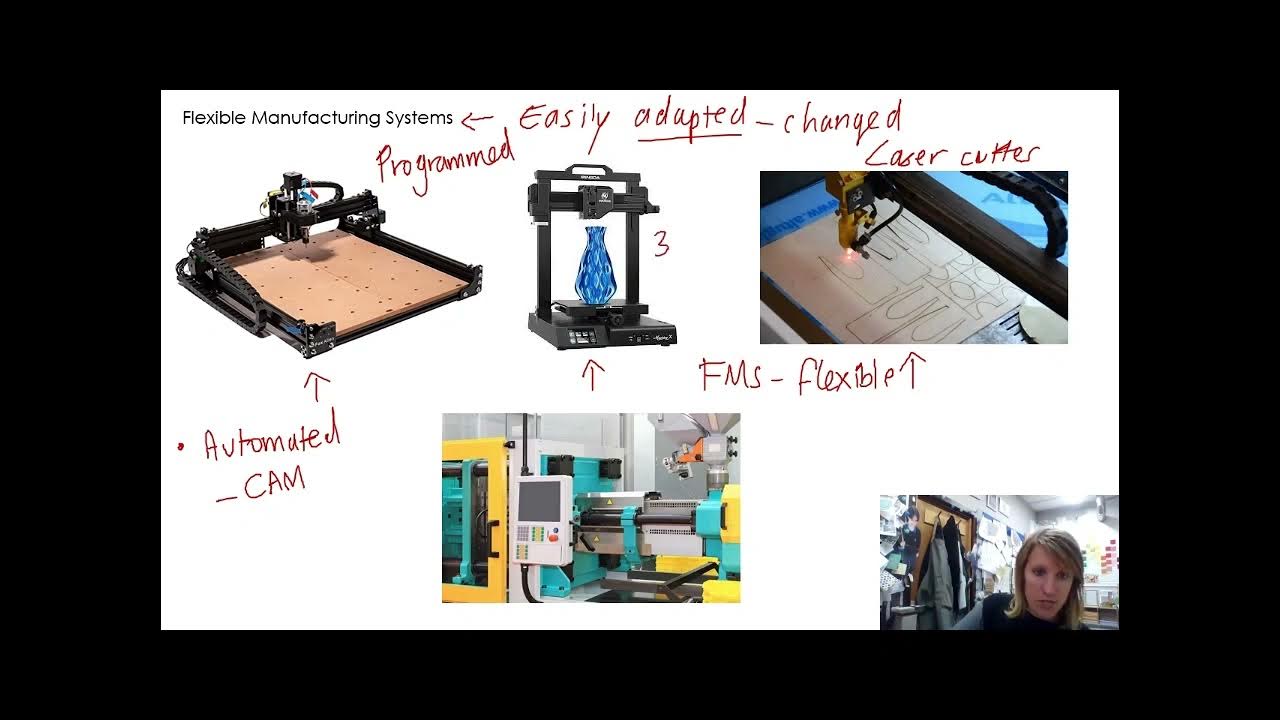
Video 2 - Flexible and Lean Manufacturing

⚙ Lean Manufacturing | A pursuit of perfection
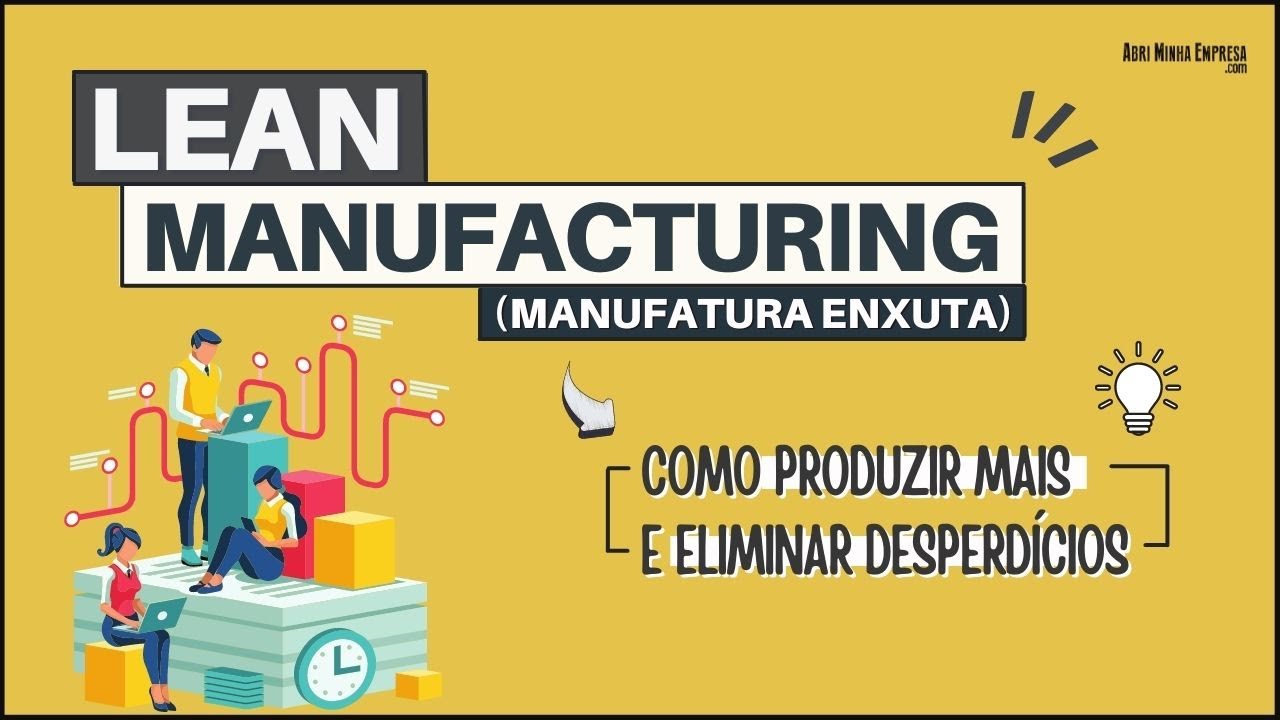
LEAN MANUFACTURING (Manufatura Enxuta) | Conheça os 8 Principais Tipos de Desperdícios
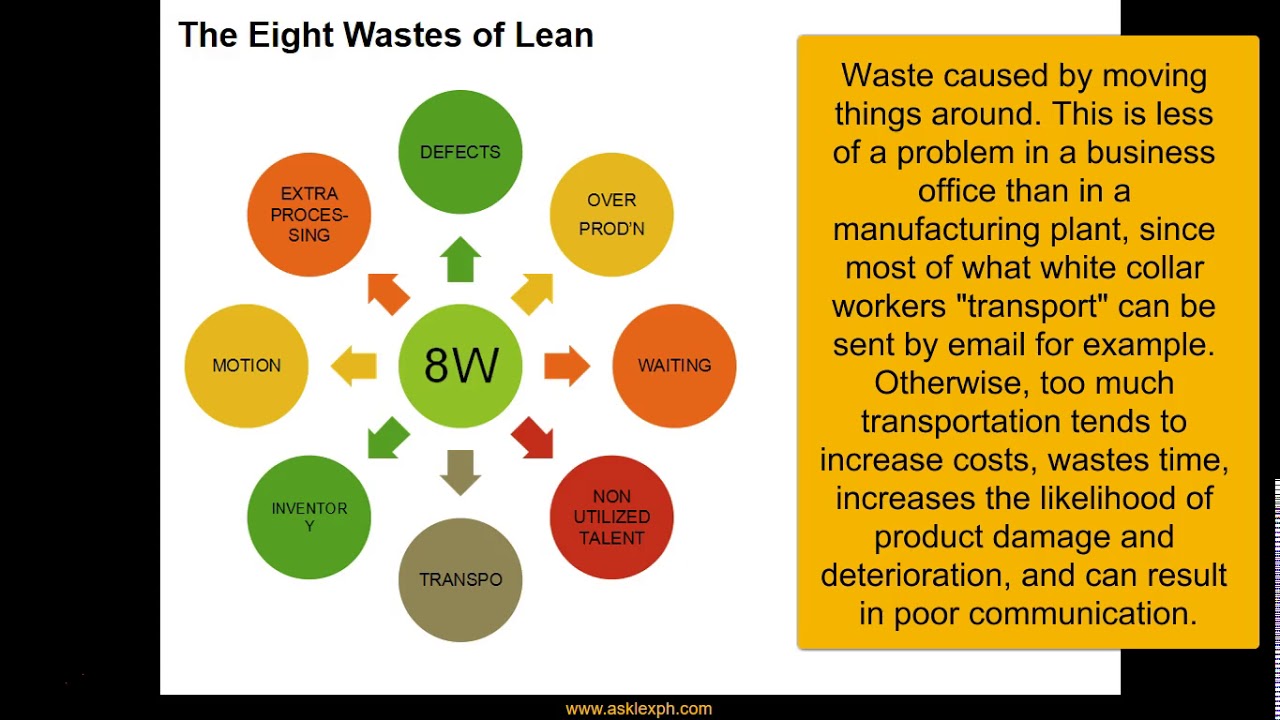
F3. The Eight Wastes of Lean (DOWNTIME)
5.0 / 5 (0 votes)